ISOLA I-TERA® MT40 Substrate Manufacturer
ISOLA I-TERA® MT40 Substrate Manufacturer,The ISOLA I-TERA® MT40 substrate is a high-performance material designed for advanced printed circuit board (PCB) applications. It features excellent electrical performance with a low dielectric constant and low loss tangent, making it ideal for high-frequency and high-speed digital designs. The substrate’s superior thermal stability ensures reliable operation under extreme conditions. With its robust mechanical properties, I-TERA® MT40 supports complex multilayer designs and provides high signal integrity. This material is particularly well-suited for telecommunications, aerospace, and automotive applications where performance and reliability are crucial.
What is ISOLA I-TERA® MT40 Substrate?
The ISOLA I-TERA® MT40 is a high-performance laminate material designed specifically for advanced PCB applications. It is a key product in the family of ISOLA’s I-TERA® series, which focuses on delivering superior performance for high-speed and high-frequency circuit boards. The MT40 variant is particularly notable for its exceptional electrical and thermal properties.
The I-TERA® MT40 substrate is composed of a modified epoxy resin system combined with ceramic fillers, which enhances its thermal stability and electrical performance. This material is engineered to support high-speed digital designs and RF applications, making it suitable for use in data centers, telecommunications, and other high-frequency environments. Its low dielectric loss and stable dielectric constant contribute to reduced signal attenuation and crosstalk, ensuring reliable signal transmission at high speeds.
In addition to its excellent electrical properties, the I-TERA® MT40 substrate offers enhanced thermal management capabilities. It has a low coefficient of thermal expansion (CTE), which helps in maintaining dimensional stability during thermal cycling. This characteristic is crucial for preventing mechanical stress and potential damage to the circuit board under varying temperature conditions.
The I-TERA® MT40 also meets stringent industry standards for flame retardancy and chemical resistance, making it a robust choice for demanding applications. Its performance attributes make it a valuable option for designers looking to push the boundaries of high-speed and high-frequency PCB technology while maintaining reliability and durability.
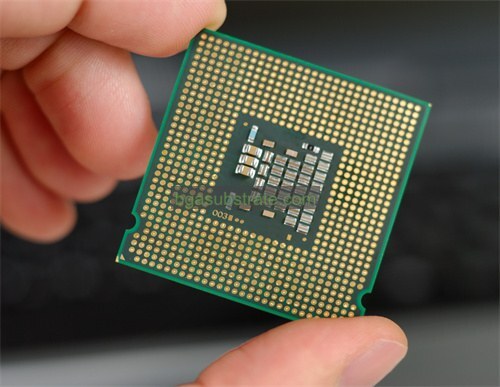
ISOLA I-TERA® MT40 Substrate Manufacturer
What is the ISOLA I-TERA® MT40 Substrate Design Guidelines?
Designing with the ISOLA I-TERA® MT40 substrate requires careful consideration of several guidelines to maximize its performance and ensure reliability. Here are key design guidelines for working with this high-performance laminate material:
- Signal Integrity: Due to its low dielectric loss and stable dielectric constant, the I-TERA® MT40 is well-suited for high-speed and high-frequency applications. Ensure that trace widths, spacing, and impedance are designed to match the specific signal requirements to minimize signal loss and crosstalk. Utilize controlled impedance design techniques to maintain signal integrity.
- Thermal Management: The I-TERA® MT40 substrate offers excellent thermal stability with a low coefficient of thermal expansion (CTE). To leverage this property, design for adequate heat dissipation, especially in high-power applications. Include sufficient thermal vias and heat sinks to manage heat effectively and prevent thermal stress.
- Mechanical Considerations: Given its low CTE, the substrate maintains dimensional stability under thermal cycling. However, ensure that the PCB design accommodates potential mechanical stresses due to thermal expansion and contraction. Use appropriate mounting and support techniques to maintain mechanical integrity.
- Layer Stack-Up: For optimal performance, carefully plan the layer stack-up to balance electrical and thermal properties. Consider the impact of layer arrangement on impedance and signal propagation. Properly align layers to prevent signal degradation and ensure consistent performance.
- Manufacturing Tolerances: The ISOLA I-TERA® MT40 substrate is precision-engineered, but adhering to specified manufacturing tolerances is crucial. Follow the substrate supplier’s recommendations for trace widths, spacing, and hole sizes to ensure compatibility and reliability.
- Environmental Considerations:Ensure the design adheres to industry standards for flame retardancy and chemical resistance. The I-TERA® MT40 meets high standards, but additional protective measures may be necessary for specific environmental conditions.
- Testing and Validation: Conduct thorough testing and validation of the PCB design, including signal integrity, thermal performance, and mechanical robustness. This ensures that the final product performs reliably under intended operating conditions.
By following these design guidelines, you can effectively utilize the ISOLA I-TERA® MT40 substrate to achieve high-performance and reliable results in demanding electronic applications.
The advantages of ISOLA I-TERA® MT40 Substrate
The ISOLA I-TERA® MT40 substrate offers several significant advantages, making it a preferred choice for high-performance and high-frequency applications:
- Low Dielectric Loss: The I-TERA® MT40 features a low dielectric loss tangent, which minimizes signal attenuation and improves overall signal integrity. This is particularly beneficial for high-speed digital and RF applications where maintaining signal quality is crucial.
- Stable Dielectric Constant: The substrate maintains a stable dielectric constant over a wide frequency range, ensuring consistent performance and reliable signal propagation. This stability helps to reduce signal distortion and crosstalk in high-frequency designs.
- Thermal Stability: With a low coefficient of thermal expansion (CTE), the I-TERA® MT40 exhibits excellent thermal stability. This property helps prevent dimensional changes and mechanical stress during thermal cycling, contributing to the durability and reliability of the PCB.
- High Thermal Conductivity: The substrate’s thermal management capabilities are enhanced by its high thermal conductivity. This allows for efficient heat dissipation, reducing the risk of overheating and improving the overall thermal performance of the electronic device.
- Chemical and Flame Retardancy: The I-TERA® MT40 meets stringent industry standards for chemical resistance and flame retardancy. This ensures the substrate can withstand harsh environments and high-temperature conditions, enhancing the safety and longevity of the PCB.
- Reduced Signal Interference: Due to its excellent electrical properties, the I-TERA® MT40 effectively reduces signal interference and crosstalk. This is crucial for maintaining high signal integrity in complex circuit designs.
- Design Flexibility: The substrate offers flexibility in design, accommodating various layer stack-ups and configurations. This versatility allows engineers to optimize their designs for performance and manufacturability.
- Reliability: The combination of low dielectric loss, stable dielectric constant, and thermal stability ensures that the I-TERA® MT40 substrate provides reliable performance over its operational life, even under demanding conditions.
These advantages make the ISOLA I-TERA® MT40 substrate an excellent choice for advanced electronics applications, including data centers, telecommunications, and high-frequency RF systems.
What is the ISOLA I-TERA® MT40 Substrate Fabrication Process?
The fabrication process for ISOLA I-TERA® MT40 substrate involves several key steps to ensure the production of high-quality, high-performance PCBs. Here is an overview of the typical fabrication process:
- Material Preparation: The process begins with the preparation of the ISOLA I-TERA® MT40 laminate material. This involves selecting and combining the resin system with ceramic fillers to create the substrate material with desired electrical and thermal properties.
- Layer Processing: The laminate material is processed into thin sheets or layers. These layers are then cut to the required dimensions for the PCB design. Each layer is carefully inspected for defects to ensure consistency and quality.
- Layer Alignment and Lamination: The individual layers are stacked and aligned according to the PCB design specifications. This stack is then subjected to a lamination process where heat and pressure are applied to bond the layers together. The lamination process ensures that the layers adhere properly and achieve the required thickness and dimensional stability.
- Drilling and Routing:Once laminated, the PCB is drilled to create vias, holes, and other necessary openings. Precision drilling equipment is used to ensure accurate placement and size of these features. After drilling, the PCB is routed to shape the board according to the design.
- Copper Deposition and Patterning: A thin layer of copper is deposited onto the substrate through a process such as electroplating or sputtering. This copper layer is then patterned using photolithography or laser etching to form the circuit traces and other conductive features on the PCB.
- Etching:Excess copper that is not part of the circuit pattern is removed through an etching process. This step ensures that only the desired copper traces remain on the PCB.
- Surface Finishing: The PCB undergoes surface finishing treatments to protect the copper traces and enhance solderability. Common finishes include HASL (Hot Air Solder Leveling), ENIG (Electroless Nickel Immersion Gold), or other plating methods.
- Inspection and Testing: The fabricated PCB is thoroughly inspected for defects, including visual inspection and electrical testing. Automated optical inspection (AOI) and functional testing are often used to ensure that the board meets all design specifications and performance criteria.
- Final Processing: Additional steps, such as applying solder mask and silkscreen layers, are completed as per the design requirements. The solder mask provides insulation for non-copper areas, while the silkscreen layer adds text and markings.
- Cutting and Packaging: The finished PCBs are cut from the production panel and packaged for shipment. Each board is carefully handled to prevent damage and ensure it arrives in optimal condition.
The fabrication process for ISOLA I-TERA® MT40 substrate is designed to maintain the high performance and reliability of the material, ensuring it meets the rigorous demands of advanced electronic applications.
The application of ceramic ISOLA I-TERA® MT40 Substrate
The ISOLA I-TERA® MT40 substrate, known for its high-performance characteristics, is used in a variety of advanced electronic applications. Here are some key applications where the ceramic ISOLA I-TERA® MT40 substrate excels:
- High-Speed Digital Circuits: The low dielectric loss and stable dielectric constant of the I-TERA® MT40 make it ideal for high-speed digital applications. It is used in data centers, server boards, and networking equipment where fast and reliable signal transmission is crucial.
- Telecommunications: The substrate’s excellent electrical properties and thermal management capabilities make it suitable for telecommunications infrastructure, including base stations and communication modules. It helps ensure high-frequency signal integrity and reduces interference.
- RF and Microwave Applications: The I-TERA® MT40’s low dielectric loss and high thermal conductivity are beneficial for RF and microwave circuits. It is used in applications such as radar systems, satellite communications, and RF front-ends where high-frequency performance is essential.
- Automotive Electronics: In the automotive industry, the substrate’s thermal stability and durability make it suitable for high-performance automotive electronics. It is used in advanced driver-assistance systems (ADAS), infotainment systems, and power management modules.
- Medical Devices: The substrate’s reliability and thermal management properties are advantageous for medical devices that require precise and stable performance. It is used in diagnostic equipment, imaging systems, and other high-performance medical electronics.
- Aerospace and Defense: The I-TERA® MT40 is utilized in aerospace and defense applications where high-speed, high-frequency, and reliable performance are critical. It is used in avionics systems, military communication devices, and satellite technology.
- Power Electronics: The substrate’s high thermal conductivity supports efficient heat dissipation in power electronics. It is used in power management circuits, inverters, and converters where thermal stability is essential for reliable operation.
- Consumer Electronics: The I-TERA® MT40 is also applied in high-performance consumer electronics such as gaming devices, high-definition displays, and smart devices. Its properties help improve signal quality and device performance.
These applications leverage the ISOLA I-TERA® MT40 substrate’s superior electrical and thermal properties to enhance performance and reliability across a range of high-demand environments.
FAQs about ISOLA I-TERA® MT40 Substrate
What are the key benefits of using I-TERA® MT40?
Key benefits include low dielectric loss for high-speed signal integrity, stable dielectric constant for reduced signal distortion, high thermal conductivity for efficient heat dissipation, and excellent thermal stability.
In what types of applications is I-TERA® MT40 used?
It is used in high-speed digital circuits, telecommunications, RF and microwave applications, automotive electronics, medical devices, aerospace and defense, power electronics, and consumer electronics.
What makes I-TERA® MT40 suitable for high-speed and high-frequency applications?
Its low dielectric loss and stable dielectric constant help maintain signal integrity and reduce interference, making it ideal for high-speed and high-frequency circuits.
How does I-TERA® MT40 handle heat?
The substrate has high thermal conductivity and a low coefficient of thermal expansion (CTE), which helps in effective heat dissipation and maintains dimensional stability during thermal cycling.
What are the main fabrication steps for I-TERA® MT40 substrates?
The main steps include material preparation, layer processing, lamination, drilling and routing, copper deposition and patterning, etching, surface finishing, and final testing and inspection.
Is I-TERA® MT40 resistant to environmental factors?
Yes, it meets industry standards for chemical resistance and flame retardancy, making it suitable for harsh environments and high-temperature applications.