TU-862 HF Substrate Manufacturer
TU-862 HF Substrate Manufacturer,TU-862 HF substrate is a high-performance laminate specifically engineered for high-frequency applications. With its low dielectric constant and low loss tangent, it delivers excellent signal integrity, making it ideal for RF circuits, antennas, and microwave devices. The substrate exhibits high thermal stability and minimal moisture absorption, ensuring reliable performance in various environmental conditions. Its robust mechanical properties support intricate designs and multilayer configurations, facilitating the production of high-density interconnects. TU-862 HF is widely used in telecommunications, automotive, and aerospace industries, where precision and durability are paramount for advanced electronic systems.
What is TU-862 HF Substrate?
The TU-862 HF substrate is a high-frequency material widely used in the manufacturing of radio frequency (RF) and microwave circuits. Its main features include a low dielectric constant and low loss tangent, which ensure excellent performance in high-frequency signal transmission. This substrate is designed to minimize signal attenuation and maintain signal integrity in high-frequency applications.
The dielectric constant of TU-862 HF substrates typically ranges from 2.9 to 3.1, making them suitable for antennas, filters, amplifiers, and other high-frequency circuits. This material is often made from polytetrafluoroethylene (PTFE) or ceramic composites, offering good thermal stability and chemical resistance, enabling it to perform well in harsh operating environments.
During the manufacturing process, precise control of the processing techniques is essential to ensure the fine details and consistency of circuit patterns. Its excellent mechanical properties and good insulation characteristics make it adaptable to various circuit design requirements, providing low phase noise and high frequency stability in high-frequency applications.
In summary, the TU-862 HF substrate is an important component in high-frequency electronic devices, supporting advancements in modern communication, radar, and radio frequency identification (RFID) technologies. It is widely used in military, aerospace, automotive electronics, and consumer electronics fields.
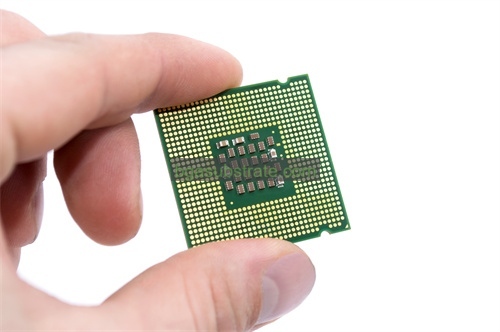
TU-862 HF Substrate Manufacturer
What is the TU-862 HF Substrate Design Guidelines?
The design guidelines for the TU-862 HF substrate typically include the following key points:
- Layer Thickness: Ensure the substrate thickness is appropriate for the specific application, considering factors like impedance control and mechanical stability.
- Trace Width and Spacing: Calculate trace widths and spacing based on the desired characteristic impedance (usually 50 or 75 ohms) using appropriate formulas or design tools.
- Via Design: Use microvias or blind/buried vias as needed, ensuring they are properly placed to minimize inductance and maintain signal integrity.
- Ground and Power Planes: Include solid ground and power planes to reduce noise and improve signal integrity, particularly in high-frequency designs.
- Thermal Management:Consider thermal dissipation requirements, especially in high-power applications. Utilize thermal vias and adequate copper thickness.
- Surface Finish: Select a suitable surface finish (like ENIG or HASL) that provides good solderability and minimizes surface oxidation.
- Layout Considerations: Maintain short and direct signal paths, and use controlled impedance routing for critical high-frequency signals to minimize losses.
- Testing and Prototyping: Plan for testing during the prototype phase to validate performance against specifications, making adjustments as necessary.
By following these guidelines, designers can optimize the performance of circuits utilizing the TU-862 HF substrate for high-frequency applications.
The advantages of TU-862 HF Substrate
The TU-862 HF substrate offers several advantages, particularly for high-frequency applications:
- Low Dielectric Constant: This feature reduces signal propagation delays and enhances performance in RF applications.
- Low Loss Tangent: Minimizes signal loss, making it ideal for high-frequency circuits where signal integrity is critical.
- Thermal Stability: Excellent thermal stability allows it to perform reliably in varying temperatures, ensuring consistent operation.
- Chemical Resistance: The substrate’s resistance to chemicals enhances its durability in harsh environments.
- Good Mechanical Strength: Provides structural integrity, supporting complex designs without compromising reliability.
- Impedance Control:Easily designed to achieve controlled impedance for optimal signal transmission, reducing reflections and losses.
- Versatility: Suitable for various applications, including antennas, filters, amplifiers, and other RF components.
- Ease of Fabrication: Compatible with standard PCB fabrication processes, allowing for efficient production.
These advantages make TU-862 HF substrates an excellent choice for applications in telecommunications, aerospace, automotive, and other high-frequency domains.
What is the TU-862 HF Substrate Fabrication Process?
The fabrication process for TU-862 HF substrates generally involves the following steps:
- Material Preparation: Start with high-quality TU-862 HF laminate sheets, which may include a dielectric layer made from PTFE or ceramic composites.
- Cutting and Sizing: The laminate sheets are cut to the desired dimensions according to the specifications of the PCB design.
- Imaging: Apply a photosensitive film to the substrate surface. This is followed by exposure to ultraviolet (UV) light through a photomask that contains the desired circuit pattern.
- Developing: The exposed substrate is developed, removing the unexposed areas of the photoresist, revealing the copper layer beneath.
- Etching: The substrate is etched using chemical solutions to remove unwanted copper, leaving only the desired circuit pattern.
- Via Drilling: Microvias or traditional vias are drilled into the substrate as required by the design, typically using laser drilling for precision.
- Via Plating: Vias are plated with copper to create electrical connections between layers.
- Surface Finishing: Apply a suitable surface finish (like ENIG or HASL) to enhance solderability and protect against oxidation.
- Testing: Perform electrical tests to ensure circuit integrity and functionality, checking for any manufacturing defects.
- Final Inspection: Conduct a thorough visual and functional inspection before the substrate is ready for assembly into the final product.
This process ensures high-quality TU-862 HF substrates that meet the stringent requirements of high-frequency applications.
The application of ceramic TU-862 HF Substrate
The ceramic TU-862 HF substrate is widely used in various high-frequency applications due to its excellent electrical and thermal properties. Key applications include:
- Antenna Design: Utilized in the fabrication of antennas for telecommunications and satellite communications, where low loss and high stability are crucial.
- RF Filters: Used in RF filter circuits to achieve high selectivity and minimal insertion loss, essential for mobile and wireless communication systems.
- Amplifiers: Employed in RF and microwave amplifiers, where signal integrity and performance at high frequencies are paramount.
- Microwave Circuits: Suitable for a range of microwave circuit applications, including radar and telemetry systems, benefiting from its low dielectric losses.
- Wireless Communication: Integrated into various wireless communication devices, such as cellular and Wi-Fi equipment, to improve signal quality and range.
- Medical Devices: Applied in medical imaging and diagnostic equipment, where reliable high-frequency performance is required.
- Automotive Electronics: Used in automotive radar systems and advanced driver-assistance systems (ADAS) for safety and navigation.
These applications leverage the TU-862 HF substrate’s properties, making it a preferred choice for manufacturers in the RF and microwave industries.
FAQs about TU-862 HF Substrate
What is TU-862 HF substrate made of?
TU-862 HF substrate is typically made from a composite material, often polytetrafluoroethylene (PTFE) or ceramic, designed for high-frequency applications.
What are the key properties of TU-862 HF substrate?
It features a low dielectric constant, low loss tangent, excellent thermal stability, and good chemical resistance, making it suitable for RF and microwave applications.
What applications is TU-862 HF substrate used for?
It is commonly used in antennas, RF filters, amplifiers, microwave circuits, wireless communication devices, and automotive radar systems.
How does the dielectric constant affect performance?
A low dielectric constant helps reduce signal propagation delays and minimizes signal loss, enhancing overall performance in high-frequency circuits.
Can TU-862 HF substrate be fabricated using standard PCB processes?
Yes, it is compatible with conventional PCB fabrication processes, allowing for efficient manufacturing.
What is the typical thickness of TU-862 HF substrate?
The thickness can vary based on specific application requirements, typically ranging from 0.5 mm to several millimeters.
How is the substrate tested for performance?
Electrical tests, including impedance and signal integrity assessments, are conducted to ensure that the substrate meets the necessary specifications.
What surface finishes are recommended for TU-862 HF substrates?
Common surface finishes include Electroless Nickel/Immersion Gold (ENIG) and Hot Air Solder Leveling (HASL), chosen for their solderability and protection against oxidation.
Are there any design considerations when using TU-862 HF substrate?
Yes, it’s essential to account for trace width, spacing, and via placement to maintain controlled impedance and minimize signal loss.