ISOLA P96/P26 Substrate Manufacturer
ISOLA P96/P26 Substrate Manufacturer,ISOLA P96/P26 is a high-performance substrate material designed for advanced PCB applications. It offers excellent electrical properties, including a low dielectric constant and low dissipation factor, which ensure high signal integrity and minimal signal loss. The substrate features outstanding thermal stability and mechanical strength, making it ideal for complex, high-layer-count circuit boards. P96/P26 is also known for its resistance to high temperatures and thermal cycling, which enhances its reliability in demanding environments. Suitable for telecommunications, automotive, and high-speed digital applications, ISOLA P96/P26 delivers robust performance and durability, making it a preferred choice for cutting-edge electronic systems.
What is ISOLA P96/P26 Substrate?
The ISOLA P96/P26 substrate is a high-performance material specifically designed for advanced printed circuit board (PCB) applications. This substrate belongs to the family of high-frequency laminates produced by Isola Group, a leading manufacturer of PCB materials.
ISOLA P96/P26 is characterized by its excellent electrical and thermal properties, making it suitable for demanding environments where high-speed signal integrity and thermal management are critical. The substrate features a dielectric constant (Dk) of around 3.8, which is crucial for maintaining signal integrity and minimizing signal loss in high-frequency applications. Additionally, it has a low dissipation factor (Df), which reduces signal attenuation and enhances overall performance.
One of the key advantages of ISOLA P96/P26 is its thermal stability. The material exhibits a high glass transition temperature (Tg), which allows it to withstand elevated temperatures during the PCB manufacturing process and in end-use conditions. This thermal robustness ensures that the substrate maintains its structural integrity and performance over time.
ISOLA P96/P26 is often used in high-frequency and high-speed digital applications, including telecommunications, aerospace, and automotive electronics. Its advanced properties make it suitable for use in RF (radio frequency) circuits, microwave applications, and high-speed digital circuits where performance and reliability are paramount.
Overall, the ISOLA P96/P26 substrate offers a combination of high electrical performance, thermal stability, and reliability, making it a preferred choice for high-performance PCB designs.
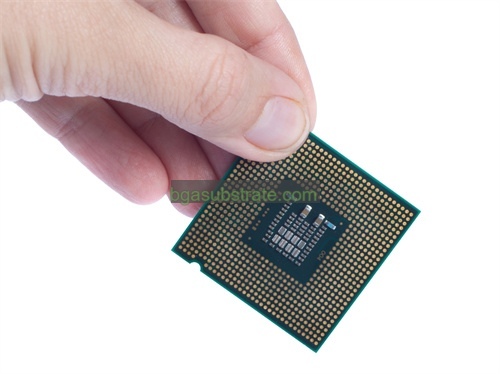
ISOLA P96/P26 Substrate Manufacturer
What is the ISOLA P96/P26 Substrate Design Guidelines?
The ISOLA P96/P26 substrate is designed to meet high-performance requirements in advanced PCB applications. To ensure optimal performance and reliability, several design guidelines should be followed when using this substrate:
- Material Properties: ISOLA P96/P26 offers a dielectric constant (Dk) of approximately 3.8 and a low dissipation factor (Df). Ensure that these properties are considered in your design to maintain signal integrity and minimize attenuation, especially in high-frequency and high-speed circuits.
- Thermal Management: With its high glass transition temperature (Tg), ISOLA P96/P26 can withstand elevated temperatures. Design your PCB to accommodate thermal expansion and manage heat dissipation effectively. Ensure that heat-sensitive components are placed away from high-heat areas and consider using thermal vias or heat sinks if necessary.
- Layer Stackup: Proper layer stackup is crucial for maintaining signal integrity. Consider using a balanced stackup to control impedance and reduce signal reflections. Pay attention to the dielectric thickness between signal layers and ground planes to achieve the desired impedance characteristics.
- Impedance Control: For high-speed and high-frequency applications, precise impedance control is essential. Use simulation tools to model the PCB and verify that the impedance of transmission lines, traces, and other critical elements meets design requirements.
- Manufacturing Considerations: Follow recommended manufacturing practices for handling and processing ISOLA P96/P26. This includes proper lamination techniques, drill and plating processes, and cleaning procedures to ensure the quality and reliability of the final PCB.
- Thermal Cycling: Given the substrate’s low coefficient of thermal expansion (CTE), it is essential to consider thermal cycling effects in your design. Design for thermal reliability by ensuring adequate mechanical support for components and minimizing stress on solder joints and interconnects.
- Electrical Performance: Incorporate shielding and grounding techniques to reduce electromagnetic interference (EMI) and ensure signal integrity. Design appropriate trace routing and avoid sharp corners to minimize signal degradation and cross-talk.
By adhering to these design guidelines, you can leverage the advanced properties of ISOLA P96/P26 to create high-performance, reliable PCBs for demanding applications.
The advantages of ISOLA P96/P26 Substrate
The ISOLA P96/P26 substrate offers several key advantages that make it highly suitable for advanced PCB applications:
- High Electrical Performance: The substrate features a dielectric constant (Dk) of approximately 3.8 and a low dissipation factor (Df). This combination ensures minimal signal loss and attenuation, which is crucial for high-speed and high-frequency applications, such as telecommunications and RF circuits.
- Thermal Stability: With a high glass transition temperature (Tg), ISOLA P96/P26 can withstand elevated temperatures during both the manufacturing process and in operational environments. This thermal robustness helps maintain the integrity and performance of the PCB over time, even under harsh conditions.
- Low Coefficient of Thermal Expansion (CTE): The substrate’s low CTE minimizes thermal stress and reduces the risk of delamination and warping during thermal cycling. This property is essential for maintaining dimensional stability and reliability in environments with fluctuating temperatures.
- Excellent Mechanical Strength: ISOLA P96/P26 provides good mechanical support, which enhances the durability of the PCB. This mechanical strength is important for ensuring that the substrate can withstand physical stresses during handling and operation.
- High Dielectric Strength: The substrate’s high dielectric strength contributes to its ability to withstand high voltages and prevent electrical breakdown. This characteristic is particularly beneficial in high-power and high-voltage applications.
- Good Chemical Resistance: ISOLA P96/P26 is resistant to various chemicals, which helps protect the substrate from degradation in harsh chemical environments. This property is important for maintaining the performance and longevity of the PCB.
- Enhanced Signal Integrity: The substrate’s properties help maintain signal integrity by reducing signal degradation and electromagnetic interference (EMI). This is critical for ensuring accurate and reliable performance in high-speed and high-frequency circuits.
- Reliability in Harsh Conditions: The combination of high thermal stability, low CTE, and good chemical resistance makes ISOLA P96/P26 well-suited for applications in harsh environments, including aerospace, automotive, and industrial sectors.
Overall, ISOLA P96/P26 substrates offer a blend of high electrical performance, thermal stability, and mechanical durability, making them a preferred choice for advanced and demanding PCB applications.
What is the ISOLA P96/P26 Substrate Fabrication Process?
The fabrication process for ISOLA P96/P26 substrates involves several key steps to ensure high-quality and reliable printed circuit boards (PCBs). Here’s an overview of the typical fabrication process:
- Material Preparation: Start with ISOLA P96/P26 prepreg sheets and copper foils. The prepreg, a composite of resin and reinforcing fibers, is crucial for the laminate structure. Copper foils are used for the conductive layers.
- Lamination: The prepreg sheets and copper foils are stacked according to the desired PCB layer configuration. This stack is then placed in a laminating press where heat and pressure are applied to bond the layers together. The process solidifies the resin, creating a solid laminate with the copper layers embedded.
- Drilling: Once laminated, the PCB is drilled to create holes for through-hole components and vias. Precision drilling is essential to ensure that the holes align correctly with the intended design and that the substrate’s integrity is maintained.
- Copper Plating: The drilled PCB is subjected to an electroplating process to deposit a thin layer of copper on the walls of the holes. This step is necessary to create electrical connections between different layers of the PCB.
- Etching: The next step involves applying a photosensitive resist to the surface of the PCB. The PCB is then exposed to UV light through a photomask, which hardens the resist in specific areas. The unexposed resist is removed, and the exposed copper is etched away using a chemical solution, leaving behind the desired circuit pattern.
- Surface Finish: The PCB undergoes a surface finishing process to improve solderability and protect the copper traces. Common finishes include HASL (Hot Air Solder Leveling), ENIG (Electroless Nickel Immersion Gold), or OSP (Organic Solderability Preservative).
- Testing and Inspection:The fabricated PCB is subjected to various testing and inspection procedures. This includes electrical testing to verify circuit integrity and visual inspections to check for any defects or inconsistencies.
- Assembly: Once the substrate is tested and verified, components are assembled onto the PCB using techniques such as soldering or adhesive bonding. The assembly process includes component placement, soldering, and final inspection.
- Final Testing: The assembled PCB undergoes final testing to ensure that all components are correctly placed and functioning as intended. This may include functional tests, performance evaluations, and quality checks.
- Packaging: Finally, the completed PCBs are packaged and prepared for shipment to customers or further integration into electronic devices.
Each step in the fabrication process is carefully controlled to ensure the high performance and reliability of ISOLA P96/P26 substrates, making them suitable for advanced and high-demand applications.
The application of ceramic ISOLA P96/P26 Substrate
The ISOLA P96/P26 substrate, while primarily known as a high-performance laminate material, is also used in various advanced electronic applications due to its superior properties. Here’s an overview of its applications:
- High-Frequency Circuits: ISOLA P96/P26’s low dielectric constant (Dk) and low dissipation factor (Df) make it ideal for high-frequency and high-speed digital circuits. It is used in RF (radio frequency) and microwave applications where maintaining signal integrity is crucial.
- Telecommunications: In telecommunications equipment, ISOLA P96/P26 substrates are employed to ensure reliable performance in signal transmission and data communication systems. The substrate’s excellent electrical properties help to reduce signal loss and interference.
- Aerospace: The substrate’s high thermal stability and low coefficient of thermal expansion (CTE) make it suitable for aerospace applications. It is used in satellite and avionics systems where reliability and performance under extreme conditions are required.
- Automotive Electronics: In the automotive industry, ISOLA P96/P26 substrates are used in high-performance electronics such as engine control units (ECUs) and advanced driver assistance systems (ADAS). The substrate’s durability and thermal stability ensure reliable operation in harsh automotive environments.
- Medical Devices: The high-performance characteristics of ISOLA P96/P26 are beneficial in medical electronics, including imaging systems and diagnostic equipment. Its stability and reliability contribute to accurate and consistent performance in critical medical applications.
- Military and Defense: The substrate’s robust properties make it suitable for military and defense electronics, where high performance and reliability are required in challenging environments. It is used in communication systems, radar, and other defense-related technologies.
- Consumer Electronics: In high-end consumer electronics, such as high-definition displays and advanced computing devices, ISOLA P96/P26 substrates help achieve optimal performance and signal integrity. Its use in these applications ensures high-quality and reliable electronics.
- High-Power Applications: The substrate’s thermal management capabilities make it suitable for high-power electronic applications where heat dissipation is a concern. It is used in power amplifiers and other high-power devices to ensure effective heat management and reliability.
Overall, ISOLA P96/P26 substrates are valued for their advanced electrical performance, thermal stability, and mechanical strength, making them suitable for a wide range of demanding applications across various industries.
FAQs about ISOLA P96/P26 Substrate
What are the key properties of ISOLA P96/P26?
Key properties include a dielectric constant (Dk) of around 3.8, a low dissipation factor (Df), high glass transition temperature (Tg), and low coefficient of thermal expansion (CTE). These properties contribute to its excellent electrical performance and thermal stability.
What applications are suitable for ISOLA P96/P26?
It is suitable for high-frequency circuits, telecommunications equipment, aerospace, automotive electronics, medical devices, military and defense applications, consumer electronics, and high-power applications.
What are the advantages of using ISOLA P96/P26?
Advantages include high electrical performance, thermal stability, low CTE, good mechanical strength, high dielectric strength, and chemical resistance. These features ensure reliable performance in demanding environments.
What is the fabrication process for ISOLA P96/P26?
The fabrication process involves material preparation, lamination, drilling, copper plating, etching, surface finishing, testing and inspection, assembly, and final testing.
How does ISOLA P96/P26 compare to other substrates?
Compared to other substrates, ISOLA P96/P26 offers superior electrical performance and thermal stability, making it a preferred choice for high-frequency and high-speed applications where precision and reliability are critical.
What should be considered when designing with ISOLA P96/P26?
Considerations include ensuring proper layer stackup, managing thermal expansion, controlling impedance, following manufacturing guidelines, and incorporating appropriate shielding and grounding techniques.