ISOLA FR406N Substrate Manufacturer
ISOLA FR406N Substrate Manufacturer,ISOLA FR406N is a high-performance substrate material designed for a range of demanding PCB applications. It features excellent electrical properties, including a low dielectric constant and low dissipation factor, which ensure superior signal integrity and reduced signal loss. The substrate provides exceptional thermal stability and mechanical durability, making it suitable for complex, high-layer-count circuit boards. FR406N is also known for its resistance to thermal cycling and high temperatures, enhancing reliability in challenging environments. Ideal for use in telecommunications, automotive, and high-speed digital systems, ISOLA FR406N combines robust performance with durability, making it a reliable choice for advanced electronic applications.
What is ISOLA FR406N Substrate?
ISOLA FR406N is a high-performance laminate substrate specifically designed for use in advanced printed circuit boards (PCBs). This material is part of the FR-4 family, but it offers enhanced properties compared to standard FR-4 substrates, making it suitable for high-frequency and high-speed electronic applications.
FR406N is known for its superior electrical performance, particularly in terms of its dielectric constant and loss tangent, which are critical for minimizing signal loss and maintaining signal integrity at high frequencies. This substrate is made from a woven glass fabric impregnated with an epoxy resin system, which provides excellent mechanical strength and durability. The “N” in FR406N typically signifies specific enhancements in the material’s formulation that improve its thermal and electrical properties.
One of the key features of FR406N is its low Coefficient of Thermal Expansion (CTE), which helps to ensure that the PCB maintains dimensional stability under varying temperature conditions. This is crucial for preventing warping or delamination that can affect the reliability and performance of electronic devices. Additionally, FR406N substrates are designed to withstand the rigorous demands of high-speed digital and RF (radio frequency) applications, making them a preferred choice for sophisticated electronic systems.
In summary, ISOLA FR406N is a specialized laminate material that offers advanced performance characteristics for high-frequency and high-speed PCB applications. Its improved electrical properties, low CTE, and enhanced durability make it a valuable choice for modern electronics requiring high reliability and precision.
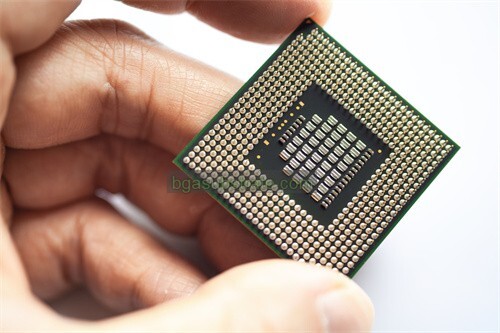
ISOLA FR406N Substrate Manufacturer
What is the ISOLA FR406N Substrate Design Guidelines?
When designing PCBs using ISOLA FR406N substrate, following specific design guidelines is crucial to ensure optimal performance and reliability. Here are key design guidelines for working with FR406N:
- Impedance Control: FR406N provides excellent electrical performance, but achieving precise impedance control is essential for high-speed and high-frequency applications. Ensure that trace widths and spacing are carefully calculated according to impedance requirements. Utilize simulation tools to validate impedance and signal integrity.
- Layer Stack-Up: The layer stack-up should be designed to minimize signal loss and interference. Incorporate appropriate grounding and power planes to provide a solid reference and reduce noise. Consider the dielectric thickness and the number of layers required to achieve desired electrical performance.
- Thermal Management: FR406N has a low Coefficient of Thermal Expansion (CTE), but thermal management remains critical. Ensure that heat-sensitive components are properly placed and consider using thermal vias or heat sinks to dissipate heat effectively.
- Hole Sizes and Plating: When designing vias and through-holes, adhere to the recommended hole sizes and plating specifications to ensure reliable electrical connections. Proper plating thickness is necessary to avoid issues with conductivity and mechanical strength.
- Signal Routing: For high-speed signals, maintain short trace lengths and avoid sharp corners that can introduce signal reflections or distortions. Use controlled impedance traces and differential pairs where necessary to maintain signal integrity.
- Manufacturing Tolerances: Ensure that the design adheres to the manufacturing tolerances specified for FR406N. This includes trace widths, spacing, and hole dimensions. Work closely with the PCB manufacturer to confirm that the design can be produced within the required specifications.
- Testing and Validation: After fabrication, perform thorough testing and validation of the PCB to confirm that it meets electrical and mechanical performance requirements. This may include impedance testing, thermal cycling tests, and reliability assessments.
By adhering to these guidelines, you can leverage the advanced properties of ISOLA FR406N to create high-performance PCBs suitable for demanding applications.
The advantages of ISOLA FR406N Substrate
ISOLA FR406N substrate offers several advantages that make it a preferred choice for high-performance printed circuit boards (PCBs). Here are the key benefits:
- High Electrical Performance: FR406N features a low dielectric constant (Dk) and low loss tangent (Df), which are crucial for maintaining signal integrity in high-speed and high-frequency applications. These properties help to reduce signal loss, crosstalk, and delay, ensuring reliable performance in demanding electronic systems.
- Low Coefficient of Thermal Expansion (CTE): The substrate’s low CTE helps to ensure dimensional stability under varying temperature conditions. This minimizes the risk of warping or delamination, which can negatively impact the reliability and functionality of the PCB.
- Enhanced Mechanical Strength: FR406N is designed with a robust epoxy resin system and woven glass fabric, providing excellent mechanical strength and durability. This makes it suitable for applications where physical robustness is critical, including rugged environments and high-stress conditions.
- Thermal Stability: The substrate is capable of withstanding high temperatures without significant degradation in performance. This thermal stability is essential for components that generate heat or are subjected to elevated temperatures during operation.
- Compatibility with Advanced Manufacturing Processes: FR406N is compatible with advanced PCB manufacturing processes, including fine line/space technologies and high-density interconnects (HDI). This versatility allows for the production of complex and high-performance circuit boards.
- Reliability in Harsh Environments: The material’s properties make it suitable for use in harsh or challenging environments, such as automotive, aerospace, and telecommunications applications, where reliability and durability are paramount.
- Reduced Signal Interference: The excellent electrical characteristics of FR406N help to minimize signal interference and noise, which is crucial for maintaining the performance and accuracy of high-speed digital and RF signals.
In summary, ISOLA FR406N substrate offers high electrical performance, mechanical strength, thermal stability, and reliability, making it an ideal choice for advanced PCBs in demanding applications.
What is the ISOLA FR406N Substrate Fabrication Process?
The fabrication process for ISOLA FR406N substrate involves several key steps to ensure high-quality printed circuit boards (PCBs) that meet performance and reliability standards. Here’s an overview of the typical fabrication process for FR406N:
- Material Preparation: The FR406N substrate starts with a base laminate material consisting of woven glass fabric impregnated with an epoxy resin. The resin is formulated to enhance the electrical and thermal properties of the substrate.
- Copper Cladding: The laminate is then coated with a thin layer of copper on one or both sides. This copper layer is used to create the circuit traces and pads. The copper cladding is typically applied through a lamination process that bonds the copper foil to the epoxy resin.
- Layering and Lamination: For multi-layer PCBs, additional layers of FR406N laminate are stacked with copper layers in between. The stack is then subjected to a lamination process, where heat and pressure are applied to bond the layers together, forming a solid, integrated substrate.
- Drilling and Via Formation: Holes are drilled into the substrate to create vias and through-holes for electrical connections between different layers. The drilling process must be precise to ensure proper alignment and functionality.
- Copper Plating: After drilling, the holes are plated with copper to establish electrical connections between the layers. This process involves depositing a thin layer of copper onto the walls of the drilled holes through an electroplating process.
- Etching: The substrate undergoes an etching process to remove unwanted copper and define the circuit traces. This involves applying a photoresist layer, exposing it to light through a mask, and then etching away the exposed copper to create the desired circuit pattern.
- Lamination of Solder Mask:A solder mask is applied to the surface of the PCB to protect the copper traces and prevent solder bridges during assembly. The solder mask is typically a polymer coating that is cured using UV light.
- Silkscreen Printing: Text and other identifying marks are added to the PCB using a silkscreen printing process. This involves applying ink to specific areas of the PCB to indicate component placement, test points, and other relevant information.
- Final Inspection and Testing: The fabricated PCBs undergo thorough inspection and testing to ensure they meet electrical and mechanical specifications. This may include visual inspection, electrical testing, and functional testing to verify performance and reliability.
- Cutting and Routing: Finally, the PCBs are cut and routed to the required size and shape. This involves separating individual boards from larger panels and machining any necessary cutouts or slots.
The ISOLA FR406N substrate fabrication process combines advanced material handling with precise manufacturing techniques to produce high-quality, high-performance PCBs suitable for demanding applications.
The application of ceramic ISOLA FR406N Substrate
The ISOLA FR406N substrate is primarily an epoxy-based laminate material, not a ceramic substrate. However, for comparison and context, here’s an overview of how ceramic substrates, including those used in high-performance applications, are applied:
- High-Frequency and High-Speed Electronics: Ceramic substrates, including advanced materials like AlN (Aluminum Nitride) and SiN (Silicon Nitride), are widely used in high-frequency and high-speed electronic applications. They offer superior electrical performance with low dielectric losses, making them suitable for RF and microwave circuits where signal integrity is crucial.
- Power Electronics: In power electronics, ceramic substrates are used for their excellent thermal conductivity. They help in efficient heat dissipation from high-power components, which is essential for maintaining reliability and performance in power conversion systems, such as inverters and power amplifiers.
- Automotive Electronics:Ceramic substrates are employed in automotive electronics due to their durability and resistance to high temperatures and harsh environments. They are used in applications such as ignition systems, engine control units, and sensors, where reliability and performance are critical.
- Aerospace and Defense: In aerospace and defense sectors, ceramic substrates are used for their high thermal stability and mechanical strength. They are applied in high-reliability applications such as radar systems, satellite communications, and other critical electronic systems that require robust performance under extreme conditions.
- Medical Devices: Ceramic substrates are also found in medical devices where biocompatibility and reliability are required. They are used in applications such as implantable devices and diagnostic equipment, where both electrical performance and material safety are crucial.
- LED Lighting: In LED lighting systems, ceramic substrates provide excellent thermal management, which is important for the longevity and efficiency of LEDs. They help dissipate heat generated by the LED chips, enhancing their performance and lifespan.
- Telecommunications: Ceramic substrates are used in telecommunications equipment, including base stations and network infrastructure, for their high dielectric constants and low signal attenuation. They ensure reliable signal transmission and reception in communication systems.
While FR406N is not a ceramic material, it is used in various high-performance PCB applications where its properties, such as low dielectric loss and mechanical durability, are beneficial. For ceramic substrates, their application spans across multiple industries where high thermal conductivity, electrical performance, and mechanical strength are essential.
FAQs about ISOLA FR406N Substrate
What is ISOLA FR406N?
ISOLA FR406N is a high-performance laminate material used for printed circuit boards (PCBs). It is part of the FR-4 family but offers enhanced electrical and thermal properties, making it suitable for high-frequency and high-speed applications.
What are the key properties of FR406N?
Key properties of FR406N include a low dielectric constant (Dk), low loss tangent (Df), and a low Coefficient of Thermal Expansion (CTE). These features contribute to excellent signal integrity, minimal signal loss, and dimensional stability under temperature variations.
What applications are suitable for FR406N?
FR406N is ideal for high-speed and high-frequency electronics, including RF and microwave circuits, power electronics, automotive systems, aerospace applications, and telecommunications equipment.
How does FR406N compare to standard FR-4 substrates?
FR406N offers superior electrical performance, including lower dielectric loss and better impedance control, compared to standard FR-4 substrates. It also has a lower CTE, providing better thermal stability and reliability in demanding applications.
What is the fabrication process for FR406N?
The fabrication process for FR406N involves material preparation, copper cladding, layering and lamination, drilling and via formation, copper plating, etching, solder mask application, silkscreen printing, and final inspection and testing.
Is FR406N compatible with advanced manufacturing processes?
Yes, FR406N is compatible with advanced PCB manufacturing processes, including fine line/space technologies and high-density interconnects (HDI).