What is Rigid-Flex PCB?
Rigid-Flex PCB Manufacturer,Rigid-Flex PCBs combine the best of both rigid and flexible circuitry into a single, versatile solution. By integrating rigid and flexible substrates, they offer space-saving designs, enhanced reliability, and improved durability. These specialized PCBs find applications in diverse fields such as consumer electronics, medical devices, aerospace, and automotive industries, where compactness, lightweight construction, and robust performance are crucial. Rigid-Flex PCBs streamline assembly processes, reduce interconnects, and withstand harsh environments, making them indispensable for modern electronic devices requiring intricate designs and reliable functionality.
A Rigid-Flex PCB (Rigid-Flexible Printed Circuit Board) is a type of PCB design that combines rigid circuit boards and flexible circuit boards. The primary feature of this design is the lamination of rigid and flexible circuit boards together, providing the stability and strength of a rigid circuit board along with the bendability and lightness of a flexible circuit board.
This hybrid structure PCB is widely used in electronic devices requiring complex designs and high-density connections, such as smartphones, wearable devices, medical instruments, and aerospace equipment. In these applications, Rigid-Flex PCBs can reduce the number of connectors and solder joints, offering more reliable connections and enhancing the performance and reliability of the devices.
The design of Rigid-Flex PCBs typically includes multiple flexible layers and rigid layers, which are electrically connected through vias and pads. The flexible parts can be bent, folded, or shaped within the device to accommodate various complex spatial layout requirements, while the rigid parts provide mechanical support and fixed points.
Compared to traditional purely rigid or flexible circuit boards, Rigid-Flex PCBs have several advantages:
- High space utilization: They can achieve more complex circuit designs within limited space.
- Lightweight: Reducing the use of connectors and other hardware lowers the overall weight.
- High reliability: Fewer mechanical connection points reduce the risk of failure.
- Design flexibility: They can adapt to various three-dimensional installation requirements, offering greater design freedom.
However, the manufacturing cost of Rigid-Flex PCBs is relatively high, and the design and production process is more complex, requiring precise technology and equipment. Therefore, they are typically used in high-end or demanding application fields.
In summary, by combining the advantages of rigid and flexible circuit boards, Rigid-Flex PCBs provide high-performance, high-reliability solutions suitable for modern electronic products that demand high space efficiency, lightweight, and reliability.
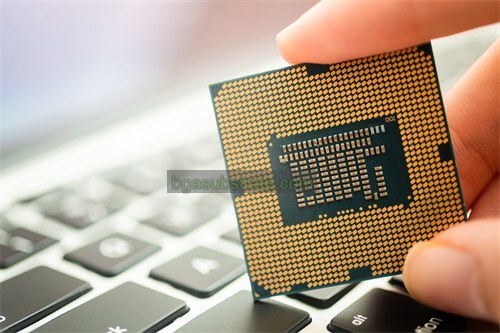
Rigid-Flex PCB Manufacturer
What is the Rigid-Flex PCB Design Guidelines?
Rigid-Flex PCB design guidelines outline best practices and considerations for designing Rigid-Flex PCBs to ensure optimal performance, reliability, and manufacturability. These guidelines typically cover various aspects of the design process, including layout, materials selection, routing, and fabrication. Here are some key points often included in Rigid-Flex PCB design guidelines:
- Layer Stackup: Define the layer stackup, including the number of rigid and flexible layers, material types, and thicknesses. Consider the mechanical and electrical requirements of the application.
- Flex Area Definition: Clearly define the flexible areas of the PCB where bending or flexing will occur. Ensure that these areas have adequate clearance from components, vias, and other features to prevent mechanical stress or damage.
- Bend Radius: Specify minimum bend radius requirements to avoid over-bending or damaging the flexible circuitry. Consider the flexibility of the chosen materials and their ability to withstand repeated bending cycles.
- Component Placement: Optimize component placement to accommodate both rigid and flexible sections of the PCB. Ensure that components are positioned to minimize stress on flexible areas during bending.
- Routing Guidelines: Follow routing guidelines to minimize signal interference, crosstalk, and impedance mismatch. Use proper trace widths, spacing, and layer transitions for both rigid and flexible sections.
- Via Design: Design vias carefully to maintain electrical continuity between rigid and flexible layers while accommodating bending and flexing. Consider the use of staggered vias or blind vias to reduce mechanical stress on flexible areas.
- Mechanical Support: Incorporate mechanical support features such as stiffeners, reinforcement ribs, or coverlays in areas where additional rigidity is required to support components or connectors.
- Connector Placement: Position connectors and interface points strategically to facilitate assembly and ensure reliable electrical connections between rigid and flexible sections.
- Thermal Management: Consider thermal management techniques to dissipate heat evenly across the PCB, especially in areas with components or traces that generate significant heat.
- Manufacturability: Design with manufacturability in mind, considering the capabilities and limitations of PCB fabrication and assembly processes. Communicate design intent clearly to PCB manufacturers to ensure accurate production.
By following these guidelines, designers can create Rigid-Flex PCBs that meet the mechanical, electrical, and reliability requirements of their specific applications while optimizing manufacturability and cost-effectiveness.
The advantages of Rigid-Flex PCB
Rigid-Flex PCBs offer several advantages over traditional rigid or flexible PCBs:
- Space Efficiency: Rigid-Flex PCBs can accommodate complex designs within a smaller footprint compared to using separate rigid and flexible boards. This space efficiency is particularly valuable in compact electronic devices where space is at a premium.
- Weight Reduction: By eliminating connectors and reducing the need for additional wiring, Rigid-Flex PCBs contribute to overall weight reduction in electronic assemblies. This is particularly advantageous in applications where weight savings are critical, such as aerospace or automotive electronics.
- Improved Reliability: Rigid-Flex PCBs have fewer interconnect points, reducing the risk of connection failures and improving overall reliability. The integrated design also minimizes the potential for signal interference and electromagnetic interference (EMI), enhancing signal integrity and system performance.
- Enhanced Durability: The combination of rigid and flexible substrates in Rigid-Flex PCBs enables them to withstand mechanical stress, vibration, and thermal cycling better than traditional PCBs. This makes them well-suited for applications subject to harsh operating conditions or frequent movement, such as wearable devices or military equipment.
- Simplified Assembly: Rigid-Flex PCBs can streamline the assembly process by reducing the number of individual components and interconnects required. This simplification not only saves assembly time but also reduces the risk of assembly errors and improves overall manufacturing yield.
- Design Flexibility: Rigid-Flex PCBs offer greater design flexibility compared to traditional PCBs, allowing for more creative and innovative product designs. Designers can incorporate three-dimensional shapes, bendable features, and customized form factors to meet specific application requirements.
- Cost Savings: While the initial manufacturing cost of Rigid-Flex PCBs may be higher than traditional PCBs, they can often lead to overall cost savings in the long run. This is due to factors such as reduced assembly time, lower component count, and decreased maintenance and repair costs resulting from improved reliability.
Overall, the advantages of Rigid-Flex PCBs make them a preferred choice for a wide range of applications, including consumer electronics, medical devices, automotive systems, and industrial equipment, where performance, reliability, and space optimization are paramount.
What is the Rigid-Flex PCB Fabrication Process?
The fabrication process for Rigid-Flex PCBs involves several steps, combining elements of both rigid and flexible PCB manufacturing processes. Here’s an overview of the typical fabrication process:
- Design: The process begins with the design of the Rigid-Flex PCB using specialized PCB design software. Designers define the layer stackup, component placement, routing, and flex areas according to the specific requirements of the application.
- Material Selection: Select appropriate materials for both the rigid and flexible portions of the PCB. Common materials include rigid substrates like FR-4 (fiberglass-reinforced epoxy laminate) and flexible substrates like polyimide (PI) or polyester (PET).
- Preparation of Rigid and Flex Materials: Prepare the rigid and flex materials separately according to the design specifications. This may involve cutting the rigid substrates to size and laminating the flexible materials with copper foil.
- Layer Alignment and Lamination: Align the rigid and flexible layers precisely according to the design layout. The layers are then bonded together using heat and pressure in a lamination press. This process creates a single, unified Rigid-Flex PCB structure.
- Drilling and Via Formation: Drill holes or vias through the entire stackup to establish electrical connections between layers. Vias may be through-hole vias, blind vias, or buried vias, depending on the design requirements.
- Copper Plating and Etching: Plate the walls of the drilled holes with copper to establish electrical conductivity. Then, apply a layer of copper to the surface of the PCB using a process called electroplating. Next, use photolithography and etching techniques to remove excess copper and define the circuit traces.
- Surface Finish: Apply a surface finish to protect the copper traces and pads from oxidation and ensure solderability. Common surface finishes include HASL (hot air solder leveling), ENIG (electroless nickel immersion gold), and OSP (organic solderability preservatives).
- Solder Mask Application: Apply solder mask ink over the entire PCB surface, leaving openings for solder pads and vias. The solder mask protects the copper traces from oxidation and provides insulation between conductive elements.
- Component Assembly: Mount components onto the Rigid-Flex PCB using surface mount technology (SMT) or through-hole technology (THT), depending on the design requirements. Automated pick-and-place machines and reflow soldering ovens are typically used for component assembly.
- Testing and Inspection: Conduct electrical testing and visual inspection to ensure the integrity and functionality of the Rigid-Flex PCB. This may include continuity testing, impedance testing, and automated optical inspection (AOI) to detect any defects or anomalies.
- Final Processing: Trim the edges of the Rigid-Flex PCB and perform any final processing steps as needed, such as adding stiffeners or coverlays for mechanical support or protection.
- Quality Control and Packaging: Perform final quality control checks to verify compliance with specifications and standards. Once approved, package the Rigid-Flex PCBs for shipment to the customer or assembly into the final product.
Throughout the fabrication process, close attention to detail, precision, and quality control is essential to ensure the reliability and performance of the Rigid-Flex PCBs. Collaboration between design engineers, fabricators, and assemblers is crucial to address any design or manufacturing challenges and achieve optimal results.
The application of ceramic Rigid-Flex PCB
Ceramic Rigid-Flex PCBs, also known as ceramic hybrid PCBs, offer unique advantages for certain specialized applications due to their high temperature resistance, excellent thermal conductivity, and superior mechanical strength. Here are some common applications of ceramic Rigid-Flex PCBs:
- High-Temperature Electronics: Ceramic Rigid-Flex PCBs are ideal for applications requiring operation in high-temperature environments, such as aerospace, automotive, and downhole drilling equipment. The ceramic material can withstand extreme temperatures without degrading, ensuring reliable performance in harsh conditions.
- Power Electronics: In power electronics applications, where high power densities and thermal management are critical, ceramic Rigid-Flex PCBs provide efficient heat dissipation and thermal conductivity. They are used in power converters, motor drives, inverters, and other high-power applications.
- Medical Devices: Ceramic Rigid-Flex PCBs are suitable for medical devices that require sterilization, such as surgical tools, diagnostic equipment, and implantable devices. The ceramic material is biocompatible and resistant to chemical agents used in sterilization processes, ensuring long-term reliability and safety.
- Sensor Systems: Ceramic Rigid-Flex PCBs are commonly used in sensor systems for industrial monitoring, environmental sensing, and automotive applications. The high mechanical strength and dimensional stability of ceramic materials help protect sensitive sensors from mechanical stress and environmental factors.
- RF/Microwave Devices: In radio frequency (RF) and microwave applications, ceramic Rigid-Flex PCBs offer low dielectric loss, high-frequency stability, and minimal signal loss. They are used in radar systems, communication equipment, satellite systems, and wireless infrastructure.
- MEMS Devices: Microelectromechanical systems (MEMS) often require rigid substrates for mechanical stability and precise positioning. Ceramic Rigid-Flex PCBs provide a rigid platform for mounting MEMS sensors and actuators while allowing flexibility in interconnects and packaging.
- Harsh Environment Electronics: In industrial and military applications exposed to harsh environments, such as vibration, shock, moisture, and chemical exposure, ceramic Rigid-Flex PCBs offer ruggedness and reliability. They are used in ruggedized computers, avionics systems, and military electronics.
- Miniaturized Electronics: Ceramic Rigid-Flex PCBs enable miniaturization of electronic devices by providing a compact, robust, and lightweight solution. They are used in miniaturized sensors, wearable electronics, and portable medical devices.
Overall, ceramic Rigid-Flex PCBs are well-suited for applications where high reliability, thermal performance, mechanical strength, and dimensional stability are paramount. While they may be more expensive than traditional PCB materials, their unique properties make them indispensable in certain demanding applications.
FAQs
What are the advantages of Rigid-Flex PCBs?
Rigid-Flex PCBs offer advantages such as space savings, weight reduction, improved reliability, enhanced durability, simplified assembly, design flexibility, and potential cost savings in the long run.
Where are Rigid-Flex PCBs commonly used?
Rigid-Flex PCBs are used in a wide range of applications, including smartphones, wearable devices, medical instruments, aerospace equipment, automotive electronics, industrial controls, and consumer electronics.
What are the key considerations when designing a Rigid-Flex PCB?
Important design considerations include defining flex areas, specifying bend radii, optimizing component placement, routing traces carefully, selecting appropriate materials, and considering manufacturing and assembly constraints.
What materials are used in Rigid-Flex PCB fabrication?
Common materials used in Rigid-Flex PCB fabrication include rigid substrates like FR-4 and flexible substrates like polyimide (PI) or polyester (PET). Copper foil, solder mask, and surface finish materials are also used in the fabrication process.
What are the challenges associated with Rigid-Flex PCB manufacturing?
Challenges include designing for manufacturability, ensuring proper material compatibility, addressing mechanical stress during bending and flexing, maintaining signal integrity, and achieving reliable electrical connections between rigid and flexible sections.
How are Rigid-Flex PCBs fabricated?
The fabrication process typically involves designing the PCB, selecting materials, preparing rigid and flexible substrates, layer alignment and lamination, drilling and via formation, copper plating and etching, surface finish application, component assembly, testing, and final processing.
What are the testing methods used to ensure the quality of Rigid-Flex PCBs?
Testing methods include electrical testing (continuity testing, impedance testing), visual inspection (automated optical inspection), mechanical testing (flexibility testing, bend testing), and thermal testing to ensure the integrity and functionality of the Rigid-Flex PCBs.
What are the cost considerations for Rigid-Flex PCBs?
Cost considerations include material costs, design complexity, fabrication complexity, assembly costs, testing costs, and volume production considerations. While Rigid-Flex PCBs may have higher upfront costs, they can offer long-term cost savings through improved reliability and reduced assembly complexity.