RF Substrate Изготовитель
Производитель радиочастотных подложек,RF substrates are specialized materials used in the manufacturing of radio frequency (РФ) circuit boards, which are essential for transmitting and receiving signals in wireless communication devices. These substrates are designed to offer excellent electrical properties, such as low dielectric loss and stable dielectric constant, ensuring minimal signal loss and high efficiency. RF substrates also possess good thermal stability and are capable of handling high frequencies, making them suitable for applications in wireless communication, satellite systems, радар, and more. Their unique properties make them critical in ensuring the performance and reliability of high-frequency electronic devices.
Что такое RF Substrate?
RF substrates are specialized materials used in the fabrication of RF (radio frequency) circuit boards and components. These substrates are designed to support high-frequency electronic signals, which are crucial in various applications such as wireless communication, satellite systems, radar technology, и микроволновые цепи.
The primary function of an RF substrate is to provide a stable and reliable platform for the transmission and reception of high-frequency signals. To achieve this, RF substrates are engineered with specific properties that minimize signal loss and distortion. Key characteristics of RF substrates include low dielectric loss, high thermal stability, and precise dielectric constant control. These properties are essential for maintaining signal integrity and performance at high frequencies.
Common materials used for RF substrates include ceramic-based materials, such as alumina and beryllia, as well as advanced polymers like PTFE (polytetrafluoroethylene) and epoxy-based composites. Each material offers distinct advantages depending on the application’s requirements, such as thermal management, Электрические характеристики, and mechanical stability.
In addition to material properties, the design of RF substrates involves careful consideration of factors like layer thickness, trace routing, and impedance control. The goal is to ensure that the substrate can handle the specific frequency ranges and power levels required for the intended application, while minimizing losses and interference.
Полный, RF substrates play a critical role in enabling the efficient and reliable operation of high-frequency electronic systems, making them a vital component in modern communication and electronic technologies.
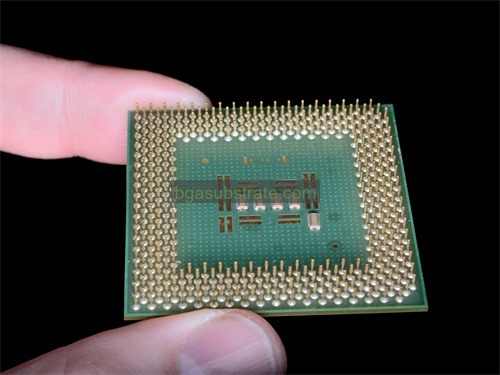
Производитель радиочастотных подложек
Что такое RF Substrate Рекомендации по проектированию?
RF substrate design guidelines are critical for ensuring optimal performance and reliability in high-frequency electronic circuits. Here are the key considerations:
- Material Selection: Choose substrates with low dielectric constant (Dk) and low loss tangent (Df) to minimize signal attenuation and maintain signal integrity at high frequencies. Common materials include PTFE (например., Rogers RO4000 series), ceramics (например., глинозем, aluminum nitride), and advanced laminates. Ensure the chosen material matches the frequency range and thermal requirements of the application.
- Dielectric Constant: Maintain a consistent dielectric constant across the substrate to ensure predictable impedance and signal behavior. Variations in Dk can lead to signal reflections, loss, and impedance mismatches. Select materials with stable Dk values and verify them with accurate measurements.
- Loss Tangent: Minimize signal loss by selecting substrates with a low loss tangent. A lower loss tangent reduces the amount of signal energy lost as heat, which is particularly important for high-frequency applications. Check the material specifications and performance in the desired frequency range.
- Thickness and Layer Structure: Design the substrate thickness and layer stack-up to control impedance and signal propagation. The thickness should be chosen to achieve the desired impedance and to support the mechanical and thermal requirements of the design. For multilayer designs, ensure proper alignment and bonding of layers to avoid performance degradation.
- Управление температурным режимом: Consider the thermal conductivity of the substrate material to manage heat dissipation effectively. High-power RF circuits generate significant heat, which must be efficiently conducted away from sensitive components. Materials with high thermal conductivity, like ceramics, can help manage heat more effectively.
- Fabrication Tolerances: Account for fabrication tolerances in the design to ensure that dimensions, layer alignments, and features are within acceptable limits. Tight tolerances are crucial for high-frequency applications to maintain impedance control and signal integrity.
- Electromagnetic Compatibility (EMC):Design the substrate to minimize electromagnetic interference (EMI) and maintain electromagnetic compatibility. This includes proper grounding, shielding, and layout practices to prevent unwanted signal coupling and cross-talk between circuits.
- Тестирование и валидация: Perform thorough testing and validation of the substrate and the final circuit to ensure that it meets the required specifications and performance criteria. This includes measuring impedance, signal loss, and other critical parameters under operational conditions.
By adhering to these guidelines, designers can ensure that RF substrates contribute to the reliable and efficient operation of high-frequency electronic systems, enhancing performance and minimizing issues related to signal integrity and thermal management.
Преимущества RF Substrate
RF substrates offer several advantages that make them essential for high-frequency and wireless communication applications. Here are the key benefits:
- Low Signal Loss: RF substrates are designed with low dielectric loss and low loss tangent properties, which minimize signal attenuation. This is crucial for maintaining signal integrity and ensuring efficient transmission of high-frequency signals.
- High Frequency Performance: Materials used in RF substrates, such as PTFE and advanced ceramics, provide stable electrical properties at high frequencies. This enables reliable operation in applications that require precise signal transmission and reception, such as RF communication systems and radar.
- Термическая стабильность: RF substrates often have excellent thermal stability, which helps in managing heat generated by high-power RF components. Materials like ceramics offer high thermal conductivity, aiding in effective heat dissipation and preventing thermal damage to the circuit.
- Управление импедансом: RF substrates allow for precise control of impedance, which is critical for minimizing signal reflections and ensuring proper signal transmission. Consistent impedance across the substrate helps maintain signal integrity and performance.
- Mechanical Robustness:Many RF substrates, especially ceramics, provide excellent mechanical strength and durability. This robustness helps the substrate withstand physical stress and environmental conditions, contributing to the longevity and reliability of the RF circuit.
- Design Flexibility: Advanced RF substrates enable the design of compact and efficient high-frequency circuits. With options for multilayer configurations and integration of passive components, designers can create sophisticated circuits with improved performance and reduced size.
- Reduced Crosstalk: The properties of RF substrates help in minimizing crosstalk and electromagnetic interference (EMI) between different circuit elements. This is important for maintaining the integrity of signal paths and reducing noise in sensitive applications.
- Consistent Performance: RF substrates offer consistent performance characteristics over a wide range of frequencies and operating conditions. This reliability is crucial for applications that demand high precision and stable operation, such as communication systems and aerospace technologies.
- Enhanced Signal Integrity: The high-quality materials used in RF substrates support enhanced signal integrity by reducing signal loss and distortion. This ensures clear and accurate signal transmission, which is vital for high-frequency applications.
Полный, RF substrates provide essential benefits for high-frequency circuit design, enabling efficient and reliable performance in a wide range of advanced electronic and communication systems. Their specialized properties and advantages make them a critical component in modern technology.
Что такое RF Substrate Процесс изготовления?
The RF substrate fabrication process involves several steps to produce high-quality substrates for high-frequency applications. Here’s a detailed overview:
- Material Selection and Preparation: Choose the appropriate substrate material based on the desired electrical, термический, и механические свойства. Common materials include PTFE (например., Rogers RO4000 series), ceramics (например., глинозем, aluminum nitride), and advanced laminates. The material is prepared in forms such as sheets or tapes, and may require pre-treatment to ensure proper adhesion and processing.
- Расслоение: For multilayer substrates, the lamination process involves bonding multiple layers of substrate material together. This is typically done using a combination of heat and pressure to ensure strong adhesion between layers. The layers are aligned precisely to maintain uniformity and control impedance.
- Patterning and Etching: The next step is to define the circuit patterns on the substrate. This involves applying a photoresist layer to the substrate, which is then exposed to UV light through a mask to create the desired pattern. The exposed photoresist is developed, and the underlying substrate material is etched away using chemical or plasma etching techniques. This process creates the necessary conductive paths and features on the substrate.
- Plating and Metallization: After patterning, the exposed areas of the substrate are plated with metal to form conductive traces. Common plating methods include electroplating and sputtering. This step adds the necessary metal layers for electrical connections and component mounting.
- Drilling and Via Formation:If the design includes vias (vertical electrical connections between layers), the substrate is drilled using precision equipment. Vias are then plated with metal to establish electrical connections between different layers of the substrate.
- Cleaning and Inspection: The substrate is thoroughly cleaned to remove any residues from the previous fabrication steps. Inspection is conducted to ensure that the substrate meets quality standards and that the circuit patterns, металлизация, and vias are correctly formed. This step often involves both visual and automated inspections.
- Тестирование и валидация: The fabricated substrates undergo electrical testing to verify that they meet the required performance specifications. Tests may include impedance measurements, signal loss analysis, and other electrical properties assessments.
- Cutting and Routing: The final substrates are cut to the desired size and shape based on the specific application requirements. Routing may also be performed to create slots or cutouts needed for mounting components or connectors.
- Final Assembly and Integration: The finished substrates are assembled into the final product. This may involve attaching components, connectors, or other elements required for the completed RF circuit. Final assembly ensures that the substrate integrates seamlessly with the rest of the electronic system.
- Packaging and Shipping: The completed RF substrates are packaged to protect them during transportation and shipping. Proper packaging ensures that the substrates arrive at their destination in good condition, ready for use in high-frequency applications.
By following these steps, manufacturers can produce RF substrates that meet the stringent requirements for high-frequency and high-performance electronic systems, ensuring reliability and efficiency in their applications.
Применение керамики RF Substrate
Ceramic RF substrates are used extensively in high-frequency and high-power electronic applications due to their superior electrical, термический, и механические свойства. Here are the key applications of ceramic RF substrates:
- High-Frequency Circuits: Ceramic RF substrates are ideal for high-frequency applications due to their low dielectric constant (Dk) and low loss tangent (Df). These properties minimize signal loss and distortion, making them suitable for use in RF communication systems, including cellular, satellite, and radar systems.
- Microwave Devices: Ceramics are used in the fabrication of microwave devices such as filters, oscillators, и усилители. The stable electrical properties of ceramic substrates ensure reliable operation at microwave frequencies, which are critical for applications like microwave communication and radar.
- Power Amplifiers: In high-power RF applications, ceramic substrates are preferred due to their excellent thermal conductivity. They help dissipate heat generated by power amplifiers, preventing overheating and ensuring stable performance. Ceramics such as aluminum nitride (AlN) are commonly used in these applications.
- Аэрокосмическая и оборонная промышленность: Ceramic RF substrates are used in aerospace and defense systems where reliability and performance are paramount. Their ability to operate effectively under extreme environmental conditions and high power levels makes them suitable for use in avionics, missile systems, and satellite communications.
- Электроника: In consumer electronics, ceramic RF substrates are employed in devices such as smartphones, Таблетки, and wireless routers. Their low signal loss and high-frequency performance contribute to efficient wireless communication and high data transfer rates.
- Automotive Applications: Ceramic substrates are used in automotive RF systems, including radar sensors for advanced driver assistance systems (АДАС). Their durability and ability to operate in harsh environments make them well-suited for automotive applications where reliability and performance are critical.
- Медицинские приборы: In medical technology, ceramic RF substrates are used in imaging systems, such as MRI machines, and in other high-frequency medical devices. Their stability and performance at high frequencies support accurate imaging and diagnostic capabilities.
- Промышленное оборудование: Ceramic substrates are also used in industrial RF equipment, including RF heating systems and communication devices used in manufacturing processes. Their robust properties and high-frequency performance contribute to the efficiency and reliability of industrial applications.
- RFID Systems: Ceramic substrates are used in Radio Frequency Identification (RFID) tags and readers. Their ability to operate at various frequencies and their durability make them suitable for RFID applications in logistics, inventory management, and access control.
- Passive Components: Ceramic substrates are used in the production of passive components such as capacitors, inductors, and resistors. These components are essential for various RF and microwave circuits and benefit from the stable electrical properties and low signal loss of ceramic materials.
Резюме, ceramic RF substrates are essential for a wide range of high-frequency and high-power applications. Their unique properties, including low signal loss, высокая теплопроводность, and mechanical robustness, make them a preferred choice for demanding electronic and communication systems.
Часто задаваемые вопросы о RF Substrate
What is an RF substrate?
An RF substrate is a material used to support and insulate electronic components in radio frequency (РФ) и микроволновые цепи. It is designed to minimize signal loss and maintain signal integrity at high frequencies.
Why are low dielectric constant (Dk) and low loss tangent (Df) important for RF substrates?
Low dielectric constant and low loss tangent are crucial because they reduce signal attenuation and loss, ensuring efficient transmission and reception of high-frequency signals with minimal distortion.
What materials are commonly used for RF substrates?
Common materials include PTFE (Политетрафторэтилен), ceramics (например., глинозем, aluminum nitride), and advanced laminates like Rogers’ RO4000 series. Each material offers specific advantages depending on the application.
How does the choice of substrate material affect RF circuit performance?
The choice of substrate material impacts impedance control, signal loss, Управление температурным режимом, and overall circuit reliability. Materials with stable electrical properties and good thermal conductivity enhance circuit performance and durability.
What is the role of thermal management in RF substrates?
Thermal management is essential to dissipate heat generated by high-power RF components. Materials with high thermal conductivity, such as ceramics, help prevent overheating and maintain stable performance.
How are RF substrates fabricated?
The fabrication process typically involves material selection, lamination, patterning, офорт, металлизация, сверление, and testing. These steps ensure precise circuit patterns, electrical connections, and overall substrate quality.