Rogers TC350 Substrate Manufacturer
Rogers TC350 Substrate Manufacturer,Rogers TC350 Substrate is a high-performance thermoset composite material known for its excellent electrical and mechanical properties. It offers a low dielectric constant and low loss tangent, making it ideal for high-frequency applications such as RF and microwave circuits. Rogers TC350 Substrate is designed to support complex circuit layouts and high-speed signal transmission, ensuring reliable performance in critical electronic systems. It is widely used in communication equipment, radar systems, and aerospace applications where stringent performance requirements are essential. Rogers TC350 Substrate provides robust solutions for applications demanding both reliability and high electrical performance.
What is Rogers TC350 Substrate?
Rogers TC350 substrate is a high-frequency laminate designed for demanding applications in the RF/microwave industry. It belongs to the family of ceramic-filled PTFE composites, offering excellent electrical performance combined with mechanical stability. This substrate is known for its low loss characteristics, making it suitable for applications requiring minimal signal attenuation over a wide range of frequencies.
Key features of Rogers TC350 include its high thermal conductivity, which helps in managing heat dissipation effectively, crucial for high-power applications. It also exhibits good dimensional stability, ensuring reliable performance in various environmental conditions.
Manufactured using a controlled process that ensures uniformity and consistency, TC350 is used in antennas, power amplifiers, radar systems, and other high-frequency circuit designs where signal integrity and reliability are paramount. Its properties make it a preferred choice for engineers designing circuits operating in the GHz range, where maintaining signal integrity and minimizing losses are critical for overall system performance.
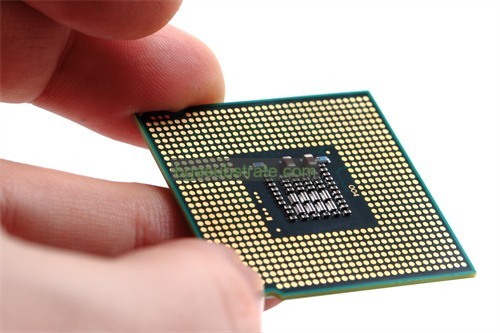
Rogers TC350 Substrate Manufacturer
What is the Rogers TC350 Substrate Design Guidelines?
Design guidelines for Rogers TC350 substrate typically focus on maximizing its electrical performance and ensuring reliable manufacturing processes. Here are some key design considerations:
- Material Properties:Understand the electrical characteristics of TC350, such as its dielectric constant (εr), loss tangent (tan δ), and thermal conductivity. These properties dictate signal integrity and heat dissipation capabilities.
- Stack-up Design:Optimize the layer stack-up to minimize signal losses and impedance mismatches. Consider the number of layers, thickness of dielectric layers, and placement of signal and ground planes to achieve desired impedance control and electromagnetic interference (EMI) suppression.
- Transmission Line Design:Use appropriate trace widths and spacing to maintain controlled impedance transmission lines. The design should account for the frequency of operation and the desired impedance (e.g., 50 ohms for RF applications).
- Component Placement: Place critical components such as RF connectors, antennas, and active devices strategically to minimize signal path lengths and reduce parasitic effects.
- Thermal Management:Given TC350’s high thermal conductivity, design for effective heat dissipation. Ensure adequate vias and thermal vias to conduct heat away from heat-sensitive components.
- Manufacturing Tolerances:Consider manufacturing tolerances for the substrate material and fabrication process. Design features should accommodate these tolerances to ensure consistent performance across production batches.
- Environmental Considerations:Account for the operating environment (temperature, humidity, etc.) in the design to ensure reliability over the substrate’s lifetime.
By following these guidelines, designers can leverage the high-performance characteristics of Rogers TC350 substrate effectively in RF and microwave circuit applications, achieving optimal signal integrity and reliability.
The advantages of Rogers TC350 Substrate
Rogers TC350 substrate offers several advantages that make it a preferred choice for high-frequency RF/microwave applications:
- Low Dielectric Loss:TC350 exhibits low loss tangent (tan δ), which minimizes signal attenuation. This property is crucial for maintaining signal integrity and maximizing the efficiency of high-frequency circuits.
- High Thermal Conductivity:With enhanced thermal conductivity compared to standard PCB materials, TC350 efficiently dissipates heat generated by high-power components. This feature helps in managing thermal issues and improving overall system reliability.
- Excellent Electrical Performance:The substrate provides stable and predictable electrical characteristics across a wide range of frequencies. This predictability is essential for achieving consistent performance in RF circuits, antennas, and other microwave applications.
- Dimensional Stability:TC350 maintains its dimensional stability under varying environmental conditions, ensuring reliable performance over time. This stability is critical in applications where mechanical integrity and precise signal transmission are required.
- Manufacturability:Designed for ease of fabrication and assembly, TC350 supports complex PCB designs and high-density interconnects. It can be processed using standard PCB manufacturing techniques, facilitating cost-effective production.
- Wide Range of Applications:Suitable for diverse applications such as aerospace, telecommunications, radar systems, and high-speed digital circuits, TC350 substrate meets the stringent requirements of modern electronic designs.
Overall, Rogers TC350 substrate’s combination of low loss, high thermal conductivity, and excellent electrical performance makes it an ideal choice for demanding RF/microwave applications where reliability, performance, and thermal management are critical considerations.
What is the Rogers TC350 Substrate Fabrication Process?
The fabrication process of Rogers TC350 substrate involves several key steps to ensure the material’s high performance and reliability:
- Material Preparation:TC350 substrate material is prepared in accordance with specific formulations that include PTFE (Polytetrafluoroethylene) and ceramic fillers. These materials are mixed to achieve the desired dielectric constant (εr), thermal conductivity, and mechanical properties.
- Prepreg Manufacturing:Prepregs are created by impregnating woven glass cloth with the TC350 resin system. This step ensures uniform resin distribution and adhesive properties between layers during lamination.
- Lamination:The lamination process involves stacking alternating layers of prepregs and copper foils according to the PCB design specifications. This stack-up is placed into a press where heat and pressure are applied to bond the layers together. Lamination consolidates the materials into a solid, unified structure.
- Drilling:After lamination, the panel undergoes mechanical drilling to create holes for vias and component mounting pads. High-precision drilling equipment is used to maintain dimensional accuracy and ensure alignment with the PCB design.
- Plating:Copper plating is applied to the panel surfaces and inside the drilled holes to create conductive pathways (traces and vias). This step involves electroplating copper onto the exposed surfaces, followed by a protective layer of tin or other finishes to prevent oxidation.
- Etching and Surface Treatment:Unwanted copper is removed from the panel using chemical etching processes, leaving behind the desired circuit patterns. Surface treatment processes such as immersion silver, OSP (Organic Solderability Preservative), or ENIG (Electroless Nickel Immersion Gold) may be applied to improve solderability and protect exposed copper surfaces.
- Final Inspection and Testing:The finished TC350 substrate undergoes rigorous inspection and testing to verify dimensional accuracy, electrical performance, and adherence to design specifications. This includes checks for impedance control, signal integrity, thermal management, and mechanical strength.
- Routing and Profiling:Panels are routed to separate individual PCBs from the larger panel size. This process includes cutting or milling the board to its final dimensions as per the design requirements.
- Quality Control:Throughout each stage of fabrication, quality control measures ensure that TC350 substrates meet industry standards and customer specifications. This includes monitoring process parameters, material integrity, and final product performance.
By following these fabrication steps with precision and attention to detail, Rogers TC350 substrates are manufactured to deliver consistent high-frequency performance, reliability, and durability in demanding RF/microwave applications.
The application of ceramic Rogers TC350 Substrate
Rogers TC350 substrate finds extensive application in high-frequency RF (Radio Frequency) and microwave circuits where performance, reliability, and thermal management are critical. Some key applications include:
- RF/Microwave Amplifiers:TC350’s low loss tangent and high thermal conductivity make it ideal for power amplifiers where minimizing signal loss and efficiently dissipating heat are essential for maintaining signal integrity and reliability.
- Antennas:Due to its stable dielectric constant and excellent dimensional stability, TC350 is used in antenna designs. It helps in achieving precise impedance matching and radiation characteristics across a wide range of frequencies.
- Wireless Communication Systems: TC350 substrates are employed in various wireless communication systems such as cellular base stations, satellite communications, and WiFi routers. They support high-speed data transmission and ensure minimal signal attenuation.
- Radar Systems: Radar systems require substrates that can handle high-power RF signals without significant loss. TC350’s high thermal conductivity helps in dissipating heat generated by radar components, ensuring reliable operation over extended periods.
- High-Speed Digital Applications:TC350 is utilized in high-speed digital circuits where maintaining signal integrity and reducing electromagnetic interference (EMI) are critical. Its low loss properties support high data rates and signal fidelity.
- Automotive Radar and Sensors:In automotive applications, TC350 substrates are used in radar sensors and communication modules for advanced driver assistance systems (ADAS). They provide the necessary electrical performance and reliability under harsh automotive environments.
- Aerospace and Defense:TC350 substrates meet the stringent requirements of aerospace and defense applications, including avionics, radar systems, and communication equipment. Their reliability in extreme temperatures and environmental conditions makes them suitable for mission-critical applications.
Overall, Rogers TC350 substrates are preferred in industries requiring high-frequency performance, thermal management capabilities, and reliability. Their applications span from telecommunications infrastructure to advanced electronic systems in aerospace, automotive, and defense sectors, where superior electrical properties and robust design are essential.
FAQs about Rogers TC350 Substrate
What is Rogers TC350 substrate?
Rogers TC350 substrate is a high-performance material designed for RF/microwave applications. It features low loss tangent, high thermal conductivity, and excellent electrical properties, making it suitable for high-frequency circuits.
What are the key advantages of using TC350 substrate?
The advantages include low signal attenuation (low loss tangent), effective thermal management, stable electrical performance across frequencies, and reliability in various environmental conditions.
What applications is TC350 substrate used for?
TC350 is used in RF amplifiers, antennas, wireless communication systems, radar systems, high-speed digital circuits, automotive radar sensors, and aerospace electronics due to its high-performance characteristics.
How does TC350 substrate compare to other materials like FR4?
TC350 offers significantly lower loss tangent and higher thermal conductivity compared to standard materials like FR4. This makes it preferable for applications requiring high-frequency performance and efficient heat dissipation.
What fabrication processes are involved in manufacturing TC350 substrates?
The fabrication process includes material preparation, prepreg manufacturing, lamination, drilling, copper plating, etching, surface treatment, final inspection, routing, and quality control measures to ensure performance consistency.
What are the environmental and reliability specifications of TC350 substrate?
TC350 substrates are designed to meet industry standards for environmental factors such as temperature, humidity, and mechanical stress. They undergo rigorous testing to ensure reliability and long-term performance stability.
Can TC350 substrates be used in high-power applications?
Yes, TC350 substrates are suitable for high-power applications such as RF amplifiers and radar systems due to their ability to manage heat effectively and maintain electrical performance under high-power conditions.
Where can I buy TC350 substrates, and what are the typical lead times?
TC350 substrates are available through authorized distributors and directly from Rogers Corporation. Lead times can vary based on order volume and customization requirements.