TU-901 Substrate Manufacturer
TU-901 Substrate Manufacturer,TU-901 substrate is a cutting-edge laminate specifically designed for high-frequency and high-speed electronic applications. Known for its low dielectric constant and low loss tangent, TU-901 ensures superior signal integrity, making it ideal for RF and microwave circuits. The substrate exhibits excellent thermal stability and low moisture absorption, enhancing reliability under various environmental conditions. Its advanced material properties allow for fine-line processing, facilitating complex multilayer designs and high-density interconnects. TU-901 is widely utilized in telecommunications, aerospace, and automotive industries, providing engineers with a robust solution that meets the demanding performance requirements of modern electronic systems.
What is TU-901 Substrate?
The TU-901 substrate is a high-performance circuit board material widely used in high-frequency electronic devices and radio frequency (RF) circuits. Its main features include excellent dielectric properties and low loss characteristics, making it effective for high-frequency signal transmission. The TU-901 substrate is typically made from polymers such as polytetrafluoroethylene (PTFE), which offers a high dielectric constant and good thermal stability, allowing it to maintain excellent electrical performance even in extreme environments.
Additionally, the TU-901 substrate exhibits outstanding chemical resistance, enabling it to withstand various chemical solvents, making it suitable for a range of industrial applications, including aerospace, automotive electronics, and communication devices. Its low thermal expansion coefficient helps minimize deformation of the circuit board during temperature fluctuations, thereby enhancing the reliability of components.
In the manufacturing process, TU-901 substrates are typically produced using advanced printed circuit technologies, such as thin-film deposition and etching, to achieve complex circuit designs. The processing and assembly techniques for this substrate are relatively mature, allowing for high precision and density in design. As high-frequency technology continues to evolve, the TU-901 substrate has a promising future and is expected to play an important role in high-tech fields.
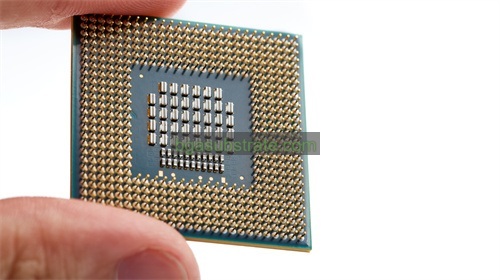
TU-901 Substrate Manufacturer
What is the TU-901 Substrate Design Guidelines?
The design guidelines for the TU-901 substrate typically focus on the following key aspects:
- Layer Stack-Up: Determine the number of layers based on the complexity of the circuit. Ensure proper spacing and alignment to minimize signal loss.
- Trace Width and Spacing: Use appropriate trace widths and spacing to manage impedance, especially for high-frequency applications. Simulation tools can help optimize these parameters.
- Via Design: Utilize microvias or blind/buried vias as needed to maintain signal integrity. Pay attention to via sizes to minimize parasitic inductance and capacitance.
- Ground Planes: Incorporate solid ground planes to reduce electromagnetic interference (EMI) and improve signal return paths.
- Thermal Management: Design for effective heat dissipation by including thermal vias and appropriate copper thickness.
- Material Properties: Consider the dielectric constant and loss tangent of TU-901 for high-frequency applications to ensure optimal performance.
- Manufacturing Considerations: Work closely with manufacturers to understand the limitations and capabilities regarding minimum features, tolerances, and processing techniques.
- Testing and Validation: Plan for thorough testing and validation of prototypes to ensure that the design meets performance specifications.
By adhering to these guidelines, designers can effectively leverage the advantages of the TU-901 substrate for high-performance applications.
The advantages of TU-901 Substrate
The TU-901 substrate offers several advantages:
- High Dielectric Constant: This enables better signal integrity, especially in high-frequency applications, allowing for compact circuit designs.
- Low Loss Characteristics: Its low loss tangent ensures minimal signal degradation, which is critical for RF and microwave applications.
- Excellent Thermal Stability: TU-901 maintains performance across a wide temperature range, making it suitable for demanding environments.
- Chemical Resistance: The substrate is resistant to various chemicals, enhancing its durability in harsh conditions.
- Low Thermal Expansion: Its low thermal expansion coefficient minimizes warping, ensuring consistent performance and reliability during temperature changes.
- Ease of Fabrication: The material supports advanced manufacturing techniques, allowing for intricate circuit designs and efficient production.
- Reduced EMI: The substrate design can help reduce electromagnetic interference, improving overall system performance.
These advantages make TU-901 an ideal choice for applications in aerospace, automotive, telecommunications, and other high-tech industries.
What is the TU-901 Substrate Fabrication Process?
The TU-901 substrate fabrication process is used in the production of high-performance RF (radio frequency) substrates. It involves several key steps:
- Material Selection: TU-901 typically starts with a high-frequency material such as a ceramic or a high-performance polymer. These materials are chosen for their excellent electrical properties, such as low dielectric loss and high thermal conductivity.
- Lamination:The substrate material is laminated to a copper foil or other conductive layer. This is often done using heat and pressure to ensure a strong bond between the layers.
- Photolithography: A photosensitive film is applied to the surface of the substrate. The design of the circuit is then transferred onto the film using ultraviolet light. This process creates a pattern on the substrate that will guide the subsequent etching process.
- Etching:The exposed areas of the copper foil are etched away to form the desired circuit pattern. This is done using a chemical etching process, where the unwanted copper is removed, leaving behind the circuitry.
- Drilling: Holes are drilled into the substrate where vias (connections between different layers) will be placed. This is usually done using a high-precision drilling machine.
- Plating: The holes are plated with a conductive material, often copper, to establish electrical connections between different layers of the substrate.
- Final Testing and Inspection: The substrate undergoes thorough testing to ensure it meets the required specifications for electrical performance, mechanical properties, and overall quality.
The TU-901 process is designed to produce substrates with high performance in terms of signal integrity and thermal management, making it suitable for advanced RF applications.
The application of ceramic TU-901 Substrate
Ceramic TU-901 substrates are primarily used in high-frequency and high-performance electronic applications due to their excellent electrical and thermal properties. Here are some common applications:
- RF and Microwave Circuits: TU-901 substrates are ideal for RF and microwave circuit boards because they offer low dielectric loss and high thermal conductivity. These properties help in maintaining signal integrity and minimizing signal degradation in high-frequency applications.
- Aerospace and Defense: In aerospace and defense industries, where reliability and performance are critical, TU-901 substrates are used in radar systems, communication devices, and other high-precision equipment. Their ability to handle high power and operate reliably at high frequencies makes them suitable for these demanding environments.
- Telecommunications: TU-901 substrates are used in telecommunications infrastructure, including base stations and satellite communications. The low loss and high-frequency performance ensure efficient signal transmission and reception.
- Automotive:Advanced automotive electronics, such as those used in advanced driver-assistance systems (ADAS) and high-frequency sensors, benefit from the high performance of TU-901 substrates. Their thermal stability and electrical performance are crucial for reliable operation in automotive environments.
- Medical Devices: In medical technology, where precision and reliability are essential, TU-901 substrates are used in high-frequency diagnostic equipment and imaging systems. Their performance ensures accurate readings and reliable operation of medical devices.
Overall, the key advantages of ceramic TU-901 substrates include low dielectric constant, low loss tangent, high thermal conductivity, and high mechanical strength, making them suitable for various demanding applications where high performance is required.
FAQs about TU-901 Substrate
What is TU-901 substrate?
TU-901 is a type of ceramic substrate used in high-frequency and high-performance electronic applications. It is known for its low dielectric loss and high thermal conductivity.
What are the main applications of TU-901 substrates?
They are commonly used in RF and microwave circuits, aerospace and defense systems, telecommunications, automotive electronics, and medical devices.
Why is TU-901 substrate preferred for high-frequency applications?
Due to its low dielectric loss and high thermal conductivity, TU-901 maintains signal integrity and performs reliably at high frequencies.
What materials are used in TU-901 substrates?
TU-901 substrates typically use ceramic materials or high-performance polymers that are engineered for low loss and high thermal performance.
How does the fabrication process work?
The process involves material selection, lamination with copper foil, photolithography to create circuit patterns, etching, drilling, plating, and final testing.
What are the benefits of using TU-901 substrates?
Benefits include excellent signal integrity, thermal management, high mechanical strength, and reliability in demanding environments.
Are TU-901 substrates suitable for all electronic applications?
No, they are specifically suited for high-frequency and high-performance applications where their properties can be fully utilized.