ISOLA P95/P25 Substrate 生産者
ISOLA P95 / P25基板メーカー,ISOLA P95/P25 is a high-performance substrate material engineered for advanced PCB applications. It offers exceptional electrical properties, including a low dielectric constant and low dissipation factor, ensuring superior signal integrity and reduced signal loss. The substrate is known for its excellent thermal stability and mechanical strength, making it suitable for complex and high-layer-count circuit boards. ISOLA P95/P25 also provides reliable performance under high temperatures and thermal cycling, enhancing its durability in challenging environments. 通信に最適, 自動車, and high-speed digital systems, ISOLA P95/P25 combines robust performance with longevity, making it a preferred choice for sophisticated electronic designs.
とは ISOLA P95/P25 Substrate?
ISOLA P95/P25 is a high-performance substrate material designed for advanced PCB (Printed Circuit Board) アプリケーション, particularly in the realms of high-frequency and high-speed digital circuits. This material is part of ISOLA’s product line, known for its high quality and reliability in the electronics industry.
The ISOLA P95/P25 substrate is typically made from a proprietary resin system and reinforced with woven fiberglass. This combination provides exceptional electrical and mechanical properties, making it suitable for demanding applications. One of the key features of P95/P25 is its low dielectric loss tangent and low relative permittivity, which contribute to reduced signal loss and improved signal integrity. These properties are crucial in high-speed and high-frequency designs, where signal integrity is a major concern.
The substrate’s thermal performance is also noteworthy. It can handle high temperatures without significant degradation, ensuring the stability and longevity of the circuit board. This is particularly important in applications where the PCB may be subjected to extreme thermal conditions.
In terms of fabrication, the ISOLA P95/P25 material is designed to be compatible with standard PCB manufacturing processes. It offers good workability and ease of handling, which contributes to its adoption in various applications including telecommunications, 自動車用電子機器, and aerospace.
全, ISOLA P95/P25 is valued for its high-performance characteristics, including excellent electrical and thermal properties, making it a preferred choice for advanced electronic applications where reliability and performance are critical.
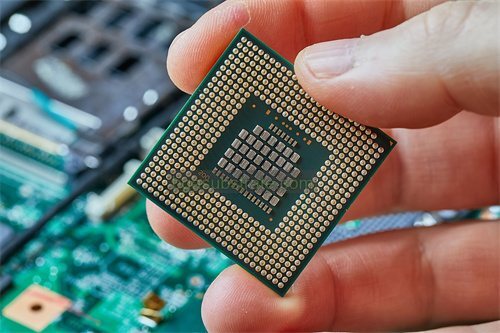
ISOLA P95 / P25基板メーカー
は何ですか ISOLA P95/P25 Substrate デザインガイドライン?
ザ ISOLA P95/P25 substrate design guidelines are essential for ensuring optimal performance and reliability in high-frequency and high-speed PCB applications. Adhering to these guidelines helps in maximizing the benefits of the substrate material and achieving the desired electrical and thermal performance. Here are key design guidelines for ISOLA P95/P25 substrates:
- 1. シグナルインテグリティ:Due to the low dielectric loss tangent and low relative permittivity of P95/P25, it is crucial to design trace widths and spacings accurately to minimize signal attenuation and crosstalk. Use controlled impedance traces and proper via design to maintain signal integrity.
- サーマルマネジメント: While P95/P25 has good thermal performance, it’s important to design adequate heat dissipation mechanisms into the PCB layout. Ensure proper heat sinking and thermal vias to manage heat effectively, 特にハイパワーアプリケーションの場合.
- Stackup Design: Carefully plan the PCB stackup to optimize the electrical performance. The use of multiple layers with appropriate dielectric thicknesses can help in managing signal integrity and controlling impedance.
- Via Design: 高周波アプリケーション向け, minimize the use of through-hole vias and consider using blind or buried vias to reduce signal loss and improve performance. Ensure that vias are properly plated and have good electrical connection.
- Manufacturing Processes: Follow recommended fabrication processes for ISOLA P95/P25 substrates to ensure quality and performance. This includes proper cleaning and handling to avoid contamination that could affect the substrate’s properties.
- テストと検証:Perform thorough testing and validation of the PCB design to verify performance and compliance with the intended application requirements. This includes signal integrity testing, thermal performance evaluation, and reliability assessments.
- 組み立てのための設計: Consider the thermal expansion properties of P95/P25 during the design phase to avoid issues with component soldering and board warping. Ensure that components are mounted securely and that the PCB can withstand thermal cycles during operation.
これらの設計ガイドラインに従う, you can leverage the high-performance characteristics of ISOLA P95/P25 substrates to create reliable and efficient PCBs for advanced electronic applications.
の利点 ISOLA P95/P25 Substrate
ザ ISOLA P95/P25 substrate offers several advantages that make it highly suitable for advanced PCB (Printed Circuit Board) アプリケーション, particularly in high-frequency and high-speed environments. Here are the key benefits of using ISOLA P95/P25 substrates:
- Low Dielectric Loss Tangent: ISOLA P95/P25 has a low dielectric loss tangent, which minimizes signal attenuation and improves signal integrity. This is crucial for high-speed and high-frequency applications where maintaining signal quality is essential.
- Low Relative Permittivity: The substrate features a low relative permittivity, which helps in controlling impedance and reducing signal distortion. This property is beneficial for maintaining consistent electrical performance across high-frequency circuits.
- Excellent Thermal Performance: The substrate can handle high temperatures without significant degradation, providing stability and reliability in thermally demanding applications. Its good thermal conductivity helps in efficient heat dissipation.
- 高い機械的強度: Reinforced with woven fiberglass, ISOLA P95/P25 offers robust mechanical properties, enhancing the durability and structural integrity of the PCB. This is particularly important for applications requiring high mechanical reliability.
- Compatibility with Standard Processes: ISOLA P95/P25 is designed to be compatible with standard PCB manufacturing processes. This ensures ease of fabrication and integration into existing production workflows.
- Enhanced Electrical Performance: The substrate’s combination of low dielectric loss and low relative permittivity leads to better electrical performance, including reduced signal loss and improved signal-to-noise ratio.
- Reliability and Longevity: The material’s resistance to thermal and mechanical stresses contributes to the overall reliability and longevity of the PCB. This makes it a suitable choice for demanding environments, 電気通信を含む, 航宇, and automotive applications.
- 万芸: ISOLA P95/P25 can be used in a wide range of applications, from high-speed digital circuits to high-frequency RF designs. Its versatile nature makes it a valuable option for various electronic systems.
全, the advantages of ISOLA P95/P25 substrate make it a preferred choice for applications requiring high performance, 確実, and durability in electronic circuits.
は何ですか ISOLA P95/P25 Substrate 製作プロセス?
The fabrication process for ISOLA P95/P25 substrates involves several key steps to ensure high-quality and reliable Printed Circuit Boards (プリント基板). Here is an overview of the typical fabrication process for ISOLA P95/P25 substrates:
- 材料の準備: The process begins with the preparation of ISOLA P95/P25 laminate sheets. These sheets are composed of a resin system and woven fiberglass reinforcement. The laminate is available in various thicknesses and is cut to the required dimensions for the PCB.
- Laminate Cleaning: Prior to processing, the laminate sheets are cleaned to remove any contaminants or particles that could affect the adhesion of subsequent layers. This step ensures a clean surface for optimal bonding.
- Layer Printing and Patterning: The next step involves printing the circuit patterns onto the laminate. This is typically done using photolithographic techniques. A photosensitive layer is applied to the laminate, and the desired circuit patterns are transferred using UV light and a photomask. The unexposed areas are then removed, leaving the circuit pattern.
- エッチング: The exposed copper is etched away to create the desired circuit pattern. This is done using chemical etchants that remove the unwanted copper, leaving behind the circuit traces as defined in the design.
- Layer Bonding:多層PCB用, multiple layers of the patterned laminate are stacked together. These layers are bonded using heat and pressure in a lamination press. The bonding process ensures that the layers are firmly attached and that the circuit connections between layers are established.
- 穴あけとメッキ: Holes are drilled into the PCB for component mounting and inter-layer connections. These holes are then plated with copper to create electrical connections between different layers of the PCB.
- 表面仕上げ: After drilling and plating, the PCB undergoes surface finishing to protect the copper and enhance solderability. Common finishing methods include HASL (熱風はんだレベリング), エニグ (無電解ニッケル浸漬金), and OSP (有機はんだ付け性防腐剤).
- テストと検査: The fabricated PCB is thoroughly tested and inspected to ensure it meets the design specifications and quality standards. これには電気試験が含まれます, visual inspection, and reliability assessments.
- Cutting and Final Assembly: The finished PCB is cut to the final dimensions and prepared for assembly. Components are mounted and soldered onto the PCB according to the design requirements.
- 品質管理: 製造プロセス全体を通して, quality control measures are implemented to monitor and ensure the integrity and performance of the ISOLA P95/P25 substrates.
次の手順に従います, the ISOLA P95/P25 substrate fabrication process ensures the production of high-performance PCBs with excellent electrical and thermal characteristics.
セラミックの応用 ISOLA P95/P25 Substrate
The ISOLA P95/P25 substrate, though primarily known for its use in high-frequency and high-speed PCB applications, can also be used in conjunction with ceramic materials in specific scenarios where enhanced performance characteristics are required. Here’s a detailed look at the applications of ceramic ISOLA P95/P25 substrates:
- High-Frequency RF Applications: Ceramic ISOLA P95/P25 substrates are well-suited for high-frequency radio frequency (RFの) applications due to their low dielectric loss tangent and low relative permittivity. These properties help in maintaining signal integrity and minimizing signal attenuation, which is critical in RF circuit designs used in telecommunications and broadcasting.
- マイクロ波回路: In microwave circuit applications, where signal frequencies can be extremely high, the use of ceramic ISOLA P95/P25 substrates ensures reliable performance by minimizing signal loss and distortion. This is essential for applications such as radar systems and satellite communications.
- カーエレクトロニクス: In automotive electronics, the durability and thermal stability of ceramic ISOLA P95/P25 substrates make them suitable for applications that require high thermal resistance and reliability. This includes components in advanced driver assistance systems (ADASの), インフォテインメントシステム, and power management circuits.
- 航空宇宙・防衛: For aerospace and defense applications, where performance and reliability are paramount, ceramic ISOLA P95/P25 substrates provide excellent electrical and thermal properties. それらはアビオニクスで使用されます, 通信システム, and other critical electronics where performance under extreme conditions is required.
- High-Power Electronics: The thermal conductivity of ceramic ISOLA P95/P25 substrates helps in managing heat dissipation in high-power electronic devices. This is important for power amplifiers, 電力変換器, and other high-power applications where efficient heat management is essential to prevent overheating and ensure long-term reliability.
- 医療機器:医療用電子機器, where precision and reliability are crucial, ceramic ISOLA P95/P25 substrates offer stability and performance. They are used in diagnostic equipment, monitoring systems, and other medical devices that require high-frequency signal processing and thermal management.
- 産業機器: Ceramic ISOLA P95/P25 substrates are also applied in industrial equipment where robustness and high performance are necessary. This includes control systems, センサー, and automated machinery that operate under demanding conditions.
- High-Speed Digital Circuits: For high-speed digital circuits, the substrate’s low dielectric loss and controlled impedance contribute to improved signal integrity and reduced signal degradation, which is critical for data processing and communication systems.
まとめ, ceramic ISOLA P95/P25 substrates are utilized in a variety of advanced electronic applications where their superior electrical, 熱の, and mechanical properties can enhance performance and reliability.
に関するFAQ ISOLA P95/P25 Substrate
What are the key benefits of using ISOLA P95/P25?
The key benefits include low signal attenuation, excellent thermal performance, high mechanical strength, 標準のPCB製造プロセスとの互換性. It is suitable for demanding applications in telecommunications, 航宇, 自動車, and more.
What types of applications are suitable for ISOLA P95/P25 substrates?
ISOLA P95/P25 substrates are ideal for high-frequency RF circuits, マイクロ波回路, 自動車用電子機器, aerospace and defense applications, high-power electronics, 医療機器, and high-speed digital circuits.
How does ISOLA P95/P25 compare to other substrates?
Compared to standard FR4 substrates, ISOLA P95/P25 offers superior electrical performance with lower dielectric loss and better thermal management. It is more suitable for high-speed and high-frequency applications where signal integrity and thermal stability are critical.
What is the typical fabrication process for ISOLA P95/P25 substrates?
製造プロセスには、材料の準備が含まれます, 清掃, layer printing and patterning, エッチング, layer bonding, drilling and plating, 表面仕上げ, 試験と検査, そして最終組み立て.
How do I ensure proper performance with ISOLA P95/P25 substrates?
To ensure optimal performance, follow design guidelines such as maintaining accurate trace widths and spacings, 熱放散の管理, 効果的なビア構造の設計, and conducting thorough testing and validation.
Is ISOLA P95/P25 compatible with standard PCB manufacturing processes?
はい, ISOLA P95/P25 substrates are designed to be compatible with standard PCB manufacturing processes, making them easy to integrate into existing production workflows.