RF Cavity PCBs Manufacturer
RF Cavity PCBs Manufacturer,An RF Cavity PCBs manufacturer specializes in producing printed circuit boards tailored for radio frequency (RF) applications. These PCBs are meticulously engineered with materials and designs optimized for high-frequency signals, ensuring minimal signal loss and interference. They cater to industries such as telecommunications, radar systems, and wireless technology, where precise RF performance is critical. The manufacturer employs advanced fabrication techniques and stringent quality controls to meet the demanding specifications of RF cavity PCBs, enabling reliable transmission and reception of RF signals in various electronic devices and communication systems.
What is RF Cavity PCBs?
RF cavity PCBs, or Radio Frequency (RF) cavity printed circuit boards, are specialized PCBs designed for use in RF cavities. RF cavities are components commonly found in radio frequency systems, such as those used in telecommunications, radar systems, particle accelerators, and medical equipment.
These PCBs are engineered with specific characteristics to meet the requirements of RF cavities, which typically operate at high frequencies. They are constructed using materials with low dielectric constants and losses to minimize signal attenuation and interference. Additionally, RF cavity PCBs may incorporate features such as controlled impedance traces, RF shielding layers, and optimized grounding structures to ensure reliable performance in high-frequency applications.
The design and fabrication of RF cavity PCBs require careful attention to detail to maintain signal integrity and minimize electromagnetic interference. They may also undergo rigorous testing and validation processes to ensure compliance with performance specifications.
Overall, RF cavity PCBs play a crucial role in facilitating the transmission, reception, and processing of radio frequency signals in various electronic systems, contributing to the efficiency and reliability of RF-based technologies.
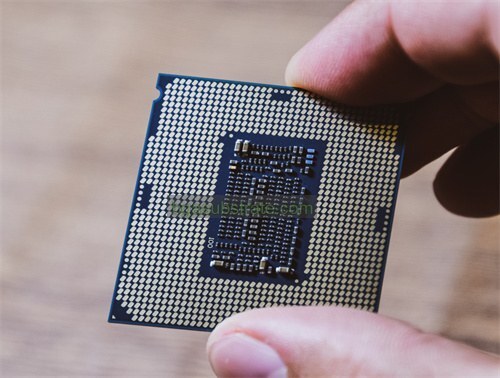
RF Cavity PCBs Manufacturer
What is the RF Cavity PCBs Design Guidelines?
Designing RF cavity PCBs requires careful consideration of various factors to ensure optimal performance at high frequencies. Here are some key design guidelines:
- Material Selection: Choose PCB materials with low dielectric constants and low loss tangents to minimize signal loss and maintain signal integrity at high frequencies. Common materials include high-frequency laminates like PTFE (e.g., Rogers RO4003) or ceramic-filled materials.
- Impedance Control: Maintain controlled impedance for RF traces to match the characteristic impedance of the transmission lines, reducing signal reflections and losses. Use impedance calculation tools and design guidelines specific to your chosen PCB material.
- RF Grounding: Implement a solid ground plane to provide a low impedance return path for RF signals and minimize ground loops. Ensure proper grounding techniques, such as via stitching and grounding vias, to maintain signal integrity and reduce electromagnetic interference (EMI).
- Component Placement and Routing: Place RF components carefully to minimize signal distortion and interference. Keep RF traces short and direct to reduce transmission line losses and electromagnetic coupling between traces. Maintain appropriate spacing between components to avoid parasitic capacitance and inductance.
- RF Shielding: Incorporate RF shielding techniques, such as grounded metal enclosures or copper shielding layers on the PCB, to contain RF signals and prevent external interference. Shield sensitive components and circuitry to minimize crosstalk and EMI.
- Thermal Management: Consider thermal management techniques, especially for high-power RF applications, to dissipate heat effectively and prevent performance degradation. Ensure proper spacing between heat-generating components and use thermal vias or heat sinks as needed.
- Testing and Validation: Perform thorough testing and validation of the RF cavity PCB design to verify performance characteristics, including impedance matching, signal integrity, and EMI/RFI compliance. Use RF test equipment such as vector network analyzers and spectrum analyzers to evaluate the PCB’s performance across the desired frequency range.
By following these design guidelines, engineers can develop RF cavity PCBs that meet the stringent requirements of high-frequency applications, ensuring reliable performance and optimal signal integrity.
The advantages of RF Cavity PCBs
RF cavity PCBs offer several advantages for high-frequency applications compared to conventional PCBs:
- Improved Signal Integrity: RF cavity PCBs are designed with low-loss materials and controlled impedance traces, minimizing signal attenuation, reflections, and distortion. This results in improved signal integrity and reduced signal loss, allowing for more reliable communication and data transmission at high frequencies.
- Enhanced RF Performance: These PCBs are optimized for radio frequency applications, providing better RF performance characteristics such as lower insertion loss, higher isolation, and improved return loss. This allows RF systems to operate more efficiently and effectively, with minimal signal degradation.
- Reduced Electromagnetic Interference (EMI): RF cavity PCBs incorporate features like RF shielding layers and optimized grounding structures to minimize electromagnetic interference. This helps prevent unwanted coupling between RF components and reduces the risk of interference from external sources, improving overall system reliability.
- Compact Design: RF cavity PCBs are often designed with compact layouts and minimal trace lengths to reduce parasitic capacitance and inductance. This compact design allows for smaller form factors, making them suitable for applications where space is limited, such as mobile devices, satellite systems, and wireless sensors.
- High Power Handling: These PCBs are engineered to handle high-power RF signals without significant loss or degradation. They are capable of dissipating heat effectively, ensuring reliable operation even in high-power applications such as RF amplifiers and transmitters.
- Customizable Design: RF cavity PCBs can be customized to meet the specific requirements of different RF systems and applications. Engineers can tailor the PCB design parameters such as trace width, dielectric thickness, and material selection to optimize performance for a particular frequency range or application.
- Cost-Effective Solutions: While RF cavity PCBs may have higher initial manufacturing costs compared to standard PCBs due to specialized materials and manufacturing processes, they offer long-term cost savings by providing reliable performance and minimizing the need for troubleshooting and redesign iterations.
Overall, the advantages of RF cavity PCBs make them indispensable components for a wide range of high-frequency applications, enabling efficient and reliable operation in various RF systems and devices.
What is the RF Cavity PCBs Fabrication Process?
The fabrication process for RF cavity PCBs involves several steps, each critical for achieving high-quality boards suitable for high-frequency applications. Here’s a general overview of the process:
- Material Selection: Choose appropriate PCB materials with low dielectric constants and low loss tangents suitable for RF applications. Common materials include high-frequency laminates like PTFE (e.g., Rogers RO4003) or ceramic-filled materials.
- Design Preparation: Develop the PCB layout using specialized RF design software. This includes determining trace widths, spacing, and layer stackup to achieve the desired impedance control and signal integrity. Pay close attention to component placement and routing to minimize signal distortion and interference.
- Film Lamination: Begin the PCB fabrication process by laminating multiple layers of copper foil and prepreg material onto a substrate. This forms the basic structure of the PCB stackup, which may include alternating layers of copper and dielectric material.
- Drilling:Precision-drill holes through the PCB stackup at locations specified by the PCB design. These holes will later accommodate through-hole components, vias, and interconnections between layers.
- Copper Plating: Apply a thin layer of copper plating to the interior surfaces of the drilled holes. This process, known as electroless copper deposition, creates conductive pathways between different layers of the PCB.
- Circuit Patterning: Apply a layer of photosensitive resist material onto the copper-clad surfaces of the PCB stackup. Use UV light and a photomask to expose the resist material to the PCB design pattern. After exposure, develop and etch the PCB to remove unwanted copper traces, leaving behind the desired circuit pattern.
- Through-hole Plating: Electroplate the drilled holes with additional copper to reinforce conductivity and ensure reliable interconnections between PCB layers. This process, known as through-hole plating, strengthens the vias and facilitates component soldering.
- Surface Finish: Apply a surface finish to protect exposed copper surfaces and facilitate soldering during assembly. Common surface finishes for RF PCBs include immersion gold (ENIG), immersion silver, or immersion tin, chosen for their compatibility with high-frequency signals.
- Final Inspection: Perform visual and electrical inspections to ensure the PCBs meet quality standards and specifications. Check for defects such as shorts, opens, and impedance variations that could affect RF performance.
- Testing: Validate the RF performance of the fabricated PCBs using specialized RF test equipment such as vector network analyzers and spectrum analyzers. Measure key parameters such as impedance matching, insertion loss, return loss, and isolation to verify compliance with design requirements.
By following these steps carefully, manufacturers can produce RF cavity PCBs that meet the stringent requirements of high-frequency applications, ensuring reliable performance and optimal signal integrity.
The application of ceramic RF Cavity PCBs
Ceramic RF cavity PCBs find application in various high-frequency and RF systems where superior performance, reliability, and thermal management are critical. Here are some common applications:
- Wireless Communication Systems: Ceramic RF cavity PCBs are used in wireless communication systems such as cellular base stations, satellite communication systems, and microwave links. They enable efficient transmission and reception of RF signals with minimal loss and interference, ensuring reliable connectivity and high data throughput.
- Radar Systems: Radar systems, including weather radar, military radar, and automotive radar, rely on ceramic RF cavity PCBs for precise signal processing and target detection. These PCBs support the high-frequency operation required for radar applications and provide excellent thermal stability for consistent performance in challenging environments.
- RF Amplifiers:Ceramic RF cavity PCBs are commonly employed in RF power amplifiers used in applications such as broadcasting, medical equipment, and industrial processes. They offer high power handling capabilities and thermal conductivity, allowing efficient amplification of RF signals while maintaining signal integrity and minimizing distortion.
- Particle Accelerators: In scientific research facilities and particle accelerators, ceramic RF cavity PCBs are used to construct resonant cavities for accelerating charged particles. These PCBs provide the necessary precision, stability, and power handling required for accelerating particles to high energies in research experiments and particle physics studies.
- Medical Imaging Equipment: Ceramic RF cavity PCBs play a crucial role in medical imaging equipment such as MRI (Magnetic Resonance Imaging) machines and CT (Computed Tomography) scanners. They enable the transmission and reception of RF signals used in imaging processes, contributing to the clarity and accuracy of medical diagnostic images.
- Aerospace and Defense Systems: Aerospace and defense applications, including avionics, surveillance systems, and electronic warfare equipment, often utilize ceramic RF cavity PCBs for their ruggedness, reliability, and high-performance capabilities. These PCBs can withstand harsh environmental conditions, including extreme temperatures, vibrations, and electromagnetic interference.
- Test and Measurement Instruments: Ceramic RF cavity PCBs are used in test and measurement instruments such as spectrum analyzers, network analyzers, and signal generators. They provide stable RF performance across a wide frequency range, allowing precise measurement and analysis of RF signals in laboratory and field applications.
Overall, ceramic RF cavity PCBs are essential components in a wide range of high-frequency and RF systems, enabling efficient signal transmission, processing, and amplification in diverse applications across industries. Their superior performance characteristics make them indispensable for achieving reliable operation and optimal signal integrity in demanding RF environments.
FAQs
What makes RF cavity PCBs different from standard PCBs?
RF cavity PCBs are engineered with specific characteristics to meet the requirements of high-frequency applications. They use materials with low dielectric constants and losses, controlled impedance traces, and RF shielding to ensure reliable RF performance.
What are the advantages of using RF cavity PCBs?
RF cavity PCBs offer advantages such as improved signal integrity, enhanced RF performance, reduced electromagnetic interference (EMI), compact design, high power handling, customizability, and cost-effective solutions for high-frequency applications.
What are some common applications of ceramic RF cavity PCBs?
Ceramic RF cavity PCBs find applications in wireless communication systems, radar systems, RF amplifiers, particle accelerators, medical imaging equipment, aerospace and defense systems, and test and measurement instruments.
What factors should be considered during the design of RF cavity PCBs?
Important factors to consider include material selection, impedance control, RF grounding, component placement and routing, RF shielding, thermal management, and testing and validation to ensure compliance with performance specifications.
How are RF cavity PCBs fabricated?
The fabrication process involves steps such as material selection, design preparation, film lamination, drilling, copper plating, circuit patterning, through-hole plating, surface finishing, final inspection, and testing to produce PCBs that meet the stringent requirements of high-frequency applications.
What testing methods are used to evaluate the performance of RF cavity PCBs?
RF cavity PCBs are typically tested using specialized RF test equipment such as vector network analyzers and spectrum analyzers. Key parameters measured include impedance matching, insertion loss, return loss, isolation, and overall RF performance across the desired frequency range.