Rogers 4500 Substrate Manufacturer
Rogers 4500 Substrate Manufacturer,Rogers 4500 Substrate is a high-frequency laminate known for its excellent RF/microwave performance. Composed of woven glass reinforced hydrocarbon/ceramic material, it provides low dielectric loss and stable electrical properties over a broad frequency range. The substrate’s robust mechanical strength and thermal stability ensure reliability in challenging environments, making it suitable for aerospace, automotive, and wireless communication systems. Rogers 4500 facilitates precise circuit integration and supports miniaturization, enhancing signal integrity and performance in high-speed digital and microwave circuits. Its consistent electrical characteristics and durability make it a preferred choice for applications requiring reliable RF performance and efficient signal transmission.
What is Rogers 4500 Substrate?
Rogers 4500 substrate is a type of high-frequency circuit material used in the electronics industry. It is known for its excellent electrical properties that make it suitable for applications requiring high performance and reliability. The substrate is primarily used in RF (radio frequency) and microwave circuits where low loss and stable dielectric constant are crucial for maintaining signal integrity.
Key characteristics of Rogers 4500 substrate include its low dielectric loss, which ensures minimal signal attenuation, especially at higher frequencies. This property is essential in applications such as telecommunications, radar systems, satellite communications, and medical equipment where maintaining signal strength and quality is critical.
Another important feature of Rogers 4500 is its stable and predictable electrical performance over a wide range of temperatures and frequencies. This stability makes it easier for engineers to design and manufacture high-frequency circuits with consistent performance.
In terms of construction, Rogers 4500 substrate typically consists of woven fiberglass reinforced with PTFE (polytetrafluoroethylene) and a ceramic filler, which contributes to its mechanical strength and thermal stability. This composition also helps in achieving the desired electrical properties required for high-frequency applications.
Overall, Rogers 4500 substrate is valued in the electronics industry for its reliability, low loss characteristics, and stable performance, making it a preferred choice for demanding RF and microwave applications where performance and consistency are paramount.
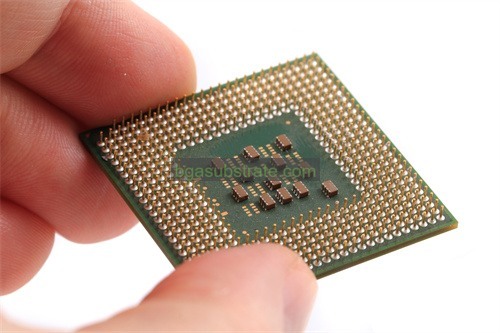
Rogers 4500 Substrate Manufacturer
What is the Rogers 4500 Substrate Design Guidelines?
Rogers 4500 is a high-frequency laminate material known for its excellent electrical and mechanical properties, commonly used in RF/microwave applications. Here are some general design guidelines for Rogers 4500 substrate:
- Dielectric Constant (εr): Rogers 4500 typically has a dielectric constant (εr) ranging from approximately 3.48 to 3.52, depending on the specific grade. It’s important to accurately specify the εr for precise RF/microwave circuit design.
- Loss Tangent (Df): The loss tangent (Df) of Rogers 4500 is low, typically around 0.0027 to 0.0030 at 10 GHz. Low Df ensures minimal signal loss in high-frequency applications.
- Thickness: Available in various thicknesses, typically ranging from 5 mils (0.127 mm) to 125 mils (3.175 mm). The chosen thickness impacts impedance control and mechanical stability.
- Copper Cladding: Rogers 4500 substrates usually come with copper cladding on one or both sides. The thickness and quality of copper cladding affect the substrate’s performance in terms of conductivity and signal integrity.
- Thermal Management: Consider thermal conductivity properties for designs where heat dissipation is critical. Rogers 4500 has moderate thermal conductivity suitable for many RF/microwave applications.
- Manufacturing Tolerances:Pay attention to manufacturing tolerances for thickness, copper thickness, and dimensional stability, as these affect the consistency and performance of circuits.
- Material Handling: Handle Rogers 4500 substrates carefully to avoid damage to the delicate copper surfaces or the laminate material itself, which could affect circuit performance.
These guidelines ensure that designers can leverage Rogers 4500’s properties effectively for high-frequency circuit designs, maintaining signal integrity and performance in RF/microwave applications.
The advantages of Rogers 4500 Substrate
Rogers 4500 substrate offers several advantages that make it popular for RF/microwave applications:
- Low Dielectric Loss: Rogers 4500 has a low loss tangent (typically around 0.003 at 10 GHz), which minimizes signal loss in high-frequency circuits. This property is crucial for maintaining signal integrity and achieving high performance in RF/microwave applications.
- Stable Electrical Properties: It exhibits stable electrical properties over a wide frequency range, making it suitable for applications where consistent performance is required across different frequencies.
- High Frequency Performance: Designed specifically for RF/microwave frequencies, Rogers 4500 substrate materials offer excellent performance characteristics, including low insertion loss and low dispersion.
- Thermal Management: It has moderate thermal conductivity, aiding in heat dissipation in electronic circuits. This property is beneficial for applications where thermal management is critical to maintaining reliability and performance.
- Dimensional Stability: Rogers 4500 substrates are known for their dimensional stability, which helps in achieving precise circuit designs and maintaining tight tolerances during manufacturing processes.
- Process Compatibility: It is compatible with standard PCB manufacturing processes, allowing for ease of fabrication and integration into existing production workflows.
- Reliability: Rogers 4500 materials are known for their reliability and durability, ensuring long-term performance in demanding applications.
- Material Options: Rogers offers different grades and thicknesses of the 4500 series, allowing designers to choose the most suitable material based on specific application requirements such as frequency, power handling, and environmental conditions.
Overall, Rogers 4500 substrate materials are favored in the RF/microwave industry for their combination of low loss, high frequency performance, thermal management capabilities, and reliability, making them ideal for critical applications where signal integrity and performance are paramount.
What is the Rogers 4500 Substrate Fabrication Process?
The fabrication process for Rogers 4500 substrate involves several key steps, typical of high-frequency laminate materials used in RF/microwave applications. Here is a general outline of the fabrication process:
- Preparation of Base Materials:Rogers 4500 substrates typically start with prepreg materials, which consist of a glass-reinforced woven fiberglass cloth impregnated with uncured resin. These prepreg sheets are cut to the required size and thickness based on the design specifications.
- Copper Foil Lamination:The next step involves laminating copper foil onto one or both sides of the prepreg sheets. This is done using heat and pressure in a lamination press, where the prepreg and copper foil are bonded together to form a copper-clad laminate. The thickness and quality of the copper foil are critical to the substrate’s conductivity and performance.
- Drilling and Tooling:Holes for vias and component mounting are drilled into the copper-clad laminate using precision drilling machines. Tooling holes for alignment during subsequent manufacturing steps are also created at this stage.
- Circuit Patterning:A photoresist layer is applied to the copper surface, which is then exposed to UV light through a photomask that contains the desired circuit pattern. This process defines the areas where copper will be etched away to create the circuit traces and pads.
- Etching:The exposed copper areas not protected by the photoresist are etched away using an etchant solution. This process leaves behind the desired circuit pattern on the substrate, with copper traces connecting various components and vias.
- Surface Finish:After etching, a surface finish is applied to the exposed copper traces to improve solderability and protect the copper from oxidation. Common surface finishes for Rogers 4500 substrates include immersion silver, immersion tin, and ENIG (Electroless Nickel Immersion Gold).
- Solder Mask Application:A solder mask layer is applied over the substrate, covering all areas except where solder joints are required. The solder mask protects the copper traces from environmental factors and prevents solder bridges during assembly.
- Silkscreen Printing: Component designators, logos, and other identifiers are printed onto the substrate using a silkscreen printing process. This step provides visual reference and identification for components on the PCB.
- Final Inspection and Testing:The fabricated Rogers 4500 substrates undergo rigorous inspection and testing to ensure they meet quality standards and design specifications. This includes electrical testing, dimensional verification, and visual inspection for any defects.
- Routing and Singulation:Once tested and approved, the substrates are routed or singulated into individual PCBs according to the specific panelization requirements of the design.
- Packaging and Shipping:Finally, the finished Rogers 4500 substrates are packaged securely to protect them during transportation and storage, ready for assembly into electronic products.
Each step in the fabrication process is critical to producing high-quality Rogers 4500 substrates that meet the stringent requirements of RF/microwave applications, ensuring optimal performance and reliability in electronic circuits.
The application of ceramic Rogers 4500 Substrate
Rogers 4500 ceramic substrates are widely used in high-frequency and microwave applications where superior electrical performance and reliability are essential. Here are some common applications of Rogers 4500 ceramic substrates:
- RF/Microwave Circuits:Rogers 4500 substrates are ideal for RF and microwave circuits due to their low loss tangent and stable dielectric properties. They are used in applications such as power amplifiers, filters, couplers, and oscillators where high frequency performance and minimal signal loss are critical.
- Antennas:Ceramic substrates like Rogers 4500 are well-suited for antenna designs in wireless communication systems. They provide excellent dimensional stability, thermal management, and RF performance necessary for antennas operating across various frequency bands.
- Aerospace and Defense:In aerospace and defense applications, Rogers 4500 substrates are chosen for their reliability and performance in radar systems, satellite communications, electronic warfare systems, and other mission-critical electronics where ruggedness and performance under extreme conditions are required.
- Medical Devices:High-frequency ceramic substrates find application in medical devices such as MRI machines, RF ablation systems, and wireless monitoring devices. Rogers 4500 substrates ensure consistent signal integrity and reliability in medical electronics.
- Telecommunications:Telecommunication equipment, including base stations, repeaters, and high-speed data transmission devices, utilize Rogers 4500 substrates for their ability to maintain signal integrity over long distances and under varying environmental conditions.
- Automotive Electronics:In automotive electronics, Rogers 4500 substrates are used in radar systems, collision avoidance systems, and vehicle-to-vehicle communication modules. They provide high reliability and performance in harsh automotive environments.
- Test and Measurement Equipment:Test and measurement instruments, such as spectrum analyzers, network analyzers, and signal generators, benefit from Rogers 4500 substrates’ low loss and high frequency capabilities, ensuring accurate and precise measurement results.
- Industrial Applications:Industrial applications such as industrial automation, robotics, and wireless sensors utilize Rogers 4500 substrates for their ability to support high-frequency signals and withstand rugged industrial environments.
In summary, Rogers 4500 ceramic substrates are chosen for applications requiring high-frequency performance, low loss tangent, thermal stability, and reliability across a wide range of industries including telecommunications, aerospace, medical, automotive, and industrial sectors. Their versatility and performance make them a preferred choice for demanding electronic applications.
FAQs about Rogers 4500 Substrate
What is Rogers 4500 substrate?
Rogers 4500 is a high-frequency ceramic-filled laminate material designed for RF/microwave applications. It offers low dielectric loss, stable electrical properties, and thermal management capabilities.
What are the key advantages of Rogers 4500 substrate?
Rogers 4500 substrates provide low loss tangent, high frequency performance, thermal stability, reliability, and compatibility with standard PCB manufacturing processes.
What are the typical applications of Rogers 4500 substrate?
Rogers 4500 substrates are used in RF/microwave circuits, antennas, aerospace and defense electronics, medical devices, telecommunications equipment, automotive electronics, and industrial applications.
What are the different grades or versions of Rogers 4500 substrate available?
Rogers offers various grades of the 4500 series with different dielectric constants, thicknesses, and thermal conductivity options to suit specific application requirements.
How does Rogers 4500 substrate compare to other materials like FR4 for high-frequency applications?
Compared to FR4 (a standard PCB material), Rogers 4500 substrate offers significantly lower dielectric loss and better performance at high frequencies, making it ideal for RF and microwave applications where signal integrity is crucial.
What surface finishes are compatible with Rogers 4500 substrate?
Surface finishes such as immersion silver, immersion tin, and ENIG (Electroless Nickel Immersion Gold) are commonly used with Rogers 4500 substrates to ensure good solderability and corrosion resistance.
What are the design considerations when using Rogers 4500 substrate?
Designers should consider factors like controlled impedance requirements, thermal management, dimensional stability, and compatibility with manufacturing processes during the design phase.