FCCSP Substrate 生産者
FCCSP基板メーカー,Flip Chip Chip Scale Package (FCCSP) substrates are advanced packaging solutions that provide a compact and efficient method for integrating semiconductor chips into electronic devices. FCCSP substrates are designed to support flip chip technology, where the chip is flipped and bonded directly onto the substrate using solder bumps. This packaging method offers excellent electrical performance, enhanced heat dissipation, and reduced package size, making it ideal for high-density and high-performance applications. FCCSP substrates are commonly used in mobile devices, ウェアラブル, and other compact electronics where space and performance are critical. Their robust design ensures reliable signal integrity and thermal management.
とは FCCSP Substrate?
FCCSP (Fine-Pitch Chip Scale Package) substrate is a type of semiconductor packaging used for integrated circuits (ICの). It is a variant of chip scale packaging that offers a compact and high-density solution, particularly beneficial for applications where space and performance are critical.
The FCCSP substrate typically features a fine-pitch ball grid array (BGAの) structure, where solder balls are arranged in a grid pattern underneath the package, allowing for a higher density of connections compared to traditional packages. This configuration facilitates better electrical performance and thermal dissipation, which are crucial for high-speed and high-power ICs.
The substrate itself is often made from materials such as FR4 (a type of fiberglass epoxy laminate) or more advanced materials like BT (Bismaleimide-Triazine) resin, depending on the performance requirements. The choice of substrate material affects the thermal conductivity, 機械的強度, and electrical characteristics of the final package.
FCCSP substrates are designed with multiple layers to include signal routing, 配電, and grounding planes, all of which contribute to the overall performance and reliability of the package. These layers are carefully engineered to ensure minimal signal interference and optimal thermal management.
まとめ, FCCSP substrates are crucial for modern electronics, providing a high-density, 効率的, and reliable packaging solution that meets the demands of advanced semiconductor devices.
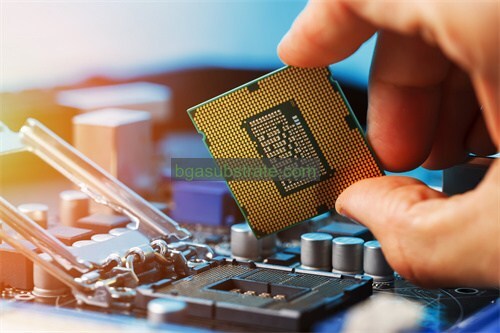
FCCSP基板メーカー
は何ですか FCCSP Substrate デザインガイドライン?
FCCSP (Fine-Pitch Chip Scale Package) 基板 design guidelines are essential for ensuring the performance, 確実, and manufacturability of the final semiconductor package. ここでは、設計上の重要な考慮事項をいくつか紹介します:
- Substrate Material Selection: Choose appropriate substrate materials based on the thermal, メカニカル, and electrical requirements of the application. 一般的な材料にはFR4が含まれます, BT (Bismaleimide-Triazine) resin, and advanced ceramics, each offering different properties such as thermal conductivity and dielectric constant.
- レイヤースタックアップ: Design the substrate with an optimal layer stackup to accommodate signal routing, 配電, and grounding. Ensure that the stackup supports the necessary electrical performance and thermal management. 通常, the stackup includes layers for signal traces, power planes, and ground planes.
- ボールグリッドアレイ (BGAの) Layout: Plan the BGA layout carefully to accommodate the fine-pitch design. The spacing and placement of solder balls should be optimized to ensure reliable connections and avoid issues such as solder bridging or misalignment.
- サーマルマネジメント: Implement effective thermal management strategies to dissipate heat generated by the IC. This may involve using heat spreaders, サーマルビア, or dedicated thermal pads to ensure the package operates within safe temperature limits.
- シグナルインテグリティ:Maintain signal integrity by designing trace routings with appropriate widths and spacing. Minimize signal interference and crosstalk by following best practices for high-speed signal routing, including impedance control and proper grounding.
- 製造に関する考慮事項: 標準的な製造プロセスと互換性を持つように基板を設計する, エッチングを含む, 鍍金, and solder mask application. Ensure that the design allows for easy alignment and assembly during the production phase.
- 信頼性試験: Include design features that facilitate reliability testing, such as test pads or inspection areas. Perform thorough testing to identify potential issues related to thermal cycling, mechanical stress, および電気的性能.
これらの設計ガイドラインに従うことにより、, FCCSP substrates can achieve high performance and reliability, meeting the demanding requirements of modern semiconductor applications.
の利点 FCCSP Substrate
FCCSP (Fine-Pitch Chip Scale Package) 基板 offer several advantages that make them a popular choice in advanced semiconductor packaging. 主な利点は次のとおりです:
- Compact Size: FCCSP substrates are designed to be smaller and more compact than traditional packages. This fine-pitch, chip-scale approach reduces the overall footprint of the package, making it ideal for space-constrained applications.
- High Density: The fine-pitch ball grid array (BGAの) layout used in FCCSP substrates allows for a higher density of connections. This enables more I/O pins in a smaller area, which is beneficial for high-performance ICs requiring numerous connections.
- 電気的性能の向上: The design of FCCSP substrates includes optimized signal routing and reduced parasitics, which enhances electrical performance. This is particularly important for high-speed and high-frequency applications, where signal integrity is crucial.
- 強化された熱管理: FCCSP substrates often incorporate features such as thermal vias or heat spreaders to improve thermal dissipation. This helps in managing the heat generated by the IC, contributing to better performance and longevity.
- Reduced Package Warping: The use of high-quality substrate materials and precise manufacturing processes in FCCSP substrates reduces the risk of package warping. This ensures better alignment and reliability during assembly and operation.
- Cost-Effective: Despite the advanced design, FCCSP substrates can be cost-effective compared to other high-density packaging options. Their compact size and efficient use of materials can lead to lower overall packaging costs.
- Manufacturing Compatibility: FCCSP substrates are compatible with standard manufacturing processes, making them easier to produce and assemble. This compatibility helps streamline production and reduce manufacturing complexities.
まとめ, FCCSP substrates offer a combination of compact size, high density, 電気的および熱的性能の向上, そして費用対効果, making them a valuable choice for modern semiconductor packaging needs.
は何ですか FCCSP Substrate 製作プロセス?
The FCCSP (Fine-Pitch Chip Scale Package) substrate fabrication process involves several critical steps to ensure the performance and reliability of the final package. ここでは、一般的なプロセスの概要を示します:
- デザインとレイアウト: The process begins with designing the FCCSP substrate layout. This involves defining the ball grid array (BGAの) pattern, signal traces, power planes, and grounding planes. The design must consider electrical performance, サーマルマネジメント, と製造可能性.
- 材料の準備: Select and prepare substrate materials, which may include FR4, BT樹脂, or other advanced materials. The choice of material affects the thermal, メカニカル, and electrical properties of the substrate.
- Photoresist Coating: Apply a photoresist layer onto the substrate material. This photoresist layer is used to define the areas that will be etched away during the manufacturing process. The coating ensures precise patterning for circuitry and other features.
- 写真石版: Use photolithography to transfer the substrate design onto the photoresist layer. This involves exposing the photoresist to ultraviolet (紫外線) light through a photomask, which creates a pattern that corresponds to the desired circuitry and features.
- エッチング: Perform etching to remove the unprotected areas of the substrate material. This step creates the necessary circuitry and features on the substrate. Both wet and dry etching methods may be used, depending on the material and design requirements.
- 鍍金: Deposit metal layers onto the substrate to form electrical connections and features. Plating involves electroplating or chemical plating techniques to apply metal such as copper to the substrate, creating the necessary conductive paths.
- ビアフォーメーション: Create vias, or vertical interconnections, through the substrate layers. These vias connect different layers of the substrate and enable electrical connections between them. Techniques like laser drilling or mechanical drilling are used to form vias.
- ソルダーマスクアプリケーション: Apply a solder mask to protect areas of the substrate where solder should not be applied. The solder mask also helps prevent solder bridging and short circuits during the assembly process.
- Ball Placement: Attach solder balls to the substrate’s BGA pattern. These solder balls serve as the electrical interface between the substrate and the printed circuit board (プリント基板) or other components. Placement accuracy is crucial to ensure reliable connections.
- Curing and Testing: Cure the substrate to solidify any applied materials and ensure proper adhesion. Conduct thorough testing to check for defects, 電気的性能, と信頼性. This includes inspecting solder ball placement and checking for any manufacturing issues.
- 最終検査と梱包: Perform a final inspection to ensure the FCCSP substrate meets all design specifications and quality standards. Package the substrates for shipment or further assembly with semiconductor chips.
まとめ, the FCCSP substrate fabrication process involves a series of steps including design, material preparation, photoresist coating, 写真石版, エッチング, 鍍金, ビアフォーメーション, ソルダーマスクアプリケーション, ball placement, 硬化, テスティング, そして最終点検. Each step is crucial for achieving the high performance and reliability required for fine-pitch chip scale packages.
セラミックの応用 FCCSP Substrate
Ceramic FCCSP (Fine-Pitch Chip Scale Package) substrates are used in various advanced electronic applications due to their superior properties. 主なアプリケーションは次のとおりです:
- ハイパフォーマンスコンピューティング: Ceramic FCCSP substrates are widely used in high-performance computing devices such as servers and processors. Their excellent thermal conductivity and electrical performance help manage heat dissipation and ensure stable operation of high-speed processors.
- 電気通信: 通信機器, ceramic FCCSP substrates provide reliable performance for high-frequency signals and data transmission. Their low dielectric loss and high signal integrity make them ideal for use in RF (無線周波数) およびマイクロ波アプリケーション.
- 家電: Ceramic FCCSP substrates are utilized in consumer electronics like smartphones, 錠剤, およびウェアラブル. Their compact size and high density support the miniaturization of devices while maintaining high performance and reliability.
- カーエレクトロニクス: 自動車業界, ceramic FCCSP substrates are employed in various applications, including advanced driver assistance systems (ADASの), インフォテインメントシステム, およびエンジン制御ユニット (ECU(エキュエート). Their robustness and thermal stability ensure reliable performance under harsh operating conditions.
- 航空宇宙・防衛: The aerospace and defense sectors benefit from ceramic FCCSP substrates due to their high reliability and resistance to extreme temperatures and radiation. それらはアビオニクスで使用されます, サテライトシステム, and other mission-critical applications where performance and durability are paramount.
- 医療機器: Ceramic FCCSP substrates are used in medical devices and equipment due to their biocompatibility and stability. Applications include medical imaging systems, 診断機器, および埋め込み型デバイス, where precision and reliability are essential.
- パワーエレクトロニクス: パワーエレクトロニクス, ceramic FCCSP substrates help manage heat and provide high reliability for power converters, インバーター, and other power management systems. Their thermal conductivity and mechanical strength are crucial for handling high power levels and maintaining performance.
まとめ, ceramic FCCSP substrates are applied in a wide range of fields, including high-performance computing, 電気通信, 家電, 自動車システム, 航空宇宙および防衛, 医療機器, およびパワーエレクトロニクス. Their advantages, such as high thermal conductivity, 電気的性能, と機械的強度, make them suitable for demanding and high-reliability applications.
に関するFAQ FCCSP Substrate
What are the advantages of FCCSP substrates?
FCCSP substrates offer a compact size, high density of connections, 電気的性能の向上, 強化された熱管理, reduced package warping, そして費用対効果.
What materials are used for FCCSP substrates?
一般的な材料にはFR4が含まれます (fiberglass epoxy), BT樹脂 (Bismaleimide-Triazine), and advanced ceramics. The choice depends on the specific requirements for thermal conductivity, 電気的性能, と機械的強度.
How is the FCCSP substrate fabricated?
The fabrication process involves designing the substrate layout, applying photoresist, 写真石版, エッチング, 鍍金, ビアの形成, applying solder masks, はんだボールの配置, and performing curing and testing.
What are the typical applications of FCCSP substrates?
FCCSP substrates are used in high-performance computing, 電気通信, 家電, 自動車システム, 航空宇宙および防衛, 医療機器, およびパワーエレクトロニクス.
What is the difference between FCCSP and other chip scale packages?
FCCSP offers a finer pitch ball grid array compared to some other chip scale packages, allowing for higher density and improved performance. It is designed to be more compact and provide better thermal and electrical characteristics.
How do FCCSP substrates handle heat?
FCCSP substrates are designed with features like thermal vias or heat spreaders to manage heat dissipation effectively, ensuring that the IC operates within safe temperature limits.