Rogers 4400 Substrate Manufacturer
Rogers 4400 Substrate Manufacturer,Rogers 4400 Substrate is a high-frequency laminate renowned for its exceptional electrical performance in RF/microwave applications. Composed of woven glass reinforced hydrocarbon/ceramic material, it offers low dielectric loss and stable electrical properties across a broad frequency range. The substrate’s robust mechanical strength and thermal stability ensure reliability in demanding environments, making it suitable for aerospace, automotive, and wireless communication systems. Rogers 4400 facilitates precise circuit integration and supports miniaturization, enhancing signal integrity and performance in high-speed digital and microwave circuits. Its consistent electrical characteristics and durability make it a preferred choice for applications requiring high reliability and superior RF performance.
What is Rogers 4400 Substrate?
Rogers 4400 is a type of high-frequency laminate substrate used primarily in RF (radio frequency) and microwave applications. It belongs to the RO4000® series of laminates manufactured by Rogers Corporation, a leading producer of advanced materials for electronics.
The Rogers 4400 substrate is known for its excellent electrical properties that make it suitable for high-frequency circuits. These properties include low dielectric constant (εr) and low dissipation factor (tan δ), which help in minimizing signal loss and ensuring high signal integrity in microwave circuits. The material also exhibits stable electrical performance over a wide range of temperatures and frequencies, which is crucial for applications where reliability is paramount.
In addition to its electrical characteristics, Rogers 4400 substrate offers good mechanical stability and ease of processing during fabrication. This makes it a preferred choice for various applications such as antennas, radar systems, satellite communications, and other wireless devices where high-performance RF circuitry is required.
Designers and engineers often choose Rogers 4400 substrate for its consistent performance and reliability in demanding environments. It enables the development of compact, efficient, and high-frequency electronic systems by providing a stable foundation for circuit components like microstrip lines, stripline circuits, and other RF structures.
Overall, Rogers 4400 substrate stands out in the field of RF and microwave engineering due to its combination of electrical properties, mechanical stability, and ease of use in manufacturing processes, making it a key material for advancing technology in telecommunications and beyond.
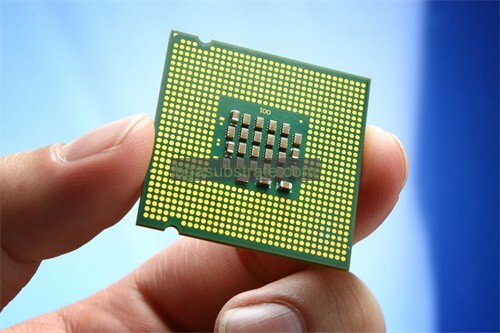
Rogers 4400 Substrate Manufacturer
What is the Rogers 4400 Substrate Design Guidelines?
Design guidelines for Rogers 4400 substrate typically focus on optimizing performance and ensuring reliability in RF (radio frequency) and microwave circuits. Here are some general design guidelines that engineers and designers often follow when working with Rogers 4400 substrate:
- Material Properties:Understand the electrical properties of Rogers 4400, such as its dielectric constant (εr), loss tangent (tan δ), and thermal conductivity. These properties affect the impedance, signal integrity, and heat dissipation characteristics of the circuits.
- Impedance Control:Rogers 4400 substrate is used in applications where maintaining precise impedance is critical for signal integrity. Design transmission lines (such as microstrip or stripline) with appropriate widths and spacings to achieve the desired impedance matching.
- Stack-up Design:Consider the layer stack-up of the PCB (Printed Circuit Board) when using Rogers 4400 substrate. Ensure proper layer ordering and thicknesses to achieve optimal RF performance and mechanical stability.
- Copper Thickness:Select an appropriate copper thickness for the PCB layers to minimize losses and improve conductivity. Typically, thicker copper layers are preferred for high-frequency applications to reduce conductor losses.
- Component Placement:Place RF components carefully to minimize parasitic effects and ensure consistent signal paths. Pay attention to spacing and orientation to maintain signal integrity and reduce electromagnetic interference (EMI).
- Grounding:Implement effective grounding techniques to reduce noise and improve overall circuit performance. Utilize solid ground planes and via stitching to enhance RF shielding and minimize ground loops.
- Thermal Management:Consider thermal management strategies, especially in high-power applications, to dissipate heat effectively. Rogers 4400 has good thermal conductivity, but proper design practices such as thermal vias and heat sinks may be necessary.
- Manufacturing Considerations:Communicate design specifications clearly with PCB manufacturers to ensure proper fabrication techniques are used. Rogers 4400 substrate requires specialized handling during manufacturing due to its unique properties.
- Testing and Validation:Conduct thorough testing and validation of the RF circuits using Rogers 4400 substrate. Verify impedance matching, signal integrity, and other performance metrics under operational conditions.
Following these guidelines helps in harnessing the full potential of Rogers 4400 substrate for designing high-frequency circuits with excellent electrical performance and reliability. Engineers often leverage simulation tools and extensive experience in RF design to optimize designs and achieve desired outcomes in terms of performance and manufacturability.
The advantages of Rogers 4400 Substrate
Rogers 4400 substrate offers several advantages that make it highly suitable for RF (radio frequency) and microwave applications:
- Low Dielectric Loss:Rogers 4400 substrate exhibits a low dissipation factor (loss tangent), which means it minimizes signal loss and maintains signal integrity at high frequencies. This property is crucial for applications requiring efficient transmission of RF signals without significant attenuation.
- Stable Electrical Performance: The material provides stable electrical properties over a wide range of frequencies and temperatures. This stability ensures consistent RF performance, making it reliable for critical communication systems and radar applications.
- High Frequency Capability:Designed for high-frequency applications, Rogers 4400 substrate supports the development of circuits operating at frequencies well into the microwave range (typically up to tens of GHz). Its low loss characteristics enable the efficient transmission of high-frequency signals with minimal distortion.
- Mechanical Stability:Rogers 4400 substrate offers good mechanical stability and dimensional control during fabrication. This stability contributes to the reliability and longevity of RF circuits, reducing the risk of performance degradation due to environmental factors or mechanical stress.
- Ease of Fabrication:The material is engineered for ease of processing, allowing for precise fabrication of complex RF circuit designs. This includes machining, drilling, and etching processes typically used in PCB manufacturing.
- Thermal Management:Rogers 4400 substrate has reasonable thermal conductivity, which helps in dissipating heat generated by active components in RF circuits. Effective thermal management contributes to enhanced reliability and performance consistency under varying operational conditions.
- Compatibility with High-Frequency Components:It is compatible with a wide range of high-frequency components such as microstrip lines, stripline circuits, antennas, and other RF structures. This compatibility facilitates the design and integration of advanced RF systems.
- Industry Standard:Rogers Corporation, the manufacturer of Rogers 4400 substrate, is known for its quality and reliability in providing advanced materials for RF and microwave applications. Engineers and designers often choose Rogers materials due to their established performance and support infrastructure.
Overall, Rogers 4400 substrate’s combination of low loss, stable electrical performance, mechanical robustness, and ease of fabrication makes it a preferred choice for demanding RF and microwave applications where high performance and reliability are paramount.
What is the Rogers 4400 Substrate Fabrication Process?
The fabrication process for Rogers 4400 substrate involves several steps to ensure the material’s properties are utilized effectively in RF (radio frequency) and microwave circuit applications:
- Material Selection:Begin by selecting Rogers 4400 substrate sheets of appropriate thickness and dimensions based on the specific design requirements. Rogers 4400 is available in various thicknesses to suit different applications.
- Preparation:Clean the substrate sheets thoroughly to remove any contaminants that could affect the adhesion and performance of subsequent layers or conductive elements.
- Copper Cladding:Apply copper cladding to the Rogers 4400 substrate. This involves laminating or bonding a thin layer of copper to one or both sides of the substrate sheet. The copper layer provides the conductive pathways necessary for RF circuitry.
- Etching: Use a photolithographic process to define the circuit patterns on the copper-clad Rogers 4400 substrate. This involves applying a photoresist material over the copper layer, exposing it to UV light through a mask with the desired circuit pattern, and then developing the exposed resist to reveal the copper areas to be etched away.
- Etching Process:Etch away the exposed copper using an etchant solution that selectively removes the copper, leaving behind the desired circuit traces and patterns. This step defines the conductive paths (e.g., microstrip lines, pads, vias) on the Rogers 4400 substrate according to the design specifications.
- Drilling:Drill holes (vias) where necessary to establish electrical connections between different layers of the PCB or to mount components. These vias are typically plated with copper to ensure electrical continuity and mechanical stability.
- Surface Finish:Apply a surface finish to the PCB to protect the copper traces from oxidation and ensure reliable soldering of components. Common surface finishes include HASL (Hot Air Solder Leveling), ENIG (Electroless Nickel Immersion Gold), or OSP (Organic Solderability Preservatives).
- Inspection and Testing:Conduct rigorous inspection and testing of the fabricated PCB to ensure that the circuit patterns, dimensions, and electrical characteristics meet the design specifications. This includes electrical testing to verify continuity, impedance matching, and signal integrity.
- Assembly:If necessary, assemble the Rogers 4400 substrate PCB with components such as resistors, capacitors, and integrated circuits. Use appropriate soldering techniques to mount and secure components onto the PCB surface.
- Final Inspection:Perform final inspection and quality assurance checks to validate the functionality, reliability, and performance of the assembled RF or microwave circuit board fabricated using Rogers 4400 substrate.
By following these fabrication steps with precision and care, engineers and manufacturers can leverage the unique properties of Rogers 4400 substrate to produce high-quality PCBs suitable for a wide range of demanding RF and microwave applications.
The application of ceramic Rogers 4400 Substrate
Rogers 4400 substrate, although primarily known for its use in RF (radio frequency) and microwave applications, particularly in PCB (Printed Circuit Board) manufacturing, has specific advantages and applications within these fields:
- Antennas:Rogers 4400 substrate is frequently utilized in the construction of antennas due to its excellent RF performance characteristics. Its low dielectric constant and low loss tangent ensure efficient signal transmission and reception, making it ideal for both transmitting and receiving antennas across various frequency bands.
- High-Frequency Circuits: Given its low loss tangent and stable dielectric properties, Rogers 4400 is extensively employed in the fabrication of high-frequency circuits. These circuits are crucial in telecommunications, radar systems, satellite communications, and other wireless applications where signal integrity and minimal attenuation are paramount.
- Power Amplifiers:The substrate’s ability to handle high frequencies and its thermal management properties make it suitable for power amplifiers. It can efficiently dissipate heat generated by active components, ensuring reliable operation at high power levels.
- RF Filters:Rogers 4400 substrate is used in the construction of RF filters due to its precise dielectric constant, which allows for accurate impedance control and minimal insertion loss. RF filters are essential in separating or combining different frequency signals in communication systems.
- Microwave PCBs:For microwave PCBs operating at frequencies up to and beyond tens of gigahertz, Rogers 4400 substrate provides the necessary electrical and mechanical properties. It enables the design of compact and high-performance circuits used in radar systems, aerospace applications, and advanced wireless technologies.
- Automotive Radar Systems:In automotive radar systems, which operate in the millimeter-wave frequency range, Rogers 4400 substrate is utilized for its ability to maintain signal integrity at high frequencies. It supports the development of collision avoidance systems, adaptive cruise control, and other radar-based safety features.
- Satellite Communications:Rogers 4400 substrate is employed in satellite communications equipment due to its reliability in extreme environmental conditions and its ability to maintain consistent electrical performance over a wide range of temperatures. It supports the transmission and reception of signals in satellite communication networks.
In summary, Rogers 4400 substrate finds application in various critical areas of RF and microwave engineering where high performance, reliability, and stability are essential. Its use in antennas, high-frequency circuits, power amplifiers, RF filters, microwave PCBs, automotive radar systems, and satellite communications highlights its versatility and importance in advancing modern telecommunications and electronic systems.
FAQs about Rogers 4400 Substrate
What is Rogers 4400 substrate used for?
Rogers 4400 substrate is primarily used in RF (radio frequency) and microwave applications. It is employed in the construction of high-frequency circuits, antennas, power amplifiers, RF filters, microwave PCBs, and satellite communications equipment.
What are the key properties of Rogers 4400 substrate?
Rogers 4400 substrate is known for its low dielectric constant (εr), low dissipation factor (loss tangent), stable electrical performance over a wide frequency range, good mechanical stability, and thermal management capabilities.
Why choose Rogers 4400 substrate over other materials?
Engineers often choose Rogers 4400 substrate for its superior RF performance, including low loss tangent for minimal signal attenuation, excellent impedance control, and reliability in high-frequency applications. It is also recognized for its ease of fabrication and compatibility with standard PCB manufacturing processes.
What frequency ranges can Rogers 4400 substrate support?
Rogers 4400 substrate is suitable for applications ranging from RF frequencies up to microwave frequencies, typically into the tens of gigahertz. It is designed to maintain consistent performance across these frequencies, making it ideal for modern wireless communication systems.
Is Rogers 4400 substrate suitable for high-power applications?
Yes, Rogers 4400 substrate is capable of handling high-power applications due to its good thermal conductivity and mechanical stability. It can efficiently dissipate heat generated by active components, ensuring reliable operation even at higher power levels.
How does Rogers 4400 substrate compare to other Rogers materials?
Rogers 4400 substrate is part of the RO4000® series of laminates from Rogers Corporation. Compared to other materials in the series, it offers specific electrical and mechanical properties optimized for high-frequency applications, striking a balance between performance, cost-effectiveness, and ease of manufacturing.
Where can I buy Rogers 4400 substrate?
Rogers 4400 substrate and other Rogers Corporation materials are available through authorized distributors and directly from Rogers Corporation. Manufacturers and engineers typically source these materials based on specific project requirements and quantities needed.