Rogers RT/duroid® 5880 Substrate Manufacturer
Rogers RT/duroid® 5880 Substrate Manufacturer,Rogers RT/duroid® 5880 Substrate is a high-performance laminate renowned for its exceptional RF/microwave properties. Constructed from a ceramic-filled PTFE composite, it offers low dielectric loss and stable electrical characteristics up to 40 GHz. The substrate provides robust mechanical strength and thermal stability, ensuring reliability in demanding environments such as aerospace and telecommunications. RT/duroid® 5880 supports intricate circuit layouts and miniaturization, facilitating efficient signal transmission with reduced loss. Its consistent performance makes it ideal for applications requiring precise RF characteristics and high reliability, including radar systems, satellite communications, and high-frequency electronic devices where signal integrity is critical.
What is Rogers RT/duroid® 5880 Substrate?
Rogers RT/duroid® 5880 is a high-frequency circuit material renowned for its excellent electrical properties and reliability in microwave applications. It belongs to the family of PTFE composites, combining low dielectric constant (εr ≈ 2.2) with a stable and predictable dielectric constant over a wide range of frequencies. This makes it ideal for use in RF and microwave circuit designs where signal integrity and minimal loss are critical.
The substrate features a tightly controlled dielectric constant tolerance of ±0.04, ensuring consistent performance across production batches. Its low loss tangent (typically around 0.0009) contributes to high signal fidelity by minimizing signal attenuation. These properties are essential for applications such as high-frequency antennas, radar systems, satellite communications, and wireless networks.
RT/duroid® 5880 is available in various thicknesses, providing flexibility in designing circuits with different impedance requirements. It is compatible with standard fabrication processes used in the electronics industry, including etching, plating, and soldering. Engineers and designers often choose RT/duroid® 5880 for its proven performance in demanding environments where stable electrical characteristics and high reliability are paramount.
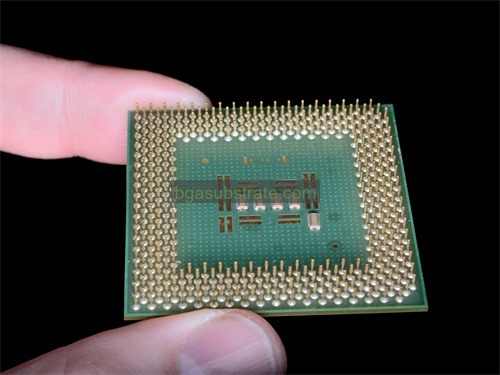
Rogers RT/duroid® 5880 Substrate Manufacturer
What is the Rogers RT/duroid® 5880 Substrate Design Guidelines?
Rogers RT/duroid® 5880 is a high-frequency laminate material known for its excellent electrical and mechanical properties, commonly used in RF/microwave applications. Here are some design guidelines for Rogers RT/duroid® 5880 substrate:
- Dielectric Constant (εr): RT/duroid® 5880 has a stable dielectric constant of around 2.2, which remains consistent across a wide frequency range. This property is critical for maintaining signal integrity in high-frequency circuits.
- Loss Tangent (Dissipation Factor): The low loss tangent (typically around 0.0009) ensures minimal signal loss, making it suitable for high-frequency applications where signal fidelity is crucial.
- Thickness Tolerance: Ensure that the substrate thickness remains within specified tolerances to maintain consistent electrical performance. Rogers RT/duroid® 5880 is available in various thicknesses to suit different design requirements.
- Copper Cladding: Properly adhere to guidelines for copper cladding thickness and quality to optimize conductivity and minimize losses.
- Fabrication Techniques:Follow recommended fabrication processes, such as drilling, routing, and etching, to avoid delamination and ensure dimensional stability.
- Environmental Considerations:Consider the substrate’s performance under different environmental conditions, such as temperature and humidity, as it may affect its electrical properties.
- Stack-up Design: Optimize the layer stack-up to achieve desired impedance levels and signal integrity. Properly design ground planes and signal traces to minimize electromagnetic interference (EMI) and crosstalk.
- Mechanical Properties: Ensure that mechanical properties, such as dimensional stability and rigidity, are suitable for the intended application, especially in harsh environments or applications requiring reliability.
These guidelines help engineers and designers leverage the superior electrical characteristics of Rogers RT/duroid® 5880 for RF/microwave circuits, ensuring optimal performance and reliability in high-frequency applications.
The advantages of Rogers RT/duroid® 5880 Substrate
Rogers RT/duroid® 5880 substrate offers several advantages that make it highly suitable for RF/microwave applications:
- Stable Electrical Properties: RT/duroid® 5880 maintains a stable dielectric constant (εr) of approximately 2.2 over a wide frequency range. This stability ensures predictable electrical performance and impedance matching, critical for maintaining signal integrity in high-frequency circuits.
- Low Loss Tangent: It features a low dissipation factor (loss tangent), typically around 0.0009, which results in minimal signal loss. This characteristic is crucial for applications requiring high Q factors and low insertion loss, enhancing overall circuit efficiency.
- High Frequency Capability: Designed for high-frequency applications, RT/duroid® 5880 supports operation up to microwave frequencies (often beyond 10 GHz), making it suitable for telecommunications, aerospace, radar systems, and other demanding RF applications.
- Mechanical Stability: The substrate exhibits excellent mechanical properties, including dimensional stability and thermal resistance. This stability ensures reliable performance under varying environmental conditions, such as temperature fluctuations and humidity.
- Ease of Fabrication:RT/duroid® 5880 is compatible with standard PCB fabrication processes, including drilling, etching, and soldering. Its robustness allows for intricate designs and fine trace widths without compromising performance.
- Durability and Reliability: Known for its durability, RT/duroid® 5880 offers long-term reliability in harsh operating environments. It maintains its electrical and mechanical properties over extended periods, reducing the need for frequent maintenance or replacement.
- Broad Availability: Rogers Corporation, the manufacturer of RT/duroid® 5880, provides comprehensive technical support and availability worldwide. This ensures consistent quality and accessibility for designers and engineers across different regions.
Overall, Rogers RT/duroid® 5880 substrate combines superior electrical performance with mechanical robustness, making it a preferred choice for high-frequency RF/microwave applications where reliability, low loss, and stable performance are critical.
What is the Rogers RT/duroid® 5880 Substrate Fabrication Process?
The fabrication process for Rogers RT/duroid® 5880 substrate involves several key steps to ensure optimal performance and reliability in high-frequency applications. Here’s an overview of the typical fabrication process:
- Material Selection: Begin with selecting the appropriate thickness and size of RT/duroid® 5880 substrate sheets based on the specific design requirements and application needs.
- Cleaning and Preparation: Clean the substrate surfaces thoroughly to remove any contaminants that could affect adhesion and subsequent processing steps. Ensure the substrate is free from dust, oils, and residues.
- Copper Cladding: Apply copper foil to both sides of the RT/duroid® 5880 substrate through a lamination process. The copper foil thickness is chosen based on the desired electrical performance and current-carrying capacity of the circuit.
- Photoresist Application: Apply a photoresist layer over the copper-clad surfaces. This layer acts as a protective mask during the subsequent etching process, defining the pattern of conductive traces and features.
- Exposure and Development: Use a photomask to expose the desired circuit pattern onto the photoresist layer using UV light. Develop the exposed photoresist to remove areas where copper is to be etched away, leaving behind the pattern of conductive traces.
- Etching: Immerse the substrate in an etchant solution (typically ferric chloride or ammonium persulfate) to dissolve the exposed copper areas not protected by the developed photoresist. This step defines the final conductive traces and circuit patterns on the substrate.
- Strip and Clean: Remove the remaining photoresist and any etchant residues from the substrate through a stripping process. Thoroughly clean the substrate to ensure it is free from contaminants that could affect subsequent assembly and testing processes.
- Drilling: Drill holes through the substrate at specified locations for component mounting and interconnection purposes. The drilling process must be precise to avoid damage to the substrate and ensure alignment with the circuit design.
- Surface Finish: Apply a surface finish to the exposed copper surfaces to enhance solderability and prevent oxidation. Common surface finishes include electroless nickel immersion gold (ENIG), immersion silver, or organic solderability preservatives (OSP).
- Inspection and Testing: Perform visual inspection and electrical testing to verify the integrity of the fabricated circuit traces, dimensions, and electrical properties. This ensures that the RT/duroid® 5880 substrate meets the required specifications and performance criteria.
- Final Assembly: If required, assemble components onto the substrate using soldering or other bonding techniques. This step completes the fabrication of the RT/duroid® 5880-based PCB or circuit assembly ready for functional testing and deployment.
By following these steps meticulously, manufacturers can achieve high-quality RT/duroid® 5880 substrates that deliver excellent electrical performance, reliability, and durability in demanding RF/microwave applications.
The application of ceramic Rogers RT/duroid® 5880 Substrate
Rogers RT/duroid® 5880 substrate, despite its name suggesting a ceramic material, is actually a PTFE-based (Polytetrafluoroethylene) composite laminate. It’s renowned for its exceptional electrical properties, making it ideal for various high-frequency applications in RF/microwave engineering. Here are some key applications where RT/duroid® 5880 substrate is commonly used:
- RF/Microwave Circuits: RT/duroid® 5880 is extensively used in the fabrication of RF and microwave circuits due to its stable dielectric constant (εr ≈ 2.2) and low loss tangent (typically around 0.0009). These properties ensure minimal signal loss and consistent performance across a wide frequency range, typically up to and beyond 10 GHz.
- Antennas: It’s employed in the construction of antennas for wireless communication systems, radar applications, and satellite communications. The substrate’s low loss characteristics help in achieving high antenna efficiency and signal transmission/reception performance.
- Aerospace and Defense: RT/duroid® 5880 is preferred in aerospace and defense applications where reliability, high performance, and resistance to environmental conditions (such as temperature variations and moisture) are critical. It’s used in radar systems, avionics, military communication equipment, and electronic warfare systems.
- Telecommunications: It finds application in telecommunications infrastructure, including base stations, repeaters, and other wireless communication equipment. The substrate’s ability to maintain signal integrity at high frequencies contributes to the efficiency and reliability of telecommunications networks.
- Test and Measurement Equipment:RT/duroid® 5880 is utilized in the construction of test fixtures, probes, and high-frequency test boards used in laboratories and production environments. Its predictable electrical properties facilitate accurate measurements and calibration processes.
- Satellite Systems: In satellite communication systems, RT/duroid® 5880 substrates are used for designing high-frequency circuitry, feed networks, and signal processing components. Its durability and performance in space environments make it suitable for satellite applications.
- Medical Devices: In medical electronics, particularly in devices requiring high-frequency signal processing and transmission (such as MRI machines and medical imaging equipment), RT/duroid® 5880 substrates can be used to ensure reliable performance and signal integrity.
- Automotive Radar: With the increasing adoption of radar-based driver assistance systems and autonomous driving technologies, RT/duroid® 5880 substrates are employed in automotive radar systems for collision detection, adaptive cruise control, and other safety features.
Overall, Rogers RT/duroid® 5880 substrate’s combination of low loss, stable electrical properties, and mechanical robustness makes it a versatile choice for demanding applications in industries requiring high-frequency performance and reliability.
FAQs about Rogers RT/duroid® 5880 Substrate
What is RT/duroid® 5880 substrate made of?
RT/duroid® 5880 is a composite laminate material based on PTFE (Polytetrafluoroethylene) with glass microfibers for reinforcement. It features a low loss tangent and stable dielectric constant suitable for high-frequency applications.
What are the key electrical properties of RT/duroid® 5880?
RT/duroid® 5880 has a dielectric constant (εr) of approximately 2.2 and a low dissipation factor (loss tangent) of around 0.0009. These properties ensure minimal signal loss and consistent performance across a wide frequency range, typically up to and beyond 10 GHz.
What applications is RT/duroid® 5880 substrate suitable for?
It is widely used in RF/microwave circuits, antennas, aerospace and defense systems, telecommunications infrastructure, test and measurement equipment, satellite systems, medical electronics, automotive radar, and other high-frequency applications requiring reliable performance.
How does RT/duroid® 5880 substrate compare to other materials like FR4?
Compared to FR4 (a common PCB substrate material), RT/duroid® 5880 offers superior electrical performance at high frequencies with lower loss and more stable dielectric properties. It is more suitable for applications where signal integrity and high-frequency operation are critical.
What are the advantages of using RT/duroid® 5880 substrate?
The substrate offers advantages such as low loss, stable electrical properties, high frequency capability, mechanical robustness, and compatibility with standard PCB fabrication processes. It ensures high reliability and performance in demanding environments.
Can RT/duroid® 5880 be used in high-power applications?
Yes, RT/duroid® 5880 can be used in high-power applications, provided that proper design considerations are taken to manage heat dissipation and ensure thermal stability. It is often used in power amplifiers and other RF components.
How is RT/duroid® 5880 substrate fabricated?
The fabrication process includes steps such as material selection, cleaning, copper cladding, photoresist application, exposure and development, etching, drilling, surface finish application, inspection, and testing to ensure the substrate meets specifications.