Wire Bond Substrate Manufacturer
Wire Bond Substrate Manufacturer,Wire bond substrates are essential components in semiconductor packaging, used to establish electrical connections between the chip and the substrate through fine wires. This traditional packaging method involves bonding wires, usually made of gold or aluminum, from the chip’s bonding pads to corresponding pads on the substrate. Wire bond substrates provide excellent electrical insulation and mechanical support, ensuring the stability and reliability of the connections. They are widely used in various applications, including integrated circuits, sensors, and microelectromechanical systems (MEMS). Wire bond substrates are valued for their simplicity, cost-effectiveness, and ability to accommodate complex and high-density chip designs, making them a versatile choice in electronic manufacturing.
What is Glass Substrate?
A glass substrate is a type of base material commonly used in the manufacturing of electronic devices and various types of displays. It serves as a foundational layer upon which other materials are applied to create functional electronic components. Glass substrates are valued for their excellent properties such as high thermal stability, optical clarity, and low electrical conductivity, which make them suitable for a range of applications.
In the electronics industry, glass substrates are often used in liquid crystal displays (LCDs) and organic light-emitting diodes (OLEDs) due to their ability to provide a smooth and stable surface for the deposition of thin films. The glass provides a robust and reliable base that can withstand the high temperatures and chemical processes involved in the production of these devices. Additionally, glass substrates are transparent, which is essential for display technologies that require light to pass through.
One of the key advantages of glass substrates is their high thermal resistance, which allows them to operate effectively under varying temperature conditions without deforming or degrading. This property is crucial for electronic devices that experience significant heat during operation.
Glass substrates can be manufactured in various thicknesses and sizes to meet specific requirements, and they are often coated with additional layers to enhance their performance, such as anti-reflective or conductive coatings. The manufacturing process involves precision techniques to ensure that the glass surface is free from defects, which is critical for the reliability and longevity of the final electronic products.
Overall, glass substrates play a vital role in modern electronics, providing a stable and high-performance base for advanced display technologies and other electronic components.
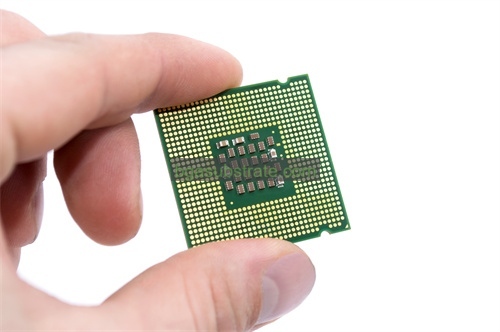
Wire Bond Substrate Manufacturer
What is the Glass Substrate Design Guidelines?
Glass substrate design guidelines are essential for ensuring the successful integration and performance of glass substrates in electronic devices and displays. These guidelines encompass several key aspects to optimize the functionality and reliability of the final product. Here are some important considerations:
- Thickness and Size: The thickness of the glass substrate should be chosen based on the specific application requirements. Thicker substrates offer higher mechanical strength but may affect the flexibility and weight of the final device. The size of the substrate must also be compatible with the dimensions of the electronic components or display panels being manufactured.
- Surface Quality: The glass surface must be free from defects such as scratches, bubbles, or impurities. High surface quality is critical for achieving good adhesion of thin films and ensuring uniform performance across the substrate. Precision polishing and cleaning processes are used to achieve the required surface finish.
- Thermal Management: Glass substrates should be designed to handle the thermal conditions they will encounter during manufacturing and operation. Proper thermal management involves selecting materials with suitable thermal expansion coefficients and ensuring that the substrate can withstand high temperatures without warping or cracking.
- Optical Properties: For applications involving displays or optical components, the glass substrate must have appropriate optical properties, such as high transparency and minimal distortion. Anti-reflective or anti-glare coatings may be applied to improve optical performance.
- Mechanical Strength: The substrate should possess adequate mechanical strength to support the various layers and components applied to it. This includes resistance to mechanical stress during handling and assembly. Glass with higher mechanical strength can reduce the risk of breakage and ensure durability.
- Chemical Compatibility: The glass substrate must be compatible with the chemical processes used in device manufacturing, such as etching, deposition, and cleaning. It should resist chemical degradation to maintain performance and integrity throughout the production process.
- Adhesion Properties: Proper adhesion between the glass substrate and subsequent layers (e.g., coatings, thin films) is crucial for device performance. The substrate surface may be treated or coated to enhance adhesion and ensure reliable layer bonding.
- Design for Manufacturing: Considerations for ease of handling, processing, and integration into manufacturing workflows should be included. This involves designing substrates that are compatible with existing equipment and processes.
By adhering to these design guidelines, manufacturers can ensure that glass substrates perform effectively and meet the quality standards required for modern electronic devices and displays.
The advantages of Glass Substrate
Glass substrates offer several significant advantages in electronic and display applications, making them a popular choice for various technologies. Here are some key benefits:
- High Optical Clarity: Glass substrates provide excellent optical transparency, which is crucial for display technologies such as LCDs and OLEDs. Their clarity ensures that images and colors are displayed accurately without distortion, making them ideal for high-resolution screens and optical applications.
- Thermal Stability: Glass substrates exhibit high thermal resistance, allowing them to withstand significant temperature variations without deforming or degrading. This property is essential for maintaining performance and reliability in devices that generate heat during operation.
- Chemical Durability: Glass substrates are resistant to many chemicals and solvents used during manufacturing processes, including etching and cleaning. This durability helps maintain the integrity and performance of the substrate throughout production and use.
- Mechanical Strength: Glass substrates offer strong mechanical support, providing a stable base for the deposition of thin films and other layers. They are robust enough to handle the stresses of manufacturing and assembly, reducing the risk of breakage and ensuring long-term durability.
- Surface Smoothness:The smooth surface of glass substrates contributes to the even application of coatings and thin films, which is essential for achieving uniform performance across electronic and display devices. High surface quality also minimizes defects that could affect the device’s functionality.
- Low Electrical Conductivity: Glass substrates have low electrical conductivity, making them suitable for use in electronic components where insulating properties are required. This characteristic helps prevent interference and ensures proper functioning of electronic circuits.
- Versatility: Glass substrates can be manufactured in various sizes, shapes, and thicknesses to meet specific application needs. Their versatility allows for customization and adaptation to different technological requirements.
- Recyclability: Glass is a recyclable material, which aligns with environmentally friendly practices. Recycling glass substrates reduces waste and supports sustainable manufacturing processes.
- Anti-Reflective Properties: Glass substrates can be coated with anti-reflective layers to improve optical performance by reducing glare and reflections. This feature enhances the visual quality of displays and optical components.
- Precision Fabrication: The ability to fabricate glass substrates with high precision enables the production of advanced electronic and display devices. Accurate manufacturing ensures that substrates meet stringent specifications and quality standards.
Overall, glass substrates provide a range of benefits that contribute to the performance, durability, and functionality of electronic devices and displays, making them a preferred choice in many high-tech applications.
What is the Glass Substrate Fabrication Process?
The fabrication process for glass substrates involves several key steps to ensure the production of high-quality, reliable materials for use in electronic devices and displays. Here’s an overview of the typical glass substrate fabrication process:
- Raw Material Selection: The process begins with selecting high-purity raw materials, such as silica sand, soda ash, and limestone. These materials are carefully chosen for their ability to produce glass with the desired properties.
- Melting: The raw materials are mixed and melted in a furnace at extremely high temperatures (typically around 1,500°C to 1,600°C). This melting process forms a molten glass, which must be homogeneous and free from impurities to ensure the quality of the final substrate.
- Forming: The molten glass is then formed into sheets or other desired shapes. This can be done using various techniques, such as float glass, where the molten glass is floated on a bed of molten tin to create a smooth, even surface. Alternatively, the glass can be drawn into sheets or rolled into large, continuous ribbons.
- Annealing: After forming, the glass undergoes an annealing process in a controlled environment. This involves slowly cooling the glass to relieve internal stresses and ensure uniform thickness and strength. The annealing process helps prevent warping or cracking during subsequent processing.
- Cutting and Shaping:Once cooled and annealed, the glass sheets are cut into smaller pieces or shapes according to the specifications of the end product. Precision cutting ensures that the substrates meet the required dimensions and tolerances.
- Surface Cleaning: The glass substrates are thoroughly cleaned to remove any contaminants, dust, or residues. This step is crucial for achieving a high-quality surface that will support the proper adhesion of coatings and thin films.
- Surface Treatment: Depending on the application, the glass substrate may undergo additional surface treatments. These treatments can include polishing to achieve a smooth finish, coating with anti-reflective or conductive layers, or other modifications to enhance performance.
- Inspection and Quality Control: The glass substrates are inspected for defects and quality assurance. This includes checking for surface imperfections, thickness uniformity, and adherence to specifications. Advanced inspection techniques, such as optical and mechanical testing, ensure that the substrates meet the required standards.
- Packaging: Once the glass substrates have passed inspection, they are carefully packaged to prevent damage during transportation and handling. Proper packaging protects the substrates from contamination and physical damage.
- Integration into Devices: Finally, the glass substrates are integrated into electronic devices or displays. This involves applying additional layers, such as thin films or electronic components, and assembling the substrates into finished products.
By following these fabrication steps, manufacturers can produce high-quality glass substrates that meet the demanding requirements of modern electronic and display technologies. Each stage of the process is carefully controlled to ensure the performance, durability, and reliability of the final products.
The application of ceramic Glass Substrate
Ceramic glass substrates are advanced materials that combine the properties of ceramics and glass to offer unique advantages for various applications. Here are some key applications of ceramic glass substrates:
- Electronic Devices: Ceramic glass substrates are used in a range of electronic devices due to their excellent electrical insulating properties and thermal stability. They serve as the base material for components such as integrated circuits, sensors, and capacitors, providing a stable platform for high-performance electronic systems.
- Display Technologies: In display technologies, such as liquid crystal displays (LCDs) and organic light-emitting diodes (OLEDs), ceramic glass substrates are valued for their optical clarity and smooth surface. They provide a reliable and high-quality base for the deposition of thin films and other layers essential for high-resolution and high-performance displays.
- Solar Panels: Ceramic glass substrates are employed in the production of solar panels, particularly in the manufacture of thin-film photovoltaic cells. Their thermal resistance and durability help to enhance the efficiency and longevity of solar panels, making them suitable for harsh environmental conditions.
- Telecommunications: In telecommunications, ceramic glass substrates are used in the production of high-frequency and millimeter-wave devices. Their low dielectric loss and high thermal conductivity are beneficial for high-speed data transmission and signal processing, contributing to the performance of communication systems.
- Optical Components: Ceramic glass substrates are used in the fabrication of various optical components, such as lenses, prisms, and optical filters. Their excellent optical properties and resistance to environmental factors make them ideal for precise optical applications in imaging and sensing systems.
- Automotive Applications: In the automotive industry, ceramic glass substrates are used in advanced driver-assistance systems (ADAS) and other electronic components. Their high thermal stability and durability ensure reliable performance in demanding automotive environments.
- Medical Devices: Ceramic glass substrates are employed in medical devices and equipment, such as diagnostic sensors and imaging systems. Their biocompatibility, electrical insulating properties, and resistance to chemical corrosion make them suitable for use in medical applications requiring high precision and reliability.
- Military and Aerospace: In military and aerospace applications, ceramic glass substrates are used for high-reliability components, including radar systems, satellite communications, and advanced avionics. Their robustness, thermal stability, and resistance to extreme conditions are essential for ensuring the performance and durability of critical systems.
- Consumer Electronics: Ceramic glass substrates are also used in various consumer electronics, such as smartphones, tablets, and wearables. Their combination of mechanical strength, optical clarity, and thermal management contributes to the overall performance and aesthetics of these devices.
Overall, ceramic glass substrates provide a range of benefits, including high thermal and electrical stability, optical clarity, and mechanical strength, making them suitable for diverse and demanding applications across multiple industries.
FAQs about Glass Substrate
What is a glass substrate?
A glass substrate is a flat, typically thin piece of glass used as a base material in various electronic devices, displays, and optical components. It provides a stable and smooth surface for the application of other materials or layers.
What are the common uses of glass substrates?
Glass substrates are commonly used in electronic displays (LCDs, OLEDs), optical components (lenses, filters), solar panels, telecommunications devices, and various consumer electronics.
Why is glass used as a substrate?
Glass is used because of its excellent optical clarity, thermal stability, chemical durability, and mechanical strength. These properties make it ideal for applications requiring high performance and reliability.
How is a glass substrate manufactured?
The manufacturing process involves melting raw materials, forming the glass into sheets or shapes, annealing to relieve stresses, cutting to size, and then cleaning and treating the surface as needed.
What are the key properties of glass substrates?
Key properties include high optical transparency, thermal resistance, chemical durability, mechanical strength, and low electrical conductivity.
Can glass substrates be customized?
Yes, glass substrates can be customized in terms of size, thickness, surface finish, and optical properties to meet specific application requirements.