Beryllium Oxide (BeO) Ceramic Substrate Manufacturer
Beryllium Oxide (BeO) Ceramic Substrate Manufacturer,Beryllium Oxide (BeO) Ceramic Substrate is prized for its superior thermal conductivity and electrical insulation properties in electronic applications. Despite its toxicity in certain forms, BeO substrates are valued for their ability to efficiently dissipate heat, crucial for high-power semiconductor devices and laser diodes. Their high dielectric strength allows for effective electrical isolation and reliability in harsh operating conditions. BeO ceramic substrates are also known for their stability at elevated temperatures and compatibility with advanced manufacturing processes, supporting the miniaturization and performance enhancements in modern electronic systems where thermal management is critical for maintaining operational efficiency and longevity.
What is Beryllium Oxide (BeO) Ceramic Substrate?
Beryllium Oxide (BeO) ceramic substrate is a specialized material used primarily in electronics and semiconductor industries due to its exceptional thermal conductivity and electrical insulation properties. It is composed of beryllium and oxygen atoms in a ceramic matrix, forming a rigid and stable structure.
The main advantage of BeO ceramic substrates lies in their high thermal conductivity, which allows efficient dissipation of heat generated by electronic components. This property helps in maintaining stable operating temperatures and preventing overheating, which can significantly affect the performance and lifespan of electronic devices.
In addition to thermal conductivity, BeO ceramics also offer excellent electrical insulation properties, making them suitable for applications where electrical isolation is crucial to prevent short circuits and interference.
BeO ceramic substrates are commonly used in high-power electronic circuits, microwave devices, laser diodes, and other applications where thermal management and electrical isolation are critical. However, it’s important to note that beryllium oxide can be toxic if inhaled as dust during manufacturing processes, necessitating careful handling and processing under controlled conditions to ensure safety.
Overall, BeO ceramic substrates are valued for their combination of thermal conductivity, electrical insulation, and mechanical stability, making them indispensable in demanding electronic and semiconductor applications.
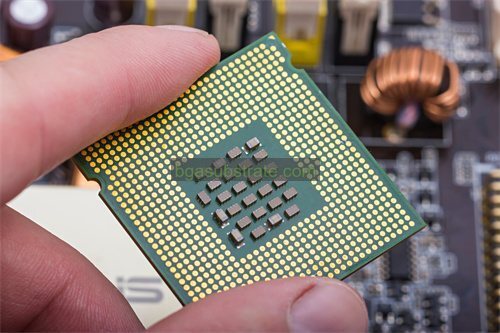
Beryllium Oxide (BeO) Ceramic Substrate Manufacturer
What is the Beryllium Oxide (BeO) Ceramic Substrate Design Guidelines?
Design guidelines for Beryllium Oxide (BeO) ceramic substrates focus on optimizing their performance in electronic and semiconductor applications while ensuring safety and reliability. Here are some key design considerations:
- Thermal Management: BeO substrates are chosen for their high thermal conductivity. Designers should maximize the contact area between components and the substrate to enhance heat dissipation. Efficient thermal management minimizes thermal gradients, reducing the risk of hot spots that could affect performance or reliability.
- Electrical Isolation: BeO ceramics offer excellent electrical insulation properties. Designers should ensure proper spacing and insulation between conductive paths or components to prevent electrical leakage or short circuits. This is critical for maintaining the integrity and reliability of electronic circuits.
- Mechanical Stability: BeO ceramic substrates are rigid and mechanically stable. Designs should consider mechanical stresses, such as thermal expansion mismatches between materials, to avoid mechanical failure or delamination. Proper mounting and handling procedures are essential to maintain substrate integrity.
- Safety Considerations: Beryllium oxide dust can be hazardous if inhaled. Designers and manufacturers must adhere to strict safety guidelines during substrate processing and handling to prevent exposure. Proper ventilation, dust control measures, and personal protective equipment (PPE) are necessary to ensure a safe working environment.
- Material Compatibility: BeO ceramic substrates are compatible with a variety of electronic materials and manufacturing processes. Designers should select compatible materials for metallization and bonding processes to ensure strong and reliable electrical connections. Adherence to material compatibility ensures optimal performance and longevity of electronic assemblies.
- Environmental Conditions: Consider the operating environment of the electronic device. BeO substrates are robust in harsh conditions, but exposure to extreme temperatures or moisture can affect performance. Designers should account for environmental factors to ensure reliability over the device’s operational lifetime.
- Regulatory Compliance: BeO is subject to regulatory controls due to its toxicity in dust form. Designers and manufacturers must comply with local regulations and industry standards regarding handling, disposal, and safety practices to protect personnel and the environment.
By adhering to these design guidelines, engineers can leverage the unique properties of Beryllium Oxide (BeO) ceramic substrates to create reliable and high-performance electronic devices while ensuring safety and compliance with regulatory requirements.
The advantages of Beryllium Oxide (BeO) Ceramic Substrate
Beryllium Oxide (BeO) ceramic substrates offer several distinct advantages that make them highly desirable in electronic and semiconductor applications:
- High Thermal Conductivity: BeO ceramics exhibit exceptionally high thermal conductivity (second only to diamond among ceramics), which allows efficient dissipation of heat from electronic components. This property helps in managing thermal loads effectively, reducing the risk of overheating and improving the reliability and longevity of electronic devices.
- Excellent Electrical Insulation: BeO ceramics provide outstanding electrical insulation properties. They have a high dielectric strength and low dielectric loss, making them ideal for applications where electrical isolation is critical. This ensures reliable performance and minimizes the risk of electrical shorts or leakage currents.
- Mechanical Stability: BeO ceramic substrates are rigid and mechanically stable, with high modulus of elasticity and low coefficient of thermal expansion. This mechanical stability helps in maintaining the structural integrity of electronic assemblies, even under varying temperatures and mechanical stresses.
- Compatibility with Semiconductor Processing: BeO substrates are compatible with various semiconductor processing techniques, including thin film deposition, metallization, and wire bonding. This compatibility allows for the integration of complex electronic circuits and devices with high precision and reliability.
- Dimensional Accuracy and Surface Finish: BeO ceramics can be manufactured with tight dimensional tolerances and excellent surface finishes. This precision is crucial for ensuring proper alignment and bonding of electronic components, which is essential for achieving optimal performance in high-frequency and high-power applications.
- Chemical Inertness and Corrosion Resistance: BeO ceramic substrates exhibit good resistance to chemical corrosion and degradation, making them suitable for use in harsh operating environments. This property enhances the durability and reliability of electronic devices deployed in challenging industrial or aerospace applications.
- Miniaturization and Weight Reduction: The high thermal conductivity of BeO ceramics allows for effective heat dissipation without requiring bulky heat sinks or cooling systems. This capability supports miniaturization efforts and helps in reducing the overall weight and size of electronic assemblies, which is advantageous in portable devices and aerospace applications.
Overall, Beryllium Oxide (BeO) ceramic substrates offer a unique combination of thermal conductivity, electrical insulation, mechanical stability, and compatibility with semiconductor processing, making them indispensable for demanding electronic and semiconductor applications where performance, reliability, and efficiency are paramount.
What is the Beryllium Oxide (BeO) Ceramic Substrate Fabrication Process?
The fabrication process of Beryllium Oxide (BeO) ceramic substrates involves several key steps to achieve the desired properties and characteristics:
- Raw Material Selection: The process begins with selecting high-purity beryllium oxide powder as the primary raw material. The purity of the powder is crucial to ensure the final ceramic substrate meets stringent quality and performance requirements.
- Formulation and Mixing: The beryllium oxide powder is mixed with binders and additives to enhance plasticity and facilitate shaping during subsequent processing steps. This mixture, known as a slurry, is thoroughly homogenized to achieve uniform distribution of particles and additives.
- Shaping (Forming): The slurry is then shaped into the desired form of the ceramic substrate through various techniques such as slip casting, extrusion, or dry pressing. Slip casting involves pouring the slurry into a mold, allowing it to solidify into the shape of the substrate. Extrusion uses pressure to force the slurry through a die to form continuous shapes. Dry pressing compacts the slurry into a mold under high pressure to form green bodies (pre-sintered shapes).
- Green Machining (Optional): In some cases, green bodies may undergo machining processes such as milling or drilling to achieve precise dimensions and surface finishes before the next stage.
- Binder Removal (Debinding): The shaped green bodies undergo a controlled thermal process known as debinding. During debinding, organic binders and additives are removed through heating in a controlled atmosphere or vacuum. This step is critical to prevent residual organics that could compromise the final ceramic’s properties.
- Sintering: The debound green bodies are then subjected to high-temperature sintering in a specialized furnace. Sintering involves heating the green bodies to temperatures close to the melting point of beryllium oxide (typically around 2500°C) to promote atomic diffusion and bond formation. This process transforms the compacted powder into a dense ceramic substrate with the desired mechanical, thermal, and electrical properties.
- Finishing: After sintering, the ceramic substrates may undergo additional finishing processes such as grinding, polishing, or machining to achieve final dimensions, surface smoothness, and tolerances as required by specific applications.
- Quality Control and Testing: Throughout the fabrication process, quality control measures are implemented to ensure consistency and reliability of the ceramic substrates. Testing may include dimensional inspection, mechanical testing, thermal conductivity measurement, and electrical insulation testing to verify adherence to specifications and standards.
- Handling and Safety: Due to the toxicity of beryllium oxide dust, strict handling and safety protocols are followed throughout the entire fabrication process to protect workers and ensure environmental compliance.
By following these steps systematically, manufacturers can produce Beryllium Oxide (BeO) ceramic substrates that meet the stringent requirements of electronic and semiconductor industries, offering high thermal conductivity, excellent electrical insulation, and mechanical stability for a wide range of applications.
The application of ceramic Beryllium Oxide (BeO) Ceramic Substrate
Beryllium Oxide (BeO) ceramic substrates find application in various high-performance electronic and semiconductor devices where thermal management, electrical insulation, and reliability are critical. Some of the key applications include:
- Power Electronics: BeO ceramic substrates are widely used in power electronic modules such as insulated gate bipolar transistors (IGBTs), diodes, and thyristors. Their high thermal conductivity helps in efficiently dissipating heat generated by power devices, improving their reliability and lifespan. They also provide excellent electrical insulation, reducing the risk of electrical breakdown.
- Microwave and RF Components: BeO substrates are ideal for microwave and radio frequency (RF) applications due to their low dielectric loss and high thermal conductivity. They are used in the production of microwave integrated circuits (MICs), RF power amplifiers, filters, and antennas. The high thermal conductivity helps in managing heat dissipation in high-frequency circuits, ensuring stable performance.
- Optoelectronics and Photonics: In optoelectronic devices such as laser diodes and light-emitting diodes (LEDs), BeO ceramic substrates play a crucial role in providing thermal management and mechanical stability. They help in dissipating heat generated by the devices, thereby maintaining optimal operating temperatures and enhancing performance.
- High-Performance Semiconductors: BeO ceramic substrates are used in the manufacturing of advanced semiconductor devices and integrated circuits (ICs). They provide a stable and reliable platform for mounting and interconnecting semiconductor chips, ensuring efficient thermal dissipation and electrical isolation.
- Aerospace and Defense: Due to their robustness, high thermal conductivity, and reliability in harsh environments, BeO ceramic substrates are extensively used in aerospace and defense applications. These include radar systems, avionics, communication equipment, and electronic warfare systems where performance under extreme conditions is critical.
- Medical Devices: BeO substrates are employed in medical imaging equipment, such as X-ray detectors and MRI machines, where thermal stability and electrical insulation are essential for reliable operation and patient safety.
- Automotive Electronics: With the increasing electrification of vehicles, BeO ceramic substrates are finding applications in automotive electronics. They contribute to efficient thermal management in power modules, battery management systems, and sensors, ensuring reliable performance in demanding automotive environments.
In summary, Beryllium Oxide (BeO) ceramic substrates are valued for their combination of high thermal conductivity, excellent electrical insulation, and mechanical stability, making them indispensable in a wide range of advanced electronic and semiconductor applications where reliability, performance, and longevity are paramount.
FAQs about Beryllium Oxide (BeO) Ceramic Substrate
What is Beryllium Oxide (BeO) ceramic?
Beryllium Oxide (BeO) ceramic is a specialized material composed of beryllium and oxygen atoms in a ceramic matrix. It is known for its high thermal conductivity, excellent electrical insulation properties, and mechanical stability.
What are the key properties of BeO ceramic substrates?
BeO ceramic substrates exhibit exceptionally high thermal conductivity, second only to diamond among ceramics. They also offer excellent electrical insulation, low dielectric loss, high mechanical stability, and chemical inertness.
What are the main applications of BeO ceramic substrates?
BeO ceramic substrates are used in power electronics (IGBTs, diodes), microwave and RF components (MICs, RF amplifiers), optoelectronics (laser diodes, LEDs), high-performance semiconductors, aerospace and defense electronics, medical devices, and automotive electronics.
What are the advantages of using BeO ceramic substrates?
The advantages include efficient heat dissipation, superior electrical insulation, mechanical stability, compatibility with semiconductor processing, and reliability in harsh environments. They contribute to enhanced device performance, longevity, and miniaturization.
Are there any safety considerations when handling BeO ceramic substrates?
Yes, beryllium oxide is toxic in dust form, posing health risks if inhaled. Therefore, strict safety protocols must be followed during substrate fabrication, handling, and disposal to prevent exposure to beryllium dust particles.
How are BeO ceramic substrates fabricated?
The fabrication process typically involves raw material selection (high-purity BeO powder), formulation, mixing, shaping (via methods like slip casting or extrusion), debinding (removal of organic binders), sintering (high-temperature consolidation), finishing (grinding, polishing), and quality control testing.
What are the environmental considerations with BeO ceramic substrates?
While BeO ceramic substrates themselves are chemically inert and stable, precautions are necessary during manufacturing to prevent environmental contamination from raw materials and waste products. Proper disposal methods should be followed to manage any hazardous by-products safely.