Alumina (Al2O3) Ceramic Substrate Manufacturer
Alumina (Al2O3) Ceramic Substrate Manufacturer,Alumina (Al2O3) Ceramic Substrate is a widely used material in electronic and semiconductor industries. Known for its excellent electrical insulation properties, high thermal conductivity, and mechanical strength, alumina substrates provide a stable platform for electronic components. They are utilized in applications requiring heat dissipation, such as power modules and LEDs, due to their ability to withstand high temperatures and thermal cycling. Alumina ceramic substrates are also valued for their chemical inertness, making them suitable for environments with harsh chemicals. Their precision machining capabilities allow for intricate circuit designs, supporting advancements in miniaturization and performance of electronic devices.
What is Alumina (Al2O3) Ceramic Substrate?
An alumina (Al2O3) ceramic substrate is a crucial component in various electronic and electrical applications due to its excellent thermal and mechanical properties. It is primarily composed of aluminum oxide (Al2O3), a ceramic material known for its high thermal conductivity, electrical insulation, and resistance to corrosion. These substrates are used extensively in the manufacturing of integrated circuits (ICs), semiconductor devices, LEDs, and electronic packages.
Alumina ceramic substrates provide a stable platform for mounting electronic components due to their ability to dissipate heat effectively. This property is crucial for maintaining the reliability and performance of electronic devices, especially those that generate significant heat during operation. Additionally, alumina substrates exhibit high dielectric strength, making them suitable for applications requiring electrical insulation between conductive components.
Manufacturing processes for alumina substrates involve shaping and firing the ceramic material to achieve desired dimensions and properties. Depending on the application, substrates may be further processed to include features such as metallization layers for interconnecting components or forming electrical contacts.
In summary, alumina (Al2O3) ceramic substrates play a vital role in modern electronics, offering thermal management, electrical insulation, and mechanical stability necessary for the efficient and reliable operation of electronic devices across various industries.
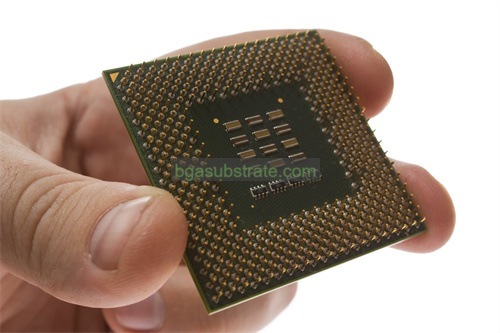
Alumina (Al2O3) Ceramic Substrate Manufacturer
What is the Alumina (Al2O3) Ceramic Substrate Design Guidelines?
Design guidelines for alumina (Al2O3) ceramic substrates are critical to ensure the optimal performance and reliability of electronic devices. Here are some key design considerations:
- Thermal Management: Alumina ceramic substrates have high thermal conductivity, but effective thermal management is still crucial. Design should include considerations for heat dissipation, such as placing heat-generating components strategically, using thermal vias to improve heat transfer to the substrate, and ensuring adequate airflow or heat sinking where necessary.
- Mechanical Design: Alumina ceramics are brittle, so mechanical stress must be minimized to prevent cracking or failure. This includes designing for adequate support and avoiding sudden changes in thickness or shape that could lead to mechanical stress concentrations.
- Electrical Isolation: Alumina is an excellent electrical insulator. Design should ensure proper spacing and isolation between conductive traces or components to prevent electrical shorts. This may involve using appropriate dielectric layers and ensuring sufficient clearance distances.
- Metallization and Interconnects: Alumina substrates often require metallization layers for interconnecting components and forming electrical contacts. Design should consider the compatibility of metallization materials with the substrate material, as well as ensuring proper adhesion and reliability of the metallization layers.
- Dimensional Tolerances and Flatness: Alumina substrates need to meet tight dimensional tolerances to ensure compatibility with mounting and assembly processes. Flatness is crucial for the uniformity of thermal interface materials (TIMs) and for proper alignment of components.
- Environmental Considerations: Consider the operating environment, including temperature variations, humidity, and exposure to chemicals or mechanical stress. Alumina is generally robust in harsh environments, but specific design choices can enhance durability and longevity.
- Manufacturability: Design for manufacturability is important to ensure cost-effective production. This includes considering standard substrate sizes, minimizing complex features that increase production difficulty, and optimizing for the chosen manufacturing processes (e.g., green machining, firing, metallization).
- Testing and Quality Assurance: Plan for testing and quality assurance processes to verify substrate performance under expected operating conditions. This may include thermal cycling tests, electrical testing for insulation integrity, and mechanical stress testing.
By adhering to these design guidelines, engineers can maximize the performance, reliability, and manufacturability of electronic devices utilizing alumina ceramic substrates. Each guideline helps mitigate potential issues related to thermal management, mechanical integrity, electrical performance, and environmental robustness, ensuring optimal functionality in diverse applications.
The advantages of Alumina (Al2O3) Ceramic Substrate
Alumina (Al2O3) ceramic substrates offer several advantages that make them highly suitable for a wide range of electronic and electrical applications:
- High Thermal Conductivity: Alumina ceramic substrates have excellent thermal conductivity compared to many other ceramic materials. This property allows them to efficiently dissipate heat generated by electronic components, thereby enhancing device reliability and longevity.
- Electrical Insulation: Alumina is a superb electrical insulator, making it ideal for applications where electrical isolation between components or circuits is critical. It helps prevent electrical shorts and ensures reliable operation of electronic devices.
- Mechanical Strength and Hardness: Alumina ceramics exhibit high mechanical strength and hardness, which contribute to their durability and resistance to mechanical wear and damage. This makes them suitable for harsh operating environments and applications where mechanical stability is crucial.
- Chemical Resistance: Alumina is resistant to many chemicals, acids, and alkalis, which enhances its suitability for applications exposed to corrosive environments or chemicals. This property contributes to the long-term reliability of devices.
- Dimensional Stability: Alumina substrates maintain their dimensional stability over a wide range of temperatures. This property is important for maintaining the integrity of electronic assemblies and ensuring consistent performance under varying thermal conditions.
- Compatibility with Metallization: Alumina substrates can be metallized with various metals such as gold, silver, or platinum. This metallization allows for reliable electrical interconnections and soldering of components, enhancing the functionality and performance of electronic devices.
- Wide Range of Applications: Due to their excellent thermal, electrical, and mechanical properties, alumina ceramic substrates find applications in diverse fields including semiconductor manufacturing, LED packaging, power electronics, sensors, and high-frequency circuits.
- Cost-Effectiveness: Alumina ceramic substrates are generally cost-effective compared to other high-performance ceramic materials like aluminum nitride (AlN) or beryllium oxide (BeO), making them a preferred choice for many electronic applications where cost considerations are important.
In summary, alumina (Al2O3) ceramic substrates combine high thermal conductivity, excellent electrical insulation, mechanical strength, chemical resistance, and dimensional stability, making them versatile and reliable materials for demanding electronic and electrical applications. These advantages contribute to improved device performance, longevity, and overall efficiency in various industries.
What is the Alumina (Al2O3) Ceramic Substrate Fabrication Process?
The fabrication process of alumina (Al2O3) ceramic substrates involves several key steps to achieve the desired properties and dimensions suitable for electronic applications:
- Powder Preparation: The process begins with the preparation of alumina powder. High-purity aluminum oxide powder is typically used, which may undergo milling and mixing to achieve a consistent particle size distribution and homogeneity.
- Forming:The alumina powder is then shaped into the desired substrate form using one of several techniques:
– Dry Pressing: Involves pressing the powder into a die at high pressure to form green (unfired) substrates.
– Injection Molding: Uses a binder and pressure to form intricate shapes or features before the binder is removed.
– Extrusion: Where the powder is mixed with a binder and forced through a die to form continuous shapes like rods or tubes.
- Green Machining: After forming, the green alumina substrates undergo machining processes to refine their shape, dimensions, and surface finish. This includes cutting, drilling, and milling to achieve precise tolerances and features.
- Drying: The green substrates are dried to remove any remaining moisture and binder. This step is crucial to prevent cracking during subsequent firing.
- Firing (Sintering): The dried green substrates are fired in a kiln at high temperatures typically ranging from 1,200 to 1,600°C (2,192 to 2,912°F), depending on the specific requirements of the alumina ceramic. During firing, the powder particles bond together through diffusion processes, forming a dense and solid ceramic structure.
- Shrinkage Control: Careful control of the firing process is necessary to manage shrinkage, which occurs as the alumina particles densify and form a solid ceramic body. Shrinkage rates are predictable based on the initial powder particle size and sintering temperature.
- Surface Finishing: After sintering, the alumina substrates may undergo additional machining or grinding processes to achieve precise dimensions, flatness, and surface roughness as required by the final application.
- Metallization: Depending on the application, metallization layers may be applied to the alumina substrate surfaces. This involves depositing thin films of metals such as gold, silver, or platinum using techniques like sputtering or thick film screen printing. Metallization enables electrical interconnection and soldering of components.
- Quality Control: Throughout the fabrication process, quality control measures are implemented to ensure the substrates meet specified dimensional, mechanical, thermal, and electrical properties. This includes inspections, testing for porosity, density, and thermal conductivity, as well as checking for defects like cracks or surface irregularities.
By following these fabrication steps, alumina (Al2O3) ceramic substrates are produced with the high thermal conductivity, excellent electrical insulation, mechanical strength, and dimensional stability required for various electronic and electrical applications. Each stage of the process is carefully designed to optimize the properties and performance of the final ceramic substrate.
The application of ceramic Alumina (Al2O3) Ceramic Substrate
Alumina (Al2O3) ceramic substrates find wide-ranging applications across various industries due to their excellent thermal, mechanical, and electrical properties. Some key applications include:
- Electronic Components: Alumina ceramic substrates are extensively used in the manufacture of electronic components such as integrated circuits (ICs), LEDs (Light Emitting Diodes), power modules, and microelectronics packaging. Their high thermal conductivity helps in efficiently dissipating heat generated by electronic devices, thereby improving performance and reliability.
- Semiconductor Manufacturing: In semiconductor fabrication, alumina substrates serve as a base for mounting and interconnecting semiconductor devices. They provide electrical insulation and mechanical support, crucial for the miniaturization and reliability of semiconductor components.
- Power Electronics: Alumina ceramic substrates are utilized in power electronic applications where high voltage and current handling capabilities are required. They enable efficient thermal management and electrical isolation, essential for devices such as power transistors, diodes, and thyristors.
- LED Packaging: LED manufacturers use alumina substrates for packaging LEDs due to their ability to withstand high operating temperatures and provide effective thermal management. This helps in maintaining LED performance and extending their operational lifespan.
- Sensor Technology: Alumina ceramic substrates are used in the production of various sensors including gas sensors, temperature sensors, and pressure sensors. Their stability at high temperatures, along with excellent electrical insulation properties, makes them suitable for sensor applications.
- Medical Devices: In medical electronics, alumina substrates are employed in devices such as implantable medical sensors, diagnostic equipment, and electronic prosthetics. Their biocompatibility, along with thermal and electrical properties, ensures safe and reliable operation within the human body.
- Aerospace and Defense: Alumina ceramic substrates are utilized in aerospace and defense applications for radar systems, communication equipment, and electronic warfare systems. They offer durability, thermal stability, and resistance to harsh environmental conditions.
- High-Frequency Applications: Due to their low dielectric loss and high-frequency properties, alumina ceramic substrates are used in RF (Radio Frequency) and microwave applications. They are employed in antennas, RF filters, and satellite communication systems.
- Industrial Equipment: Alumina substrates play a role in industrial automation and control systems, where they are used in circuit boards and power modules for machinery and equipment. Their thermal and mechanical robustness ensures reliable performance in demanding industrial environments.
- Consumer Electronics: Alumina ceramic substrates can be found in various consumer electronic devices such as smartphones, tablets, and laptops. They contribute to the miniaturization and reliability of electronic components within these devices.
In summary, alumina (Al2O3) ceramic substrates are versatile materials that contribute significantly to the advancement of technology across multiple industries. Their combination of thermal conductivity, electrical insulation, mechanical strength, and reliability makes them indispensable for modern electronic and electrical applications.
FAQs about Alumina (Al2O3) Ceramic Substrate
What is alumina (Al2O3) ceramic substrate?
Alumina ceramic substrate is a material composed primarily of aluminum oxide (Al2O3), known for its excellent thermal conductivity, electrical insulation, mechanical strength, and chemical resistance. It is widely used in electronic and electrical applications for mounting and interconnecting components.
What are the advantages of alumina ceramic substrates?
Alumina ceramic substrates offer high thermal conductivity, superb electrical insulation, mechanical durability, chemical resistance, and dimensional stability. These properties make them ideal for applications requiring efficient heat dissipation, electrical isolation, and reliability in harsh environments.
What are the main applications of alumina ceramic substrates?
Alumina ceramic substrates find applications in various industries, including electronics (ICs, LEDs, power modules), semiconductor manufacturing, LED packaging, sensor technology, medical devices, aerospace and defense, high-frequency applications (RF/microwave), and consumer electronics.
How are alumina ceramic substrates manufactured?
The fabrication process involves preparing alumina powder, forming it into the desired shape (via methods like pressing, injection molding, or extrusion), drying, and then sintering (firing) at high temperatures to achieve a dense ceramic structure. The substrates may undergo further processing for metallization and surface finishing.
What factors should be considered when designing with alumina ceramic substrates?
Design considerations include thermal management to optimize heat dissipation, mechanical design to minimize stress concentrations, ensuring adequate electrical isolation, choosing compatible metallization materials, maintaining dimensional stability, and considering environmental factors such as temperature and chemical exposure.
Are alumina ceramic substrates suitable for high-power applications?
Yes, alumina ceramic substrates are suitable for high-power applications due to their high thermal conductivity and ability to handle high voltage and current. They are used in power electronics, where efficient heat dissipation and electrical isolation are crucial.
What are the limitations of alumina ceramic substrates?
Although alumina ceramic substrates offer many advantages, they can be brittle and prone to cracking under mechanical stress if not properly handled. Their thermal conductivity, while high, is lower than some other ceramics like aluminum nitride (AlN), which may be preferred for certain high-power applications.
Can alumina ceramic substrates be customized for specific applications?
Yes, alumina ceramic substrates can be customized in terms of dimensions, shapes, surface finishes, and metallization patterns to meet specific application requirements. Customization allows for optimized performance and integration into various electronic and electrical devices.