Teflon PCB Manufacturer
Teflon PCB Manufacturer,Teflon PCBs are high-performance circuit boards made from Teflon, a brand name for polytetrafluoroethylene (PTFE). Known for its excellent electrical insulating properties, Teflon provides low dielectric loss and high-frequency stability, making these PCBs ideal for high-frequency and microwave applications. They offer superior performance in environments with high temperatures and harsh conditions due to their chemical resistance and thermal stability. Teflon PCBs are commonly used in aerospace, telecommunications, and high-speed digital applications where signal integrity and minimal signal degradation are critical. Their high performance, combined with durability, makes them a preferred choice for demanding electronic systems.
What is Teflon PCB?
Teflon PCB refers to printed circuit boards (PCBs) that use Teflon as their primary substrate material. Teflon, a trademark of Chemours, is a brand name for polytetrafluoroethylene (PTFE), a high-performance polymer known for its exceptional dielectric properties.
Teflon PCBs are prized for their high-frequency performance and low dielectric constant, making them ideal for high-speed, high-frequency applications. This is particularly crucial in radio frequency (RF) and microwave circuits, where signal integrity and minimal signal loss are essential. The low dielectric constant of Teflon helps in reducing signal attenuation and maintaining high-speed signal transmission with minimal distortion.
One of the key advantages of Teflon PCBs is their excellent thermal stability. Teflon can withstand high temperatures without significant degradation, which is advantageous in applications with fluctuating or high temperatures. Additionally, Teflon has a low coefficient of thermal expansion (CTE), which helps in maintaining dimensional stability under thermal stress.
However, Teflon PCBs are more expensive compared to conventional FR4 PCBs due to the cost of Teflon material and the specialized processing required. Manufacturing Teflon PCBs often involves advanced techniques and precise handling to ensure proper bonding and integration with other circuit components.
Overall, Teflon PCBs are used in applications where high performance and reliability at high frequencies are critical, such as in aerospace, telecommunications, and high-frequency electronics. Despite their higher cost, their superior electrical and thermal properties make them a preferred choice for demanding environments.
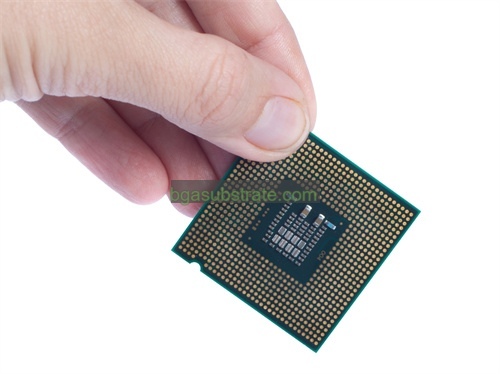
Teflon PCB Manufacturer
What is the Teflon PCB Design Guidelines?
Designing Teflon PCBs requires specific guidelines to ensure optimal performance and reliability due to the unique properties of Teflon (PTFE) as a substrate material. Here are some key design guidelines for Teflon PCBs:
- Signal Integrity: Teflon’s low dielectric constant and loss tangent are beneficial for high-frequency applications. Ensure that signal traces are designed to minimize impedance mismatches and signal reflections. Utilize controlled impedance traces and high-quality connectors to maintain signal integrity.
- Layer Stack-Up:Carefully plan the PCB layer stack-up to manage the distribution of signals and power. Teflon is often used in multi-layer PCBs where precise control over layer spacing is crucial for maintaining signal integrity and reducing cross-talk.
- Trace Width and Spacing: Due to Teflon’s different dielectric properties compared to traditional FR4, trace widths and spacing must be calculated using specialized tools or guidelines that account for the unique characteristics of Teflon. This ensures proper impedance matching and minimizes signal loss.
- Via and Hole Design: Minimize the use of vias and holes where possible, as they can introduce signal loss and affect impedance. When vias are necessary, use high-frequency optimized via designs and consider using plated-through holes or blind/buried vias for better performance.
- Thermal Management: Teflon has good thermal stability, but thermal management remains crucial. Design the PCB with adequate thermal vias and heat sinks if the circuit will experience significant temperature variations or generate substantial heat.
- Manufacturing Considerations: Teflon PCBs require specialized manufacturing processes. Ensure that the PCB manufacturer has experience with Teflon materials and can handle the unique processing requirements, such as bonding and etching.
- Testing and Validation: Due to the high-performance nature of Teflon PCBs, thorough testing and validation are essential. Perform extensive electrical and thermal testing to ensure that the PCB meets design specifications and operates reliably in its intended application.
- Design Software and Tools: Use simulation tools and design software capable of handling high-frequency designs and Teflon-specific characteristics. This helps in accurately predicting performance and avoiding potential design issues.
By adhering to these guidelines, you can optimize the performance of Teflon PCBs for high-frequency and high-speed applications, ensuring reliability and efficiency in demanding environments.
The advantages of Teflon PCB
Teflon PCBs offer several significant advantages, especially for high-frequency and high-performance applications. Here are the key benefits of using Teflon as a PCB substrate:
- Low Dielectric Constant: Teflon has a low dielectric constant, which reduces signal loss and maintains signal integrity at high frequencies. This is crucial for high-speed and RF applications where minimizing signal attenuation is essential.
- Low Loss Tangent: Teflon exhibits a low loss tangent (dissipation factor), which means it has minimal signal attenuation. This characteristic helps in maintaining signal quality and performance over longer distances and at higher frequencies.
- High Thermal Stability: Teflon can withstand high temperatures without significant degradation, making it suitable for applications with fluctuating or elevated temperatures. This thermal stability helps in maintaining the PCB’s performance and structural integrity.
- Excellent Chemical Resistance: Teflon is highly resistant to chemicals and solvents. This property ensures the longevity and durability of PCBs in harsh environments or where exposure to corrosive substances is expected.
- Good Electrical Insulation: Teflon provides excellent electrical insulation properties, reducing the likelihood of electrical interference and cross-talk between traces. This is particularly beneficial in sensitive electronic circuits.
- Stable Electrical Properties: Teflon maintains stable electrical properties over a wide range of temperatures and frequencies. This consistency ensures reliable performance in precision applications such as telecommunications and aerospace.
- Low Moisture Absorption: Teflon’s low moisture absorption prevents changes in dielectric properties due to humidity. This stability is important for maintaining consistent performance in varying environmental conditions.
- High Flexibility in Design: Teflon PCBs can be designed with precise impedance control, enabling the creation of complex, high-performance circuits. This flexibility supports advanced applications such as microwave and RF circuits.
While Teflon PCBs are more expensive and require specialized manufacturing processes, their superior electrical and thermal properties make them highly advantageous for demanding applications where performance and reliability are critical.
What is the Teflon PCB Fabrication Process?
The fabrication process for Teflon PCBs involves several specialized steps due to the unique properties of Teflon (PTFE) as a substrate material. Here’s an overview of the Teflon PCB fabrication process:
- Design and Layout: The design of the PCB is created using specialized CAD software. This includes designing the circuit layout, trace routing, and layer stack-up, considering the unique dielectric properties of Teflon for impedance control and signal integrity.
- Substrate Preparation: Teflon sheets are prepared as the base material for the PCB. Teflon is chosen for its low dielectric constant and high thermal stability. The sheets are cut to the required size and cleaned to remove any contaminants that could affect adhesion and etching.
- Lamination: In multi-layer Teflon PCBs, multiple layers of Teflon are laminated together with prepreg (pre-impregnated resin) layers. The lamination process involves applying heat and pressure to bond the layers together. Due to Teflon’s unique properties, this process must be carefully controlled to ensure proper adhesion.
- Drilling: Holes for vias and through-holes are drilled using precision equipment. Drilling Teflon requires specialized drills to prevent material degradation and ensure clean holes. This step must be performed with high accuracy to maintain signal integrity.
- Copper Plating: A thin layer of copper is applied to the Teflon substrate using an electroplating process. This copper layer forms the circuit traces and pads. Teflon’s low surface energy makes adhesion challenging, so additional steps like surface treatment or roughening may be used to improve copper bonding.
- Patterning and Etching: The copper layer is patterned to create the desired circuit traces. A photoresist layer is applied to the copper, and ultraviolet light is used to transfer the circuit design onto the photoresist. The unexposed photoresist is then removed, and the exposed copper is etched away, leaving the circuit pattern.
- Surface Finish: To protect the copper traces and improve solderability, a surface finish is applied. Common finishes include gold plating, electroless nickel, or immersion tin. This step ensures the PCB’s durability and enhances the performance of solder joints.
- Testing and Inspection: The fabricated Teflon PCB undergoes rigorous testing and inspection to verify that it meets design specifications and performance criteria. Tests may include electrical checks, thermal analysis, and visual inspection to ensure the PCB’s reliability and functionality.
- Cutting and Profiling: The final PCB is cut to the desired shape and size. This may involve routing or sawing the PCB to fit specific enclosures or mounting requirements.
- Final Assembly: The PCB is then assembled with components, soldered, and prepared for use in the final application. This step may include additional processes such as component placement, soldering, and final inspection.
The fabrication of Teflon PCBs requires specialized equipment and techniques due to Teflon’s unique properties. Precise control throughout the process is essential to achieve high performance and reliability in demanding applications.
The application of ceramic Teflon PCB
Ceramic Teflon PCBs combine the high-performance characteristics of ceramic substrates with the exceptional dielectric properties of Teflon (PTFE). These PCBs are used in specialized applications where superior electrical and thermal performance is critical. Here are some key applications of ceramic Teflon PCBs:
- High-Frequency and RF Circuits: Ceramic Teflon PCBs are ideal for radio frequency (RF) and microwave circuits due to their low dielectric constant and loss tangent. These properties minimize signal attenuation and maintain high signal integrity, which is essential for RF communication systems and high-frequency applications.
- Aerospace and Defense: In aerospace and defense industries, where reliability and performance are paramount, ceramic Teflon PCBs are used in satellite communication systems, radar equipment, and other advanced electronic systems. Their thermal stability and low signal loss make them suitable for harsh environments and high-reliability applications.
- Telecommunications: For telecommunications equipment such as base stations, antennas, and communication modules, ceramic Teflon PCBs provide the necessary performance to handle high-speed signals and reduce interference. They are used in both terrestrial and satellite communication systems to ensure reliable data transmission.
- Medical Devices: In medical electronics, such as diagnostic equipment and imaging systems, ceramic Teflon PCBs are utilized for their high precision and low signal loss. Their stability and reliability are crucial for maintaining the accuracy and performance of sensitive medical instruments.
- High-Performance Computing: For high-performance computing systems, including servers and data centers, ceramic Teflon PCBs are employed to manage high-speed data signals and provide efficient thermal management. Their ability to handle high frequencies and dissipate heat makes them suitable for advanced computing applications.
- Automotive Electronics: In automotive applications, particularly in high-frequency communication and advanced driver-assistance systems (ADAS), ceramic Teflon PCBs are used to ensure reliable performance and signal integrity. They help in managing the complex electronic systems found in modern vehicles.
- Test and Measurement Equipment: Ceramic Teflon PCBs are used in test and measurement equipment where accurate and stable signal measurement is critical. Their low signal loss and high-frequency performance make them suitable for precision testing applications.
- Power Amplifiers: In high-power RF and microwave power amplifiers, ceramic Teflon PCBs are used to handle the high-frequency signals and dissipate heat effectively. Their robust electrical and thermal properties contribute to the efficient operation of power amplification systems.
By leveraging the advantages of both ceramic and Teflon materials, ceramic Teflon PCBs provide enhanced performance and reliability for demanding electronic applications. Their ability to handle high frequencies, maintain signal integrity, and withstand harsh environments makes them a valuable choice in advanced technological fields.
FAQs about Teflon PCB
What are the advantages of Teflon PCBs?
Teflon PCBs offer low dielectric constant and low loss tangent, which reduce signal loss and maintain signal integrity. They also have high thermal stability, excellent chemical resistance, and stable electrical properties over a wide range of temperatures and frequencies.
What applications are Teflon PCBs used for?
Teflon PCBs are used in high-frequency and RF circuits, aerospace and defense systems, telecommunications, medical devices, high-performance computing, automotive electronics, test and measurement equipment, and power amplifiers.
How does the fabrication of Teflon PCBs differ from other PCBs?
The fabrication of Teflon PCBs requires specialized processes due to Teflon’s unique properties. This includes precise control in lamination, copper plating, and drilling. Teflon PCBs also need specific handling to ensure proper adhesion and performance.
Are Teflon PCBs more expensive than standard PCBs?
Yes, Teflon PCBs are generally more expensive than standard FR4 PCBs due to the cost of the material and the specialized manufacturing processes involved.
Can Teflon PCBs be used for all types of electronics?
While Teflon PCBs provide superior performance for high-frequency and high-speed applications, they may not be necessary for low-frequency or standard electronics. Their use is typically reserved for applications where their specific advantages are needed.
What are the challenges in designing Teflon PCBs?
Designing Teflon PCBs involves careful consideration of trace width, spacing, and impedance matching due to the material’s unique dielectric properties. Accurate design and simulation are crucial to ensure optimal performance.