Rogers RT/duroid® 6006 Substrate Manufacturer
Rogers RT/duroid® 6006 Substrate Manufacturer,Rogers RT/duroid® 6006 Substrate is a high-performance PTFE-based glass fiber reinforced composite material known for its excellent high-frequency electrical properties and stable mechanical performance. With a low loss tangent and precise dielectric constant, it is suitable for RF and microwave applications, supporting complex circuit designs and high-speed signal transmission. Widely used in communication equipment, satellite communications, radar systems, and other high-frequency electronic devices, Rogers RT/duroid® 6006 Substrate provides reliable performance and durability.
What is Rogers RT/duroid® 6006 Substrate?
Rogers RT/duroid® 6006 is a high-performance, ceramic-filled PTFE (Polytetrafluoroethylene) composite substrate material designed for high-frequency applications in PCB (Printed Circuit Board) manufacturing. It offers excellent electrical properties, including a low dielectric constant (εr) of 6.15 ± 0.15, which remains stable across a wide frequency range, making it ideal for microwave and RF (Radio Frequency) circuits. This stability ensures consistent signal integrity and minimal loss in high-frequency applications.
The RT/duroid® 6006 substrate also boasts a low loss tangent (tan δ) of 0.0026, which contributes to its efficient signal transmission capabilities. This characteristic is crucial in applications requiring high data rates or where signal attenuation must be minimized. Additionally, its high thermal conductivity helps in managing heat dissipation, which is beneficial for maintaining the reliability and performance of electronic devices operating at high frequencies.
Manufactured by Rogers Corporation, RT/duroid® 6006 substrates are available in various thicknesses and copper cladding options to suit different design requirements. They are widely used in industries such as telecommunications, aerospace, defense, and automotive electronics where high-frequency performance and reliability are critical. These substrates are compatible with standard PCB fabrication processes, enabling efficient integration into complex circuit designs while meeting stringent performance standards.
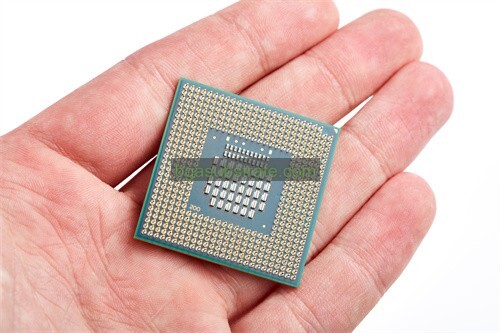
Rogers RT/duroid® 6006 Substrate Manufacturer
What is the Rogers RT/duroid® 6006 Substrate Design Guidelines?
Design guidelines for Rogers RT/duroid® 6006 substrate typically include several key considerations to ensure optimal performance in high-frequency PCB applications:
- Material Properties: Understand and utilize the electrical properties of RT/duroid® 6006, such as its low dielectric constant (εr), low loss tangent (tan δ), and thermal conductivity, to design circuits that minimize signal loss and maintain signal integrity.
- Stackup Design: Optimize the PCB stackup to achieve desired impedance control and signal routing efficiency. This involves selecting appropriate layer thicknesses, copper weights, and dielectric constants to match the impedance requirements of the circuit.
- Transmission Line Design: Use controlled impedance transmission lines to minimize signal reflections and losses. Design traces with appropriate widths and spacing to achieve the desired characteristic impedance, typically 50 ohms or other specified values depending on the application.
- Via Design: Ensure via structures are optimized for minimal impedance discontinuities and signal integrity. Consider using plated-through holes (PTH) or microvias depending on the density and frequency requirements of the circuit.
- Heat Management: Utilize the high thermal conductivity of RT/duroid® 6006 for effective heat dissipation in high-power applications. Design thermal vias or heatsinks as necessary to prevent overheating and ensure reliability.
- Material Handling and Processing: Follow recommended handling procedures during PCB fabrication to prevent contamination or damage to the substrate material, which could affect its electrical properties and performance.
- Environmental Considerations: Assess the substrate’s performance under varying environmental conditions, such as temperature and humidity, to ensure reliability and longevity of the PCB in different operating environments.
By adhering to these design guidelines, designers can leverage the superior electrical and thermal properties of Rogers RT/duroid® 6006 substrates to achieve high-performance, reliable PCB solutions for demanding high-frequency applications.
The advantages of Rogers RT/duroid® 6006 Substrate
Rogers RT/duroid® 6006 substrate offers several advantages that make it highly suitable for high-frequency electronic applications:
- Low Dielectric Constant (εr): RT/duroid® 6006 has a low dielectric constant of 6.15 ± 0.15, which remains stable over a wide frequency range. This property ensures minimal signal loss and excellent signal integrity, making it ideal for high-frequency circuits where maintaining consistent electrical performance is crucial.
- Low Loss Tangent (tan δ): With a low loss tangent of 0.0026, RT/duroid® 6006 exhibits low signal attenuation. This characteristic is essential for applications requiring high data rates or sensitive RF signals, ensuring efficient signal transmission and minimal energy loss.
- High Thermal Conductivity: The substrate’s high thermal conductivity helps in effective heat dissipation from electronic components, contributing to enhanced reliability and longevity of circuits operating at high power levels or in demanding thermal environments.
- Mechanical Stability: RT/duroid® 6006 maintains mechanical stability under various environmental conditions, including temperature fluctuations and humidity. This stability reduces the risk of dimensional changes or performance degradation over time, ensuring consistent performance in diverse operating environments.
- Compatibility with High-Frequency Designs: Designed for microwave and RF applications, RT/duroid® 6006 substrates are compatible with high-frequency circuit designs requiring precise impedance control, tight tolerances, and efficient signal propagation.
- Ease of Processing: The substrate is compatible with standard PCB fabrication processes, allowing for efficient manufacturing and integration into complex circuit designs. This compatibility helps reduce production costs and time-to-market for electronic products utilizing RT/duroid® 6006.
- Industry Standard:As a product from Rogers Corporation, a well-established manufacturer in the field of high-frequency materials, RT/duroid® 6006 adheres to industry standards and specifications, ensuring reliability and performance consistency across different applications.
Overall, Rogers RT/duroid® 6006 substrate’s combination of low dielectric constant, low loss tangent, high thermal conductivity, and mechanical stability makes it a preferred choice for demanding high-frequency and RF applications where performance, reliability, and signal integrity are paramount.
What is the Rogers RT/duroid® 6006 Substrate Fabrication Process?
The fabrication process for Rogers RT/duroid® 6006 substrate involves several key steps to ensure the material meets the high-performance requirements for high-frequency applications:
- Material Preparation: The process begins with the preparation of RT/duroid® 6006 material sheets. These sheets are typically composed of a ceramic-filled PTFE (Polytetrafluoroethylene) composite, which provides the substrate with its low dielectric constant (εr), low loss tangent (tan δ), and high thermal conductivity properties.
- Layer Stacking: Multiple layers of RT/duroid® 6006 material may be stacked together to achieve the desired thickness for the substrate. Each layer is inspected for uniformity and quality to ensure consistent electrical and mechanical properties across the substrate.
- Copper Cladding: The RT/duroid® 6006 material layers are clad with copper foil on one or both sides. Copper cladding is essential for forming conductive paths (traces) on the substrate to create the desired circuit patterns.
- Lamination: The layered structure undergoes lamination under controlled temperature and pressure conditions. This process bonds the copper-clad RT/duroid® 6006 layers together into a solid substrate. Proper lamination ensures good adhesion between layers and maintains the substrate’s dimensional stability.
- Drilling: After lamination, holes are drilled into the substrate where vias and component mounting holes will be located. Precision drilling is critical to maintain tight tolerances and ensure the integrity of signal paths and electrical connections.
- Circuit Patterning: Circuit patterns are created on the substrate by etching away excess copper using chemical etchants or plasma processes. This step defines the conductive traces and pads that form the electrical connections between components on the PCB.
- Surface Finishing: The exposed copper surfaces on the substrate are typically treated with surface finishes such as immersion gold (ENIG), immersion silver, or OSP (Organic Solderability Preservatives). These finishes improve solderability, protect against oxidation, and enhance the overall reliability of the PCB.
- Testing and Inspection: Throughout the fabrication process, rigorous testing and inspection procedures are employed to verify the substrate’s electrical performance, dimensional accuracy, and adherence to design specifications. This includes impedance testing, continuity checks, and visual inspection for defects.
- Final Fabrication: Once all processes are complete and the substrate meets quality standards, it is trimmed to final dimensions, inspected one last time, and prepared for shipment or further assembly into electronic products.
By following these fabrication steps with precision and quality control measures, manufacturers ensure that Rogers RT/duroid® 6006 substrates meet the stringent requirements of high-frequency applications, providing reliable performance in demanding electronic systems.
The application of ceramic Rogers RT/duroid® 6006 Substrate
Rogers RT/duroid® 6006 substrate finds application primarily in high-frequency electronic circuits where low loss, stable electrical properties, and high thermal conductivity are critical. Some common applications include:
- Microwave and RF Circuits: RT/duroid® 6006 substrates are widely used in microwave and radio frequency circuits due to their low dielectric constant (εr) and low loss tangent (tan δ). These properties ensure minimal signal loss and high signal integrity, making them suitable for applications such as radar systems, satellite communications, and wireless infrastructure.
- High-Speed Digital PCBs: In high-speed digital applications, RT/duroid® 6006 substrates help maintain signal integrity and reduce electromagnetic interference (EMI). They are used in PCBs for high-performance computing, data centers, and network equipment where fast data transmission rates are crucial.
- Aerospace and Defense: The substrate’s robust performance in harsh environments, coupled with its high thermal conductivity, makes it ideal for aerospace and defense applications. It is used in radar systems, avionics, military communication systems, and electronic warfare equipment where reliability under extreme conditions is essential.
- Automotive Electronics: RT/duroid® 6006 substrates are employed in automotive radar sensors, advanced driver-assistance systems (ADAS), and vehicle-to-vehicle communication systems. Their high-frequency capabilities and thermal stability support the demanding requirements of automotive electronics.
- Wireless Communication Equipment: Base stations, antennas, and other wireless communication equipment benefit from RT/duroid® 6006 substrates’ ability to handle high frequencies and maintain consistent performance over a wide range of temperatures and environmental conditions.
- Medical Devices: In medical electronics, where precision and reliability are paramount, RT/duroid® 6006 substrates are used in devices such as MRI machines, diagnostic equipment, and implantable medical devices that require high-frequency signal processing and low noise operation.
- Industrial Electronics: RT/duroid® 6006 substrates are applied in industrial control systems, test and measurement instruments, and other industrial electronics where high-frequency signal processing and reliability are critical for efficient operation.
Overall, the application of Rogers RT/duroid® 6006 substrate spans across industries that demand high-performance electronic solutions with stringent requirements for signal integrity, thermal management, and reliability in high-frequency environments.
FAQs about Rogers RT/duroid® 6006 Substrate
What is RT/duroid® 6006 substrate?
RT/duroid® 6006 is a high-performance, ceramic-filled PTFE composite substrate designed for high-frequency applications in PCB manufacturing. It offers low dielectric constant, low loss tangent, and high thermal conductivity properties.
What are the key advantages of RT/duroid® 6006 substrate?
RT/duroid® 6006 substrate offers advantages such as low signal loss, excellent signal integrity, high thermal conductivity for heat dissipation, mechanical stability, and compatibility with high-frequency designs.
Where is RT/duroid® 6006 substrate commonly used?
It is commonly used in applications such as microwave and RF circuits, high-speed digital PCBs, aerospace and defense electronics, automotive radar systems, wireless communication equipment, medical devices, and industrial electronics.
What are the typical electrical properties of RT/duroid® 6006 substrate?
RT/duroid® 6006 substrate typically has a low dielectric constant (εr) of 6.15 ± 0.15 and a low loss tangent (tan δ) of 0.0026, which remain stable over a wide frequency range.
How does RT/duroid® 6006 substrate compare to other materials?
Compared to other substrates, RT/duroid® 6006 offers superior high-frequency performance, low loss characteristics, and good thermal management capabilities, making it suitable for demanding electronic applications.
What fabrication processes are involved in manufacturing RT/duroid® 6006 substrate?
The fabrication process includes material preparation, layer stacking, copper cladding, lamination, drilling, circuit patterning, surface finishing, testing, and final fabrication steps to ensure high-quality substrate production.
Is RT/duroid® 6006 substrate compatible with standard PCB fabrication methods?
Yes, RT/duroid® 6006 substrate is compatible with standard PCB fabrication methods, allowing for efficient manufacturing and integration into complex high-frequency circuit designs.