Glass Substrate Manufacturer
Glass Substrate Manufacturer,Glass substrates are used in advanced electronics and photonics applications, offering unique properties that make them suitable for high-precision devices. They provide excellent dimensional stability, low thermal expansion, and high optical clarity, making them ideal for use in displays, sensors, and microelectromechanical systems (MEMS). Glass substrates are also chemically resistant and can withstand high temperatures, which is crucial for manufacturing processes that involve high thermal loads. Additionally, their smooth surface and transparency make them an excellent choice for optoelectronic devices. With the capability to be processed with fine features and integrated with various thin-film technologies, glass substrates are key components in next-generation electronic and optical systems.
What is Glass Substrate?
Glass substrates are foundational materials widely used in electronic and optoelectronic devices. They are primarily made from high-purity silicate or borosilicate glass, offering excellent optical transparency, chemical stability, and mechanical strength. Due to these properties, glass substrates find applications in various high-tech fields, including display technology, optical components, and semiconductor devices.
In display technology, glass substrates are core components of liquid crystal displays (LCDs) and organic light-emitting diode (OLED) screens. Their superior optical properties ensure clear and accurate display images. Additionally, glass substrates provide robust support, protecting the electronic components inside the display.
In the optoelectronic field, glass substrates are used in the manufacture of optical sensors, lasers, and optical fibers. Their excellent transparency and low-loss characteristics enable efficient light signal transmission and processing.
In semiconductor devices, glass substrates are widely used due to their excellent insulating properties and high-temperature stability. For instance, in the manufacture of integrated circuits (ICs), glass substrates offer a stable foundation that ensures device performance and reliability.
Overall, glass substrates, with their superior physical and chemical properties, are essential materials in electronic and optoelectronic devices. As technology advances, the demands on glass substrates continue to rise, and their application areas keep expanding.
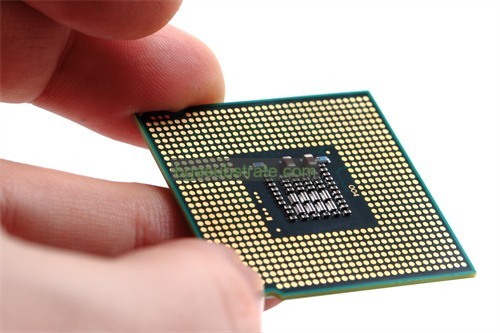
Glass Substrate Manufacturer
What is the Glass Substrate Design Guidelines?
Designing with glass substrates requires adherence to specific guidelines to ensure performance, reliability, and manufacturability. Here are key considerations for designing glass substrates:
- Thermal Expansion Matching:lass substrates have unique thermal expansion characteristics. It is crucial to match the thermal expansion coefficient of the glass with other materials used in the assembly to avoid thermal stress and warping during temperature changes.
- Thickness and Flatness:The thickness of the glass substrate should be chosen based on the application requirements. For high-precision applications, maintaining a high level of flatness is essential to ensure proper alignment and functionality of the electronic or optical components.
- Surface Quality:The surface of the glass substrate must be smooth and free of defects such as scratches, bubbles, or inclusions. Surface quality directly impacts the performance of optical devices and the adhesion of coatings or other materials.
- Edge Treatment:Proper edge treatment is necessary to prevent chipping and damage during handling and processing. Edges should be smoothly rounded or polished to reduce the risk of breakage.
- Patterning and Etching:When designing circuits or features on glass substrates, precise patterning and etching techniques are required. Ensure that the etching process does not introduce stress or compromise the structural integrity of the glass.
- Coatings and Films:Consider the type of coatings or films that will be applied to the glass substrate. These coatings should be compatible with the glass material and the intended application, such as anti-reflective coatings for optical applications or protective coatings for electronic devices.
- Handling and Assembly:Due to the brittleness of glass, careful handling and assembly practices are necessary. Use appropriate fixtures and tools to avoid mechanical stress or contamination that could affect the glass substrate.
- Environmental Considerations:Ensure that the glass substrate design can withstand the operating environment, including exposure to chemicals, moisture, and temperature extremes. Proper sealing and protective measures may be required depending on the application.
By following these design guidelines, you can optimize the performance and reliability of glass substrates in various applications, from display technologies to optical components and semiconductor devices.
The advantages of Glass Substrate
Glass substrates offer several distinct advantages that make them a preferred choice in various high-tech applications. Here are some of the key benefits:
- Excellent Optical Properties:Glass substrates provide superior optical transparency, making them ideal for applications requiring clear visibility and high light transmission. This quality is essential in display technologies, optical sensors, and imaging systems.
- High Chemical Stability:Glass substrates are highly resistant to chemical reactions, making them suitable for environments where exposure to corrosive substances or solvents is a concern. This chemical inertness ensures the longevity and reliability of devices.
- Mechanical Strength:Despite their brittle nature, glass substrates offer substantial mechanical strength and rigidity. They provide a stable foundation for sensitive components, reducing the risk of mechanical deformation during operation.
- Thermal Stability:Glass substrates can withstand high temperatures without significant changes in their physical properties. This thermal stability makes them suitable for applications involving high-temperature processes or environments.
- Electrical Insulation:Glass substrates exhibit excellent electrical insulation properties, which is crucial in preventing electrical interference and ensuring the proper functioning of electronic circuits.
- Surface Smoothness:The inherent smoothness of glass surfaces contributes to high-quality performance in applications requiring precise alignment and adhesion. Smooth surfaces also facilitate the deposition of thin films and coatings.
- Durability and Longevity:Glass substrates are known for their durability and resistance to wear and tear. Their long-term stability ensures that devices maintain their performance and reliability over extended periods.
- Compatibility with Thin Film Technologies:Glass substrates are compatible with various thin film deposition techniques, including sputtering and chemical vapor deposition (CVD). This compatibility allows for the integration of advanced coatings and layers.
- Eco-Friendly:Glass is a recyclable material, making it an environmentally friendly choice. Its use in electronic and optical devices contributes to sustainability by reducing waste and promoting recycling.
These advantages make glass substrates a versatile and reliable choice for a wide range of applications, from high-resolution displays to advanced optical systems and semiconductor devices.
What is the Glass Substrate Fabrication Process?
The fabrication process of glass substrates involves several key steps to ensure high quality and performance. Here is an overview of the typical process:
- Glass Selection:The process begins with selecting the appropriate type of glass based on the intended application. Common types include borosilicate glass, aluminosilicate glass, and soda-lime glass, each offering specific properties like thermal stability, optical clarity, and chemical resistance.
- Cutting and Shaping:The raw glass is cut into desired shapes and sizes using precision cutting tools. This step may involve slicing large glass sheets into smaller substrates or shaping the glass into specific dimensions based on design requirements.
- Surface Preparation:The glass surfaces are cleaned and prepared to remove any contaminants, dust, or residues. This is typically done using ultrasonic cleaning, acid baths, or other methods to ensure a smooth and clean surface.
- Polishing:To achieve the required surface smoothness and flatness, the glass substrates undergo polishing. This step is crucial for applications where high optical clarity and precise alignment are needed.
- Patterning and Etching:For applications requiring specific patterns or features, photolithography or maskless lithography techniques are used to transfer designs onto the glass substrate. The glass is then etched using chemical or plasma etching to create the desired patterns or structures.
- Coating Application:Thin films or coatings are applied to the glass substrate as needed. This may include anti-reflective coatings, conductive layers, or protective films. Techniques such as sputtering, chemical vapor deposition (CVD), or spin coating are commonly used.
- Heat Treatment:Some glass substrates undergo thermal processes such as annealing or tempering to improve their mechanical strength and thermal stability. This step helps to relieve internal stresses and enhance the overall durability of the substrate.
- Inspection and Quality Control:The final glass substrates are thoroughly inspected for defects such as scratches, bubbles, or warping. Quality control measures ensure that the substrates meet the required specifications and standards.
- Cutting and Finishing:After inspection, the substrates may be further cut or trimmed to exact specifications. Additional finishing processes, such as edge treatment, are applied to prevent chipping and ensure safe handling.
- Packaging and Shipping:The finished glass substrates are carefully packaged to prevent damage during transportation. Proper packaging ensures that the substrates arrive at their destination in pristine condition.
These steps collectively ensure the production of high-quality glass substrates suitable for a wide range of applications, from electronic devices and optical components to advanced display technologies.
The application of ceramic Glass Substrate
Ceramic glass substrates are employed across various high-tech industries due to their unique combination of properties. Here’s a look at some key applications:
- Electronics:Ceramic glass substrates are widely used in the electronics industry for high-performance components. Their excellent electrical insulation properties and thermal stability make them ideal for applications such as high-frequency circuit boards, power electronics, and integrated circuits. They support reliable operation in demanding environments by providing stability and reducing electrical interference.
- Optical Devices:In optical applications, ceramic glass substrates are utilized for their superior optical clarity and minimal light distortion. They are used in lenses, mirrors, and optical filters, where precise light transmission and high durability are essential. Their ability to withstand high temperatures and harsh conditions further enhances their suitability for optical systems.
- Display Technology:Ceramic glass substrates are key components in display technologies, including liquid crystal displays (LCDs) and organic light-emitting diodes (OLEDs). Their smooth surface and excellent transparency ensure high-quality display performance, while their robustness provides protection and support for delicate display elements.
- Telecommunications:In telecommunications, ceramic glass substrates are employed in various components such as antennas, waveguides, and filters. Their high-frequency performance and thermal stability are crucial for maintaining signal integrity and reliability in communication systems.
- Sensors and Detectors:Ceramic glass substrates are used in sensors and detectors, including gas sensors and infrared detectors. Their ability to withstand harsh environments and provide accurate measurements makes them suitable for applications requiring high precision and durability.
- Medical Devices:The biocompatibility and chemical resistance of ceramic glass substrates make them suitable for medical devices and diagnostic equipment. They are used in applications such as sensors, imaging devices, and analytical instruments, where hygiene and reliability are critical.
- Automotive Industry:In the automotive sector, ceramic glass substrates are employed in sensors, displays, and electronic control units. Their durability and ability to function in extreme conditions make them valuable for automotive applications requiring high performance and longevity.
- Aerospace and Defense:The aerospace and defense industries use ceramic glass substrates for components such as avionics displays, radar systems, and protective covers. Their high thermal and mechanical stability is essential for ensuring reliable performance in demanding environments.
These diverse applications highlight the versatility and importance of ceramic glass substrates in modern technology. Their unique properties make them a critical component in a wide range of advanced systems and devices.
FAQs about Glass Substrate
What are the main types of glass used for substrates?
Common types include borosilicate glass, aluminosilicate glass, and soda-lime glass. Each type offers different properties such as thermal stability, optical clarity, and chemical resistance.
What are the advantages of using glass substrates?
Glass substrates offer excellent optical transparency, high chemical stability, mechanical strength, thermal stability, and electrical insulation. They are also durable and compatible with thin film technologies.
How are glass substrates fabricated?
The fabrication process involves selecting the glass type, cutting and shaping it, polishing surfaces, patterning and etching, applying coatings, heat treating, and conducting quality control inspections.
What are common applications of glass substrates?
They are used in electronics (circuit boards, displays), optical devices (lenses, filters), telecommunications (antennas, waveguides), sensors, medical devices, automotive components, and aerospace technology.
How do you handle and process glass substrates?
Handle glass substrates carefully to avoid breakage or contamination. Use appropriate tools and fixtures during processing and ensure surfaces are cleaned and treated properly.
Can glass substrates be recycled?
Yes, glass substrates are recyclable, making them an environmentally friendly choice. Recycling helps reduce waste and supports sustainability in technology manufacturing.