TU-943N Substrate Manufacturer
TU-943N Substrate Manufacturer,TU-943N substrate is a high-performance laminate engineered for advanced RF and microwave applications. It features a low dielectric constant and low loss tangent, which contribute to superior signal integrity and minimal signal loss, making it ideal for high-frequency circuits. The substrate is designed for excellent thermal stability and low moisture absorption, ensuring reliability in challenging environments. Its properties allow for fine-line processing, supporting complex multilayer designs and high-density interconnects. TU-943N is widely used in telecommunications, aerospace, and automotive industries, providing a dependable solution for engineers seeking optimal performance in their electronic systems.
What is TU-943N Substrate?
TU-943N substrate is a high-performance circuit substrate primarily used for high-frequency and high-temperature applications. This substrate is typically made from polyimide materials, which offer excellent electrical properties and thermal stability, enabling it to maintain performance in harsh environments.
The dielectric constant of TU-943N is relatively low, usually ranging from 3.0 to 3.5, which effectively reduces signal loss and delay in high-frequency signal transmission. Additionally, the substrate has a high thermal conductivity, allowing for rapid heat dissipation, thus enhancing the overall reliability and performance of the circuit.
The processing characteristics of this substrate are favorable, making it suitable for the manufacture of fine lines and supporting miniaturization design requirements. The surface treatment of TU-943N is relatively straightforward, compatible with various PCB processes such as gold plating and tin plating, meeting diverse customer needs.
In practical applications, TU-943N substrates are widely used in wireless communication, RF devices, satellite communications, radar systems, and various high-frequency electronic devices. As electronic devices trend toward higher frequency, speed, and miniaturization, the demand for this substrate continues to grow.
Overall, TU-943N substrates play an important role in the high-tech industry, thanks to their outstanding electrical performance and good processing characteristics, meeting modern electronic products’ requirements for high-performance materials.
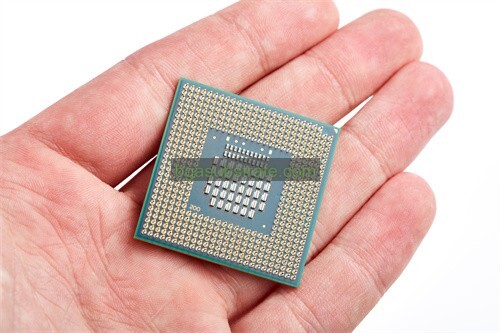
TU-943N Substrate Manufacturer
What is the TU-943N Substrate Design Guidelines?
The design guidelines for the TU-943N substrate typically include the following key considerations:
- Layer Stack-Up: Define the appropriate layer configuration based on the specific application requirements. Consider the use of ground planes and signal layers to optimize performance.
- Trace Width and Spacing: Determine the trace width and spacing based on the substrate’s dielectric properties and the desired impedance. Use appropriate calculators to ensure signal integrity, especially for high-frequency applications.
- Via Design: Select via types (through-hole, blind, or buried) based on the layer configuration. Ensure adequate pad sizes and annular rings to maintain reliability.
- Thermal Management: Incorporate thermal vias or other cooling methods to dissipate heat effectively, especially in high-power applications.
- Surface Treatment: Choose surface finishes compatible with the manufacturing process and the application environment, such as ENIG (Electroless Nickel Immersion Gold) or OSP (Organic Solderability Preservative).
- Mechanical Considerations: Account for the thermal expansion characteristics of the TU-943N material during the design phase to prevent stress and warping.
- Testing and Validation: Plan for appropriate electrical and thermal testing during the prototype phase to ensure compliance with performance specifications.
- DFM (Design for Manufacturing): Ensure that the design adheres to best practices for manufacturability, minimizing complex geometries that could complicate fabrication.
By following these guidelines, designers can optimize the performance and reliability of circuits built on TU-943N substrates.
The advantages of TU-943N Substrate
TU-943N is a high-performance PCB substrate material commonly used in various advanced electronic applications. Here are some key advantages of TU-943N substrates:
- High Thermal Conductivity: TU-943N offers excellent thermal conductivity, which helps in efficiently dissipating heat generated by high-power components. This is crucial for maintaining performance and reliability in demanding applications.
- Low Dielectric Loss: The substrate provides low dielectric loss, which contributes to improved signal integrity and reduced signal attenuation, making it suitable for high-frequency applications.
- Stable Electrical Properties: TU-943N maintains stable electrical properties across a wide frequency range, ensuring consistent performance in both high-speed and high-frequency circuits.
- Thermal Stability: The substrate has good thermal stability, which means it can withstand high temperatures without significant degradation of its electrical and mechanical properties.
- Mechanical Strength: TU-943N substrates offer strong mechanical support, enhancing the durability and reliability of the PCB, especially in environments where mechanical stress is a factor.
- Compatibility with Lead-Free Soldering: This substrate material is compatible with lead-free soldering processes, aligning with modern environmental and regulatory standards.
- Versatility: TU-943N can be used in a variety of applications, including RF/microwave circuits, power electronics, and high-frequency digital applications, due to its balanced performance characteristics.
Overall, TU-943N substrates are well-regarded for their combination of thermal, electrical, and mechanical properties, making them a popular choice for advanced PCB designs.
What is the TU-943N Substrate Fabrication Process?
The fabrication process for TU-943N substrates involves several key steps to ensure high-quality performance and reliability. Here’s a general overview of the process:
- Material Preparation: The TU-943N substrate material, typically a ceramic-based or composite material with high thermal conductivity and low dielectric loss, is prepared in the form of sheets or rolls.
- Lamination: The substrate material is laminated with copper foils using a high-pressure lamination process. This involves heating the material and applying pressure to bond the copper to the substrate.
- Etching: After lamination, the copper layers are patterned using an etching process. This involves applying a photoresist layer to the copper, exposing it to UV light through a mask, and then developing the pattern. The exposed copper is etched away, leaving the desired circuit pattern on the substrate.
- Drilling: Holes are drilled into the substrate for vias and component leads. This is typically done using laser or mechanical drilling techniques to ensure precision and alignment.
- Plating: The drilled holes are plated with a thin layer of copper to create electrical connections between different layers of the PCB. This step involves electroplating the holes with copper to provide conductivity.
- Solder Mask Application: A solder mask is applied over the copper traces to protect them from soldering and prevent short circuits. The solder mask is then cured to harden it.
- Silkscreen Printing: Component labels, markings, and other identifiers are printed onto the substrate using a silkscreen process. This provides visual guidance for assembly and troubleshooting.
- Inspection and Testing: The fabricated substrates undergo rigorous inspection and testing to ensure they meet quality standards. This includes visual inspection, electrical testing, and thermal testing to verify performance and reliability.
- Cutting and Finishing: Finally, the substrates are cut to the desired size and shape. Any additional finishing processes, such as edge plating or additional surface treatments, are performed as needed.
- Packaging: The completed substrates are packaged and prepared for shipment to customers or for further assembly into electronic devices.
Each step in the fabrication process is carefully controlled to ensure that the TU-943N substrates meet the high performance and reliability standards required for advanced electronic applications.
The application of ceramic TU-943N Substrate
Ceramic TU-943N substrates are used in various advanced electronic applications due to their exceptional thermal and electrical properties. Here are some key applications:
- High-Frequency RF/Microwave Circuits: The low dielectric loss and stable electrical properties of TU-943N make it ideal for high-frequency RF and microwave applications, including antennas, filters, and amplifiers.
- Power Electronics: The high thermal conductivity of TU-943N helps in managing heat dissipation in power electronic devices, such as power amplifiers, converters, and inverters, improving their performance and reliability.
- Automotive Electronics:In automotive applications, TU-943N substrates are used in components that require high thermal management and durability, such as engine control units (ECUs), powertrain controllers, and high-power sensors.
- Telecommunications: The substrate is used in telecommunications equipment, including base stations and communication transceivers, where high-frequency performance and heat dissipation are critical.
- Aerospace and Defense: TU-943N is utilized in aerospace and defense applications for its ability to withstand extreme environmental conditions while maintaining high electrical performance. This includes radar systems, communication systems, and avionics.
- Medical Devices:In medical electronics, TU-943N substrates are used in devices that require precision and reliability, such as imaging systems, diagnostic equipment, and implantable devices.
- Consumer Electronics: The substrate can be found in high-performance consumer electronics, such as smartphones, tablets, and gaming consoles, where high-speed and high-frequency performance is essential.
- Test and Measurement Equipment: TU-943N substrates are used in test and measurement instruments where accurate signal transmission and thermal management are crucial for precise measurements and reliable operation.
Overall, the ceramic TU-943N substrate’s excellent thermal conductivity, low dielectric loss, and stable electrical properties make it suitable for a wide range of demanding applications.
FAQs about TU-943N Substrate
What is TU-943N?
TU-943N is a high-performance ceramic PCB substrate known for its excellent thermal conductivity, low dielectric loss, and stable electrical properties.
What are the primary applications of TU-943N?
TU-943N is used in high-frequency RF/microwave circuits, power electronics, automotive electronics, telecommunications, aerospace and defense, medical devices, consumer electronics, and test and measurement equipment.
What are the key advantages of TU-943N substrates?
Key advantages include high thermal conductivity, low dielectric loss, thermal stability, mechanical strength, and compatibility with lead-free soldering.
How does TU-943N compare to other substrates?
Compared to other substrates, TU-943N offers superior thermal management and electrical performance, making it ideal for high-frequency and high-power applications.
What is the typical fabrication process for TU-943N?
The fabrication process includes material preparation, lamination with copper foils, etching, drilling, plating, solder mask application, silkscreen printing, inspection, and final cutting.
Can TU-943N substrates be used in high-temperature environments?
Yes, TU-943N has good thermal stability and can withstand high temperatures, making it suitable for high-temperature applications.
Is TU-943N compatible with lead-free soldering processes?
Yes, TU-943N is compatible with lead-free soldering processes, aligning with modern environmental and regulatory standards.