Rogers Xtreme Speed RO1200 Substrate Manufacturer
Rogers Xtreme Speed RO1200 Substrate Manufacturer,Rogers Xtreme Speed RO1200 Substrate is a cutting-edge material tailored for high-speed digital and RF applications. It boasts low dielectric constant and loss, ensuring minimal signal distortion and high data integrity. RO1200 Substrate’s exceptional thermal conductivity enables efficient heat dissipation, crucial for maintaining signal integrity under demanding conditions. It is widely used in advanced telecommunications, networking equipment, and radar systems where high performance and reliability are paramount. RO1200 Substrate’s superior electrical properties and robust mechanical strength make it an industry leader, supporting the development of next-generation electronics requiring enhanced speed and efficiency.
What is Rogers Xtreme Speed RO1200 Substrate?
Rogers Xtreme Speed RO1200 substrate is a high-frequency laminate designed for demanding applications in the RF/microwave industry. It offers exceptional electrical performance and reliability, making it suitable for high-speed digital and high-frequency analog circuits.
The RO1200 substrate is known for its low loss tangent, which minimizes signal loss and distortion, crucial for maintaining signal integrity in high-frequency designs. This property also supports its use in applications requiring high data rates and precise signal transmission.
Moreover, RO1200 substrates typically feature excellent thermal management capabilities, ensuring stable performance across a wide temperature range. This thermal stability is essential for applications subjected to varying environmental conditions or those requiring consistent operation over extended periods.
In manufacturing, Rogers RO1200 substrates are engineered to provide consistency and uniformity, meeting stringent quality standards. This reliability is critical for ensuring predictable performance in complex RF and microwave systems.
Overall, Rogers Xtreme Speed RO1200 substrates are favored in industries such as telecommunications, aerospace, defense, and automotive, where high-frequency performance, reliability, and signal integrity are paramount. Their advanced properties make them a preferred choice for engineers designing cutting-edge electronic systems.
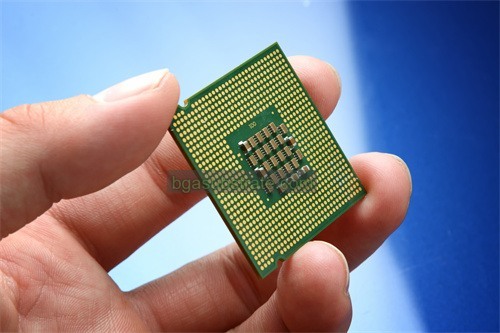
Rogers Xtreme Speed RO1200 Substrate Manufacturer
What is the Rogers Xtreme Speed RO1200 Substrate Design Guidelines?
The design guidelines for Rogers Xtreme Speed RO1200 substrates typically focus on maximizing their high-frequency performance and ensuring reliable operation in RF/microwave applications. Here are some key aspects generally covered in the design guidelines:
- Material Properties: Understanding the electrical characteristics of RO1200 substrates, such as dielectric constant (εr) and loss tangent (tan δ), which are crucial for calculating impedance, signal attenuation, and ensuring minimal signal loss.
- Layer Stackup: Guidelines for layer configurations and thicknesses to optimize signal integrity, impedance matching, and minimize cross-talk between adjacent signal layers. This includes recommendations for utilizing ground and power planes effectively to reduce electromagnetic interference (EMI).
- Transmission Line Design: Techniques for designing transmission lines (microstrip, stripline, coplanar waveguide) to maintain controlled impedance and minimize losses. This involves considerations for line width, spacing, and via structures.
- Via Design: Guidelines for via types (plated-through hole, microvia) and placement to minimize signal degradation, maintain controlled impedance, and ensure reliable electrical connections between layers.
- Thermal Management: Recommendations for managing thermal dissipation to prevent overheating, which can affect electrical performance and reliability. This includes selecting appropriate thermal vias and optimizing copper distribution.
- Manufacturing Tolerances: Understanding the tolerances and capabilities of manufacturing processes (e.g., drilling, lamination) to ensure design specifications are achievable and consistent across production batches.
- Environmental Considerations: Ensuring designs are robust against environmental factors such as temperature variations, humidity, and mechanical stress, which can impact substrate performance over time.
- EMC Compliance: Guidelines to ensure designs meet electromagnetic compatibility (EMC) standards, minimizing interference and susceptibility to external electromagnetic fields.
- Signal Integrity Analysis: Conducting simulations and analyses (e.g., using tools like HFSS, ADS) to validate design parameters such as impedance, insertion loss, and return loss to ensure they meet performance requirements.
- Documentation and Verification: Documenting design specifications, materials used, and test results for verification purposes. This helps in troubleshooting and ensuring designs can be replicated reliably in subsequent iterations or production runs.
These guidelines are crucial for engineers working with Rogers Xtreme Speed RO1200 substrates to achieve optimal performance and reliability in high-frequency applications, ensuring designs meet stringent performance requirements and deliver consistent results in real-world conditions.
The advantages of Rogers Xtreme Speed RO1200 Substrate
Rogers Xtreme Speed RO1200 substrate offers several advantages that make it highly desirable for high-frequency and high-speed applications in the RF/microwave industry:
- Low Loss Tangent: RO1200 substrates exhibit a low loss tangent, which minimizes signal attenuation. This property is critical for maintaining signal integrity in high-frequency circuits, enabling efficient transmission of signals without significant loss.
- High Frequency Performance: Designed specifically for high-frequency applications, RO1200 substrates provide excellent electrical performance across a broad range of frequencies. This capability supports the transmission of signals at GHz frequencies commonly used in modern RF and microwave systems.
- Stable Dielectric Constant:The stable and predictable dielectric constant (εr) of RO1200 substrates ensures consistent electrical characteristics across different temperatures and frequencies. This stability is essential for maintaining accurate impedance matching and reliable circuit performance.
- Thermal Management: Effective thermal management capabilities help in dissipating heat generated during operation. This is crucial for maintaining the reliability and longevity of electronic components, especially in systems operating under high-power conditions or in environments with varying temperatures.
- Dimensional Stability: RO1200 substrates exhibit excellent dimensional stability, which is important for maintaining tight tolerances during manufacturing processes and ensuring reliable performance over time.
- Manufacturing Consistency: Rogers’ stringent manufacturing processes ensure uniformity and consistency in material properties and electrical performance across production batches. This reliability is crucial for meeting design specifications and reducing variability in circuit performance.
- Compatibility with High-Speed Designs: RO1200 substrates are well-suited for high-speed digital and analog designs due to their low loss and high-frequency performance. This makes them ideal for applications requiring high data rates, low latency, and minimal signal distortion.
- Environmental Durability: The robust design of RO1200 substrates ensures resilience against environmental factors such as moisture, humidity, and mechanical stress. This durability enhances the substrate’s reliability in challenging operating conditions.
- EMI Shielding: The construction of RO1200 substrates often includes effective EMI shielding properties, which help in reducing electromagnetic interference. This feature is crucial for maintaining signal integrity and preventing cross-talk in densely packed electronic assemblies.
Overall, Rogers Xtreme Speed RO1200 substrates are valued for their superior electrical performance, reliability, and suitability for demanding RF/microwave applications where precision, stability, and high-frequency operation are essential requirements.
What is the Rogers Xtreme Speed RO1200 Substrate Fabrication Process?
The fabrication process for Rogers Xtreme Speed RO1200 substrates involves several key steps to ensure the material achieves its high-performance characteristics suitable for RF/microwave applications:
- Material Preparation: The process begins with the preparation of raw materials. Rogers RO1200 substrates typically consist of woven glass-reinforced ceramic laminates with specific resin systems tailored for high-frequency performance.
- Layer Preparation and Cutting: The laminates are prepared by cutting them to the required size and layer configuration. This step ensures that each substrate meets the dimensional requirements and layer stackup specified in the design.
- Drilling and Tooling: Precision drilling is performed to create holes for vias and mounting components. This step requires high accuracy to maintain tight tolerances and ensure alignment across multiple layers in complex designs.
- Copper Cladding: Copper foil is laminated onto the substrate surfaces through a process of heat and pressure. This step forms the conductive layers (signal layers, ground planes, power planes) necessary for routing signals and providing electrical conductivity.
- Etching: Etching is used to selectively remove excess copper from areas not covered by the circuit pattern, defining the conductive traces and creating the desired circuit layout. This process ensures precise control over trace widths and spacing, critical for maintaining controlled impedance.
- Plating and Surface Finish: Vias and pads are plated with copper to ensure electrical continuity between layers and facilitate soldering of components. Surface finishes such as ENIG (Electroless Nickel Immersion Gold) or HASL (Hot Air Solder Leveling) are applied to protect exposed copper and ensure reliable solder joints.
- Lamination: The prepared layers are stacked together and bonded under heat and pressure using an epoxy resin system. This lamination process ensures strong adhesion between layers, creating a durable substrate capable of withstanding mechanical stress and environmental conditions.
- Curing: The assembled substrate undergoes curing in a controlled environment to ensure the resin fully hardens and achieves its specified mechanical and electrical properties. This step is crucial for stabilizing the substrate’s dimensional characteristics and minimizing internal stresses.
- Routing and Final Inspection: After curing, the substrate is routed to trim excess material and create the final shape according to design specifications. Each substrate undergoes rigorous inspection to verify dimensional accuracy, layer alignment, electrical continuity, and compliance with performance standards.
- Testing and Quality Assurance: Comprehensive testing is conducted to evaluate electrical properties such as impedance, insertion loss, and signal integrity. Quality assurance measures ensure that each substrate meets or exceeds performance criteria before being released for use in electronic assemblies.
Throughout the fabrication process, strict adherence to design guidelines and quality control measures is essential to produce Rogers Xtreme Speed RO1200 substrates that deliver consistent high-frequency performance, reliability, and durability required for advanced RF/microwave applications.
The application of ceramic Rogers Xtreme Speed RO1200 Substrate
Rogers Xtreme Speed RO1200 substrates find application in various high-frequency and high-speed electronic systems where superior electrical performance and reliability are critical. Some common applications include:
- Telecommunications: RO1200 substrates are used in RF amplifiers, antennas, base stations, and satellite communications systems. Their low loss tangent and high-frequency capabilities ensure efficient signal transmission and reception.
- Wireless Infrastructure: They are employed in wireless routers, access points, and other networking equipment where high-speed data transmission at GHz frequencies is required. The stable dielectric constant and excellent thermal management support reliable operation in these applications.
- Radar Systems: RO1200 substrates are utilized in radar transmitters and receivers due to their ability to handle high-power signals with minimal loss and distortion. This makes them suitable for both civilian and military radar applications.
- Test and Measurement Equipment: They are used in high-frequency test fixtures, probes, and measurement instruments where precise signal integrity and low insertion loss are crucial for accurate testing and analysis.
- Satellite Communication: RO1200 substrates support satellite communication systems, providing robust performance in the harsh space environment. Their reliability under extreme temperatures and vacuum conditions makes them ideal for spaceborne electronics.
- Automotive Radar: They are employed in automotive radar systems for collision avoidance, adaptive cruise control, and other advanced driver assistance systems (ADAS). The substrates’ ability to maintain signal integrity in high-speed automotive environments is essential for safety and reliability.
- Aerospace and Defense: RO1200 substrates are used in avionics, radar systems, electronic warfare systems, and military communications equipment. Their rugged design, low loss, and high-frequency performance meet stringent requirements for reliability and performance in defense applications.
- Medical Devices: They are utilized in medical imaging equipment such as MRI machines and ultrasound devices, where high-frequency signals and low electromagnetic interference (EMI) are critical for accurate diagnostics.
Overall, Rogers Xtreme Speed RO1200 substrates are preferred in applications requiring high-frequency performance, low loss tangent, stable electrical properties, and robust thermal management. Their versatility and reliability make them suitable for a wide range of demanding electronic systems across various industries.
FAQs about Rogers Xtreme Speed RO1200 Substrate
What is Rogers Xtreme Speed RO1200 substrate?
Rogers Xtreme Speed RO1200 substrate is a high-performance material designed for high-frequency and high-speed electronic applications. It offers low loss tangent, stable dielectric constant, and excellent thermal management properties.
What are the key advantages of RO1200 substrate?
The substrate provides superior electrical performance, including low signal attenuation, high-frequency capability, and reliable signal integrity. It also offers excellent thermal stability and dimensional consistency.
Where is RO1200 substrate typically used?
RO1200 substrates find application in telecommunications, wireless infrastructure, radar systems, test and measurement equipment, satellite communications, automotive radar, aerospace, defense, and medical devices.
What are the main features of RO1200 substrate?
It features a low loss tangent for minimal signal attenuation, stable dielectric constant for consistent electrical properties, good thermal management capabilities, and compatibility with high-frequency designs.
How is RO1200 substrate fabricated?
The fabrication process includes material preparation, layer cutting and preparation, copper cladding, drilling, etching, lamination, curing, and final inspection. Strict adherence to design guidelines and quality control is maintained throughout.
What are the environmental and mechanical characteristics of RO1200 substrate?
It exhibits robust environmental durability, including resistance to moisture, humidity, and mechanical stress. This makes it suitable for use in challenging operating conditions and harsh environments.
Is RO1200 substrate suitable for space applications?
Yes, RO1200 substrates are used in satellite communication systems and other spaceborne electronics due to their reliability under extreme temperatures and vacuum conditions.