MSD Substrate Manufacturer
MSD Substrate Manufacturer,MSD (Molded Substrate Device) substrates are advanced packaging solutions used to encapsulate and protect semiconductor components while providing robust electrical and mechanical support. These substrates are created using a molding process that forms a protective resin around the semiconductor die and its interconnections. MSD substrates offer excellent thermal dissipation, electrical insulation, and resistance to environmental factors, making them suitable for high-performance and high-reliability applications. They are commonly used in consumer electronics, automotive systems, and industrial devices where durability and stability are crucial. The molded design helps reduce package size and improve the overall performance and longevity of electronic components.
What is MSD Substrate?
MSD (Moisture Sensitivity Device) substrates are specifically designed to address the moisture sensitivity of semiconductor devices. These substrates are critical in the electronics industry because many electronic components are susceptible to damage from moisture. When moisture seeps into these components, it can lead to various issues such as delamination, corrosion, and ultimately, failure of the device.
MSD substrates are engineered to mitigate these risks by incorporating materials and technologies that enhance moisture resistance. This is achieved through advanced material choices, such as specialized coatings or laminates, that provide a protective barrier against moisture. Additionally, the design of MSD substrates often includes features that help in dissipating moisture and preventing it from reaching sensitive areas of the semiconductor.
One common application of MSD substrates is in the packaging of integrated circuits (ICs). The packaging process typically involves sealing the IC in a protective enclosure, and the choice of substrate plays a crucial role in ensuring that the package remains intact and functional over its intended lifespan. By using MSD substrates, manufacturers can extend the reliability and performance of their electronic components, which is especially important in high-reliability applications like aerospace, automotive, and medical devices.
In summary, MSD substrates are essential in safeguarding electronic components from moisture-related damage, thereby enhancing the overall durability and reliability of semiconductor devices.
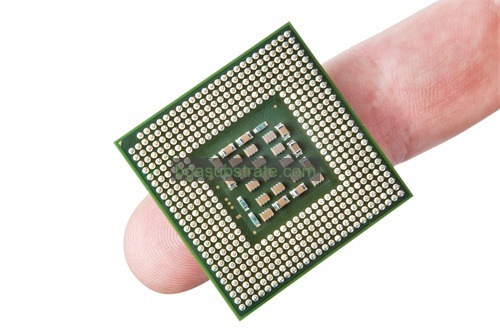
MSD Substrate Manufacturer
What is the MSD Substrate Design Guidelines?
MSD (Moisture Sensitivity Device) substrate design guidelines are crucial for ensuring that electronic components remain reliable and functional despite exposure to moisture. These guidelines help in creating substrates that effectively protect semiconductor devices from moisture-induced damage. Here’s an overview of the key design guidelines:
- Material Selection: Choose substrates made from moisture-resistant materials, such as those with low moisture absorption rates. Materials like high-density polyethylene (HDPE), epoxy resins, and other specialized laminates are often used due to their excellent moisture barriers.
- Protective Coatings:Apply moisture-resistant coatings or laminates to the substrate surface. These coatings act as barriers, preventing moisture ingress and protecting sensitive electronic components.
- Ventilation and Drainage: Design substrates with features that facilitate moisture dissipation. Incorporate drainage channels or ventilation holes to allow trapped moisture to escape, reducing the risk of damage during thermal cycling or soldering processes.
- Sealing Techniques: Ensure that all edges and seams of the substrate are properly sealed. Use adhesives or encapsulants that are effective at keeping moisture out and maintaining the integrity of the substrate.
- Testing and Validation: Implement rigorous testing protocols to verify the moisture resistance of the substrate. This includes subjecting the substrate to various environmental conditions and assessing its performance under stress.
- Compliance with Standards: Follow industry standards and guidelines for moisture sensitivity. Adhering to standards such as JEDEC J-STD-020 ensures that the substrate design meets the required moisture sensitivity levels and performance criteria.
- Packaging and Handling: Use appropriate packaging materials and methods to protect substrates during transportation and storage. Proper handling practices help prevent exposure to moisture before the final assembly of the electronic components.
By following these design guidelines, manufacturers can enhance the durability and reliability of electronic components, ensuring their performance in various environments and applications.
The advantages of MSD Substrate
MSD (Moisture Sensitivity Device) substrates offer several advantages that enhance the reliability and performance of electronic components, particularly in environments where moisture exposure is a concern. Here are the key advantages:
- Improved Reliability: MSD substrates significantly reduce the risk of moisture-related damage, such as delamination and corrosion, which can lead to component failure. This enhances the overall reliability and longevity of electronic devices.
- Enhanced Performance:By protecting sensitive components from moisture, MSD substrates help maintain optimal performance levels. This is crucial in high-reliability applications such as automotive, aerospace, and medical devices where performance consistency is critical.
- Extended Lifespan: Components packaged with MSD substrates are less susceptible to degradation over time. This contributes to a longer operational lifespan, reducing the need for frequent replacements and maintenance.
- Compliance with Standards: MSD substrates help ensure compliance with industry standards and regulations related to moisture sensitivity, such as JEDEC J-STD-020. This compliance is essential for manufacturers to meet quality and performance benchmarks.
- Reduced Failure Rates: By minimizing the potential for moisture-induced failures, MSD substrates help reduce the overall failure rates of electronic components. This leads to increased customer satisfaction and lower warranty costs.
- Versatility: MSD substrates can be designed for a wide range of applications and environments, making them versatile and adaptable to different industry needs. This flexibility allows manufacturers to address various moisture sensitivity challenges effectively.
- Enhanced Manufacturing Efficiency: Proper use of MSD substrates can streamline the manufacturing process by reducing the likelihood of defects and rework caused by moisture-related issues. This leads to more efficient production cycles and cost savings.
In summary, MSD substrates offer significant advantages in terms of reliability, performance, and cost-effectiveness, making them a valuable choice for protecting electronic components from moisture-related damage.
What is the MSD Substrate Fabrication Process?
The fabrication process for MSD (Moisture Sensitivity Device) substrates involves several critical steps to ensure that the final product effectively protects electronic components from moisture-related damage. Here’s an overview of the typical MSD substrate fabrication process:
- Material Selection and Preparation: The process begins with the selection of moisture-resistant materials, such as high-density polyethylene (HDPE), epoxy resins, or specialized laminates. These materials are then prepared and processed to meet the specific requirements of the substrate design.
- Substrate Formation: The chosen materials are formed into substrate sheets or panels. This often involves techniques like lamination, where multiple layers of material are bonded together under heat and pressure to create a robust substrate.
- Coating Application: A critical step is applying moisture-resistant coatings or laminates to the substrate surface. These coatings act as a barrier to prevent moisture ingress. The coating is typically applied through processes such as spin coating, spray coating, or roller coating, and is then cured to form a protective layer.
- Ventilation and Drainage Design: Substrates may be designed with integrated ventilation channels or drainage features. These elements help to dissipate moisture and prevent it from accumulating within the substrate or component package.
- Sealing and Encapsulation: Edges and seams of the substrate are sealed using adhesives or encapsulants. This ensures that all potential entry points for moisture are effectively closed off, enhancing the substrate’s overall moisture resistance.
- Patterning and Etching: If required, the substrate undergoes patterning and etching to define circuit paths or other features. This step involves applying a photoresist material, exposing it to light to create a pattern, and then etching away unwanted material to form the desired circuitry.
- Testing and Quality Control: The substrate is subjected to rigorous testing to verify its moisture resistance and overall quality. Testing methods include humidity exposure, thermal cycling, and other environmental simulations to ensure the substrate meets performance standards.
- Final Inspection and Packaging: After testing, the substrates undergo a final inspection to ensure they meet all specifications. Once approved, they are packaged using moisture-resistant materials to prevent exposure during transportation and storage.
By following these steps, manufacturers can produce MSD substrates that offer enhanced protection against moisture, thereby improving the reliability and performance of electronic components.
The application of ceramic MSD Substrate
Ceramic MSD (Moisture Sensitivity Device) substrates are employed in various applications where high moisture resistance is crucial. Their inherent properties make them suitable for demanding environments. Here’s an overview of their applications:
- High-Performance Electronics: Ceramic MSD substrates are used in high-performance electronic devices where moisture protection is essential. They are commonly found in applications such as aerospace and defense electronics, where reliability and durability are critical under extreme conditions.
- Automotive Industry: In automotive applications, ceramic MSD substrates are used in components exposed to harsh environments, such as engine control units (ECUs) and sensors. Their moisture resistance helps ensure long-term performance and reliability in vehicles.
- Medical Devices: Medical devices often require high levels of reliability and resistance to moisture. Ceramic MSD substrates are used in critical components of medical equipment, such as implantable devices and diagnostic instruments, to prevent moisture-related failures and ensure patient safety.
- Telecommunications: Ceramic MSD substrates are employed in telecommunications infrastructure, including base stations and communication modules. Their moisture resistance helps maintain signal integrity and device functionality in varying environmental conditions.
- Consumer Electronics: In consumer electronics, such as smartphones and tablets, ceramic MSD substrates are used to enhance the durability and reliability of components. They help protect sensitive electronics from moisture damage, contributing to longer device lifespans.
- Industrial Equipment: Industrial machinery and equipment that operate in environments with high humidity or exposure to liquids benefit from ceramic MSD substrates. These substrates help ensure that electronic controls and sensors continue to function reliably.
- Power Electronics: In power electronics, ceramic MSD substrates are used in applications such as power converters and inverters. Their moisture resistance helps maintain performance and prevents degradation in high-power systems.
In summary, ceramic MSD substrates are highly valued in applications where moisture resistance is crucial for maintaining the reliability and longevity of electronic components. Their versatility and durability make them suitable for a wide range of industries and applications.
FAQs about MSD Substrate
Why are MSD substrates important?
MSD substrates are important because they help maintain the reliability and performance of electronic components in environments where moisture exposure could lead to failure or degradation.
What materials are commonly used for MSD substrates?
Common materials include high-density polyethylene (HDPE), epoxy resins, and specialized laminates. These materials are chosen for their low moisture absorption and high protective qualities.
How are MSD substrates manufactured?
The manufacturing process includes selecting moisture-resistant materials, applying protective coatings, designing ventilation and drainage features, sealing edges, and performing rigorous testing to ensure moisture resistance.
In what applications are MSD substrates used?
MSD substrates are used in high-performance electronics, automotive components, medical devices, telecommunications equipment, consumer electronics, industrial machinery, and power electronics.
How do MSD substrates differ from standard substrates?
MSD substrates are specifically designed to offer enhanced moisture resistance compared to standard substrates, which may not provide the same level of protection against moisture-related damage.
How can I test the effectiveness of an MSD substrate?
Effectiveness can be tested through various methods, including humidity exposure tests, thermal cycling tests, and other environmental simulations to verify moisture resistance and overall quality.