Rogers RT/duroid® 6002 Substrate Manufacturer
Rogers RT/duroid® 6002 Substrate Manufacturer,Rogers RT/duroid® 6002 Substrate is a high-performance PTFE-based glass fiber reinforced composite material known for its excellent high-frequency electrical properties and stable mechanical performance. Its low loss tangent and precise dielectric constant make it highly effective in RF and microwave applications, supporting complex circuit designs and high-speed signal transmission. Widely used in communication equipment, satellite communications, radar systems, and other high-frequency fields, Rogers RT/duroid® 6002 Substrate provides reliable performance and durability in demanding electronic environments.
What is Rogers RT/duroid® 6002 Substrate?
Rogers RT/duroid® 6002 is a high-frequency laminate substrate renowned for its excellent electrical and mechanical properties, specifically designed for RF and microwave applications. It features a PTFE (Polytetrafluoroethylene) composite material reinforced with woven fiberglass, ensuring low loss and stable performance across a wide range of frequencies.
The key attributes of Rogers RT/duroid® 6002 include high thermal conductivity, which helps in dissipating heat efficiently, crucial for maintaining signal integrity in high-power applications. Its low moisture absorption and excellent dimensional stability make it suitable for environments with varying temperature and humidity conditions.
Engineered with tight dielectric constant and thickness tolerances, RT/duroid® 6002 ensures consistent electrical performance, supporting precise impedance matching and signal transmission. These characteristics make it ideal for applications such as aerospace and defense systems, satellite communication, radar systems, and high-frequency PCB designs where reliability and performance are critical.
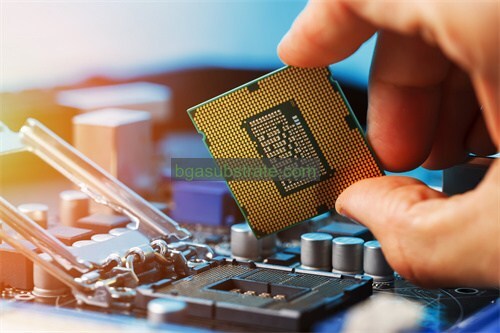
Rogers RT/duroid® 6002 Substrate Manufacturer
What is the Rogers RT/duroid® 6002 Substrate Design Guidelines?
Design guidelines for Rogers RT/duroid® 6002 substrate typically include several key considerations to ensure optimal performance in RF and microwave applications:
- Material Properties: Understand and utilize the specific electrical properties of RT/duroid® 6002, such as its dielectric constant (εr) and loss tangent (tan δ), which are crucial for designing circuits with precise impedance matching and minimal signal loss.
- Layer Stackup Design:Plan the layer stackup carefully to achieve desired impedance levels and minimize signal interference. Consider the thickness and order of copper layers, ground planes, and signal traces to optimize signal integrity.
- Transmission Line Design: Use appropriate transmission line structures (e.g., microstrip, stripline) based on frequency requirements and signal propagation characteristics. Calculate line widths and spacings to achieve the desired characteristic impedance.
- Grounding and Decoupling: Ensure proper grounding techniques to minimize noise and interference. Use vias and stitching capacitors where necessary for effective decoupling and to maintain signal integrity.
- Thermal Management: Address heat dissipation challenges by designing adequate thermal vias and spreading copper areas to manage power dissipation and maintain substrate integrity under high-power conditions.
- Mechanical Considerations: Account for mechanical stability and dimensional tolerance in the substrate design to withstand thermal cycling and mechanical stress typical in aerospace and defense applications.
- Manufacturing Constraints:Work closely with PCB manufacturers familiar with handling RT/duroid® 6002 to optimize fabrication processes and ensure compliance with material handling guidelines to prevent contamination and maintain substrate properties.
By adhering to these guidelines, designers can leverage the high-performance characteristics of Rogers RT/duroid® 6002 substrate effectively, ensuring reliable operation in demanding RF and microwave circuits.
The advantages of Rogers RT/duroid® 6002 Substrate
Rogers RT/duroid® 6002 substrate offers several advantages that make it a preferred choice for high-frequency RF and microwave applications:
- Low Dielectric Loss: RT/duroid® 6002 exhibits low dielectric loss (low dissipation factor), which minimizes signal attenuation and ensures high signal integrity over a wide frequency range. This characteristic is crucial for maintaining the efficiency and reliability of RF and microwave circuits.
- High Thermal Conductivity: The substrate’s high thermal conductivity allows for efficient heat dissipation, making it suitable for applications requiring high-power handling capability. It helps in reducing thermal gradients and maintaining stable electrical performance even under demanding operating conditions.
- Excellent Dimensional Stability: RT/duroid® 6002 demonstrates excellent dimensional stability, ensuring consistent electrical properties over time and under varying environmental conditions (temperature and humidity). This stability contributes to long-term reliability and performance consistency in critical applications.
- Precise Electrical Properties: It offers tight control over electrical properties such as dielectric constant (εr) and loss tangent (tan δ), enabling precise impedance matching and predictable signal propagation characteristics. This capability is essential for designing high-performance RF and microwave circuits.
- Wide Range of Applications: Due to its high performance and reliability, RT/duroid® 6002 is used in diverse applications including aerospace and defense systems, satellite communications, radar systems, automotive radar, and high-frequency PCB designs. Its versatility and robustness make it suitable for both commercial and military applications.
- Manufacturability: Rogers RT/duroid® 6002 substrate is well-suited for standard PCB manufacturing processes, facilitating ease of fabrication and integration into complex circuit designs. It supports various fabrication techniques, including multilayer PCBs and high-density interconnects, while maintaining high yield and reliability.
Overall, Rogers RT/duroid® 6002 substrate’s combination of low loss, high thermal conductivity, dimensional stability, and precise electrical properties positions it as a leading choice for demanding RF and microwave applications where performance, reliability, and longevity are critical considerations.
What is the Rogers RT/duroid® 6002 Substrate Fabrication Process?
The fabrication process for Rogers RT/duroid® 6002 substrate typically involves several key steps to ensure the material’s properties and performance characteristics are preserved:
- Material Preparation: The process begins with preparing the RT/duroid® 6002 material sheets. These sheets are typically supplied with specified thickness and copper cladding on one or both sides, depending on the application requirements.
- Layer Preparation:If needed, the copper layers are laminated onto the RT/duroid® 6002 material sheets. This lamination process ensures a strong bond between the copper and the substrate, essential for electrical conductivity and mechanical stability.
- Circuit Design and Imaging:The circuit design, including trace patterns and component placements, is transferred onto the copper-clad RT/duroid® 6002 sheets using photolithography or direct imaging methods. This step defines the electrical pathways and connections within the PCB.
- Etching:The excess copper that is not part of the desired circuit pattern is etched away using chemical etchants. This process defines the final shape and dimensions of the conductive traces and pads on the substrate.
- Drilling:Precision holes are drilled through the substrate where vias are required to connect different layers of the PCB. These vias enable electrical connections between the conductive layers and facilitate multilayer PCB designs.
- Plating:After drilling, the vias are typically plated with conductive materials (such as copper) to ensure reliable electrical connections between the different layers of the PCB. This plating process enhances the PCB’s electrical performance and durability.
- Surface Finish:The PCB’s surface is finished with a suitable coating to protect the copper traces from oxidation and ensure solderability during component assembly. Common surface finishes include HASL (Hot Air Solder Leveling), ENIG (Electroless Nickel Immersion Gold), and OSP (Organic Solderability Preservatives).
- Inspection and Testing:Throughout the fabrication process, quality checks and inspections are conducted to verify dimensional accuracy, electrical continuity, and adherence to design specifications. Electrical testing may include impedance measurements and signal integrity tests to ensure the PCB meets performance requirements.
- Final Assembly:Once fabricated and tested, the RT/duroid® 6002 PCBs are ready for component assembly. Surface-mount and through-hole components are soldered onto the PCB, and functional testing may be performed to ensure proper operation.
By following these fabrication steps, manufacturers can produce Rogers RT/duroid® 6002 substrates that meet stringent performance standards for high-frequency RF and microwave applications, ensuring reliability and optimal electrical performance in demanding environments.
The application of ceramic Rogers RT/duroid® 6002 Substrate
Rogers RT/duroid® 6002 substrate, despite its name suggesting ceramic properties, is actually a high-frequency laminate material designed primarily for RF (Radio Frequency) and microwave applications rather than being a traditional ceramic substrate. Here are some common applications where RT/duroid® 6002 substrate is extensively used:
- Aerospace and Defense: RT/duroid® 6002 is widely employed in aerospace and defense systems due to its high reliability, low loss tangent, and excellent dimensional stability. It is used in radar systems, satellite communications, electronic warfare systems, and avionics where high-frequency performance and durability are critical.
- Telecommunications: In telecommunications infrastructure, RT/duroid® 6002 substrates are utilized in high-frequency PCB designs for base stations, antennas, RF amplifiers, and other wireless communication equipment. Its low loss characteristics help in minimizing signal attenuation and maximizing transmission efficiency.
- Automotive Radar: With the rise of autonomous driving technologies, RT/duroid® 6002 is increasingly used in automotive radar systems. It supports high-frequency RF circuits necessary for collision avoidance, adaptive cruise control, and other radar-based safety features.
- Medical Devices: In medical electronics, RT/duroid® 6002 substrates find applications in devices such as MRI coils, RF ablation systems, and medical telemetry equipment where reliable RF performance is crucial for accurate diagnosis and treatment.
- Industrial Applications: Industrial equipment and instrumentation that require precise RF and microwave signal processing often incorporate RT/duroid® 6002 substrates. This includes test and measurement instruments, industrial automation systems, and sensors operating at high frequencies.
- Consumer Electronics: Although less common in consumer electronics due to its specialized nature, RT/duroid® 6002 substrates may be used in high-frequency applications such as wireless communication devices and high-performance computing where RF performance is a priority.
Overall, the application of Rogers RT/duroid® 6002 substrate spans across industries where high-frequency, low-loss, and reliable electrical performance are essential requirements. Its use ensures that RF and microwave circuits maintain signal integrity, efficiency, and stability even in challenging operational environments.
FAQs about Rogers RT/duroid® 6002 Substrate
What is RT/duroid® 6002 substrate?
RT/duroid® 6002 is a high-frequency laminate material developed by Rogers Corporation. It consists of a PTFE (Polytetrafluoroethylene) composite reinforced with woven fiberglass, designed for RF and microwave applications requiring low loss and high reliability.
What are the key properties of RT/duroid® 6002 substrate?
RT/duroid® 6002 offers low dielectric loss, high thermal conductivity, excellent dimensional stability, and precise electrical properties (dielectric constant and loss tangent). These properties make it ideal for applications demanding high-frequency performance.
What applications is RT/duroid® 6002 substrate used in?
It is commonly used in aerospace and defense systems (radar, satellite communication), telecommunications (base stations, antennas), automotive radar, medical electronics (MRI coils, RF ablation systems), industrial equipment (test and measurement instruments), and other high-frequency RF and microwave circuits.
How does RT/duroid® 6002 substrate compare to other materials like FR-4?
Compared to FR-4 (a standard PCB material), RT/duroid® 6002 offers significantly lower dielectric loss and better electrical performance at higher frequencies. It is specifically engineered for applications where signal integrity and performance under high-frequency conditions are critical.
What are the benefits of using RT/duroid® 6002 substrate?
The benefits include minimized signal attenuation, enhanced thermal conductivity for heat dissipation, stable electrical performance over a wide temperature range, and suitability for complex multilayer PCB designs.
How is RT/duroid® 6002 substrate fabricated?
The fabrication process involves material preparation, layer lamination, circuit design and imaging, etching of copper traces, drilling of vias, plating for interconnection, surface finishing, inspection, and final assembly. This process ensures the substrate meets stringent performance standards.
Where can RT/duroid® 6002 substrate be sourced?
RT/duroid® 6002 substrates are available through authorized distributors of Rogers Corporation or directly from PCB manufacturers specializing in high-frequency applications. These suppliers ensure proper handling and adherence to Rogers’ material specifications.