Rogers TMM® 6 Substrate Manufacturer
Rogers TMM® 6 Substrate Manufacturer,Rogers TMM® 6 Substrate is renowned for its exceptional performance in high-frequency applications. This advanced material offers low dielectric loss, ensuring minimal signal attenuation and high reliability. Its superior thermal management properties make it ideal for demanding environments where heat dissipation is critical. Rogers TMM® 6 Substrate is favored in RF and microwave circuits for its excellent dimensional stability and ease of fabrication, supporting precise designs and consistent performance. Whether in aerospace, telecommunications, or radar systems, TMM® 6 Substrate continues to set the standard for high-frequency circuitry due to its unmatched combination of electrical and mechanical characteristics.
What is Rogers TMM® 6 Substrate?
Rogers TMM® 6 (Thermoset Microwave Materials) substrate is a high-frequency laminate designed for applications requiring excellent electrical performance at microwave frequencies. It features a low dielectric constant (εr) and low loss tangent (tan δ), making it suitable for RF (Radio Frequency) and microwave circuits where signal integrity and minimal loss are critical.
This substrate is known for its stability over a wide range of frequencies and temperatures, which is advantageous in high-performance applications such as radar systems, satellite communications, and wireless infrastructure. The Rogers TMM® 6 substrate offers consistent electrical properties and mechanical stability, ensuring reliable performance in demanding environments.
Manufactured using advanced processing techniques, TMM® 6 substrates are engineered to provide precise control over dielectric constant and thickness, essential for achieving optimal signal transmission and impedance matching in RF circuit designs. Its robust construction also enhances durability and reliability, meeting the stringent requirements of aerospace, defense, and telecommunications industries.
Overall, Rogers TMM® 6 substrate stands out for its high-frequency performance, low loss characteristics, and reliability, making it a preferred choice for designers and engineers seeking superior RF and microwave solutions.
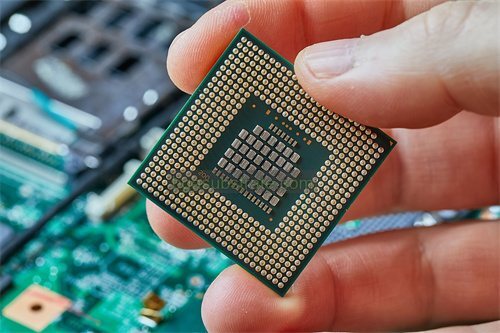
Rogers TMM® 6 Substrate Manufacturer
What is the Rogers TMM® 6 Substrate Design Guidelines?
Design guidelines for Rogers TMM® 6 substrates are crucial for ensuring optimal performance and reliability in RF and microwave circuit applications. Here are some key design considerations typically recommended:
- Material Properties: Understand the electrical properties of Rogers TMM® 6, including its dielectric constant (εr) and loss tangent (tan δ), which are critical for determining signal integrity and attenuation characteristics at high frequencies.
- Layer Stack-up: Design the layer stack-up to achieve the desired impedance and signal routing requirements. Rogers TMM® 6 substrates are often used in multilayer PCBs to accommodate complex RF designs.
- Impedance Control: Maintain tight impedance tolerances across traces and transmission lines to minimize signal reflections and ensure consistent performance. Use impedance calculators or simulation tools to verify designs.
- Transmission Line Design: Follow transmission line design guidelines to minimize losses and ensure proper signal propagation. Consider factors such as trace width, spacing, and termination techniques based on the substrate’s electrical properties.
- Grounding and Power Distribution: Implement effective grounding techniques to minimize noise and interference. Ensure adequate power distribution to RF components to maintain stable operation.
- Component Placement: Place RF components strategically to minimize signal path lengths and reduce parasitic effects. Consider thermal management requirements for components operating at high frequencies.
- Manufacturing Considerations: Communicate design specifications clearly with PCB manufacturers familiar with Rogers TMM® 6 substrates. Ensure compatibility with manufacturing processes such as drilling, plating, and etching.
- Environmental Factors: Consider the substrate’s performance under varying environmental conditions, including temperature and humidity, to ensure reliability over the product’s lifecycle.
By adhering to these design guidelines, engineers can optimize the performance of RF and microwave circuits using Rogers TMM® 6 substrates, achieving high-frequency stability, low loss characteristics, and reliable signal integrity in demanding applications.
The advantages of Rogers TMM® 6 Substrate
Rogers TMM® 6 substrate offers several advantages that make it a preferred choice for RF (Radio Frequency) and microwave applications:
- Low Dielectric Constant (εr): TMM® 6 substrates feature a low dielectric constant, typically around 2.7 to 3.0. This property helps in minimizing signal loss and dispersion, making it ideal for high-frequency circuits where signal integrity is crucial.
- Low Loss Tangent (tan δ): The low loss tangent of TMM® 6 substrates contributes to minimal signal attenuation, ensuring efficient transmission of RF signals with reduced energy loss. This characteristic is essential for maintaining high signal quality and reliability in RF systems.
- Stable Electrical Properties: TMM® 6 substrates exhibit stable electrical properties over a wide range of frequencies and temperatures. This stability ensures consistent performance in varying environmental conditions, critical for applications in aerospace, defense, and telecommunications.
- Dimensional Stability: These substrates are engineered for excellent dimensional stability, minimizing changes in electrical properties due to temperature variations or mechanical stress. This stability enhances the reliability and longevity of RF and microwave circuits.
- Ease of Fabrication: Rogers TMM® 6 substrates are designed for ease of fabrication, supporting precise machining, drilling, and etching processes required for complex RF PCB designs. This ease of fabrication contributes to shorter production cycles and cost-effectiveness.
- Compatibility with High-Frequency Applications: Due to its excellent RF properties, TMM® 6 substrates are suitable for a wide range of high-frequency applications, including radar systems, satellite communications, wireless infrastructure, and automotive radar sensors.
- Proven Performance: Rogers Corporation, a leader in advanced materials, ensures rigorous quality control and reliability testing of TMM® 6 substrates. This proven performance and industry reputation make it a trusted choice among RF engineers and designers.
Overall, Rogers TMM® 6 substrates offer a compelling combination of low dielectric constant, low loss tangent, stability, and ease of fabrication, making them ideal for demanding RF and microwave circuit applications where performance and reliability are paramount.
What is the Rogers TMM® 6 Substrate Fabrication Process?
The fabrication process for Rogers TMM® 6 substrates involves several key steps to ensure the material’s properties are optimized for high-frequency RF (Radio Frequency) and microwave applications:
- Material Selection: Rogers TMM® 6 substrates are composed of specially formulated thermoset materials that provide low dielectric constant (εr) and low loss tangent (tan δ). These materials are selected for their high-performance characteristics in RF circuits.
- Preparation: The substrate manufacturing process begins with preparing the raw materials according to precise formulations and mixing ratios. This step is crucial to ensure uniformity and consistency in material properties.
- Substrate Formation: The mixed materials are then formed into sheets or panels using techniques such as calendaring or extrusion. This process involves applying heat and pressure to achieve the desired thickness and density of the substrate material.
- Curing: Once formed, the substrate material undergoes a curing process where it is heated to a specific temperature and held for a defined period. Curing is essential to cross-link the polymer chains within the material, enhancing its mechanical strength and electrical properties.
- Surface Treatment: After curing, the substrate surfaces may undergo treatment to improve adhesion and facilitate subsequent processes such as metallization or soldering. Surface treatments can include plasma cleaning or chemical etching to remove contaminants and promote bonding.
- Metallization: In some applications, metallization layers are deposited onto the substrate surfaces to create conductive traces and pads. This step typically involves processes like sputtering, evaporation, or electroplating to apply metal layers with precise thickness and conductivity.
- Etching and Patterning:Using photolithography techniques, patterns for circuit traces and features are defined on the substrate surface. Etching processes selectively remove unwanted metal or substrate material, leaving behind the desired circuitry layout.
- Quality Control: Throughout the fabrication process, rigorous quality control measures are implemented to ensure the substrate meets specified electrical and mechanical requirements. Testing may include dimensional inspection, electrical impedance verification, and reliability testing under simulated operating conditions.
- Final Inspection and Packaging: Once fabrication and testing are complete, TMM® 6 substrates undergo final inspection to verify performance and adherence to customer specifications. Substrates are then packaged to protect them from handling and environmental damage during shipping and storage.
By following these steps with precision and utilizing advanced manufacturing techniques, Rogers TMM® 6 substrates are produced to deliver consistent electrical properties, dimensional stability, and reliability required for high-frequency RF and microwave applications in various industries.
The application of ceramic Rogers TMM® 6 Substrate
Rogers TMM® 6 substrate, known for its excellent RF (Radio Frequency) and microwave properties, finds application across various industries where high-performance circuitry is essential. Some key applications include:
- Wireless Communication Systems: TMM® 6 substrates are widely used in wireless communication systems such as cellular base stations, antennas, and satellite communication systems. Their low dielectric constant and low loss tangent characteristics enable efficient signal transmission and reception, critical for maintaining communication integrity over long distances.
- Radar Systems: In radar applications, including military and automotive radar systems, TMM® 6 substrates support high-frequency circuit designs that require precise signal processing and low signal loss. They contribute to radar systems’ accuracy and reliability in detecting and tracking objects.
- Aerospace and Defense: TMM® 6 substrates are utilized in aerospace and defense applications for radar systems, communication modules, electronic warfare systems, and avionics. Their stability across temperature fluctuations and mechanical robustness make them suitable for harsh environmental conditions.
- High-Frequency Test Equipment: Test and measurement equipment operating at high frequencies benefit from TMM® 6 substrates due to their consistent electrical performance and reliability. They are used in signal generators, spectrum analyzers, and network analyzers to ensure accurate measurement results.
- Satellite Systems: TMM® 6 substrates play a crucial role in satellite communication systems, where they facilitate the transmission and reception of signals between ground stations and satellites. Their ability to maintain signal integrity over a wide range of frequencies supports reliable satellite communications.
- Automotive Radar Sensors: In the automotive industry, TMM® 6 substrates are employed in radar sensors for advanced driver assistance systems (ADAS), collision avoidance systems, and autonomous driving applications. Their high-frequency capabilities enable precise detection and monitoring of surrounding objects.
- Medical Devices: Certain medical devices that utilize RF technology, such as imaging systems and diagnostic equipment, benefit from TMM® 6 substrates’ low loss tangent and stable electrical properties. These substrates contribute to the accuracy and reliability of medical diagnostics.
Overall, Rogers TMM® 6 substrates are chosen for applications requiring high-frequency performance, minimal signal loss, and reliability in challenging environments. Their versatility across industries underscores their role in advancing technology for communication, defense, aerospace, automotive, and medical sectors.
FAQs about Rogers TMM® 6 Substrate
What is Rogers TMM® 6 substrate used for?
Rogers TMM® 6 substrate is used primarily in RF (Radio Frequency) and microwave applications where high-performance materials with low dielectric constant and low loss tangent are required. Common applications include wireless communication systems, radar systems, aerospace electronics, automotive radar sensors, and high-frequency test equipment.
What are the key advantages of Rogers TMM® 6 substrate?
The advantages include low dielectric constant (typically around 2.7 to 3.0), low loss tangent, stable electrical properties over a wide range of frequencies and temperatures, and excellent dimensional stability. These properties ensure efficient signal transmission, minimal signal loss, and reliability in demanding environments.
How does Rogers TMM® 6 substrate compare to other materials?
Compared to standard FR-4 materials, Rogers TMM® 6 offers superior performance in high-frequency applications due to its lower dielectric constant and loss tangent. It provides better signal integrity and reduced signal attenuation, making it suitable for high-frequency circuits where performance is critical.
What types of circuits are suitable for Rogers TMM® 6 substrate?
TMM® 6 substrate is suitable for a wide range of circuits including transmission lines, antennas, filters, amplifiers, and other RF/microwave components. It supports high-frequency designs that require precise impedance control and minimal signal loss.
How is Rogers TMM® 6 substrate fabricated?
The fabrication process involves material preparation, substrate formation using heat and pressure, curing to cross-link polymer chains, surface treatment for adhesion, metallization for conductive traces, and precision etching for circuit patterning. Quality control measures ensure adherence to specified electrical and mechanical properties.
Where can I purchase Rogers TMM® 6 substrate?
Rogers TMM® 6 substrates are available through authorized distributors and directly from Rogers Corporation. Customers can contact Rogers or their local distributor for pricing, availability, and technical support.
What are the environmental and reliability considerations for Rogers TMM® 6 substrate?
TMM® 6 substrates are designed to maintain stable performance under varying environmental conditions including temperature, humidity, and mechanical stress. They undergo rigorous testing to ensure reliability and longevity in critical applications such as aerospace, defense, and telecommunications.