Mitsubishi BT Substrate Manufacturer
Mitsubishi BT Substrate Manufacture,Mitsubishi BT Substrate is a highly engineered material renowned for its exceptional thermal conductivity and reliability in electronic packaging. Designed for power modules and RF applications, it offers superior heat dissipation, ensuring efficient operation under high-power conditions. Mitsubishi BT Substrate features low thermal expansion and excellent mechanical strength, supporting robust performance across varying temperatures and environmental stresses. Its ability to facilitate complex circuit designs while maintaining electrical integrity makes it ideal for automotive, industrial, and telecommunications sectors. Engineers value Mitsubishi BT Substrate for its consistent quality and suitability in demanding applications where reliability and thermal management are critical.
What is Mitsubishi BT Substrate?
Mitsubishi BT Substrate refers to a type of ceramic substrate used primarily in electronic packaging and semiconductor applications. It belongs to the family of High Temperature Co-Fired Ceramics (HTCC), known for their excellent thermal and electrical properties.
These substrates are fabricated using a process where multiple layers of ceramic material are screen-printed with conductive and insulating pastes. After printing, the layers are stacked and fired at high temperatures, typically above 1000°C, to achieve dense, robust structures capable of withstanding harsh environmental conditions and high frequencies.
Mitsubishi BT Substrates are valued for their low dielectric constant (εr), which ensures minimal signal loss and high signal integrity, crucial for high-frequency applications such as RF/microwave circuits and power modules. Their thermal conductivity properties also enable efficient heat dissipation, making them suitable for power electronics where thermal management is critical.
Applications of Mitsubishi BT Substrates span various industries, including telecommunications, automotive electronics, aerospace, and medical devices. Their ability to integrate complex circuit designs in a compact form factor while maintaining reliability under extreme conditions makes them indispensable in modern electronic systems.
Manufacturers often customize Mitsubishi BT Substrates to meet specific design requirements, offering options in thickness, layer count, and surface finishes tailored to optimize performance in different electronic applications. As technology advances, these substrates continue to evolve, supporting the development of smaller, faster, and more efficient electronic devices.
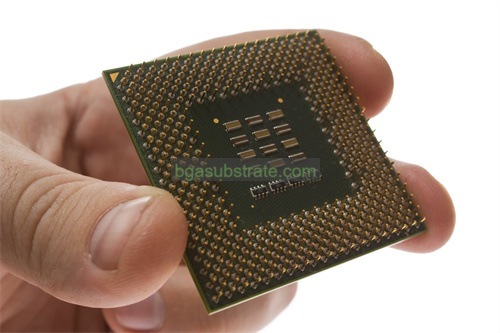
Mitsubishi BT Substrate Manufacturer
What is the Mitsubishi BT Substrate Design Guidelines?
The design guidelines for Mitsubishi BT Substrates typically encompass several key aspects to ensure optimal performance and manufacturability. Here are some common considerations:
- Material Properties: Understanding the thermal conductivity, dielectric constant (εr), and mechanical strength of Mitsubishi BT Substrates is crucial. These properties dictate how well the substrate can dissipate heat, minimize signal loss, and withstand mechanical stress.
- Layer Configuration: Designers need to determine the optimal number of layers and their stacking sequence based on the complexity of the circuit design and the required electrical performance. This includes deciding on the distribution of signal, power, and ground layers to achieve desired impedance matching and noise reduction.
- Via Design: Proper via placement and sizing are critical for ensuring reliable electrical connections between different layers of the substrate. Vias should be optimized to minimize signal distortion and ensure sufficient current-carrying capacity.
- Dimensional Tolerances: Mitsubishi BT Substrates have specific dimensional tolerances that designers must adhere to, ensuring compatibility with assembly processes and mating components. This includes tolerances for hole sizes, edge margins, and overall substrate dimensions.
- Surface Finish and Coating: Selection of appropriate surface finishes and coatings is essential to ensure good solderability, corrosion resistance, and compatibility with assembly methods (e.g., soldering, wire bonding). Common surface finishes include ENIG (Electroless Nickel Immersion Gold), HASL (Hot Air Solder Leveling), and OSP (Organic Solderability Preservatives).
- Thermal Management: Since Mitsubishi BT Substrates are often used in applications requiring efficient heat dissipation, designers should consider incorporating features like thermal vias, heat sinks, or thermal pads to enhance thermal management capabilities.
- Electromagnetic Interference (EMI) Shielding: Depending on the application, provisions for EMI shielding may be necessary. This could involve incorporating metal layers or designing the substrate layout to minimize electromagnetic emissions and susceptibility.
- Testing and Quality Assurance: Designers should plan for testing methodologies to verify electrical performance, mechanical robustness, and adherence to specifications throughout the manufacturing process.
By following these guidelines, designers can maximize the performance, reliability, and manufacturability of Mitsubishi BT Substrates in various electronic applications, ranging from RF/microwave circuits to power electronics and beyond.
The advantages of Mitsubishi BT Substrate
Mitsubishi BT Substrates offer several advantages that make them highly suitable for a range of electronic applications:
- 1. High Thermal Conductivity: These substrates exhibit excellent thermal conductivity, allowing efficient dissipation of heat generated by electronic components. This property helps in maintaining optimal operating temperatures and prolonging component lifespan.
- Low Dielectric Constant: With a low dielectric constant (εr), Mitsubishi BT Substrates minimize signal loss and ensure high signal integrity, making them ideal for high-frequency applications such as RF/microwave circuits. This characteristic also supports the transmission of high-speed digital signals.
- Mechanical Strength: HTCC materials, including Mitsubishi BT Substrates, are inherently strong and durable. They can withstand mechanical stresses, including thermal cycling, vibrations, and shocks, which is crucial for reliable performance in rugged environments such as automotive and aerospace applications.
- Design Flexibility:These substrates offer design flexibility with the ability to create complex multilayer structures. Designers can customize layer configurations, via placements, and surface finishes to optimize electrical performance and meet specific application requirements.
- Compatibility with High Temperature Environments: Mitsubishi BT Substrates are designed to withstand high temperatures during manufacturing processes and in operation. This capability makes them suitable for applications where exposure to elevated temperatures is common, such as automotive under-the-hood electronics and industrial equipment.
- Chemical and Environmental Resistance: HTCC materials are generally resistant to chemicals and environmental factors like moisture and humidity, ensuring long-term reliability in harsh conditions.
- Miniaturization: Due to their high mechanical strength and excellent electrical properties, Mitsubishi BT Substrates enable the miniaturization of electronic devices and modules without sacrificing performance or reliability.
- Cost-Effective Production: While initially more expensive than some traditional PCB materials, the cost-effectiveness of Mitsubishi BT Substrates increases when considering their durability, reliability, and performance benefits over the product lifecycle.
Overall, Mitsubishi BT Substrates are valued for their robustness, thermal management capabilities, high-frequency performance, and suitability for demanding applications across various industries, contributing to the advancement of electronic technologies.
What is the Mitsubishi BT Substrate Fabrication Process?
The fabrication process of Mitsubishi BT Substrates, as part of High Temperature Co-Fired Ceramic (HTCC) technology, involves several key steps to create complex, high-performance ceramic substrates:
- Material Preparation: The process begins with selecting high-purity ceramic materials, typically alumina (Al₂O₃) or other ceramics with desired thermal and electrical properties. These materials are finely ground and mixed to achieve a homogeneous ceramic paste.
- Screen Printing: Ceramic pastes are screen-printed onto green sheets of ceramic material. The green sheets are flexible and can be stacked to create multilayer structures. During screen printing, conductive materials (usually silver or gold-based pastes) are applied to form circuit patterns, while insulating pastes define the substrate’s layers.
- Layer Stacking: Multiple green sheets, each printed with conductive and insulating patterns, are stacked layer by layer according to the substrate design. Each layer’s patterns are aligned precisely to ensure proper electrical connectivity and component placement.
- Laminating: The stacked green sheets undergo a lamination process under controlled pressure and temperature. This step removes air and ensures intimate contact between layers, enhancing the substrate’s mechanical integrity.
- Cofiring (Firing): The laminated stack undergoes a firing process in a high-temperature kiln, typically above 1000°C (1832°F). During firing, the ceramic materials densify, and the organic binders in the green sheets burn out, leaving a solid, robust ceramic substrate with the printed conductive and insulating layers fused together.
- Machining: After firing, the ceramic substrate undergoes precision machining processes such as drilling, cutting, and milling to create vias, holes, and the final substrate shape according to design specifications.
- Metallization: Metal layers (typically gold or other suitable metals) are deposited on the substrate surfaces and inside vias through processes like sputtering or electroplating. This metallization step provides electrical connectivity between different layers and facilitates component attachment (soldering or wire bonding).
- Surface Finishing: Finally, the substrate undergoes surface finishing treatments such as applying solder masks or protective coatings to ensure solderability, corrosion resistance, and durability during assembly and operation.
Throughout the fabrication process, strict quality control measures are implemented to verify dimensions, electrical properties, and overall substrate integrity. Mitsubishi BT Substrates are tailored for demanding applications requiring high reliability, thermal management, and electrical performance, such as in automotive electronics, telecommunications, aerospace, and medical devices.
The application of ceramic Mitsubishi BT Substrate
Mitsubishi BT Substrates find wide application across various industries due to their excellent thermal management, high-frequency performance, and mechanical robustness. Some key applications include:
- RF/Microwave Modules: These substrates are ideal for RF/microwave modules and circuits due to their low dielectric constant (εr) and high thermal conductivity. They minimize signal loss and heat buildup, crucial for maintaining signal integrity and reliability in high-frequency communication systems.
- Power Electronics:Mitsubishi BT Substrates are used in power modules for efficient heat dissipation and electrical insulation. Their ability to withstand high temperatures and mechanical stress makes them suitable for power inverters, converters, and motor drive applications in automotive, industrial, and renewable energy sectors.
- Automotive Electronics: In automotive applications, Mitsubishi BT Substrates are employed in engine control units (ECUs), sensors, radar systems, and LED lighting modules. Their robustness and thermal management capabilities ensure reliable operation in harsh environments with temperature variations and vibrations.
- Aerospace and Defense: These substrates support critical electronic systems in aerospace and defense applications, including radar systems, avionics, satellite communications, and missile guidance systems. Their high reliability and resistance to environmental factors make them essential for mission-critical operations.
- Medical Devices: Mitsubishi BT Substrates are used in medical electronics such as imaging equipment (MRI, CT scanners), patient monitoring systems, and implantable devices. Their biocompatibility, thermal stability, and electrical performance contribute to the reliability and safety of medical electronics.
- Telecommunications: For telecommunications infrastructure, these substrates are employed in base station antennas, satellite communication systems, and high-speed data transmission equipment. They enable compact designs with high-frequency performance and reliability in telecommunications networks.
- Industrial Electronics: In industrial applications, Mitsubishi BT Substrates are used in power supplies, industrial automation systems, and control electronics. Their ability to handle high currents, thermal cycling, and harsh industrial environments ensures dependable operation in manufacturing and process control systems.
Overall, Mitsubishi BT Substrates play a crucial role in advancing electronic technologies across diverse industries, contributing to enhanced performance, reliability, and miniaturization of electronic devices and systems.
FAQs about Mitsubishi BT Substrate
What materials are used in Mitsubishi BT Substrates?
Typically, high-purity alumina (Al₂O₃) or other ceramics with desired thermal and electrical properties are used in Mitsubishi BT Substrates.
Can Mitsubishi BT Substrates be customized?
Yes, they can be customized in terms of layer configuration, via placement, surface finish, and overall design to meet specific application requirements.
What are the thermal management capabilities of Mitsubishi BT Substrates?
They have high thermal conductivity, which allows efficient dissipation of heat generated by electronic components, maintaining optimal operating temperatures and enhancing reliability.
Why are Mitsubishi BT Substrates suitable for high-frequency applications?
Their low dielectric constant minimizes signal loss, ensuring high signal integrity, which is crucial for RF/microwave circuits and high-speed digital signal transmission.
What surface finishes are available for Mitsubishi BT Substrates?
Common surface finishes include ENIG (Electroless Nickel Immersion Gold), HASL (Hot Air Solder Leveling), and OSP (Organic Solderability Preservatives), depending on the specific application requirements.
What industries benefit from using Mitsubishi BT Substrates?
Industries such as automotive, telecommunications, aerospace, medical, industrial electronics, and defense benefit from the advanced properties of Mitsubishi BT Substrates.
How do Mitsubishi BT Substrates contribute to miniaturization?
Their high mechanical strength and excellent electrical properties allow for the design of compact and complex electronic modules, enabling the miniaturization of electronic devices.