Antenna Cavity PCBs Manufacturer
Antenna Cavity PCBs Manufacturer,Antenna cavity PCBs are specialized printed circuit boards designed to integrate antenna elements within a controlled cavity structure. This design optimizes antenna performance by minimizing electromagnetic interference (EMI) and maximizing signal efficiency. They are crucial in applications requiring reliable wireless communication, offering advantages such as compact size, improved mechanical stability, and enhanced integration with other electronic components. Antenna cavity PCBs find wide use in telecommunications, automotive electronics, aerospace, and IoT devices, where they contribute to achieving robust and efficient wireless connectivity solutions in various demanding environments.
What is Antenna Cavity PCBs?
Antenna cavity PCBs refer to printed circuit boards designed specifically to house and integrate antenna elements within their structure. These PCBs are engineered to optimize antenna performance by providing a controlled environment that minimizes interference and maximizes signal efficiency. They often include specialized features such as precise dimensions, shielding layers, and controlled impedance traces to ensure the antenna operates effectively within specified frequency ranges.
The design of antenna cavity PCBs takes into account factors like signal propagation, electromagnetic interference (EMI) reduction, and mechanical stability. They are commonly used in applications where wireless communication is critical, such as in telecommunications, satellite systems, radar systems, and IoT devices. The cavity design helps in containing and focusing electromagnetic waves emitted or received by the antenna, thereby enhancing overall performance and reliability.
Manufacturing antenna cavity PCBs involves advanced techniques to ensure the integrity of signal paths and the durability of the board under various environmental conditions. Engineers and designers carefully select materials and manufacturing processes to meet performance requirements while maintaining cost-effectiveness and reliability. As technology evolves, antenna cavity PCBs continue to play a crucial role in enabling robust wireless communication solutions across various industries.
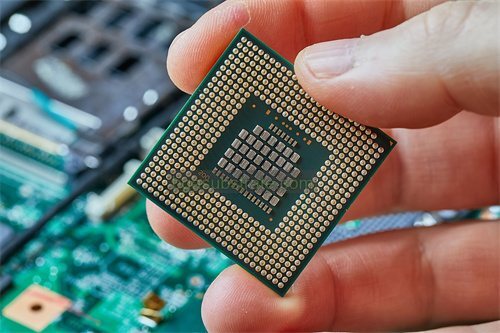
Antenna Cavity PCBs Manufacturer
What is the Antenna Cavity PCBs Design Guidelines?
Designing antenna cavity PCBs involves adhering to several key guidelines to ensure optimal performance of the antenna system. Here are some essential design guidelines:
- Cavity Dimensions and Geometry: The dimensions and geometry of the cavity should be carefully designed to resonate at the desired frequency or frequencies of operation. This involves calculating the dimensions based on wavelength and considering factors like the size of the antenna element and the required isolation from other components.
- Material Selection: Selecting appropriate PCB materials is crucial for antenna cavity PCBs. High-frequency laminates with low dielectric constant (εr) and low loss tangent (tan δ) are preferred to minimize signal losses and interference. The material should also have good mechanical strength and dimensional stability.
- Cavity Shielding: Proper shielding of the cavity is essential to minimize electromagnetic interference (EMI) from external sources and to prevent radiation from the antenna affecting nearby components. Metallic coatings or additional shielding layers within the PCB can be employed for this purpose.
- Impedance Matching: Ensuring proper impedance matching between the antenna, transmission line, and PCB is critical for maximizing power transfer and minimizing reflection losses. This involves careful design of transmission line widths, lengths, and matching networks.
- Placement of Components: Components such as the antenna feed point, matching components, and connectors should be strategically placed within the cavity to minimize signal losses and maintain impedance matching. This requires careful consideration of signal paths and avoiding areas with high EMI.
- Heat Dissipation: Antenna cavity PCBs may generate heat, especially in high-power applications or when integrated with active components. Proper thermal management techniques such as heat sinks, vias, and adequate PCB copper area should be incorporated into the design to prevent overheating.
- Environmental Considerations: Antenna cavity PCBs may operate in various environmental conditions. Designers should consider factors such as temperature range, humidity, and exposure to moisture or chemicals when selecting materials and designing the PCB layout.
- Testing and Validation: Comprehensive testing and validation of the antenna cavity PCB design are essential to ensure it meets performance specifications. This includes testing for impedance matching, radiation patterns, and overall antenna efficiency.
By following these guidelines, designers can create antenna cavity PCBs that offer high performance, reliability, and efficiency in various wireless communication applications.
The advantages of Antenna Cavity PCBs
Antenna cavity PCBs offer several advantages that make them preferred choices in various wireless communication applications:
- Improved Antenna Performance: By integrating antenna elements within a controlled cavity, these PCBs can enhance antenna efficiency, gain, and radiation patterns. The cavity structure helps in minimizing electromagnetic interference (EMI) and improves isolation between antenna elements and other components, thereby optimizing overall performance.
- Reduced Interference: The cavity design provides shielding that reduces interference from external electromagnetic sources, improving signal integrity and reliability. This shielding also prevents the antenna’s radiation from affecting other nearby components on the PCB, maintaining system stability.
- Compact Design: Antenna cavity PCBs allow for a more compact and integrated design compared to external antenna solutions. This is particularly beneficial in devices where space is limited or where aesthetics and form factor are important considerations.
- Customizable and Tunable: The dimensions and geometry of the cavity can be customized to match specific frequency requirements and performance goals. This flexibility allows designers to optimize the antenna’s resonance and impedance characteristics for different frequency bands or communication standards.
- Mechanical Stability: Integrating the antenna within the PCB provides mechanical stability and durability. This reduces the risk of antenna misalignment or damage that could occur with external antenna installations, especially in harsh environments or during transportation.
- Cost Efficiency: While initial design and manufacturing costs may be higher compared to simple PCBs, antenna cavity PCBs can lead to cost savings in overall system design and production. They eliminate the need for additional external antenna components and reduce assembly complexity.
- Enhanced Design Integration: Integrating antennas within the PCB allows for better integration with other circuit components and subsystems. This can simplify PCB layout, reduce signal losses in transmission lines, and improve overall system performance and reliability.
- Application Versatility: Antenna cavity PCBs find applications across a wide range of industries and technologies, including telecommunications, IoT devices, automotive electronics, aerospace, and military applications. Their versatility makes them suitable for various communication standards and frequencies.
In summary, antenna cavity PCBs offer advantages such as improved performance, reduced interference, compact design, customization flexibility, mechanical stability, cost efficiency, enhanced integration, and broad application versatility. These benefits make them a preferred choice in designing high-performance wireless communication systems and devices.
What is the Antenna Cavity PCBs Fabrication Process?
The fabrication process of antenna cavity PCBs involves several specialized steps to ensure the precise integration of antenna elements within the PCB structure. Here is an overview of the typical fabrication process:
- Design and Layout: The process begins with the design phase, where engineers define the dimensions, geometry, and placement of the antenna cavity within the PCB. This includes selecting suitable PCB materials with specific dielectric properties and mechanical strength to meet performance requirements.
- Material Selection: High-frequency PCB materials with low dielectric constant (εr) and low loss tangent (tan δ) are preferred for antenna cavity PCBs to minimize signal losses and interference. Common materials include PTFE (Polytetrafluoroethylene) based laminates such as Rogers 4000 series or similar high-frequency substrates.
- Cavity Formation: The cavity where the antenna elements will be housed is typically formed by milling or etching processes. CNC (Computer Numerical Control) milling machines are used to accurately mill out the cavity on the PCB substrate. Alternatively, chemical etching processes may be employed for creating the cavity structure.
- Copper Plating: After milling or etching the cavity, the PCB undergoes copper plating to reinforce the cavity walls and provide electrical conductivity. This step ensures that the cavity maintains its structural integrity and provides a conductive surface for grounding or other purposes.
- Circuit Patterning: The PCB then undergoes standard PCB fabrication processes such as imaging, etching, and drilling to create the circuitry and vias necessary for connecting the antenna elements, transmission lines, and other components on the board. Special care is taken to maintain the integrity of the cavity and its shielding properties during these processes.
- Component Placement: Antenna components such as feeding points, matching networks, and connectors are carefully placed within the cavity area according to the PCB layout design. Placement is critical to ensure optimal performance and impedance matching of the antenna system.
- Assembly and Soldering: Surface-mount technology (SMT) or through-hole components are soldered onto the PCB as per the design requirements. Precision soldering techniques are used to minimize any interference with the antenna’s performance.
- Testing and Inspection: Once assembled, antenna cavity PCBs undergo rigorous testing and inspection. This includes electrical testing to verify impedance matching, signal integrity, and radiation patterns. Visual inspection and mechanical testing ensure that the PCB meets quality standards and functional requirements.
- Finishing and Coating: Finally, the PCB may undergo finishing processes such as applying protective coatings or surface finishes (e.g., ENIG – Electroless Nickel Immersion Gold) to enhance durability, solderability, and environmental resistance.
- Quality Assurance: Throughout the fabrication process, quality assurance measures are implemented to ensure consistency and reliability of the antenna cavity PCBs. This includes adherence to design specifications, material traceability, and compliance with industry standards.
By following these steps, manufacturers can produce antenna cavity PCBs that offer high performance, reliability, and durability for various wireless communication applications. Each step in the fabrication process is critical to achieving optimal antenna functionality and integration within the PCB structure.
The application of ceramic Antenna Cavity PCBs
Ceramic antenna cavity PCBs find application in situations where high-frequency performance, durability, and miniaturization are critical factors. Here are some key applications where ceramic antenna cavity PCBs are commonly used:
- Wireless Communication Devices: Ceramic antenna cavity PCBs are widely employed in wireless communication devices such as smartphones, tablets, wearables, and IoT devices. Their compact size and excellent high-frequency characteristics make them suitable for integrating antennas in small form factors without sacrificing performance.
- Automotive Electronics: In automotive applications, ceramic antenna cavity PCBs are utilized for keyless entry systems, remote key fobs, vehicle-to-vehicle (V2V) communication, and GPS systems. They withstand temperature fluctuations and harsh environmental conditions typical in automotive environments while maintaining reliable wireless connectivity.
- Telecommunications:Ceramic antenna cavity PCBs play a crucial role in telecommunications infrastructure, including base stations, repeaters, and antennas for cellular networks. Their high-frequency capabilities and stable performance ensure efficient signal transmission and reception over long distances.
- Aerospace and Defense: In aerospace and defense applications, ceramic antenna cavity PCBs are used for radar systems, satellite communication, unmanned aerial vehicles (UAVs), and military communication equipment. They offer robust performance in challenging environments and comply with stringent reliability and durability standards.
- Medical Devices: Medical devices often require compact and reliable wireless communication capabilities. Ceramic antenna cavity PCBs are used in devices such as implantable medical devices, remote patient monitoring systems, and diagnostic equipment where high reliability and miniaturization are critical.
- Industrial IoT (IIoT): Industrial IoT applications benefit from ceramic antenna cavity PCBs due to their ability to withstand harsh industrial environments, including temperature extremes, moisture, and vibration. They are used in applications such as industrial sensors, asset tracking systems, and smart manufacturing equipment.
- Consumer Electronics: Beyond smartphones and wearables, ceramic antenna cavity PCBs are also found in consumer electronics like smart home devices, remote controls, gaming consoles, and Bluetooth accessories. Their compact size and reliable performance contribute to seamless connectivity and user experience.
Overall, ceramic antenna cavity PCBs offer superior high-frequency performance, mechanical robustness, and thermal stability compared to traditional FR4 PCBs. These characteristics make them indispensable in modern wireless communication systems across various industries where efficient and reliable connectivity is essential.
FAQs
What are antenna cavity PCBs?
Antenna cavity PCBs are printed circuit boards designed to integrate antenna elements within a controlled cavity structure. They are used to optimize antenna performance by minimizing electromagnetic interference (EMI) and enhancing signal efficiency.
What are the advantages of using antenna cavity PCBs?
Antenna cavity PCBs offer advantages such as improved antenna performance, reduced interference, compact design, customization flexibility, mechanical stability, cost efficiency, enhanced integration, and broad application versatility. These benefits make them ideal for high-performance wireless communication systems.
Where are antenna cavity PCBs commonly used?
Antenna cavity PCBs find applications in various industries including telecommunications, automotive electronics, aerospace, defense, medical devices, industrial IoT (IIoT), and consumer electronics. They are used in devices ranging from smartphones and base stations to satellites and medical implants.
How are antenna cavity PCBs fabricated?
The fabrication process of antenna cavity PCBs involves steps such as design and layout, material selection (often high-frequency ceramics or specialized laminates), cavity formation (milling or etching), copper plating, circuit patterning, component placement, assembly, testing, and finishing. Each step is crucial to ensure optimal antenna performance and reliability.
What materials are used for antenna cavity PCBs?
Antenna cavity PCBs are typically made from high-frequency materials such as ceramic substrates (Alumina or Aluminum Nitride) or specialized high-frequency laminates (e.g., Rogers 4000 series). These materials offer low dielectric loss, excellent mechanical stability, and high thermal conductivity, which are essential for high-frequency applications.
What are the key considerations when designing antenna cavity PCBs?
Key considerations include cavity dimensions and geometry for resonance, material selection for optimal performance, shielding for EMI reduction, impedance matching for efficient signal transmission, heat dissipation, component placement for minimal interference, and testing/validation for performance verification.
Why choose antenna cavity PCBs over external antennas?
Antenna cavity PCBs offer advantages such as improved integration, reduced footprint, enhanced performance due to minimized losses and interference, and better durability in harsh environments. They eliminate the need for external antennas, simplifying device design and improving aesthetics.
What are the challenges associated with antenna cavity PCBs?
Challenges may include higher fabrication costs compared to standard PCBs, complexity in design and assembly due to cavity integration, and the need for specialized expertise in high-frequency design and testing. Ensuring proper shielding and impedance matching can also pose challenges in some designs.