Megtron 6 Substrate Manufacturer
Megtron 6 Substrate Manufacturer,Megtron 6 Substrate is an advanced material designed for high-frequency and high-speed digital applications, known for its exceptional performance and reliability. It features a low dielectric constant and low dissipation factor, ensuring minimal signal loss and excellent signal integrity across a broad frequency range. Megtron 6 offers superior thermal conductivity and stability, crucial for efficient heat dissipation and consistent electrical performance in demanding environments. Its robust mechanical properties, including high glass transition temperature and low thermal expansion, support complex circuit designs with precision and reliability. Engineers trust Megtron 6 Substrate for applications in telecommunications, computing, and aerospace industries where performance and durability are paramount.
What is Megtron 6 Substrate?
Megtron 6 substrate is an advanced material used in printed circuit boards (PCBs) known for its high-frequency performance and reliability. It belongs to the Megtron series developed by Panasonic, designed to meet the demanding requirements of high-speed digital and RF/microwave applications. Megtron 6 offers excellent signal integrity, low transmission loss characteristics, and thermal reliability, making it suitable for applications where high data transmission rates and minimal signal distortion are critical.
Key features of Megtron 6 include its low dielectric constant (εr) and low dissipation factor (tanδ), which contribute to its high-frequency performance. It is capable of supporting high layer counts and complex designs, making it ideal for use in advanced PCBs for telecommunications, automotive electronics, and aerospace industries. Megtron 6 substrates are also known for their thermal stability and reliability under harsh environmental conditions, ensuring consistent performance over the PCB’s operational lifetime.
Manufacturers appreciate Megtron 6 for its compatibility with lead-free assembly processes and its ability to reduce electromagnetic interference (EMI) in electronic circuits. Overall, Megtron 6 substrate stands out as a robust choice for high-performance PCB applications demanding high-speed signal transmission, reliability, and durability.
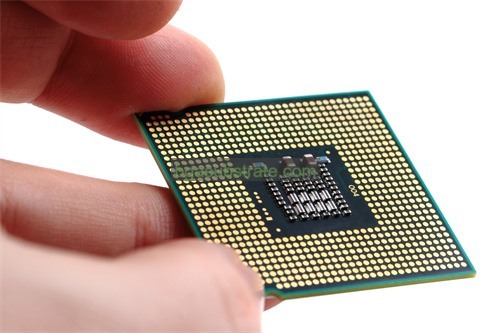
Megtron 6 Substrate Manufacturer
What is the Megtron 6 Substrate Design Guidelines?
The design guidelines for Megtron 6 substrate focus on optimizing PCB layouts to leverage its high-frequency performance and reliability. Here are some key points typically included in design guidelines for Megtron 6:
- Dielectric Constant and Loss Tangent: Understand the specified values of dielectric constant (εr) and loss tangent (tanδ) for Megtron 6. Designers should account for these parameters to ensure signal integrity and minimize signal loss, especially at higher frequencies.
- Impedance Control: Maintain controlled impedance traces to match specified values accurately. Megtron 6’s stable dielectric properties help in achieving consistent impedance characteristics across the PCB, critical for high-speed signal integrity.
- Via Design: Optimize via structures to minimize impedance discontinuities and signal reflections. Consider using blind and buried vias where necessary to conserve PCB real estate and enhance signal integrity.
- Routing and Trace Width: Design traces with appropriate widths to handle high-frequency signals effectively. Follow recommended guidelines for spacing between traces and clearance from other components to prevent crosstalk and EMI issues.
- Thermal Management:Ensure adequate thermal management strategies, such as heat sinks or thermal vias, especially in designs involving high power or components susceptible to temperature variations. Megtron 6’s thermal reliability supports efficient heat dissipation.
- Material Handling: Adhere to best practices for handling and storage to prevent contamination or damage to Megtron 6 substrates, which can affect electrical performance.
- Manufacturing Process Compatibility: Verify compatibility with chosen PCB fabrication processes, including soldering and assembly techniques. Megtron 6 substrates are typically compatible with lead-free assembly methods but should be verified for specific applications.
- Environmental Considerations: Consider environmental factors such as humidity, temperature variations, and mechanical stress during design to ensure PCB reliability over its operational lifespan.
By following these guidelines, designers can harness the full potential of Megtron 6 substrate’s capabilities, ensuring robust performance in high-frequency and high-speed applications across various industries.
The advantages of Megtron 6 Substrate
Megtron 6 substrate offers several advantages that make it a preferred choice for high-performance printed circuit board (PCB) applications:
- High-Frequency Performance: Megtron 6 has a low dielectric constant (εr) and low dissipation factor (tanδ), which enable excellent signal integrity and minimal signal loss at high frequencies. This characteristic is crucial for applications requiring reliable high-speed data transmission and low electromagnetic interference (EMI).
- Thermal Reliability: The substrate exhibits robust thermal stability, making it suitable for PCBs operating in environments with varying temperatures. It helps in maintaining consistent electrical performance even under thermal stress, ensuring reliability over the PCB’s lifetime.
- Mechanical Strength: Megtron 6 substrates are known for their mechanical strength and dimensional stability. They can withstand mechanical stress during PCB fabrication and assembly processes, reducing the risk of delamination or warping.
- Compatibility with Lead-Free Processes:It is compatible with lead-free soldering processes, aligning with environmental regulations and industry trends towards sustainable manufacturing practices.
- Design Flexibility: Megtron 6 supports high layer counts and complex PCB designs, offering flexibility in designing multilayer boards with dense circuitry. It allows for precise impedance control and optimal routing of high-frequency signals.
- Reduced Electromagnetic Interference (EMI): Due to its excellent signal integrity and low loss tangent, Megtron 6 helps in minimizing electromagnetic interference, enhancing overall circuit performance and reducing the need for additional shielding measures.
- Reliability in Harsh Environments: Ideal for applications in automotive electronics, telecommunications, and aerospace industries, Megtron 6 substrates excel in harsh environmental conditions where reliability and durability are critical factors.
Overall, Megtron 6 substrate’s combination of high-frequency performance, thermal reliability, mechanical strength, and design flexibility makes it a preferred choice for demanding PCB applications requiring superior electrical and mechanical properties.
What is the Megtron 6 Substrate Fabrication Process?
The fabrication process of Megtron 6 substrate typically involves several key steps to ensure its high-performance characteristics and reliability:
- Material Preparation: Megtron 6 substrate materials, which include specialized glass cloth impregnated with epoxy resin and reinforced with ceramic fillers, are prepared according to specified formulations. These materials are selected for their low dielectric constant (εr) and low dissipation factor (tanδ) properties.
- Lamination:The prepared Megtron 6 materials are stacked layer by layer with copper foil interleaved between them. This stack is then pressed together under controlled temperature and pressure in a lamination press. This process bonds the layers of material and forms a solid composite structure.
- Drilling:After lamination, the composite panel undergoes precision drilling to create holes for vias and component mounting pads. Advanced drilling techniques are employed to ensure accuracy and consistency across the panel.
- Copper Plating:The panel is subjected to copper plating processes. This involves electroplating copper onto the walls of the drilled holes (vias) and onto the surface of the panel to form the circuit traces. Copper plating enhances conductivity and ensures proper electrical connectivity throughout the PCB.
- Etching:Circuit patterns are defined by etching away excess copper from the surface using chemical etchants. This step ensures that only the desired copper traces and pads remain, conforming to the PCB design layout.
- Surface Finish:Surface finish processes are applied to protect the exposed copper surfaces from oxidation and facilitate solderability during assembly. Common surface finishes for Megtron 6 substrates include immersion tin, immersion silver, ENIG (Electroless Nickel Immersion Gold), and OSP (Organic Solderability Preservatives).
- Testing and Inspection:Quality control measures such as electrical testing, dimensional verification, and visual inspection are performed to ensure that the fabricated Megtron 6 PCB meets specified performance criteria and industry standards.
- Final Processing:Once the PCBs pass inspection, they undergo final processing steps such as routing, scoring, or panelization to prepare them for assembly into electronic devices.
Throughout these fabrication steps, careful attention to detail and adherence to process parameters are critical to achieving the high-frequency performance, thermal reliability, and mechanical strength characteristics that Megtron 6 substrates are known for.
The application of ceramic Megtron 6 Substrate
Megtron 6 substrate, despite its name suggesting ceramic, is actually an advanced epoxy-based material developed by Panasonic for high-performance printed circuit board (PCB) applications. Here are some key applications where Megtron 6 substrate excels:
- High-Speed Digital Electronics: Megtron 6 is widely used in high-speed digital electronics such as servers, network equipment, and high-performance computing (HPC) systems. Its low dielectric constant (εr) and low dissipation factor (tanδ) help in maintaining signal integrity and reducing signal loss, crucial for data transmission at high frequencies.
- Telecommunications: In telecommunications equipment, Megtron 6 substrates are employed for their excellent high-frequency performance. They support the design of RF/microwave circuits, antennas, and base station components where reliable signal transmission and low electromagnetic interference (EMI) are essential.
- Automotive Electronics: Due to its robust thermal stability and mechanical strength, Megtron 6 is used in automotive electronics applications. It can withstand harsh environmental conditions, vibrations, and temperature fluctuations commonly encountered in automotive systems, making it suitable for engine control units, infotainment systems, and advanced driver-assistance systems (ADAS).
- Aerospace and Defense: Megtron 6 substrates are chosen for aerospace and defense applications where reliability and durability are critical. They are used in radar systems, avionics, satellite communications, and other mission-critical electronic equipment that require high performance under extreme conditions.
- Industrial Electronics: Industrial applications such as control systems, power electronics, and instrumentation benefit from Megtron 6 substrates. Their thermal reliability ensures consistent performance in industrial environments, while their high-frequency capabilities support precise control and monitoring systems.
- Consumer Electronics: Megtron 6 can also be found in consumer electronics where high-speed data transmission and compact designs are needed. Applications include high-end computing devices, gaming consoles, and multimedia equipment where PCB performance directly impacts user experience and device functionality.
Overall, Megtron 6 substrate’s combination of high-frequency performance, thermal reliability, and mechanical strength makes it suitable for a wide range of demanding applications across various industries, contributing to the advancement of electronic technologies in both commercial and specialized fields.
FAQs about Megtron 6 Substrate
What is Megtron 6 substrate?
Megtron 6 is an advanced epoxy-based material developed by Panasonic for printed circuit board (PCB) applications. It offers low dielectric constant (εr) and low dissipation factor (tanδ), making it ideal for high-frequency and high-speed electronic designs.
What are the key advantages of using Megtron 6 substrate?
Megtron 6 substrate offers advantages such as excellent high-frequency performance, robust thermal reliability, mechanical strength, compatibility with lead-free processes, and reduced electromagnetic interference (EMI).
Where is Megtron 6 substrate commonly used?
It is commonly used in applications requiring high-speed digital electronics, telecommunications equipment, automotive electronics, aerospace and defense systems, industrial electronics, and consumer electronics.
What are the typical applications of Megtron 6 substrate?
Megtron 6 substrate is used in servers, network equipment, HPC systems, RF/microwave circuits, automotive control units, ADAS systems, aerospace electronics, radar systems, industrial control systems, and high-end consumer electronics.
How does Megtron 6 substrate compare to other PCB materials?
Compared to standard PCB materials, Megtron 6 offers superior high-frequency performance, better thermal reliability, and mechanical strength, making it suitable for demanding applications where these properties are critical.
What are the design considerations when using Megtron 6 substrate?
Designers should consider impedance control, routing for high-frequency signals, thermal management, material handling practices, and compatibility with fabrication processes to fully leverage the benefits of Megtron 6 substrate.
Is Megtron 6 substrate environmentally friendly?
Megtron 6 is designed to be compatible with lead-free assembly processes, aligning with environmental regulations and sustainable manufacturing practices in the electronics industry.