Rogers TC600 Substrate Manufacturer
Rogers TC600 Substrate Manufacturer,Rogers TC600 Substrate is an advanced thermoset composite material known for its exceptional electrical and mechanical properties. It features a low dielectric constant and low loss tangent, making it ideal for high-frequency applications like RF and microwave circuits. This substrate supports complex circuit designs and high-speed signal transmission, ensuring reliable performance in demanding electronic systems. Rogers TC600 Substrate is widely utilized in communication networks, satellite technologies, and radar systems where superior signal integrity and thermal stability are crucial. It provides robust solutions for applications requiring high reliability and precise electrical characteristics in challenging environments.
What is Rogers TC600 Substrate?
Rogers TC600 is a high-performance thermoset laminate material designed by Rogers Corporation, renowned for its exceptional electrical and mechanical properties. This substrate is widely used in high-frequency applications where signal integrity and reliability are critical.
TC600 features a low dielectric constant (Dk) of around 6.15 and a low dissipation factor (Df) of approximately 0.0027 at 10 GHz, making it suitable for applications requiring minimal signal loss and high-speed data transmission. Its excellent dimensional stability over a wide temperature range ensures reliability in diverse environmental conditions.
Manufactured using woven fiberglass reinforcement combined with a proprietary blend of thermoset resins, TC600 offers robust mechanical strength and durability, essential for demanding electronic designs. Its thermal conductivity supports efficient heat dissipation, enhancing overall performance in high-power applications.
Designers favor TC600 for its ease of fabrication, allowing for intricate circuit designs and fine-line etching processes. Its compatibility with standard PCB manufacturing techniques facilitates cost-effective production without compromising on quality or performance.
Overall, Rogers TC600 substrate stands out for its superior electrical characteristics, mechanical robustness, and reliability, making it a preferred choice in telecommunications, aerospace, defense, and other high-frequency electronic applications.
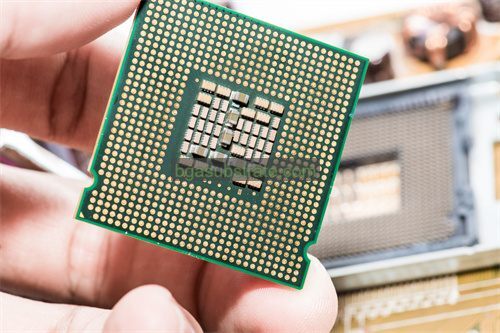
Rogers TC600 Substrate Manufacturer
What is the Rogers TC600 Substrate Design Guidelines?
The design guidelines for Rogers TC600 substrate focus on optimizing performance and reliability in high-frequency electronic applications. Here are key considerations:
- Material Properties: Understand TC600’s electrical characteristics, such as its low dielectric constant (Dk) and low dissipation factor (Df). These properties influence signal integrity and loss, critical for high-frequency designs.
- Transmission Line Design: Use controlled impedance traces to match signal requirements precisely. Design trace widths and spacing according to TC600’s Dk to minimize impedance variations and ensure consistent signal propagation.
- Via Design: Optimize via structures to maintain signal integrity and minimize parasitic effects. Properly size vias and use via fences or stitching to reduce electromagnetic interference (EMI) and ensure reliable electrical connections.
- Component Placement: Position components strategically to minimize signal path lengths and reduce potential for interference. Consider RF and high-speed signal routing to maintain signal integrity across the PCB.
- Thermal Management:Address heat dissipation through proper thermal vias and heatsinking techniques, leveraging TC600’s thermal conductivity properties to manage high-power components effectively.
- Manufacturing Considerations: Coordinate with PCB manufacturers experienced in handling high-frequency materials like TC600. Ensure processes meet tight tolerances for etching, drilling, and laminating to maintain material integrity and performance.
- Testing and Validation: Conduct thorough testing and validation, including impedance testing, signal integrity analysis, and thermal testing, to verify design performance against specifications and ensure reliability under operational conditions.
By adhering to these design guidelines, engineers can maximize the benefits of Rogers TC600 substrate, ensuring robust performance and reliability in demanding high-frequency applications.
The advantages of Rogers TC600 Substrate
Rogers TC600 substrate offers several advantages that make it highly desirable for high-frequency electronic applications:
- Low Dielectric Constant (Dk): TC600 has a low dielectric constant of approximately 6.15 at 10 GHz, which minimizes signal loss and ensures high signal integrity. This property is crucial for maintaining the quality of high-frequency signals in RF/microwave circuits.
- Low Dissipation Factor (Df): With a low dissipation factor of about 0.0027 at 10 GHz, TC600 substrate exhibits minimal signal attenuation. This characteristic is essential for applications requiring precise signal transmission and low noise performance.
- High Thermal Conductivity: TC600 offers good thermal conductivity, allowing for efficient heat dissipation from high-power components. This property helps in managing thermal issues and maintaining electronic device reliability, especially in power amplifiers and other high-power applications.
- Dimensional Stability: The substrate maintains excellent dimensional stability over a wide temperature range, ensuring consistent electrical performance across varying environmental conditions. This stability is critical for maintaining signal integrity and reliability over time.
- Mechanical Strength: TC600 substrate is robust and mechanically strong, making it suitable for applications where durability and resistance to mechanical stress are important. It can withstand handling during manufacturing and assembly processes without compromising performance.
- Compatibility with High-Frequency Designs: Designed for high-frequency applications, TC600 substrate supports fine-line etching and precise trace width control, enabling complex circuit designs with tight tolerance requirements. It is ideal for RF/microwave circuits, antennas, filters, and other high-frequency components.
- Reliability in Harsh Environments: The substrate’s excellent electrical and mechanical properties make it reliable in harsh operating conditions typical of aerospace, defense, automotive, and industrial applications. It can withstand thermal cycling, moisture, and other environmental stresses without degradation in performance.
- Ease of Fabrication: Despite its advanced properties, TC600 is compatible with standard PCB fabrication processes, allowing for cost-effective manufacturing of high-performance electronic assemblies. It supports processes such as drilling, lamination, and fine-line etching with precision.
Overall, Rogers TC600 substrate stands out for its superior electrical characteristics, thermal management capabilities, mechanical resilience, and reliability in demanding electronic applications. These advantages make it a preferred choice for designers seeking optimal performance and longevity in high-frequency circuits and systems.
What is the Rogers TC600 Substrate Fabrication Process?
The fabrication process for Rogers TC600 substrate involves several key steps to ensure high-quality production suitable for high-frequency electronic applications:
- Material Preparation: Begin by preparing Rogers TC600 laminate sheets, which typically consist of woven fiberglass reinforcement impregnated with a proprietary thermoset resin system.
- Cleaning and Inspection: Clean the laminate surfaces thoroughly to remove any contaminants that could affect bonding or etching processes. Inspect for uniformity and integrity of the material.
- Drilling: Use precision drilling techniques to create holes for vias and component mounting. Ensure drill bits are suitable for fiberglass-reinforced laminates to prevent burring and maintain hole integrity.
- Layer Stacking: Assemble multiple layers of TC600 laminate and prepreg material to build up the desired thickness and stack configuration. Align layers accurately to ensure proper registration of circuit features.
- Lamination: Apply heat and pressure to laminate layers together, activating the resin system to bond them securely. This step consolidates the stack into a single integrated substrate with consistent electrical and mechanical properties.
- Etching: Use chemical etching or mechanical milling processes to selectively remove copper from the substrate surface, defining the circuit traces and features according to the design specifications. Etching accuracy is crucial for maintaining signal integrity.
- Surface Treatment: Apply surface finishes such as ENIG (Electroless Nickel Immersion Gold) or HASL (Hot Air Solder Leveling) to protect exposed copper surfaces from oxidation and facilitate solderability during assembly.
- Quality Control:Conduct rigorous inspections throughout the fabrication process to verify dimensional accuracy, copper thickness, laminate thickness, and adherence to design tolerances. Test samples for electrical performance characteristics like impedance and signal loss.
- Routing and Profiling: Rout the substrate to shape and size, using precision equipment to cut out individual PCBs from the larger panel. Profiling ensures the final boards meet exact dimensional specifications.
- Final Inspection and Packaging: Perform final quality checks to ensure all PCBs meet customer specifications and industry standards. Package finished boards securely for shipment or further assembly processes.
By following these steps meticulously, PCB manufacturers can produce Rogers TC600 substrates that meet stringent requirements for high-frequency performance, reliability, and durability in advanced electronic applications.
The application of ceramic Rogers TC600 Substrate
Rogers TC600 substrate, a high-performance thermoset laminate, finds application primarily in high-frequency electronic circuits where excellent electrical properties, reliability, and thermal management are critical. Here are some key applications:
- RF/Microwave Circuits: TC600 is widely used in RF and microwave applications due to its low dielectric constant (Dk) and low loss tangent (Df), which minimize signal loss and ensure high signal integrity. It supports high-frequency operation, making it suitable for antennas, filters, amplifiers, and other components in wireless communication systems.
- Aerospace and Defense: The substrate’s ability to withstand harsh environmental conditions, coupled with its reliable performance at high frequencies, makes it ideal for aerospace and defense applications. It is used in radar systems, satellite communications, avionics, and military electronic warfare equipment.
- Automotive Radar: TC600 is employed in automotive radar systems for collision detection, adaptive cruise control, and other advanced driver assistance systems (ADAS). Its stable electrical properties and thermal conductivity contribute to reliable performance in automotive environments.
- Test and Measurement Equipment: Instruments requiring precise signal transmission and low noise benefit from TC600’s consistent electrical characteristics. It is used in spectrum analyzers, network analyzers, and other test equipment where signal integrity is crucial for accurate measurements.
- Medical Devices: TC600 substrate supports high-frequency medical devices such as imaging systems (MRI, CT scanners), wireless medical telemetry, and diagnostic equipment. Its reliability and performance contribute to the accuracy and effectiveness of medical technologies.
- Industrial Applications: The substrate’s thermal conductivity and mechanical strength make it suitable for industrial applications like power amplifiers, sensors, and high-frequency modules in industrial automation and control systems.
- Consumer Electronics:TC600 is used in consumer electronics where high-speed data transmission and compact design are essential, such as in smartphones, tablets, and wearable devices.
In each of these applications, Rogers TC600 substrate plays a crucial role in ensuring the performance, reliability, and longevity of electronic circuits operating at high frequencies or in demanding environments. Its advanced material properties contribute to the efficiency and functionality of various technological advancements across industries.
FAQs about Rogers TC600 Substrate
What are the key properties of Rogers TC600 substrate?
Rogers TC600 substrate is known for its low dielectric constant (Dk) of approximately 6.15 and low dissipation factor (Df) of about 0.0027 at 10 GHz. It offers excellent electrical performance, thermal conductivity, and mechanical stability.
What are the typical applications of Rogers TC600 substrate?
TC600 is commonly used in high-frequency electronic circuits such as RF/microwave applications, aerospace and defense systems, automotive radar, medical devices, test and measurement equipment, industrial applications, and consumer electronics.
What advantages does Rogers TC600 substrate offer?
TC600 substrate provides superior signal integrity, minimal loss tangent, thermal management capabilities, and dimensional stability across a wide range of temperatures. It supports high-speed data transmission and is reliable in demanding environmental conditions.
How does Rogers TC600 substrate compare to other materials like FR-4?
Compared to standard FR-4 materials, TC600 offers lower Dk and Df, making it more suitable for high-frequency applications where signal integrity is critical. It also has better thermal conductivity and can withstand higher operating temperatures.
What are the fabrication considerations for TC600 substrate?
Fabrication of TC600 involves precision drilling, lamination under controlled conditions, fine-line etching for trace definition, and careful handling to maintain material integrity. It requires expertise in handling high-frequency laminates and ensuring compliance with design specifications.
Is Rogers TC600 substrate suitable for high-power applications?
Yes, TC600 substrate’s thermal conductivity and mechanical strength make it suitable for high-power applications where efficient heat dissipation and robust performance are required. It is often used in power amplifiers and other high-frequency modules.
How can TC600 substrate contribute to product reliability?
TC600’s consistent electrical properties and reliable performance in various environmental conditions contribute to the overall reliability and longevity of electronic products. It helps maintain signal integrity and minimize performance degradation over time.