Taconic PCB Manufacturer
Taconic PCB Manufacturer,Taconic PCBs are advanced circuit boards made from Taconic materials, which are renowned for their exceptional electrical and thermal properties. Taconic substrates, often composed of PTFE (polytetrafluoroethylene) and other high-performance materials, offer low dielectric loss and high-frequency stability, making them ideal for RF and microwave applications. These PCBs excel in maintaining signal integrity and minimizing signal degradation, even at high frequencies. They are widely used in telecommunications, aerospace, and high-speed digital circuits where reliability and performance are crucial. The combination of high thermal stability, chemical resistance, and superior electrical characteristics makes Taconic PCBs a top choice for demanding electronic systems.
What is Taconic PCB?
Taconic PCB refers to a type of printed circuit board (PCB) that utilizes Taconic’s specialized materials, which are known for their high-performance properties. Taconic is a leading manufacturer of advanced substrate materials, particularly those used in high-frequency and high-speed electronic applications.
Taconic PCBs typically employ materials such as PTFE (polytetrafluoroethylene) and ceramic-filled PTFE composites. These materials are renowned for their excellent dielectric properties, low loss tangents, and high thermal stability. They are particularly useful in applications requiring high-frequency signal transmission, such as microwave and RF (radio frequency) circuits.
The key advantages of Taconic PCBs include their superior electrical performance, which is crucial for maintaining signal integrity and reducing signal loss. The low dielectric constant and loss tangent of Taconic materials help in minimizing signal degradation, making them ideal for high-speed digital and RF applications.
Additionally, Taconic PCBs offer high thermal conductivity and stability, ensuring reliable performance in demanding environments. The materials used can handle high power levels and are resistant to temperature fluctuations, which is important for maintaining PCB performance under various operational conditions.
Overall, Taconic PCBs are a preferred choice for applications in telecommunications, aerospace, and high-speed computing due to their advanced material properties and reliability in high-frequency scenarios.
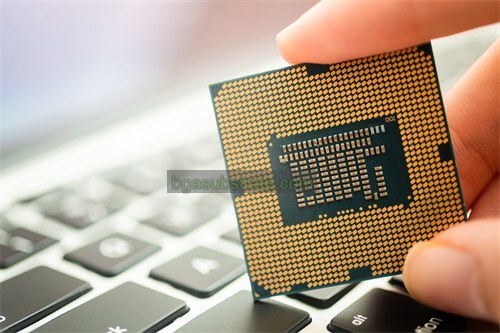
Taconic PCB Manufacturer
What is the Taconic PCB Design Guidelines?
Taconic PCB Design Guidelines are a set of best practices and recommendations tailored to ensure optimal performance and reliability when designing printed circuit boards using Taconic’s advanced substrate materials. These guidelines address the unique properties of Taconic materials, such as PTFE (polytetrafluoroethylene) and ceramic-filled PTFE composites, which are known for their high-frequency and high-speed capabilities.
- Material Selection: Choose the appropriate Taconic material based on the specific application requirements. For high-frequency applications, materials with low dielectric constants and loss tangents are essential. Taconic’s materials are designed to provide excellent signal integrity and minimal signal loss.
- Layer Stack-Up: Design the PCB stack-up with careful consideration of the dielectric thickness and material properties. The stack-up should be optimized to balance impedance control, signal integrity, and thermal management. Ensure that the dielectric layers are consistent and properly aligned to maintain signal performance.
- Impedance Control: Pay close attention to impedance control when designing traces and signal paths. Use appropriate trace widths and spacing to achieve the desired impedance. Taconic materials offer precise impedance control, but it is crucial to model and verify the impedance using simulation tools.
- Thermal Management: Consider thermal management strategies to handle heat dissipation effectively. Taconic materials have high thermal conductivity, which helps in managing heat, but ensure that the PCB design includes sufficient thermal vias and heat sinks where necessary.
- Signal Integrity: Implement design techniques to minimize signal degradation and noise. This includes careful routing of high-speed signals, proper grounding, and minimizing signal reflections. Use ground planes and shielding to enhance signal integrity and reduce electromagnetic interference (EMI).
- Manufacturing Considerations: Follow best practices for manufacturing and assembly processes specific to Taconic materials. Ensure compatibility with standard fabrication techniques and verify that the design adheres to the material’s handling and processing requirements.
- Testing and Validation: Perform thorough testing and validation of the PCB design to ensure that it meets performance specifications. Use simulation tools to model the PCB behavior and conduct physical testing to verify the design under real-world conditions.
By adhering to these guidelines, designers can leverage the advanced properties of Taconic PCB materials to create high-performance and reliable circuit boards for demanding applications.
The advantages of Taconic PCB
Taconic PCBs offer several distinct advantages due to the advanced properties of the materials used in their construction. Here are the key benefits:
- Superior Electrical Performance: Taconic materials, such as PTFE (polytetrafluoroethylene) and ceramic-filled PTFE composites, provide excellent electrical performance. Their low dielectric constants and loss tangents help minimize signal degradation and signal loss, making them ideal for high-frequency and high-speed applications.
- High Thermal Stability: Taconic PCBs are known for their high thermal stability and conductivity. This property allows them to effectively manage heat, maintaining reliable performance even in demanding thermal environments. The materials are designed to withstand high temperatures without degrading, ensuring long-term reliability.
- Impedance Control: The advanced materials used in Taconic PCBs offer precise impedance control, which is crucial for maintaining signal integrity in high-speed and high-frequency circuits. This ensures consistent performance and reduces signal reflections and distortions.
- Low Signal Loss: Taconic substrates have low signal loss characteristics, which is essential for high-speed digital and RF (radio frequency) applications. The low loss tangent of Taconic materials helps in preserving signal quality and achieving better overall system performance.
- Reduced Electromagnetic Interference (EMI): The materials used in Taconic PCBs provide effective shielding against electromagnetic interference. This reduces noise and improves the overall performance of electronic systems, particularly in sensitive RF applications.
- Enhanced Durability: Taconic materials are known for their durability and resistance to mechanical stress. This contributes to the longevity and robustness of the PCB, even in challenging operational conditions.
- Consistency and Reliability:Taconic’s manufacturing processes ensure that their materials maintain consistent properties across different production runs. This consistency helps in achieving reliable and repeatable performance in electronic applications.
- Versatility: Taconic PCBs can be used in a wide range of applications, including telecommunications, aerospace, and automotive industries. Their versatile properties make them suitable for various high-performance and high-reliability applications.
Overall, Taconic PCBs are valued for their high-performance characteristics, thermal stability, and ability to maintain signal integrity in demanding electronic applications.
What is the Taconic PCB Fabrication Process?
The Taconic PCB fabrication process involves several specialized steps tailored to handle the unique properties of Taconic’s advanced substrate materials, such as PTFE (polytetrafluoroethylene) and ceramic-filled PTFE composites. Here’s an overview of the typical fabrication process:
- Material Preparation: Begin with the selection and preparation of Taconic materials. The substrates, such as PTFE laminates, are sourced and prepared according to the specifications of the design. These materials are often supplied in sheets or rolls.
- Layer Cutting and Laminating: Cut the Taconic materials to the required sizes for the PCB layers. The layers are then laminated together using a high-pressure laminator. The laminating process ensures that the layers adhere properly, with uniform pressure and temperature to achieve a strong bond.
- Drilling: Once the laminate is prepared, drill holes for vias and through-holes. Taconic materials, especially PTFE, require specialized drilling equipment due to their unique properties. Precise drilling is crucial for ensuring proper alignment and functionality of the vias.
- Imaging and Etching:Apply a photoresist layer to the surface of the PCB. The circuit pattern is then transferred to the photoresist using a photomask and ultraviolet light. After imaging, the board undergoes etching to remove the unwanted copper, leaving behind the desired circuit pattern. Taconic materials require careful handling during etching to maintain the integrity of the substrate.
- Plating: Plate the drilled holes with copper to create conductive paths. This process, known as electroplating, involves depositing a thin layer of copper onto the interior surfaces of the vias and through-holes. This step ensures electrical connectivity between different layers of the PCB.
- Solder Mask Application: Apply a solder mask layer to protect the copper traces and prevent solder bridging during assembly. The solder mask is typically applied as a liquid coating and then cured. It also helps in reducing the risk of oxidation and contamination.
- Surface Finish:Apply a surface finish to protect the exposed copper areas and enhance solderability. Common surface finishes include HASL (Hot Air Solder Leveling), ENIG (Electroless Nickel/Immersion Gold), and OSP (Organic Solderability Preservative). The choice of finish depends on the specific requirements of the application.
- Testing and Inspection: Perform thorough testing and inspection of the fabricated PCB. This includes electrical testing to verify connectivity, visual inspection for defects, and possibly advanced testing techniques like X-ray inspection for internal structures.
- Cutting and Profiling: Cut the PCB from the larger panel and perform any necessary profiling or routing to achieve the final shape and size of the individual boards.
- Final Assembly: Once the PCB is fabricated, it can be assembled with electronic components. This involves soldering components onto the PCB, either manually or using automated processes such as reflow soldering.
Throughout the fabrication process, it is essential to follow precise procedures and handle Taconic materials with care to maintain their unique properties and achieve high-performance PCBs.
The application of ceramic Taconic PCB
Ceramic Taconic PCBs are used in a variety of high-performance applications due to their exceptional material properties. The use of ceramic-filled Taconic substrates, such as those combining PTFE with ceramic fillers, provides several advantages that are ideal for specific demanding environments. Here are the key applications:
- High-Frequency and RF Circuits: Ceramic Taconic PCBs are particularly well-suited for high-frequency and radio frequency (RF) applications. The low dielectric constant and low loss tangent of ceramic-filled Taconic materials help minimize signal loss and maintain signal integrity at high frequencies, making them ideal for use in RF amplifiers, filters, and antennas.
- Microwave Communications: In microwave communication systems, ceramic Taconic PCBs ensure high performance due to their excellent electrical properties and low signal attenuation. They are used in components such as microwave antennas, transmitters, and receivers, where maintaining signal clarity is critical.
- Aerospace and Defense: The aerospace and defense industries require components that can withstand harsh environments and high temperatures. Ceramic Taconic PCBs provide the necessary thermal stability and mechanical durability, making them suitable for applications in radar systems, satellite communications, and avionics.
- Medical Devices: In medical electronics, where precision and reliability are crucial, ceramic Taconic PCBs offer stable performance and durability. They are used in advanced medical imaging systems, patient monitoring equipment, and other critical medical devices where signal integrity and thermal management are essential.
- High-Power Electronics: The thermal conductivity of ceramic Taconic PCBs makes them suitable for high-power electronics applications. They can handle higher power densities and dissipate heat effectively, which is important for power amplifiers, high-power RF circuits, and other high-power components.
- Automotive Electronics: With the increasing complexity of automotive electronics, including advanced driver-assistance systems (ADAS) and infotainment systems, ceramic Taconic PCBs provide reliable performance under varying temperature conditions and vibrations, enhancing the durability and functionality of automotive electronic systems.
- Telecommunications: In telecommunications infrastructure, such as base stations and signal processors, ceramic Taconic PCBs ensure high-speed signal transmission and low loss, supporting reliable and efficient communication networks.
- Test and Measurement Equipment: For test and measurement applications where precision is critical, ceramic Taconic PCBs provide stable and accurate performance. They are used in oscilloscopes, signal analyzers, and other high-precision testing equipment.
Overall, ceramic Taconic PCBs are valued for their excellent electrical properties, thermal stability, and mechanical strength, making them suitable for a wide range of high-performance and demanding applications.
FAQs about Taconic PCB
What are the key benefits of Taconic PCBs?
Taconic PCBs offer superior electrical performance with low signal loss, high thermal stability, precise impedance control, reduced electromagnetic interference (EMI), and enhanced durability.
What applications are suitable for Taconic PCBs?
Taconic PCBs are ideal for high-frequency and RF circuits, microwave communications, aerospace and defense, medical devices, high-power electronics, automotive electronics, telecommunications, and test and measurement equipment.
What materials are used in Taconic PCBs?
Taconic PCBs commonly use PTFE (polytetrafluoroethylene) and ceramic-filled PTFE composites. These materials provide excellent dielectric properties and thermal stability.
How are Taconic PCBs fabricated?
The fabrication process includes material preparation, layer cutting and laminating, drilling, imaging and etching, plating, solder mask application, surface finish application, testing, and final assembly.
What are the typical challenges in using Taconic PCBs?
Challenges include handling the specialized materials during fabrication, maintaining precise impedance control, and ensuring proper thermal management. The unique properties of Taconic materials require careful attention to detail.
How do Taconic PCBs compare to traditional FR4 PCBs?
Taconic PCBs generally offer better performance in high-frequency and high-speed applications compared to traditional FR4 PCBs. They provide lower signal loss, higher thermal stability, and more precise impedance control.