IsoClad® 933 Substrate Manufacturer
IsoClad® 933 Substrate Manufacturer,IsoClad® 933 is a high-performance substrate known for its superior thermal and electrical properties. Engineered for demanding applications, this substrate offers exceptional thermal conductivity, ensuring efficient heat dissipation. Its low dielectric constant and loss tangent contribute to excellent signal integrity, making it ideal for high-frequency and high-speed applications. IsoClad® 933 is designed to provide reliability and durability in various electronic components, enhancing overall performance and longevity. With its advanced material composition, it stands out in the industry for applications requiring robust thermal management and precise electrical performance.
What is IsoClad® 933 Substrate?
IsoClad® 933 is a specialized substrate material designed for high-performance electronic applications. It is part of the IsoClad® family, which is known for its advanced thermal and electrical properties. IsoClad® 933 is typically used in environments that require superior thermal management and electrical insulation.
The substrate is composed of a ceramic material that combines high thermal conductivity with excellent electrical insulation properties. This makes it suitable for use in applications where efficient heat dissipation and reliable electrical performance are critical, such as in power electronics, RF (radio frequency) applications, and high-frequency circuits.
One of the key features of IsoClad® 933 is its ability to withstand high temperatures without degrading its performance. This is essential in many modern electronic devices where temperature fluctuations can impact the reliability and longevity of components. Additionally, IsoClad® 933 provides a stable platform for the mounting of electronic components, ensuring that connections remain reliable under thermal stress.
The substrate’s composition and manufacturing process are optimized to provide a balance between thermal conductivity and electrical insulation, making it an ideal choice for applications where both attributes are crucial. This material is also engineered to offer durability and resistance to mechanical stress, further enhancing its performance in demanding environments.
In summary, IsoClad® 933 is a high-performance substrate designed to meet the rigorous demands of advanced electronic applications, providing excellent thermal management, electrical insulation, and mechanical stability.
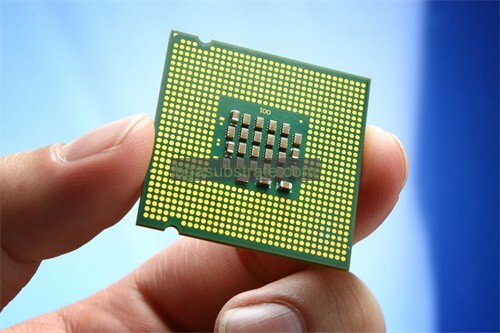
IsoClad® 933 Substrate Manufacturer
What is the IsoClad® 933 Substrate Design Guidelines?
When designing with IsoClad® 933 substrates, several key guidelines should be followed to ensure optimal performance and reliability:
- Thermal Management:IsoClad® 933 offers excellent thermal conductivity, making it crucial to design your layout to maximize heat dissipation. Ensure that heat-sensitive components are placed away from high-heat areas and use adequate heat sinks or thermal vias to manage heat flow effectively.
- Electrical Isolation:The substrate provides superior electrical insulation. Maintain appropriate spacing between conductive traces and components to prevent unintended electrical interference. Follow industry-standard guidelines for clearance and creepage distances based on the operating voltage and environmental conditions.
- Mechanical Stability:IsoClad® 933 is designed to withstand mechanical stress. However, it’s important to consider the mechanical design of the assembly. Ensure that the substrate is properly mounted and supported to avoid stress concentrations that could lead to cracking or other damage.
- Layer Stack-Up:When designing multilayer circuits, carefully plan the stack-up of layers to optimize both thermal and electrical performance. Properly align and bond the layers to maintain uniformity and integrity throughout the substrate.
- Manufacturing Tolerances:Account for manufacturing tolerances and ensure that your design accommodates these variations. This includes allowing for proper spacing around vias, pads, and other features to avoid issues during the fabrication and assembly processes.
- Environmental Considerations:Evaluate the operating environment of the device. IsoClad® 933 is suitable for high-temperature applications, but additional considerations may be needed for extreme environmental conditions such as high humidity or corrosive environments.
- Design for Reliability:Implement design practices that enhance reliability, such as using redundant traces, reinforced vias, and thermal reliefs. Conduct thorough testing and validation to ensure that the design meets all performance and reliability requirements.
By adhering to these design guidelines, you can leverage the advantages of IsoClad® 933 substrates to create high-performance electronic devices with excellent thermal management, electrical insulation, and mechanical stability.
The advantages of IsoClad® 933 Substrate
- High Thermal Conductivity:IsoClad® 933 provides exceptional thermal management, allowing efficient heat dissipation from heat-generating components. This capability helps to maintain optimal operating temperatures and enhances the reliability and longevity of electronic devices.
- Superior Electrical Insulation:The substrate offers excellent electrical insulation properties, which helps in preventing electrical interference and maintaining signal integrity. This is crucial for high-frequency and power electronics applications where signal quality and performance are paramount.
- Temperature Stability:IsoClad® 933 is designed to withstand high temperatures without compromising its performance. It maintains its structural integrity and electrical properties even under extreme thermal conditions, making it suitable for high-temperature applications.
- Mechanical Durability:The substrate is engineered for mechanical stability, providing resistance to physical stress and vibration. This durability helps in maintaining the reliability of the electronic assembly, reducing the risk of mechanical failure or damage.
- Enhanced Reliability:By combining high thermal conductivity with superior electrical insulation and mechanical stability, IsoClad® 933 enhances the overall reliability of electronic devices. It ensures consistent performance and minimizes the risk of thermal and electrical issues.
- Design Flexibility:IsoClad® 933 supports a wide range of design requirements, including complex geometries and multilayer configurations. Its flexibility allows for customization to meet specific application needs and integration into various electronic systems.
- Reduced Thermal Expansion Issues:The substrate is designed to minimize the effects of thermal expansion, which helps in maintaining the alignment and integrity of components during temperature fluctuations. This contributes to the longevity and reliability of the device.
- High-Performance Applications: IsoClad® 933 is well-suited for demanding applications such as power electronics, RF circuits, and high-frequency designs. Its advanced properties enable it to perform effectively in environments that require both high thermal and electrical performance.
Overall, IsoClad® 933 substrates offer a combination of high thermal conductivity, excellent electrical insulation, mechanical durability, and design flexibility, making them ideal for high-performance electronic applications.
What is the IsoClad® 933 Substrate Fabrication Process?
The fabrication of IsoClad® 933 substrates involves several critical steps to ensure high performance and reliability. The process typically includes:
- Material Preparation:The process begins with selecting and preparing the raw materials for IsoClad® 933. This involves sourcing high-quality ceramic materials that offer the desired thermal and electrical properties. The raw materials are meticulously processed to achieve the required specifications.
- Ceramic Substrate Formation:The prepared ceramic materials are then formed into substrate shapes. This is often done through techniques such as pressing, casting, or extrusion, depending on the specific requirements of the substrate design. The substrate is initially in a green state, which means it is still unfired and relatively soft.
- Sintering:The green substrates are subjected to a sintering process, where they are heated to high temperatures in a controlled atmosphere. Sintering causes the ceramic particles to fuse together, enhancing the substrate’s mechanical strength and thermal conductivity. The sintering temperature and time are carefully controlled to achieve the desired material properties.
- Lamination and Bonding:For multilayer substrates, additional layers are bonded to the base layer. This involves applying bonding materials and using lamination techniques to fuse the layers together. The bonding process must ensure that the layers adhere well and that the final structure maintains uniformity and performance.
- Metallization:After the basic substrate structure is formed, metallization is performed to add conductive traces and pads. This step typically involves deposition techniques such as sputtering, evaporation, or plating to apply metal layers onto the substrate. These metal layers are patterned to create the required circuit features.
- Patterning and Etching:The metallized layers are then patterned using photolithography and etching processes. This involves applying a photosensitive resist, exposing it to light through a mask, and then etching away the exposed metal to create the desired circuit patterns.
- Drilling and Vias:Holes and vias are drilled into the substrate to allow electrical connections between different layers or components. The drilling process must be precise to avoid damaging the substrate or misaligning the vias.
- Final Inspection and Testing:Once fabrication is complete, the substrates undergo rigorous inspection and testing to ensure they meet quality standards. This includes checking for defects, verifying electrical performance, and conducting thermal and mechanical tests.
- Packaging and Delivery:After passing inspection, the substrates are packaged and prepared for delivery. Proper packaging is essential to protect the substrates during transportation and handling.
The IsoClad® 933 fabrication process is designed to produce substrates with high thermal conductivity, excellent electrical insulation, and mechanical durability, making them suitable for demanding electronic applications.
The application of ceramic IsoClad® 933 Substrate
- Power Electronics:IsoClad® 933 substrates are extensively used in power electronics due to their excellent thermal conductivity. They help dissipate heat from power devices like transistors and diodes, which is crucial for maintaining reliable performance and extending the lifespan of these components.
- RF and Microwave Circuits:The substrate’s superior electrical insulation properties make it ideal for RF and microwave applications. It supports high-frequency signal transmission with minimal loss and interference, making it suitable for use in communication systems and radar technologies.
- High-Temperature Environments:IsoClad® 933 substrates are designed to withstand high temperatures without degradation. This makes them suitable for applications in environments with extreme thermal conditions, such as automotive electronics and industrial machinery.
- LED Lighting:In LED lighting systems, efficient heat management is essential for optimal performance and longevity. IsoClad® 933 substrates help in managing the heat generated by LEDs, ensuring consistent light output and enhancing the reliability of the lighting system.
- Power Supply Modules:The substrate’s ability to handle high power densities and its thermal stability make it a good choice for power supply modules. It ensures stable operation and reduces the risk of thermal-related failures in power conversion and distribution systems.
- Aerospace and Defense:In aerospace and defense applications, reliability under extreme conditions is critical. IsoClad® 933 substrates are used in avionics and defense electronics where high performance and durability are required in harsh environments.
- Medical Devices:For medical electronics that require precise thermal and electrical performance, IsoClad® 933 substrates provide a stable platform. They are used in various medical devices and equipment where reliability and accuracy are paramount.
- Consumer Electronics:The substrate is also used in consumer electronics where high-performance requirements are needed. It supports devices such as smartphones, tablets, and high-performance computing equipment that benefit from its thermal and electrical properties.
- High-Frequency Sensors:IsoClad® 933 is used in high-frequency sensors where it aids in maintaining accurate readings and signal integrity by providing a stable substrate that minimizes interference and signal loss.
In summary, ceramic IsoClad® 933 substrates are employed in a wide range of applications that require high thermal conductivity, excellent electrical insulation, and mechanical stability. Their versatility makes them suitable for demanding environments across various industries, including power electronics, RF and microwave circuits, high-temperature environments, and more.
FAQs about IsoClad® 933 Substrate
What is IsoClad® 933?
IsoClad® 933 is a high-performance ceramic substrate known for its excellent thermal conductivity, electrical insulation, and mechanical durability, making it suitable for demanding electronic applications.
What are the key advantages of IsoClad® 933?
Key advantages include high thermal conductivity, superior electrical insulation, temperature stability, mechanical durability, and design flexibility. These properties help in managing heat effectively and maintaining reliable performance.
What applications are suitable for IsoClad® 933?
IsoClad® 933 is used in power electronics, RF and microwave circuits, high-temperature environments, LED lighting, power supply modules, aerospace and defense, medical devices, consumer electronics, and high-frequency sensors.
How does IsoClad® 933 handle high temperatures?
IsoClad® 933 is designed to withstand high temperatures without compromising its properties, making it suitable for applications with extreme thermal conditions.
What materials are used in IsoClad® 933?
The substrate is made from advanced ceramic materials that provide high thermal conductivity and excellent electrical insulation.
Can IsoClad® 933 be used in multilayer designs?
Yes, IsoClad® 933 supports multilayer designs and can be used in complex electronic assemblies where multiple layers are required.