Rogers RT/duroid® 6010 Substrate Manufacturer
Rogers RT/duroid® 6010 Substrate Manufacturer,Rogers RT/duroid® 6010 Substrate is a high-performance PTFE-based glass fiber reinforced composite material renowned for its excellent high-frequency electrical properties and stable mechanical performance. With low loss tangent and precise dielectric constant, it is suitable for RF and microwave applications, supporting complex circuit designs and high-speed signal transmission. Widely used in communication equipment, satellite communications, radar systems, and other high-frequency electronic devices, Rogers RT/duroid® 6010 Substrate provides reliable performance and durability in demanding environments.
What is Rogers RT/duroid® 6010 Substrate?
Rogers RT/duroid® 6010 is a high-performance material used primarily in microwave and RF applications due to its excellent electrical properties and stability over a wide range of frequencies. It belongs to the RT/duroid® family of laminates, known for their reliability and consistency in demanding environments.
RT/duroid® 6010 substrates are characterized by their low dielectric loss, high thermal conductivity, and tight dimensional stability. These properties make them ideal for applications requiring high frequency performance, such as antennas, radar systems, satellite communications, and aerospace electronics. The material’s low moisture absorption and resistance to thermal cycling enhance its suitability for outdoor and harsh environmental conditions.
Manufactured by Rogers Corporation, RT/duroid® 6010 substrates typically consist of a ceramic-filled PTFE composite with a flame-retardant epoxy resin system. This composition results in a material with excellent mechanical strength, allowing for precise machining and fine-line etching during PCB fabrication processes. Engineers and designers value RT/duroid® 6010 for its ability to support high-frequency signals with minimal signal loss and dispersion, crucial for maintaining signal integrity in advanced electronic systems.
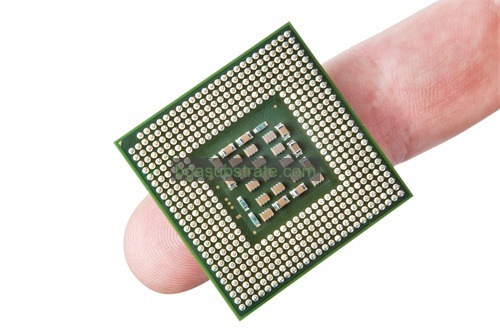
Rogers RT/duroid® 6010 Substrate Manufacturer
What is the Rogers RT/duroid® 6010 Substrate Design Guidelines?
Design guidelines for Rogers RT/duroid® 6010 substrates are crucial for ensuring optimal performance in high-frequency applications. Here are some key design considerations:
- Material Properties: Understand the electrical and mechanical properties of RT/duroid® 6010, including its dielectric constant (typically around 10.2), loss tangent (0.0023), and thermal conductivity (0.52 W/m·K). These properties influence signal propagation, power handling, and thermal management.
- Stackup Design: Design a PCB stackup that minimizes losses and matches impedance requirements. RT/duroid® 6010 is often used for RF and microwave circuits where controlled impedance is critical. Ensure proper layer arrangement to achieve desired impedance levels and signal integrity.
- Transmission Line Design: Use appropriate transmission line structures such as microstrips or coplanar waveguides (CPWs) based on your circuit requirements. Ensure consistent trace widths, spacing, and via structures to maintain impedance continuity and minimize reflections.
- Via Design: Pay attention to via placement and design to minimize impedance disruptions and signal loss. Consider using via fences or stitching vias to enhance signal integrity and reduce electromagnetic interference (EMI).
- Component Placement: Place components strategically to minimize signal path lengths and reduce parasitic effects. High-frequency components should be located close to each other and connected with short, direct traces to maintain signal integrity.
- Grounding: Implement a solid grounding strategy using ground planes or grids to provide low impedance paths for return currents. Proper grounding reduces noise and improves the overall performance of RF and microwave circuits.
- Thermal Management: Consider thermal dissipation requirements, especially in power amplifier or high-power RF applications. RT/duroid® 6010’s thermal conductivity helps in spreading heat efficiently, but ensure adequate thermal vias and heat sinking techniques are employed as needed.
- Manufacturing Constraints:Communicate design requirements clearly with PCB manufacturers familiar with handling high-frequency materials like RT/duroid® 6010. Ensure they can achieve tight tolerances and high-quality fabrication processes necessary for RF and microwave circuits.
By adhering to these design guidelines, engineers can leverage the excellent electrical and mechanical properties of Rogers RT/duroid® 6010 substrates to achieve reliable and high-performance RF and microwave circuit designs.
The advantages of Rogers RT/duroid® 6010 Substrate
Rogers RT/duroid® 6010 substrate offers several advantages that make it highly suitable for high-frequency RF and microwave applications:
- Low Dielectric Loss: RT/duroid® 6010 exhibits a low loss tangent (typically around 0.0023), which minimizes signal attenuation. This property is crucial for maintaining signal integrity and achieving high-frequency performance in RF circuits.
- High Thermal Conductivity: With a thermal conductivity of approximately 0.52 W/m·K, RT/duroid® 6010 effectively dissipates heat generated by high-power components. This thermal management capability enhances reliability and longevity in circuits operating at elevated power levels.
- Stable Electrical Properties: The material offers stable electrical characteristics over a wide frequency range, making it predictable and reliable for designing circuits operating from RF to microwave frequencies. This stability ensures consistent performance in various environmental conditions.
- Dimensional Stability: RT/duroid® 6010 maintains tight dimensional stability, which is critical for achieving precise and reliable fabrication of PCBs. It allows for fine-line etching and accurate machining of circuit features, essential for high-frequency applications.
- Mechanical Strength: The substrate’s composite construction, typically a ceramic-filled PTFE with an epoxy resin system, provides excellent mechanical strength. This strength supports the fabrication of complex PCB designs and ensures durability during handling and operation.
- Compatibility with High-Frequency Designs: RT/duroid® 6010 is specifically engineered for high-frequency applications where controlled impedance and minimal signal loss are paramount. It supports the design of antennas, radar systems, satellite communications, and other RF and microwave circuits requiring high performance.
- Environmental Resistance: The material’s low moisture absorption and resistance to environmental factors contribute to its reliability in outdoor and harsh operating conditions. This makes RT/duroid® 6010 suitable for aerospace, defense, and telecommunications applications.
Overall, Rogers RT/duroid® 6010 substrate’s combination of low loss, high thermal conductivity, stable electrical properties, and mechanical robustness makes it a preferred choice for demanding high-frequency electronic designs that prioritize performance and reliability.
What is the Rogers RT/duroid® 6010 Substrate Fabrication Process?
The fabrication process for Rogers RT/duroid® 6010 substrate involves several steps to ensure the material’s high performance and reliability in RF and microwave applications:
- Material Preparation: RT/duroid® 6010 substrate is typically supplied in sheet form with specific thicknesses and copper foil laminated on one or both sides. The material is stored and handled in controlled environments to prevent moisture absorption and maintain dimensional stability.
- Preparation for Etching: The substrate sheets are cleaned thoroughly to remove any contaminants that could affect adhesion or etching quality. This step ensures a clean surface for subsequent processing steps.
- Photoresist Application: A photoresist layer is applied to the substrate surface. This layer will be patterned to define the circuit traces and features required for the PCB design. The photoresist helps protect areas of the substrate that should remain after etching.
- Exposure and Development:The photoresist layer is exposed to UV light through a photomask that contains the desired circuit pattern. This exposure step transfers the pattern onto the photoresist. After exposure, the photoresist is developed to remove areas not exposed to UV light, revealing the underlying substrate where copper will be etched away.
- Etching: The substrate undergoes chemical etching to remove copper from the areas not protected by the developed photoresist. This process defines the circuit traces and features according to the pattern transferred from the photomask. Etching is carefully controlled to achieve precise trace widths and maintain consistent impedance characteristics across the PCB.
- Photoresist Stripping: After etching, the remaining photoresist is stripped from the substrate using appropriate solvents. This step prepares the PCB surface for further processing and inspection.
- Surface Finish Application: Depending on the application requirements, the PCB may undergo surface finish processes such as applying solder mask and finishing with hot air leveling (HAL), immersion gold (ENIG), or other finishes to protect exposed copper and facilitate soldering of components.
- Final Inspection and Testing: The fabricated PCB undergoes thorough inspection and testing to ensure it meets design specifications for electrical performance, dimensional accuracy, and reliability. This includes checks for impedance matching, solderability, and continuity of circuit traces.
Throughout the fabrication process, strict adherence to quality control measures is crucial to ensure that Rogers RT/duroid® 6010 substrates maintain their high-frequency performance characteristics, dimensional stability, and reliability in demanding RF and microwave applications.
The application of ceramic Rogers RT/duroid® 6010 Substrate
Rogers RT/duroid® 6010 substrate, being a high-performance material with excellent electrical properties, finds wide application in RF and microwave circuits where precision and reliability are critical. Some key applications include:
- Antennas: RT/duroid® 6010 substrates are used in the construction of high-frequency antennas due to their low dielectric loss and stable electrical properties. They enable efficient signal transmission and reception in communication systems, radar systems, satellite communications, and more.
- Aerospace and Defense: The material’s high thermal conductivity and mechanical strength make it suitable for aerospace and defense applications. It is used in radar systems, avionics, missile guidance systems, and electronic warfare equipment where reliability under extreme conditions is essential.
- Wireless Communications: RT/duroid® 6010 substrates support the design of RF amplifiers, filters, couplers, and other components in wireless communication networks. They ensure low signal loss and high signal integrity, critical for maintaining network performance.
- Satellite Systems: Given its ability to withstand thermal cycling and maintain dimensional stability, RT/duroid® 6010 is used in satellite communication systems for both payload electronics and ground-based equipment.
- Test and Measurement Equipment: The substrate’s predictable electrical properties and low loss tangent make it suitable for high-frequency test fixtures and measurement equipment. It ensures accurate signal transmission and measurement in laboratory environments.
- Automotive Radar: RT/duroid® 6010 substrates are employed in automotive radar systems for collision avoidance, adaptive cruise control, and other safety applications. Their high reliability and performance help meet stringent automotive industry standards.
- Medical Devices: In medical electronics, RT/duroid® 6010 substrates are utilized in RF generators, imaging equipment, and other medical devices requiring high-frequency performance and reliability.
- Industrial Applications: Industries requiring high-frequency signal processing, such as industrial automation and control systems, utilize RT/duroid® 6010 substrates for their robustness and ability to maintain signal integrity in harsh environments.
Overall, Rogers RT/duroid® 6010 substrate’s combination of low loss, high thermal conductivity, stability over a wide frequency range, and mechanical durability makes it a preferred choice for demanding applications in telecommunications, aerospace, defense, and other high-tech industries.
FAQs about Rogers RT/duroid® 6010 Substrate
What is RT/duroid® 6010 substrate used for?
RT/duroid® 6010 substrate is used primarily in RF and microwave applications where high-frequency performance, low loss tangent, and dimensional stability are critical. It finds applications in antennas, radar systems, satellite communications, wireless networks, and more.
What are the key properties of RT/duroid® 6010 substrate?
RT/duroid® 6010 substrate is known for its low dielectric loss (typically around 0.0023), high thermal conductivity (0.52 W/m·K), and stable electrical properties over a wide frequency range. It also offers excellent mechanical strength and dimensional stability.
How does RT/duroid® 6010 substrate compare to other materials like FR-4?
Unlike FR-4, which is a standard PCB material, RT/duroid® 6010 is specifically designed for high-frequency applications. It offers lower loss tangent, higher thermal conductivity, and better performance at RF and microwave frequencies, albeit at a higher cost.
What fabrication processes are involved in working with RT/duroid® 6010 substrate?
Fabrication of RT/duroid® 6010 substrates involves processes such as material preparation, photoresist application and patterning, etching to define circuit traces, surface finish application, and final inspection. These processes ensure the material’s performance and reliability.
Is RT/duroid® 6010 substrate suitable for outdoor or harsh environments?
Yes, RT/duroid® 6010 substrate is designed to withstand harsh environmental conditions due to its low moisture absorption and excellent dimensional stability. It is commonly used in aerospace, defense, and outdoor communication systems.
What are some typical design considerations when using RT/duroid® 6010 substrate?
Designers need to consider controlled impedance requirements, transmission line design (microstrips or CPWs), grounding strategies, thermal management, and compatibility with high-frequency components. These considerations ensure optimal performance and reliability of RF and microwave circuits.
Where can I purchase RT/duroid® 6010 substrate?
RT/duroid® 6010 substrate is available through authorized distributors of Rogers Corporation products. It’s important to source from reputable suppliers to ensure quality and authenticity.