Rogers 4835 Substrate Manufacturer
Rogers 4835 Substrate Manufacturer,Rogers 4835 Substrate is a high-frequency laminate designed for advanced RF/microwave applications. Composed of woven fiberglass reinforced with PTFE (Polytetrafluoroethylene) composite, it delivers exceptional electrical performance with low dielectric loss and stable properties across frequencies up to 40 GHz. The substrate’s robust mechanical strength and thermal stability ensure reliable operation in challenging environments, making it ideal for aerospace, defense, and telecommunications sectors. Rogers 4835 supports precise circuit designs and miniaturization, enabling efficient signal transmission and high reliability. Its capability to maintain signal integrity and performance makes it a preferred choice for high-speed digital communications and radar systems where consistency and durability are crucial.
What is Rogers 4835 Substrate?
Rogers 4835 is a type of high-frequency laminate substrate used primarily in RF (Radio Frequency) and microwave applications. It belongs to the family of high-performance PCB (Printed Circuit Board) materials designed to meet stringent requirements for signal integrity, low loss, and reliability at high frequencies.
Rogers 4835 substrate is known for its excellent electrical properties, including low dielectric loss and stable dielectric constant over a wide range of frequencies. This makes it suitable for applications such as wireless communications, radar systems, satellite communications, and other RF/microwave circuits where maintaining signal integrity is crucial.
Key characteristics of Rogers 4835 include its relatively low dissipation factor (loss tangent), which helps in minimizing signal attenuation, and its high thermal conductivity for effective heat dissipation. These properties make it a preferred choice for designing high-frequency circuits that operate efficiently and reliably.
In terms of construction, Rogers 4835 typically consists of a woven fiberglass reinforced ceramic-filled PTFE (Polytetrafluoroethylene) composite substrate with copper cladding on one or both sides. The choice of copper thickness can vary based on specific application requirements, ensuring flexibility in design while maintaining performance.
Overall, Rogers 4835 substrate’s combination of high-frequency performance, low loss, and thermal stability positions it as a critical material in advanced RF and microwave circuit designs where precision and reliability are paramount.
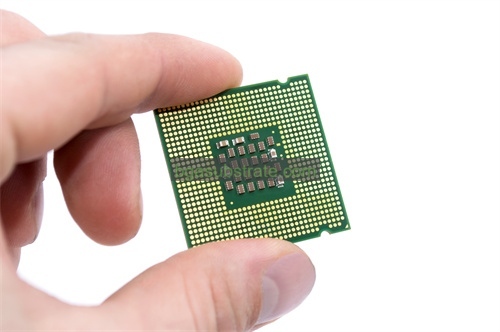
Rogers 4835 Substrate Manufacturer
What is the Rogers 4835 Substrate Design Guidelines?
Rogers 4835 is a high-frequency laminate material used in RF and microwave applications. Here are some general design guidelines for Rogers 4835 substrate:
- Dielectric Constant (Dk): Rogers 4835 has a relatively stable and low dielectric constant (Dk) of around 3.48 at 10 GHz. Ensure that the design takes into account this specific Dk value for accurate signal propagation and impedance matching.
- Loss Tangent (Df): The loss tangent (Df) of Rogers 4835 is typically low, contributing to low signal loss and improved performance at high frequencies. Design considerations should focus on minimizing conductor losses and optimizing trace widths accordingly.
- Thickness: Rogers 4835 substrates are available in various thicknesses. The chosen thickness affects impedance control, mechanical stability, and overall performance. Ensure the substrate thickness is suitable for the desired application frequencies and mechanical requirements.
- Copper Cladding: Proper adhesion and quality of copper cladding are crucial for maintaining consistent electrical performance. Design guidelines recommend specific copper thicknesses and treatments to optimize signal integrity and reliability.
- Fabrication Tolerances: Pay attention to fabrication tolerances, such as etching precision and layer alignment, to maintain signal integrity and minimize manufacturing variations that could affect performance.
- Environmental Considerations: Rogers 4835 substrates are designed to withstand a range of environmental conditions. Ensure that the design considers factors such as temperature stability, moisture resistance, and durability to maintain long-term reliability.
- RF Performance: Given its high-frequency capabilities, designs should be optimized for RF performance, including impedance matching, signal attenuation, and power handling capabilities.
These guidelines are essential to ensure that designs utilizing Rogers 4835 substrates achieve optimal performance and reliability in high-frequency applications.
The advantages of Rogers 4835 Substrate
Rogers 4835 substrate offers several advantages, particularly in high-frequency RF and microwave applications:
- Low Dielectric Loss: Rogers 4835 has a low loss tangent (typically around 0.0037 at 10 GHz), which results in minimal signal loss. This characteristic is crucial for maintaining signal integrity and achieving high-performance in RF circuits.
- Stable Dielectric Constant (Dk): The substrate exhibits a stable and predictable dielectric constant (Dk) of approximately 3.48 at 10 GHz. This stability ensures consistent impedance characteristics across different frequencies and temperatures, which is critical for maintaining signal integrity and achieving accurate performance in RF circuits.
- Excellent High-Frequency Performance: Rogers 4835 is designed to perform well at high frequencies, making it suitable for applications requiring high data rates, wide bandwidths, and low insertion losses. It supports frequencies up to 40 GHz and beyond, making it ideal for various wireless communication systems and radar applications.
- Thermal Stability: The substrate material offers good thermal stability, maintaining its electrical properties over a wide temperature range. This characteristic ensures reliable performance in environments with fluctuating temperatures, such as aerospace and automotive applications.
- Mechanical Durability: Rogers 4835 substrates are engineered to withstand mechanical stresses and maintain dimensional stability during fabrication and assembly processes. This durability contributes to the overall reliability and longevity of RF circuit designs.
- Process Compatibility:It is compatible with standard PCB manufacturing processes, including drilling, plating, and etching. This ease of processing facilitates cost-effective production and allows for complex RF circuit designs to be implemented efficiently.
- Broad Application Suitability: Due to its high-performance characteristics, Rogers 4835 substrate finds applications in various industries, including telecommunications, satellite communications, automotive radar systems, and military electronics, where high-frequency performance and reliability are critical.
Overall, Rogers 4835 substrate’s combination of low loss tangent, stable Dk, high-frequency capability, and mechanical robustness makes it a preferred choice for demanding RF and microwave applications requiring excellent performance and reliability.
What is the Rogers 4835 Substrate Fabrication Process?
The fabrication process for Rogers 4835 substrate involves several steps to ensure the material’s properties are preserved while achieving precise circuit patterns and structures. Here are the key steps typically involved in the fabrication process:
- Material Preparation:Rogers 4835 substrate material is received in the form of sheets or panels with specific thicknesses. These sheets are inspected for quality and dimensional accuracy.
- Circuit Design and Layout:The circuit design is prepared using specialized PCB design software. This involves determining the placement of components, signal traces, and ground planes while considering the high-frequency characteristics and impedance requirements of the Rogers 4835 substrate.
- Substrate Cleaning:Before processing, the substrate surfaces are cleaned thoroughly to remove any contaminants that could affect adhesion or circuit performance. This step typically involves using cleaning solutions and rinsing processes.
- Lamination:Rogers 4835 substrate is typically laminated with copper foil on one or both sides. The lamination process involves applying heat and pressure to bond the copper foil to the substrate material. This step ensures good adhesion and conductivity for subsequent circuit fabrication.
- Photoresist Application:A layer of photoresist is applied onto the copper-clad surface of the substrate. This photoresist layer will be used to define the circuit patterns through a photolithography process.
- Exposure and Development:The circuit design is transferred onto the substrate by exposing the photoresist-coated surface to UV light through a photomask. The areas exposed to light become polymerized and are subsequently developed to remove the unexposed photoresist, leaving behind the desired circuit pattern.
- Etching:The substrate undergoes chemical etching to remove the exposed copper that is not protected by the developed photoresist. This process defines the conductive traces and pads according to the circuit design.
- Strip and Clean:After etching, the remaining photoresist is stripped away, leaving clean copper traces and pads on the Rogers 4835 substrate. The substrate is then cleaned again to remove any residues from the etching process.
- Surface Finish:Depending on the application requirements, the substrate may undergo surface finishing processes such as solder mask application, hot air leveling (HASL), immersion silver, immersion gold, or other finishes to protect the copper traces and provide solderability.
- Final Inspection and Testing:The fabricated Rogers 4835 substrate undergoes inspection and testing to ensure that it meets the specified design parameters, including dimensional accuracy, electrical performance, and reliability under high-frequency conditions.
- Routing and Final Processing:If required, the substrate may undergo routing, where excess material is removed to create the final shape and dimensions of the PCB. Final processing steps may include edge plating, scoring, or other finishing touches as per the design requirements.
By following these fabrication steps with precision and adherence to design specifications, manufacturers can produce high-quality Rogers 4835 substrates suitable for a wide range of RF and microwave applications. Each step plays a crucial role in maintaining the substrate’s electrical characteristics and mechanical integrity.
The application of ceramic Rogers 4835 Substrate
Rogers 4835 substrate, despite being a ceramic-filled PTFE material, finds wide application in various RF and microwave circuit designs due to its excellent electrical properties and performance characteristics. Here are some common applications where Rogers 4835 substrate is extensively used:
- RF and Microwave Circuits:Rogers 4835 is widely used in the fabrication of RF and microwave circuits such as power amplifiers, low noise amplifiers (LNAs), mixers, filters, couplers, and antennas. Its low loss tangent and stable dielectric constant (Dk) make it suitable for high-frequency applications where signal integrity and minimal signal loss are critical.
- Telecommunications:In telecommunications systems, Rogers 4835 substrates are used in base station antennas, satellite communications equipment, radar systems, and high-speed data transfer devices. Its high-frequency capability and reliability under varying environmental conditions make it ideal for these applications.
- Wireless Communication Systems:Rogers 4835 substrates are employed in wireless communication systems including cellular networks (5G and earlier generations), WiFi routers, Bluetooth devices, and other wireless communication modules. Its ability to support high data rates and wide bandwidths contributes to the efficient transmission of signals.
- Aerospace and Defense:Due to its ruggedness, thermal stability, and reliability in harsh environments, Rogers 4835 substrates are extensively used in aerospace and defense applications. This includes radar systems, avionics, missile guidance systems, and military communication devices where performance under extreme conditions is crucial.
- Automotive Radar Systems:In automotive applications, Rogers 4835 substrates are utilized in radar systems for collision avoidance, adaptive cruise control, and other driver assistance technologies. Its high-frequency performance and ability to withstand temperature variations make it suitable for automotive radar applications.
- Medical Devices:Rogers 4835 substrates find use in medical devices that utilize RF and microwave technologies, such as MRI machines, medical imaging equipment, and wireless medical telemetry systems. Its reliability and low signal loss characteristics support precise and consistent performance in medical applications.
- Test and Measurement Equipment:Test and measurement equipment, including spectrum analyzers, signal generators, and network analyzers, often incorporate Rogers 4835 substrates due to their ability to maintain accurate signal integrity and measurement accuracy at high frequencies.
Overall, Rogers 4835 substrate’s combination of low loss tangent, stable Dk, high-frequency capability, and mechanical durability makes it a preferred choice for critical applications demanding high performance, reliability, and consistency in RF and microwave circuits across various industries.
FAQs about Rogers 4835 Substrate
What is Rogers 4835 substrate?
Rogers 4835 is a high-frequency laminate material composed of woven glass reinforced ceramic-filled PTFE (Polytetrafluoroethylene). It is designed to provide excellent electrical properties for RF and microwave applications.
What are the key characteristics of Rogers 4835 substrate?
Rogers 4835 substrate is known for its low loss tangent (typically around 0.0037 at 10 GHz), stable dielectric constant (Dk) of approximately 3.48 at 10 GHz, high-frequency performance up to 40 GHz, and mechanical durability under varying environmental conditions.
What are the advantages of using Rogers 4835 substrate?
The advantages include low signal loss, stable electrical properties over a wide frequency range, high reliability in harsh environments, and compatibility with standard PCB manufacturing processes.
Where is Rogers 4835 substrate commonly used?
It is commonly used in RF and microwave circuits such as power amplifiers, antennas, filters, and high-speed data communication devices. Applications span industries including telecommunications, aerospace, defense, automotive radar systems, and medical devices.
What are the fabrication considerations for Rogers 4835 substrate?
Fabrication involves processes like lamination with copper foil, photolithography for circuit pattern definition, etching to create conductor traces, surface finishing, and final inspection/testing to ensure quality and performance.
Is Rogers 4835 substrate suitable for high-power applications?
Yes, Rogers 4835 substrate is suitable for high-power RF applications due to its low loss tangent and ability to handle high-frequency signals with minimal power dissipation.
How does Rogers 4835 substrate compare to other high-frequency materials?
Compared to other materials like FR4, Rogers 4350, or ceramic substrates, Rogers 4835 offers superior high-frequency performance and lower loss characteristics, making it ideal for demanding RF and microwave applications.
What are the environmental and reliability characteristics of Rogers 4835 substrate?
Rogers 4835 substrate exhibits good thermal stability, moisture resistance, and mechanical durability, making it suitable for use in environments with varying temperatures and conditions.