What is Cavity PCBs?
Cavity PCBs Manufacturer,Cavity PCBs, also known as embedded PCBs, feature integrated cutouts or cavities within the board itself, housing components or modules. This innovative design approach offers space-saving benefits, allowing for higher component density and more efficient use of board space. Additionally, cavity PCBs enhance thermal management by positioning components closer to the board’s surface, improving heat dissipation. With improved reliability and protection for housed components, cavity PCBs find applications across industries such as automotive, aerospace, consumer electronics, and medical devices, where compactness, performance, and durability are paramount.
Cavity PCBs, also known as embedded PCBs or cavity boards, refer to printed circuit boards (PCBs) that feature cavities or cutouts within the board itself. These cavities can be used to house components, connectors, or even other electronic modules. This design approach offers several advantages.
Firstly, cavity PCBs enable a more compact and streamlined design, allowing for higher component density and more efficient use of space within electronic devices. By integrating components directly into the PCB, manufacturers can reduce the overall footprint of the device, which is especially beneficial for applications where size and weight are critical factors.
Secondly, cavity PCBs can help improve thermal management by allowing components to be positioned closer to the surface of the board, where heat dissipation mechanisms such as heatsinks or thermal vias can be more effectively utilized. This can enhance the reliability and performance of the electronic system, particularly in high-power applications or environments with limited airflow.
Additionally, cavity PCBs offer enhanced protection for sensitive components by enclosing them within the board itself, shielding them from external environmental factors such as dust, moisture, or mechanical shock. This can contribute to increased durability and longevity of the electronic device.
Overall, cavity PCBs represent a versatile and innovative approach to PCB design, offering numerous benefits in terms of space efficiency, thermal management, and component protection. However, they may require specialized manufacturing processes and incur higher production costs compared to traditional PCBs, which should be taken into consideration during the design and production phases.
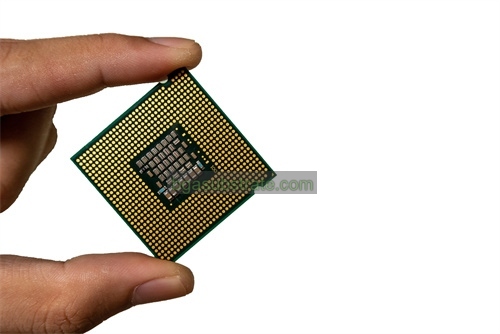
Cavity PCBs Manufacturer
What is the Cavity PCBs Design Guidelines?
Designing cavity PCBs requires careful consideration of several factors to ensure optimal performance and manufacturability. Here are some key guidelines:
- Cavity Size and Shape: Determine the dimensions and shape of the cavity based on the components or modules it will house. Ensure that the cavity is large enough to accommodate the components comfortably while maintaining sufficient clearance to prevent electrical interference or mechanical conflicts.
- Cavity Placement: Strategically position cavities within the PCB layout to minimize signal routing complexity and ensure efficient use of board space. Consider factors such as signal integrity, thermal management, and accessibility for assembly and servicing.
- Cavity Depth: Determine the depth of the cavity based on the height of the components it will contain and any additional clearance requirements for assembly and soldering processes. Ensure that the depth is adequate to accommodate the tallest components without causing interference with adjacent layers or compromising structural integrity.
- Cavity Wall Thickness: Design the walls of the cavity with sufficient thickness to provide mechanical stability and support for components mounted within. Consider the material properties of the PCB substrate and any additional reinforcement techniques, such as filling the cavity with epoxy or resin, to enhance structural integrity.
- Cavity Edge Clearance: Maintain adequate clearance around the edges of the cavity to prevent electrical short circuits or mechanical damage during assembly, handling, and operation. Follow standard design rules for PCB edge clearance and consider incorporating protective features such as chamfers or fillets to reduce stress concentrations.
- Signal Routing and Ground Planes: Plan the placement of signal traces and ground planes around the cavity to minimize signal interference and ensure signal integrity. Maintain proper signal return paths and impedance matching considerations, especially near high-speed or high-frequency components housed within the cavity.
- Thermal Management: Consider the impact of cavity design on thermal management requirements. Ensure sufficient airflow or thermal vias to dissipate heat generated by components within the cavity effectively. Design the PCB with provisions for thermal relief and heatsinking as needed to maintain optimal operating temperatures.
- Assembly and Manufacturing Considerations: Evaluate the manufacturability of the cavity PCB design, considering factors such as solder mask alignment, component placement accuracy, and accessibility for inspection and rework. Collaborate closely with PCB fabrication and assembly partners to address any specific process requirements or limitations associated with cavity designs.
By adhering to these design guidelines, engineers can develop cavity PCBs that meet performance objectives while facilitating efficient manufacturing and assembly processes. Regular design reviews and collaboration with stakeholders can help identify and address potential issues early in the design cycle, ensuring successful implementation of cavity PCBs in electronic systems.
The advantages of Cavity PCBs
Cavity PCBs offer several advantages over traditional PCB designs, making them an attractive option for various electronic applications:
- Space Efficiency: By integrating components directly into the PCB through cavities or cutouts, cavity PCBs can achieve a more compact and space-efficient design compared to traditional surface-mounted components. This allows for higher component density and more efficient use of available board space, making cavity PCBs ideal for miniaturized or space-constrained electronic devices.
- Improved Thermal Management: Cavity PCBs enable components to be positioned closer to the surface of the board, where thermal management mechanisms such as heatsinks, thermal vias, or airflow can be more effectively utilized. This facilitates better heat dissipation and thermal conduction, reducing the risk of overheating and improving the overall reliability and performance of the electronic system.
- Enhanced Signal Integrity: By embedding components within the PCB substrate, cavity PCBs can minimize signal routing complexity and reduce the length of signal traces, leading to improved signal integrity and reduced electromagnetic interference (EMI). This is particularly advantageous for high-speed or high-frequency applications where signal integrity is critical.
- Component Protection: Cavity PCBs offer enhanced protection for sensitive components by enclosing them within the board itself, shielding them from external environmental factors such as dust, moisture, or mechanical shock. This can contribute to increased durability and longevity of the electronic device, especially in harsh operating environments.
- Mechanical Stability: The presence of cavities within the PCB can enhance its mechanical stability and rigidity, reducing the risk of flexing or bending during handling, assembly, or operation. This can improve the overall robustness and durability of the electronic system, making it more resistant to mechanical stresses and vibrations.
- Streamlined Assembly: Cavity PCBs can simplify the assembly process by integrating components directly into the board, reducing the need for additional mounting hardware or secondary assembly steps. This can result in faster assembly times, lower production costs, and improved overall manufacturing efficiency.
- Design Flexibility: Cavity PCBs offer greater design flexibility, allowing engineers to customize the shape, size, and placement of cavities according to the specific requirements of the electronic system. This flexibility enables innovative design solutions and facilitates the integration of complex functionalities within a compact form factor.
Overall, the advantages of cavity PCBs make them a versatile and effective solution for a wide range of electronic applications, ranging from consumer electronics and telecommunications to automotive and aerospace systems. By leveraging the space-saving benefits, improved thermal management, and enhanced reliability offered by cavity PCBs, designers can create more compact, efficient, and robust electronic devices.
What is the Cavity PCBs Fabrication Process?
The fabrication process for cavity PCBs involves several steps, each crucial for creating the cavities within the board and integrating components effectively. Here’s a general overview of the cavity PCB fabrication process:
- Design Phase: The process begins with the design of the PCB layout, including the placement and dimensions of the cavities. Design software such as Altium Designer, Eagle, or KiCad is commonly used for this purpose. Engineers specify the size, shape, and location of the cavities based on the components to be housed within them and other design requirements.
- Substrate Selection: Choose a suitable substrate material for the PCB based on factors such as thermal conductivity, mechanical strength, and dielectric properties. Common substrate materials for cavity PCBs include FR-4, high-temperature laminates, or specialty materials designed for enhanced thermal management.
- Cavity Creation: The cavities are typically created during the PCB manufacturing process using advanced machining techniques such as milling, routing, or laser ablation. CNC (Computer Numerical Control) machines are often employed to precisely cut the cavities according to the design specifications. Care must be taken to ensure that the cavities are accurately positioned and dimensioned to accommodate the components without compromising the structural integrity of the PCB.
- Layer Stacking: Once the cavities are created, the individual layers of the PCB are stacked and laminated together using heat and pressure to form a single, cohesive structure. The cavity layers are aligned with the other layers of the PCB to ensure proper registration and alignment of the components within the cavities.
- Copper Deposition and Etching: Copper traces and pads are deposited onto the surface of the PCB using techniques such as electroplating or chemical deposition. A layer of copper is applied uniformly across the entire surface of the board, including within the cavities. Photolithography and etching processes are then used to selectively remove excess copper and define the desired circuit patterns.
- 6. Component Mounting: Surface-mount and through-hole components are mounted onto the PCB using automated pick-and-place machines or manual assembly techniques. Components that are to be housed within the cavities are placed into their respective cavities, ensuring proper alignment and clearance.
- Soldering and Assembly: Once all components are placed, the PCB undergoes soldering processes to establish electrical connections between the components and the PCB traces. This may involve reflow soldering, wave soldering, or hand soldering techniques depending on the specific requirements of the design. Additional assembly steps, such as conformal coating or potting, may be performed to protect the components and enhance reliability.
- Testing and Inspection: The finished PCB undergoes rigorous testing and inspection to verify functionality, electrical continuity, and adherence to quality standards. Automated testing equipment and visual inspection methods are commonly used to identify any defects or anomalies that may require correction.
- Final Finishing: Once testing is complete, the PCB is subjected to final finishing processes such as surface finish application, edge plating, and labeling. These finishing steps enhance the durability, corrosion resistance, and solderability of the PCB, preparing it for integration into the final electronic assembly.
By following these steps, manufacturers can produce cavity PCBs that meet the design requirements and performance expectations of various electronic applications. Close collaboration between design engineers, PCB fabricators, and assembly partners is essential to ensure a smooth and successful fabrication process.
The application of Cavity PCBs
Cavity PCBs find applications across various industries and electronic devices where space efficiency, thermal management, and component protection are critical considerations. Some common applications include:
- Mobile Devices: Cavity PCBs are widely used in smartphones, tablets, and wearable devices to achieve compact form factors while accommodating the necessary components such as processors, memory modules, and sensors. The space-saving benefits of cavity PCBs are particularly valuable in the design of slim and lightweight mobile devices.
- Automotive Electronics: In automotive applications, cavity PCBs are utilized in advanced driver-assistance systems (ADAS), infotainment systems, engine control units (ECUs), and other onboard electronics. The ability to integrate components within the PCB contributes to space optimization and enhances reliability in harsh operating environments.
- Medical Devices: Cavity PCBs are employed in various medical devices and equipment, including patient monitoring systems, diagnostic devices, and implantable devices. The compact design and component protection offered by cavity PCBs are beneficial for medical devices that require high reliability, precision, and durability.
- Aerospace and Defense: Cavity PCBs are used in aerospace and defense applications such as avionics systems, satellite communication systems, and radar systems. The lightweight, rugged, and space-efficient design of cavity PCBs makes them well-suited for aerospace and defense electronics, where reliability and performance are paramount.
- Industrial Automation: In industrial automation and control systems, cavity PCBs are utilized in programmable logic controllers (PLCs), motor drives, robotics, and monitoring equipment. The ability to integrate components within the PCB contributes to space optimization and facilitates streamlined assembly and maintenance processes.
- Consumer Electronics: Cavity PCBs are employed in a wide range of consumer electronics products, including smart home devices, gaming consoles, audio/video equipment, and digital cameras. The compact design and component protection offered by cavity PCBs contribute to the sleek aesthetics and enhanced durability of consumer electronics products.
- Telecommunications: Cavity PCBs play a vital role in telecommunications infrastructure, including base stations, routers, switches, and optical networking equipment. The space-saving benefits and thermal management capabilities of cavity PCBs are essential for maintaining the reliability and performance of telecommunications systems.
- Energy Systems: Cavity PCBs are utilized in renewable energy systems, power converters, and energy storage systems. The compact design and thermal management capabilities of cavity PCBs contribute to the efficiency and reliability of energy conversion and storage systems.
Overall, the versatility, space efficiency, thermal management, and component protection offered by cavity PCBs make them well-suited for a wide range of applications across industries, contributing to the development of more compact, reliable, and efficient electronic devices and systems.
FAQs
What are the advantages of cavity PCBs?
The advantages of cavity PCBs include space efficiency, improved thermal management, enhanced signal integrity, component protection, mechanical stability, streamlined assembly, and design flexibility. These benefits make cavity PCBs suitable for various electronic applications.
How are cavity PCBs fabricated?
The fabrication process for cavity PCBs involves several steps, including substrate selection, cavity creation using machining techniques, layer stacking, copper deposition and etching, component mounting, soldering and assembly, testing and inspection, and final finishing. Close collaboration between design engineers and manufacturing partners is crucial for successful fabrication.
What are the applications of cavity PCBs?
Cavity PCBs find applications across industries such as mobile devices, automotive electronics, medical devices, aerospace and defense, industrial automation, consumer electronics, telecommunications, and energy systems. They are used in various electronic devices and systems where space efficiency, thermal management, and component protection are essential.
What design guidelines should be followed when designing cavity PCBs?
Design guidelines for cavity PCBs include considerations for cavity size and shape, cavity placement, cavity depth, cavity wall thickness, cavity edge clearance, signal routing and ground planes, thermal management, and assembly and manufacturing considerations. Adhering to these guidelines ensures optimal performance and manufacturability of cavity PCB designs.
How do cavity PCBs contribute to space optimization in electronic devices?
Cavity PCBs enable components to be integrated directly into the PCB, reducing the overall footprint of electronic devices and allowing for higher component density. This space-saving design approach is particularly valuable in applications where size and weight constraints are critical factors.
What are the challenges associated with designing and manufacturing cavity PCBs?
Challenges associated with cavity PCBs include the complexity of cavity design and fabrication, potential issues with signal integrity and thermal management, increased manufacturing costs due to specialized processes, and the need for close collaboration between design engineers and manufacturing partners to address specific requirements and limitations.