Mitsubishi Series Substrate Manufacturer
Mitsubishi Series Substrate Manufacturer,Mitsubishi Series Substrates encompass a diverse range of advanced materials tailored for various electronic applications. These substrates are known for their exceptional thermal management, low thermal expansion, and high mechanical reliability, ensuring stable performance across different environments. Whether used in power modules, RF devices, LED packaging, or automotive electronics, Mitsubishi Series Substrates offer superior electrical characteristics and precise manufacturing quality. Engineers value them for their ability to support complex circuit designs while maintaining consistency in electrical performance. Mitsubishi Series Substrates continue to innovate and set standards in electronic packaging, contributing to the advancement of reliable and efficient electronic systems globally.
What is Mitsubishi Series Substrate?
Mitsubishi Series Substrate typically refers to a range of advanced substrates manufactured by Mitsubishi Materials Corporation, a prominent player in the electronics and semiconductor industries. These substrates are known for their high performance and reliability in various applications, particularly in semiconductor packaging and printed circuit boards (PCBs).
The Mitsubishi Series Substrate encompasses several specialized types tailored to different technological needs. These substrates often feature high thermal conductivity, excellent electrical properties, and mechanical robustness, making them suitable for demanding environments such as automotive electronics, telecommunications infrastructure, and aerospace systems.
One notable example is the Mitsubishi BT Substrate, which is recognized for its thermal management capabilities. It efficiently dissipates heat generated by electronic components, thus enhancing the overall reliability and longevity of electronic devices. This substrate type is crucial in applications requiring efficient heat dissipation to maintain optimal performance and prevent overheating issues.
Moreover, Mitsubishi Series Substrates are designed with precise material composition and manufacturing processes to meet specific performance requirements. This includes considerations for thermal expansion, dielectric properties, and compatibility with different assembly techniques like flip-chip bonding or wire bonding.
In summary, Mitsubishi Series Substrates represent a diverse portfolio of advanced materials essential for modern electronic manufacturing. Their ability to deliver superior performance in thermal management and electrical insulation makes them integral to the development of cutting-edge electronic devices across various industries.
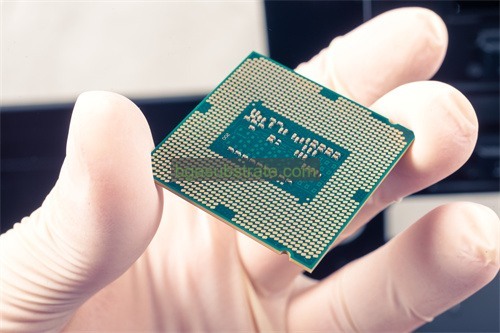
Mitsubishi Series Substrate Manufacturer
What is the Mitsubishi Series Substrate Design Guidelines?
The Mitsubishi Series Substrate Design Guidelines provide comprehensive instructions and recommendations for designing electronic circuits and assemblies using Mitsubishi’s advanced substrate materials. These guidelines are crucial for ensuring optimal performance, reliability, and manufacturability of electronic devices utilizing Mitsubishi substrates.
Key aspects covered in the Mitsubishi Series Substrate Design Guidelines typically include:
- Material Specifications:Detailed specifications of the substrate materials such as thermal conductivity, dielectric constant, coefficient of thermal expansion (CTE), and mechanical properties. These specifications guide designers in selecting the appropriate substrate material based on the specific requirements of their application.
- Layer Stack-up:Guidelines on the optimal layer stack-up configuration, including the number of layers, thickness of each layer, and the arrangement of signal, power, and ground planes. Proper layer stack-up is critical for achieving desired electrical performance and signal integrity.
- Routing and Layout Guidelines:Recommendations for routing high-speed signals, power traces, and critical pathways to minimize signal loss, noise, and electromagnetic interference (EMI). This includes guidelines for impedance control, via design, and clearance requirements between different signal traces and components.
- Thermal Management:Strategies for effective thermal management, including guidelines for placing thermal vias, heat sinks, and thermal pads to efficiently dissipate heat generated by electronic components. This ensures that the substrate maintains acceptable operating temperatures and prevents thermal-induced failures.
- Manufacturing Constraints:Considerations for manufacturing processes such as PCB fabrication, assembly, and testing. Design guidelines often include rules for minimum trace widths and clearances, aspect ratio limits for vias, and other constraints to facilitate smooth production and assembly processes.
- Reliability and Testing:Recommendations for designing for reliability, including guidelines for design margin, reliability testing methodologies, and considerations for environmental factors such as temperature and humidity.
- Compatibility with Assembly Techniques:Guidance on compatibility with various assembly techniques such as surface-mount technology (SMT), flip-chip bonding, and wire bonding. This ensures that the substrate design accommodates the chosen assembly method without compromising performance or reliability.
By following the Mitsubishi Series Substrate Design Guidelines, designers can optimize their electronic designs to leverage the full potential of Mitsubishi substrates, ensuring robust performance, reliability, and manufacturability of electronic devices across diverse applications.
The advantages of Mitsubishi Series Substrate
The Mitsubishi Series Substrate offers several advantages that make it a preferred choice for electronic applications demanding high performance and reliability:
- High Thermal Conductivity:Mitsubishi substrates are known for their excellent thermal management capabilities. High thermal conductivity materials like the Mitsubishi BT Substrate efficiently dissipate heat generated by electronic components, reducing the risk of thermal stress and improving overall reliability.
- Reliability and Durability:These substrates are engineered to provide robust mechanical and electrical properties. They exhibit low coefficient of thermal expansion (CTE), which helps in minimizing stress during temperature cycling, thereby enhancing the durability and longevity of electronic devices.
- Electrical Performance:Mitsubishi substrates offer superior electrical insulation and dielectric properties, ensuring reliable signal integrity and minimizing signal loss. This is critical for high-frequency applications and designs requiring precise electrical performance.
- Versatility and Customization:The Mitsubishi Series includes a range of substrate types tailored to different applications and design requirements. Whether for automotive electronics, telecommunications infrastructure, or aerospace systems, Mitsubishi substrates can be customized in terms of material composition, thickness, and thermal characteristics.
- Compatibility with Advanced Manufacturing Processes:These substrates are designed to be compatible with advanced manufacturing techniques such as surface-mount technology (SMT), flip-chip bonding, and wire bonding. This facilitates efficient assembly and integration into complex electronic systems.
- Environmental Stability:Mitsubishi substrates are engineered to withstand harsh environmental conditions including temperature extremes, humidity, and chemical exposure. This stability ensures consistent performance in challenging operating environments.
- Cost-Effectiveness:While offering high performance, Mitsubishi substrates are designed with cost-effectiveness in mind. They optimize material usage and manufacturing processes to provide value without compromising quality.
Overall, the Mitsubishi Series Substrate stands out for its combination of thermal management efficiency, electrical performance, reliability, and versatility, making it a preferred choice for demanding electronic applications across various industries.
What is the Mitsubishi Series Substrate Fabrication Process?
The fabrication process for Mitsubishi Series Substrates involves several key steps to ensure the production of high-quality, reliable substrates tailored to specific application requirements. While exact details may vary depending on the specific substrate type and application, here is a generalized overview of the typical fabrication process:
- Material Selection and Preparation:The process begins with the selection of appropriate substrate materials based on desired electrical, thermal, and mechanical properties. Mitsubishi offers a range of materials with varying compositions to meet specific application needs.
- Substrate Preparation:Raw substrate materials undergo preparation steps such as cleaning and surface treatment to remove impurities and contaminants. This ensures proper adhesion and quality of subsequent layers and coatings.
- Layer Formation and Deposition:Depending on the substrate design, layers of different materials are deposited onto the prepared substrate surface. This may include dielectric layers, conductive layers (such as copper), and additional functional layers needed for thermal management or electrical insulation.
- Pattern Formation (Lithography):Lithography techniques are used to define the patterns and circuitry on the substrate. This involves applying a photoresist layer, exposing it to UV light through a mask to transfer the desired pattern, and then developing the resist to reveal the pattern on the substrate surface.
- Etching:Etching processes are employed to selectively remove material from the substrate surface based on the pattern defined in the previous step. This step is crucial for forming conductive traces, vias, and other features essential for electrical connectivity and signal routing.
- Surface Finishing:After etching, the substrate surface undergoes surface finishing processes to improve solderability, corrosion resistance, and overall durability. This may involve applying surface treatments or coatings such as solder masks, ENIG (Electroless Nickel Immersion Gold), or HASL (Hot Air Solder Leveling).
- Quality Control and Testing:Throughout the fabrication process, rigorous quality control measures are implemented to ensure the substrates meet specified standards for dimensional accuracy, electrical conductivity, thermal performance, and reliability. Testing procedures may include electrical testing, thermal cycling tests, and visual inspections.
- Final Inspection and Packaging:Once fabrication and testing are completed, substrates undergo final inspection to verify adherence to quality standards and customer specifications. Substrates are then carefully packaged to protect them during transportation and storage, ready for integration into electronic assemblies.
The Mitsubishi Series Substrate fabrication process emphasizes precision, quality control, and customization to deliver substrates optimized for high-performance electronic applications across industries such as automotive, telecommunications, aerospace, and more. Each step in the process plays a critical role in ensuring the substrates meet stringent performance and reliability requirements demanded by modern electronic devices.
The application of ceramic Mitsubishi Series Substrate
The ceramic Mitsubishi Series Substrate finds extensive application in various high-performance electronic and semiconductor devices where thermal management, reliability, and electrical performance are critical. Here are some key applications:
- Power Electronics:Mitsubishi Series Substrates are widely used in power electronic modules and devices. Their high thermal conductivity helps in efficiently dissipating heat generated by power components such as transistors, diodes, and integrated circuits. This capability improves device reliability and extends operational lifespan.
- RF/Microwave Devices:For RF (Radio Frequency) and microwave applications, Mitsubishi substrates offer excellent dielectric properties and dimensional stability. They support the precise fabrication of microstrip lines, antennas, and other components critical for signal integrity and high-frequency performance.
- Automotive Electronics:In automotive electronics, Mitsubishi Series Substrates are employed in engine control modules, powertrain systems, and advanced driver-assistance systems (ADAS). Their ability to withstand high temperatures and harsh environmental conditions ensures reliable performance in automotive applications.
- Telecommunications Infrastructure:Telecommunications equipment such as base stations, routers, and network switches utilize Mitsubishi substrates for their thermal management capabilities and electrical insulation properties. These substrates help maintain stable operation under varying load conditions and environmental factors.
- Aerospace and Defense:In aerospace and defense applications, where reliability and performance under extreme conditions are paramount, Mitsubishi Series Substrates are used in avionics systems, satellite communications, radar systems, and missile guidance systems. Their rugged construction and high thermal conductivity contribute to the overall reliability and mission-critical performance.
- LED Lighting:Mitsubishi substrates play a crucial role in LED lighting applications, where efficient thermal management is essential to maintain LED performance and longevity. They are used in high-power LED modules and arrays, ensuring optimal heat dissipation and enhancing overall energy efficiency.
- Medical Devices:Medical devices requiring high reliability and precision, such as diagnostic equipment and patient monitoring systems, benefit from Mitsubishi Series Substrates. These substrates support the integration of sensitive electronics while ensuring robust performance in medical environments.
- Consumer Electronics:In consumer electronics, Mitsubishi substrates are utilized in smartphones, tablets, and other portable devices where compact size, thermal efficiency, and reliability are critical factors. They contribute to the miniaturization and improved performance of electronic gadgets.
Overall, the Mitsubishi Series Substrate’s diverse applications across industries highlight its versatility and capability to meet stringent requirements for thermal management, electrical performance, and reliability in modern electronic devices and systems.
FAQs about Mitsubishi Series Substrate
What is Mitsubishi Series Substrate?
Mitsubishi Series Substrate refers to a range of advanced ceramic substrates manufactured by Mitsubishi Materials Corporation. These substrates are known for their high thermal conductivity, excellent electrical properties, and reliability, making them suitable for various electronic applications.
What are the key advantages of Mitsubishi Series Substrate?
The advantages include high thermal conductivity for effective heat dissipation, superior electrical insulation and performance, reliability under harsh conditions, compatibility with advanced manufacturing processes, and customization options to meet specific application needs.
What industries use Mitsubishi Series Substrate?
Mitsubishi Series Substrate is used in industries such as automotive electronics, telecommunications, aerospace and defense, power electronics, RF/microwave devices, LED lighting, medical devices, and consumer electronics.
What are the typical applications of Mitsubishi Series Substrate?
Typical applications include power electronic modules, RF/microwave components, automotive engine control units, telecommunications infrastructure, aerospace avionics, LED lighting modules, medical devices, and consumer electronics.
How does Mitsubishi Series Substrate compare to other substrate materials?
Mitsubishi Series Substrate stands out for its high thermal conductivity, which is superior to many other substrate materials. It also offers excellent electrical properties and reliability, making it a preferred choice for demanding electronic applications.
What are the fabrication processes involved in manufacturing Mitsubishi Series Substrate?
The fabrication process includes material selection, substrate preparation, layer deposition, lithography and etching for pattern formation, surface finishing, rigorous quality control and testing, and final inspection and packaging.
Where can Mitsubishi Series Substrate be purchased or sourced?
Mitsubishi Series Substrate can typically be sourced directly from Mitsubishi Materials Corporation or through authorized distributors specializing in electronic materials and components.