TU-1300E Substrate Изготовитель
Производитель подложек ТУ-1300Е,TU-1300E Substrate is a specialized material designed for high-frequency RF and microwave applications. Known for its low dielectric constant and loss tangent, TU-1300E ensures minimal signal attenuation and excellent signal integrity. It offers superior thermal stability and reliability, making it suitable for harsh operating environments. TU-1300E Substrate is widely used in telecommunications, Радиолокационные системы, and aerospace applications where high-performance electronic components are essential. Its ability to support complex circuit designs and maintain consistent electrical properties over a wide range of frequencies makes TU-1300E Substrate a preferred choice for engineers and designers working on cutting-edge RF and microwave technologies.
Что такое TU-1300E Substrate?
TU-1300E substrate, also known as a glass core package substrate, is a specialized material used in advanced electronics manufacturing. It features a glass core with high thermal conductivity, which enhances heat dissipation and thermal management in electronic devices. This substrate is crucial in applications requiring efficient thermal performance and reliability, such as in high-power LEDs, RF/microwave devices, and power modules.
The TU-1300E substrate offers several advantages. Its low coefficient of thermal expansion (CTE) helps minimize stress during temperature changes, reducing the risk of component failure. Moreover, its excellent dimensional stability ensures precise alignment of components, crucial for maintaining signal integrity in high-frequency applications. The glass core also provides mechanical robustness, making it suitable for environments with demanding mechanical stresses.
Manufacturers often use TU-1300E substrates in products where thermal management is critical, such as in automotive electronics, telecommunications equipment, and aerospace applications. By leveraging its thermal properties and reliability, TU-1300E substrates contribute significantly to improving the performance and longevity of electronic systems operating in challenging conditions.
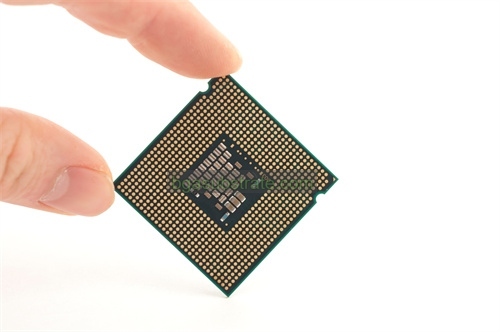
Производитель подложек ТУ-1300Е
Что такое TU-1300E Substrate Рекомендации по проектированию?
Рекомендации по проектированию TU-1300E substrates typically focus on optimizing thermal performance, надёжность, и технологичность. Here are some key aspects usually considered in TU-1300E substrate design:
- Управление температурным режимом: Due to its high thermal conductivity, design should maximize heat dissipation efficiency. This involves strategically placing heat-generating components and thermal vias to facilitate effective heat transfer to the substrate.
- Стабильность размеров: TU-1300E substrates have a low coefficient of thermal expansion (CTE), minimizing dimensional changes with temperature variations. Design guidelines emphasize maintaining tight tolerances to ensure component alignment and prevent mechanical stress during operation.
- Signal Integrity: For RF/microwave applications, maintaining signal integrity is crucial. Design considerations include minimizing signal loss and interference by optimizing trace routing, Согласование импеданса, and minimizing signal crosstalk.
- Mechanical Durability: TU-1300E substrates offer mechanical robustness, but designs should still account for mechanical stresses, such as vibrations and shocks. Secure mounting of components and adequate support structures are essential to ensure reliability in harsh environments.
- Технологичность: Design guidelines also focus on ensuring ease of manufacturing and assembly. This includes considerations for substrate thickness, via design, pad sizes, and alignment markers to facilitate accurate and efficient assembly processes.
- Экологические соображения: Applications in automotive, аэрокосмический, and other rugged environments require designs that can withstand temperature extremes, влажность, and exposure to chemicals or moisture. Encapsulation and conformal coating may be recommended to enhance environmental resilience.
- Cost Optimization: Balancing performance requirements with cost considerations is essential. Design guidelines may suggest optimizing material usage, reducing complex features that increase manufacturing costs, and considering alternative designs or materials where feasible.
Полный, adhering to these design guidelines for TU-1300E substrates ensures that electronic systems achieve optimal performance, надёжность, and longevity across various demanding applications.
Преимущества TU-1300E Substrate
TU-1300E substrate offers several advantages that make it a preferred choice in advanced electronics:
- Высокая теплопроводность: The substrate’s glass core provides excellent thermal conductivity, facilitating efficient heat dissipation from electronic components. This property helps in managing heat effectively, reducing the risk of thermal-induced failures and improving overall system reliability.
- Low Coefficient of Thermal Expansion (CTE): TU-1300E substrates exhibit a low CTE, which minimizes dimensional changes under temperature variations. This characteristic ensures dimensional stability, critical for maintaining tight tolerances and preventing stress on solder joints and components.
- Mechanical Robustness: The glass core enhances mechanical strength, providing durability and resistance to mechanical stresses such as vibrations and shocks. This feature is advantageous in applications where reliability in harsh environments is essential, such as automotive electronics and aerospace systems.
- Electrical Performance: TU-1300E substrates offer good electrical properties, including low dielectric loss and excellent insulation characteristics. These properties contribute to maintaining signal integrity and minimizing signal loss in high-frequency applications, making them suitable for RF/microwave devices.
- Design Flexibility: The substrate’s properties allow for intricate and precise designs, facilitating the integration of complex circuits and high-density interconnects. Designers can optimize layouts to improve performance and efficiency without compromising on reliability.
- Environmental Resilience: TU-1300E substrates are designed to withstand harsh environmental conditions, including temperature extremes, влажность, and exposure to chemicals. This resilience enhances the longevity and operational stability of electronic devices deployed in challenging environments.
- Cost-effectiveness: Despite its advanced properties, TU-1300E substrates are manufactured with considerations for cost-effectiveness. They offer a balance between performance and cost, making them viable for a wide range of applications from consumer electronics to industrial and military sectors.
Резюме, TU-1300E substrates combine thermal management capabilities, механическая прочность, Электрические характеристики, and design flexibility, making them a versatile choice for demanding electronic applications where reliability and performance are paramount.
Что такое TU-1300E Substrate Процесс изготовления?
The fabrication process of TU-1300E substrate involves several key steps to achieve its desired properties and characteristics. Here is a general outline of the fabrication process:
- Material Selection: The process begins with selecting high-quality materials that meet the specifications for TU-1300E substrates. This typically includes a glass core with specific thermal conductivity properties and compatible materials for the dielectric layers.
- Preparation of Glass Core: The glass core, which provides the substrate’s structural integrity and thermal properties, undergoes preparation. This includes cutting the glass into desired shapes and sizes, and sometimes polishing or surface treatment to ensure smoothness and cleanliness.
- Dielectric Layer Application: Dielectric layers are applied to the glass core. These layers serve multiple purposes, including providing electrical insulation, supporting the circuit patterns, and enhancing mechanical stability. The dielectric material is applied in thin, uniform layers using techniques such as screen printing, spin coating, or lamination.
- Circuit Patterning:Circuit patterns are defined on the substrate to create electrical pathways and connection points. This involves photolithography processes where a photoresist layer is applied over the dielectric, exposed to UV light through a mask, developed to reveal the pattern, and then etched to remove unwanted material.
- Металлизация: Metallization is performed to deposit conductive materials onto the substrate surface. This step creates the conductive traces, Колодки, and vias necessary for electrical connectivity between components. Metallization techniques include sputtering, electroplating, or screen printing, depending on the application requirements.
- Обработка поверхности: Surface finishing processes are applied to ensure the substrate’s surface is suitable for component attachment. This may involve applying solder mask layers to define areas for soldering, applying surface treatments for enhanced solderability, and adding protective coatings to improve durability and resistance to environmental factors.
- Инспекция и тестирование: На протяжении всего процесса изготовления, rigorous inspection and testing are conducted to verify the substrate’s dimensional accuracy, Электрические характеристики, and reliability. This includes checks for defects, electrical continuity, и соответствие проектным спецификациям.
- Assembly and Integration: Once fabricated, TU-1300E substrates are ready for assembly into electronic modules or systems. Components are mounted onto the substrate using soldering or bonding techniques, and the assembled units undergo further testing to ensure functionality and reliability.
- Packaging and Quality Control: Наконец, the substrates are packaged to protect them during transportation and handling. Quality control procedures continue to monitor the substrates for any defects or performance issues that may arise during or after fabrication.
Полный, the fabrication process of TU-1300E substrates combines precision manufacturing techniques with materials science to produce substrates that meet stringent requirements for thermal management, Электрические характеристики, and mechanical durability in advanced electronic applications.
Применение керамики TU-1300E Substrate
TU-1300E substrates find application in various high-performance electronic devices and systems where thermal management, надёжность, and electrical performance are critical. Вот некоторые ключевые области применения:
- Светодиодная упаковка: TU-1300E substrates are used in LED (Light Emitting Diode) packages, particularly in high-power LEDs where efficient heat dissipation is essential for maintaining longevity and performance. The substrate’s high thermal conductivity helps in managing the heat generated by LEDs, thereby improving their efficiency and reliability.
- RF/Microwave Devices: Due to their excellent electrical properties and low dielectric loss, TU-1300E substrates are ideal for RF (Радиочастота) и микроволновые приложения. They are used in components such as power amplifiers, Антенны, Фильтры, and other RF circuits where signal integrity and low loss are crucial.
- Power Modules: In power electronics, TU-1300E substrates are employed in power modules for devices like inverters, Конвертеры, and motor drives. The substrate’s ability to efficiently dissipate heat helps in enhancing the reliability and performance of these power devices, particularly under high-load conditions.
- Автомобильная электроника: TU-1300E substrates are used in automotive electronics, where they contribute to the thermal management and durability of electronic control units (Экю), Силовые модули, Датчики, and LED lighting systems. They withstand the mechanical stresses and temperature fluctuations typical in automotive environments.
- Аэрокосмическая и оборонная промышленность: In aerospace and defense applications, TU-1300E substrates are utilized in radar systems, Коммуникационное оборудование, avionics, and satellite components. Their robustness against mechanical stress and thermal cycling, coupled with high reliability, makes them suitable for demanding aerospace environments.
- Электросвязь: TU-1300E substrates support telecommunications infrastructure by providing reliable substrates for base station equipment, RF transceivers, and other network components. They help in maintaining signal integrity and operational stability in telecommunications networks.
- Электроника: In consumer electronics, TU-1300E substrates may be used in devices requiring high reliability and thermal management, such as high-performance computing systems, servers, and networking equipment.
Полный, TU-1300E substrates play a crucial role in enabling the performance, надёжность, and longevity of electronic devices across a wide range of industries and applications where advanced thermal and electrical properties are essential. Their integration helps in improving efficiency, reducing heat-related failures, and enhancing overall product performance in challenging operating conditions.
Часто задаваемые вопросы о TU-1300E Substrate
What is TU-1300E substrate?
TU-1300E substrate is a specialized ceramic material primarily composed of a glass core with high thermal conductivity. It is used in electronics for its excellent thermal management capabilities and reliability.
What are the key advantages of TU-1300E substrate?
TU-1300E substrate offers high thermal conductivity, low coefficient of thermal expansion (CTE), механическая прочность, good electrical performance, and design flexibility. These properties make it ideal for applications requiring efficient heat dissipation and reliability.
Where is TU-1300E substrate commonly used?
It is commonly used in LED packaging, RF/microwave devices, Силовые модули, Автомобильная электроника, aerospace applications, telecommunications equipment, and high-performance consumer electronics.
How does TU-1300E substrate compare to other materials like FR4?
Compared to FR4 (a common PCB substrate), TU-1300E substrate offers superior thermal conductivity and better mechanical and electrical properties, making it suitable for high-power and high-frequency applications where thermal management and reliability are critical.
What are the fabrication processes involved in making TU-1300E substrate?
The fabrication process typically includes material selection, preparation of the glass core, application of dielectric layers, circuit patterning, металлизация, surface finishing, осмотр, testing, assembly, and packaging.
What are the environmental considerations when using TU-1300E substrate?
TU-1300E substrate is designed to withstand harsh environmental conditions, including temperature extremes, влажность, and exposure to chemicals. This resilience enhances its suitability for applications in challenging environments such as automotive and aerospace industries.
How can TU-1300E substrate help improve the performance of electronic devices?
By efficiently dissipating heat, maintaining signal integrity, and enhancing mechanical durability, TU-1300E substrate contributes to improving the overall performance, надёжность, and longevity of electronic devices and systems.
What factors should be considered when designing with TU-1300E substrate?
Design considerations include thermal management, dimensional stability, Целостность сигнала, механическая прочность, manufacturability, environmental resilience, and cost-effectiveness.