Rogers 4003C Substrate Manufacturer
Rogers 4003C Substrate Manufacturer,Rogers 4003C Substrate is a high-performance circuit material known for its reliability and versatility in RF/microwave applications. Composed of woven fiberglass reinforced with PTFE (Polytetrafluoroethylene), it offers low dielectric loss and stable electrical properties across a broad frequency range. The substrate’s consistent mechanical strength and thermal stability make it ideal for high-frequency circuit designs requiring precision and reliability. Rogers 4003C facilitates efficient signal transmission and supports the miniaturization of electronic devices due to its uniform thickness and controlled dielectric constant. It is widely used in wireless communication systems, radar applications, and aerospace electronics where high-performance RF characteristics are essential.
What is Rogers 4003C Substrate?
Rogers 4003C is a type of high-frequency circuit board substrate known for its excellent electrical performance and reliability. It belongs to the RO4000 series of laminates manufactured by Rogers Corporation, specifically designed for applications requiring high-frequency performance, low dielectric loss, and stable electrical properties over a wide range of temperatures.
The “C” designation in Rogers 4003C signifies its enhanced copper foil adhesion, which is crucial for maintaining signal integrity in high-frequency circuits. This substrate is commonly used in RF (radio frequency) and microwave circuits, antennas, power amplifiers, and other wireless communication systems where low loss and predictable electrical characteristics are essential.
Engineered with a PTFE (polytetrafluoroethylene) composite and ceramic filler material, Rogers 4003C offers a low dissipation factor (Df) and a low relative permittivity (εr), which are critical for minimizing signal loss and maintaining signal integrity at high frequencies. Its consistent dielectric constant and tight thickness control make it suitable for applications demanding high reliability and performance under stringent environmental conditions.
Overall, Rogers 4003C substrate is favored in the electronics industry for its combination of electrical properties, thermal stability, and manufacturability, making it a reliable choice for high-frequency circuit design and fabrication.
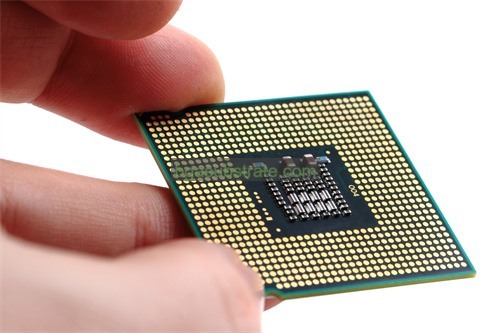
Rogers 4003C Substrate Manufacturer
What is the Rogers 4003C Substrate Design Guidelines?
Design guidelines for Rogers 4003C substrate primarily focus on ensuring optimal performance and reliability in high-frequency circuit applications. Here are some key considerations:
- Dielectric Constant (εr): Rogers 4003C has a stable dielectric constant of approximately 3.38 over a wide frequency range. Designers should account for this value in calculating characteristic impedance and ensuring signal integrity.
- Loss Tangent (Df): The substrate offers a low loss tangent (typically around 0.0027), which is crucial for minimizing signal attenuation. Designers should consider this parameter to maintain signal integrity, especially in high-frequency applications.
- Copper Foil Adhesion:Rogers 4003C is known for its strong copper foil adhesion (designated by the “C” in 4003C), ensuring reliable performance in circuits where copper conductivity and adhesion are critical.
- Thermal Stability: The substrate exhibits good thermal stability, which is important for applications exposed to varying temperatures. Designers should consider thermal expansion coefficients and how they might affect circuit performance.
- Manufacturability: Rogers 4003C is designed for ease of manufacturing, including processes like etching, drilling, and soldering. Design guidelines often provide recommendations for optimal manufacturing techniques to achieve desired electrical performance.
- Dimensional Stability:Maintaining dimensional stability is crucial to ensure consistent electrical properties across different batches of substrates. Designers should adhere to recommended thicknesses and tolerances specified by Rogers Corporation.
- Environmental Considerations: Ensure the substrate’s performance meets environmental requirements such as humidity, temperature extremes, and chemical exposure, depending on the application’s operating conditions.
- Stack-up Design: Proper stack-up design is essential for achieving desired impedance matching and signal integrity. Design guidelines typically include recommended layer thicknesses, copper weights, and dielectric thicknesses for various circuit configurations.
- Electromagnetic Interference (EMI) Considerations: Rogers 4003C substrate is designed to minimize electromagnetic interference and crosstalk between adjacent circuit elements. Design guidelines may include recommendations for ground plane placement and shielding techniques.
- Documentation and Compliance: Ensure compliance with industry standards and regulations relevant to the application, including IPC standards for PCB design and manufacturing.
By following these design guidelines, engineers can leverage the electrical and mechanical properties of Rogers 4003C substrate to achieve high-performance, reliable circuits for RF and microwave applications.
The advantages of Rogers 4003C Substrate
Rogers 4003C substrate offers several advantages that make it a preferred choice for high-frequency circuit applications:
- Low Dielectric Loss: Rogers 4003C has a low dissipation factor (Df) of approximately 0.0027, which minimizes signal loss and ensures excellent signal integrity. This property is crucial in high-frequency circuits where even small losses can degrade performance.
- Stable Electrical Properties: The substrate maintains stable electrical characteristics over a wide range of frequencies and temperatures. This stability in dielectric constant (εr around 3.38) and loss tangent (Df) ensures predictable performance in various environmental conditions.
- High Thermal Conductivity: It exhibits good thermal conductivity, allowing for efficient heat dissipation. This property helps in managing thermal issues in electronic devices, particularly in power amplifiers and other components where heat generation is significant.
- Strong Copper Adhesion: Rogers 4003C is designed with enhanced copper foil adhesion (denoted by “C” in the name), ensuring robust connectivity and reliability in circuits. This feature is essential for maintaining electrical performance over time and under varying environmental conditions.
- Ease of Fabrication: The substrate is engineered for ease of fabrication processes such as drilling, etching, and soldering. This facilitates efficient manufacturing of complex high-frequency circuits, reducing production costs and time.
- Dimensional Stability:It offers excellent dimensional stability, which is critical for maintaining consistent electrical properties across different batches of substrates. This stability contributes to reliable performance and ease of design implementation.
- Wide Application Range: Rogers 4003C is suitable for a broad range of applications including RF and microwave circuits, antennas, power amplifiers, and high-speed digital circuits. Its versatility and performance make it a preferred choice in telecommunications, aerospace, automotive radar systems, and other advanced electronics industries.
- Environmental Durability: The substrate is designed to withstand harsh environmental conditions, including humidity, temperature fluctuations, and exposure to chemicals. This durability enhances the reliability and longevity of electronic devices utilizing Rogers 4003C substrate.
Overall, Rogers 4003C substrate combines low loss, stable electrical properties, strong copper adhesion, and ease of manufacturing, making it an ideal choice for demanding high-frequency applications where performance and reliability are paramount.
What is the Rogers 4003C Substrate Fabrication Process?
The fabrication process for Rogers 4003C substrate involves several key steps to ensure optimal electrical performance and reliability:
- Material Selection: Rogers 4003C is a high-frequency laminate composed of a PTFE (polytetrafluoroethylene) composite with ceramic fillers. The choice of this material ensures low dielectric loss (low Df) and stable electrical properties across a wide range of frequencies.
- Preparation: The substrate material is prepared by cutting it to the desired panel sizes. This step ensures uniformity and facilitates the subsequent manufacturing processes.
- Cleaning and Surface Preparation: Surface cleaning is critical to remove any contaminants that could affect adhesion and performance. The substrate surfaces are typically cleaned using appropriate solvents and methods to ensure a clean and smooth surface.
- Copper Cladding: Copper foils are laminated onto the substrate surfaces using heat and pressure. The substrate’s strong copper foil adhesion (enhanced by the “C” designation in 4003C) ensures reliable electrical connectivity and conductivity.
- Circuit Patterning (Etching): A photoresist layer is applied to the copper-clad substrate, followed by exposure to UV light through a photomask containing the circuit pattern. After exposure, the substrate undergoes development to remove the unexposed photoresist, leaving behind the patterned photoresist mask.
- Etching: The exposed copper not protected by the photoresist is etched away using an appropriate etchant solution. This process defines the circuit traces and features on the substrate according to the desired design specifications.
- Surface Finish: After etching, the remaining photoresist is typically stripped off, and the substrate may undergo surface finishing processes such as chemical treatment or application of surface coatings to enhance solderability and protect against oxidation.
- Drilling: Holes are drilled into the substrate at specified locations for component mounting and interconnection. Precision drilling is essential to ensure alignment and accuracy in complex circuit designs.
- Inspection and Testing: Throughout the fabrication process, rigorous inspection and testing are conducted to verify dimensional accuracy, electrical continuity, and adherence to design specifications. Various techniques such as automated optical inspection (AOI) and electrical testing may be employed.
- Final Processing: Once fabrication and testing are complete, the substrates are typically routed into individual boards or panels, depending on the manufacturing requirements. Final processing steps may include edge trimming, surface cleaning, and packaging for shipment.
By following these fabrication steps, manufacturers ensure that Rogers 4003C substrates meet the stringent requirements of high-frequency circuit applications, providing reliable performance and consistent electrical properties essential for advanced electronic systems.
The application of ceramic Rogers 4003C Substrate
Rogers 4003C substrate, despite being primarily composed of PTFE (polytetrafluoroethylene) with ceramic fillers rather than being a full ceramic material itself, finds extensive application in various high-frequency and RF (radio frequency) circuit designs. Here are some common applications:
- RF and Microwave Circuits: Rogers 4003C is widely used in RF and microwave circuits due to its low dielectric loss (Df around 0.0027) and stable electrical properties over a wide frequency range. It is suitable for applications such as amplifiers, filters, couplers, and antennas in wireless communication systems.
- Wireless Communication Systems: The substrate’s excellent RF performance makes it ideal for base station antennas, satellite communication systems, radar systems, and other wireless infrastructure components. Its low loss tangent helps minimize signal attenuation, ensuring efficient signal transmission and reception.
- High-Speed Digital Circuits: In addition to RF applications, Rogers 4003C is employed in high-speed digital circuits where controlled impedance and signal integrity are crucial. It supports the design of high-performance computing equipment, signal processing units, and data communication devices.
- Automotive Radar Systems: Due to its thermal stability and reliability under harsh environmental conditions, Rogers 4003C is used in automotive radar systems. It helps in achieving precise detection and ranging capabilities essential for advanced driver assistance systems (ADAS) and autonomous driving technologies.
- Aerospace and Defense Electronics: The substrate’s robust performance in extreme temperatures and demanding environments makes it suitable for aerospace and defense applications. It is used in radar systems, electronic warfare (EW) equipment, satellite communication systems, and avionics.
- Medical Electronics: Rogers 4003C finds application in medical devices and equipment where reliable and precise electronic performance is critical. It supports the design of medical imaging systems, diagnostic equipment, and implantable devices that require low noise and high reliability.
- Test and Measurement Equipment: Its predictable electrical characteristics and consistent performance across different batches make Rogers 4003C suitable for test and measurement instruments. It helps maintain accuracy and reliability in equipment used for signal analysis, spectrum monitoring, and wireless testing.
Overall, Rogers 4003C substrate is valued for its combination of low loss, stable electrical properties, thermal stability, and reliability, making it a preferred choice in industries requiring high-frequency performance and stringent quality standards. Its versatility across various applications underscores its importance in advancing modern electronic technologies.
FAQs about Rogers 4003C Substrate
What is Rogers 4003C substrate?
Rogers 4003C is a high-frequency circuit board substrate known for its low dielectric loss, stable electrical properties, and strong copper adhesion. It is part of the RO4000 series of laminates manufactured by Rogers Corporation.
What are the key properties of Rogers 4003C substrate?
Rogers 4003C substrate has a low dissipation factor (Df) of approximately 0.0027, a stable dielectric constant (εr) around 3.38, and excellent thermal conductivity. It also features enhanced copper foil adhesion (“C” designation), ensuring reliable connectivity.
What applications is Rogers 4003C substrate used for?
It is used in a wide range of applications including RF and microwave circuits, antennas, power amplifiers, and high-speed digital circuits. Industries such as telecommunications, aerospace, automotive radar systems, and consumer electronics benefit from its performance characteristics.
How does Rogers 4003C substrate compare to other materials?
Compared to other substrates, Rogers 4003C offers superior electrical performance at high frequencies, lower loss tangent, and better thermal management capabilities. It is often chosen for its reliability and consistency in demanding electronic applications.
What are the design guidelines for Rogers 4003C substrate?
Design guidelines include considerations for dielectric constant, loss tangent, copper adhesion, thermal stability, manufacturability, and dimensional stability. These guidelines ensure optimal performance and reliability in circuit design.
How is Rogers 4003C substrate fabricated?
The fabrication process typically involves material preparation, laminate bonding, copper foil lamination, circuit pattern imaging (etching), drilling, surface finish application, and final inspection. This process ensures the substrate meets stringent quality and performance standards.
Where can I purchase Rogers 4003C substrate?
Rogers 4003C substrate can be purchased from authorized distributors and directly from Rogers Corporation. It is available in various thicknesses and configurations to meet specific application requirements.
What are the environmental considerations for Rogers 4003C substrate?
The substrate is designed to withstand environmental factors such as temperature variations, humidity, and exposure to chemicals typically encountered in electronic applications. It maintains its electrical properties and reliability under challenging conditions.