キャビティPCBとは?
キャビティPCBメーカー,キャビティPCB, 組み込みPCBとも呼ばれます, ボード自体に統合されたカットアウトまたはキャビティを特徴としています, ハウジングコンポーネントまたはモジュール. この革新的な設計アプローチにより、省スペースの利点が得られます, より高い部品密度と基板スペースのより効率的な使用を可能にします. かつ, キャビティPCBは、コンポーネントをボードの表面の近くに配置することにより、熱管理を強化します, 放熱性の向上. ハウジングコンポーネントの信頼性と保護の向上, キャビティPCBは、自動車などの業界で使用されています, 航宇, 家電, および医療機器, コンパクトさ, パフォーマンス, そして耐久性は最優先事項です.
キャビティPCB, 組み込みPCBまたはキャビティボードとも呼ばれます, プリント回路基板を参照してください (プリント基板) ボード自体に空洞や切り欠きがあるもの. これらのキャビティは、コンポーネントを収容するために使用できます, コネクタ, あるいは他の電子モジュール. この設計アプローチには、いくつかの利点があります.
第一に, キャビティPCBにより、よりコンパクトで合理化された設計が可能になります, より高い部品密度と電子機器内のスペースのより効率的な使用を可能にします. コンポーネントをPCBに直接統合する, メーカーは、デバイスの全体的な設置面積を削減できます, これは、サイズと重量が重要な要素であるアプリケーションに特に有益です.
第二に, キャビティPCBは、コンポーネントをボードの表面の近くに配置できるようにすることで、熱管理を改善するのに役立ちます, ヒートシンクやサーマルビアなどの放熱メカニズムをより効果的に利用できる場所. これにより、電子システムの信頼性とパフォーマンスを向上させることができます, 特に、高電力アプリケーションやエアフローが限られている環境で.
かつ, キャビティPCBは、敏感なコンポーネントをボード自体に囲むことにより、保護を強化します, ほこりなどの外部環境要因からそれらを保護, 湿気, または機械的衝撃. これにより、電子機器の耐久性と寿命の向上に貢献することができます.
全, キャビティPCBは、PCB設計に対する汎用性の高い革新的なアプローチを表しています, スペース効率の面で多くの利点を提供します, サーマルマネジメント, およびコンポーネント保護. しかし, それらは特殊な製造プロセスを必要とする可能性があり、従来のPCBと比較してより高い製造コストが発生します, これは、設計および製造段階で考慮する必要があります.
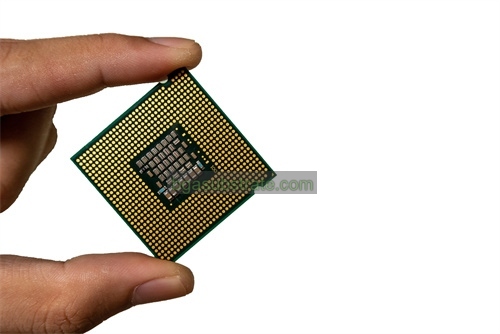
キャビティPCBメーカー
キャビティPCB設計ガイドラインとは?
キャビティPCBを設計するには、最適な性能と製造性を確保するために、いくつかの要素を慎重に検討する必要があります. ここでは、いくつかの主要なガイドラインを示します:
- キャビティのサイズと形状: キャビティの寸法と形状は、キャビティが収容するコンポーネントまたはモジュールに基づいて決定します. キャビティがコンポーネントを快適に収容するのに十分な大きさであることを確認しながら、電気的干渉や機械的な衝突を防ぐために十分なクリアランスを維持します.
- キャビティ配置: PCBレイアウト内にキャビティを戦略的に配置して、信号配線の複雑さを最小限に抑え、基板スペースを効率的に使用できるようにします. シグナルインテグリティなどの要素を考慮する, サーマルマネジメント, 組み立てとサービスのためのアクセシビリティ.
- キャビティの深さ: キャビティに含まれるコンポーネントの高さと、組み立ておよびはんだ付けプロセスのための追加のクリアランス要件に基づいて、キャビティの深さを決定します. 深さが、隣接する層との干渉を引き起こしたり、構造的完全性を損なったりすることなく、最も背の高いコンポーネントを収容するのに十分な深さであることを確認してください.
- キャビティ肉厚: キャビティの壁を十分な厚さで設計し、内部に取り付けられたコンポーネントの機械的安定性とサポートを提供します. PCB基板の材料特性と追加の補強技術を検討してください, キャビティをエポキシや樹脂で充填するなど, 構造的完全性を高めるため.
- キャビティエッジクリアランス: キャビティの端の周りに適切なクリアランスを維持して、組み立て中の電気的短絡や機械的損傷を防ぎます, 取り扱い, と操作. PCBエッジクリアランスの標準設計ルールに従い、面取りやフィレットなどの保護機能を組み込んで応力集中を減らすことを検討してください.
- 信号配線とグランドプレーン: キャビティの周囲に信号トレースとグランドプレーンを配置する計画を立てて、信号の干渉を最小限に抑え、信号の完全性を確保します. 適切な信号リターンパスとインピーダンスマッチングの考慮事項を維持する, 特に、キャビティ内に収納された高速または高周波の部品の近く.
- サーマルマネジメント: キャビティ設計が熱管理要件に与える影響を考慮する. キャビティ内のコンポーネントから発生する熱を効果的に放散するために、十分なエアフローまたはサーマルビアを確保します. 最適な動作温度を維持するために、必要に応じてサーマルリリーフとヒートシンクを備えたPCBを設計します.
- 組み立てと製造に関する考慮事項: キャビティPCB設計の製造可能性を評価, ソルダーマスクのアライメントなどの要素を考慮する, コンポーネント配置精度, 検査と手直しのためのアクセシビリティ. PCB製造およびアセンブリパートナーと緊密に協力して、キャビティ設計に関連する特定のプロセス要件または制限に対処します.
これらの設計ガイドラインに従うことにより、, エンジニアは、効率的な製造および組み立てプロセスを促進しながら、性能目標を達成するキャビティPCBを開発できます. 定期的な設計レビューと関係者とのコラボレーションは、設計サイクルの早い段階で潜在的な問題を特定し、対処するのに役立ちます, 電子システムへのキャビティPCBの実装を成功させる.
キャビティPCBの利点
キャビティPCBは、従来のPCB設計に比べていくつかの利点があります, さまざまな電子アプリケーションにとって魅力的なオプションとなっています:
- スペース効率: キャビティやカットアウトを介してコンポーネントをPCBに直接統合します, キャビティPCBは、従来の表面実装コンポーネントと比較して、よりコンパクトでスペース効率の高い設計を実現できます. これにより、部品密度が高くなり、利用可能な基板スペースをより効率的に使用できます, キャビティPCBを小型化またはスペースに制約のある電子機器に最適に.
- 熱管理の改善: キャビティPCBにより、コンポーネントをボードの表面の近くに配置できます, ヒートシンクなどの熱管理メカニズム, サーマルビア, または、気流をより効果的に利用することができます. これにより、熱放散と熱伝導が向上します, 過熱のリスクを減らし、電子システムの全体的な信頼性と性能を向上させます.
- シグナルインテグリティの向上: PCB基板内に部品を埋め込む, キャビティPCBは、信号ルーティングの複雑さを最小限に抑え、信号トレースの長さを短縮できます, シグナルインテグリティの向上と電磁干渉の低減につながります (EMIの). これは、シグナルインテグリティが重要な高速または高周波アプリケーションにとって特に有利です.
- コンポーネント保護: キャビティPCBは、敏感なコンポーネントをボード自体に封入することにより、保護を強化します, ほこりなどの外部環境要因からそれらを保護, 湿気, または機械的衝撃. これにより、電子機器の耐久性と寿命の向上に貢献することができます, 特に過酷な動作環境での対応.
- 機械的安定性: PCB内にキャビティが存在すると、その機械的安定性と剛性が向上します, 取り扱い中に曲がったり曲がったりするリスクを軽減, 集会, または操作. これにより、電子システムの全体的な堅牢性と耐久性を向上させることができます, 機械的ストレスや振動に対する耐性を高める.
- 合理化された組み立て: キャビティPCBは、コンポーネントをボードに直接統合することにより、組み立てプロセスを簡素化できます, 追加の取り付けハードウェアや二次的な組み立てステップの必要性を削減. これにより、組み立て時間が短縮されます, 生産コストの削減, 全体的な製造効率の向上.
- 設計の柔軟性: キャビティPCBは、設計の柔軟性を高めます, エンジニアが形状をカスタマイズできるようにする, 大きさ, 電子システムの特定の要件に応じたキャビティの配置. この柔軟性により、革新的な設計ソリューションが可能になり、コンパクトなフォームファクタ内での複雑な機能の統合が容易になります.
全, キャビティPCBの利点により、キャビティPCBは幅広い電子アプリケーションに対応する用途が広く効果的なソリューションになります, 民生用電子機器や電気通信から自動車や航空宇宙システムまで、さまざまな分野で活躍しています. 省スペースの利点を活用することで, 熱管理の改善, キャビティPCBによって提供される信頼性の向上, デザイナーはよりコンパクトに作成できる, 効率的, および堅牢な電子デバイス.
キャビティPCB製造プロセスとは?
キャビティPCBの製造プロセスには、いくつかのステップが含まれます, それぞれが、ボード内にキャビティを作成し、コンポーネントを効果的に統合するために重要です. キャビティPCB製造プロセスの一般的な概要は次のとおりです:
- 設計フェーズ: このプロセスは、PCBレイアウトの設計から始まります, キャビティの配置と寸法を含む. Altium Designerなどの設計ソフトウェア, 鷲, または、KiCad がこの目的のために一般的に使用されます. エンジニアがサイズを指定します, 形, キャビティ内に収納されるコンポーネントおよびその他の設計要件に基づくキャビティの位置.
- 基板選択: 熱伝導率などの要因に基づいて、PCBに適した基板材料を選択してください, 機械的強度, および誘電特性. キャビティPCBの一般的な基板材料には、FR-4が含まれます, 高温ラミネート, または、熱管理を強化するために設計された特殊材料.
- キャビティの作成: キャビティは通常、フライス盤などの高度な機械加工技術を使用してPCB製造プロセス中に作成されます, ルーティング, またはレーザーアブレーション. CNCの (コンピュータ数値制御) 機械は、設計仕様に従ってキャビティを正確に切断するためによく使用されます. PCBの構造的完全性を損なうことなく、キャビティが正確に配置され、コンポーネントを収容するように寸法が調整されるように注意する必要があります.
- レイヤースタッキング: 空洞が作成されたら, PCBの個々の層は、熱と圧力を使用して積み重ねられ、ラミネートされて単一の層を形成します, 凝集構造. キャビティ層はPCBの他の層と位置合わせされ、キャビティ内のコンポーネントの適切な位置合わせと位置合わせが保証されます.
- 銅蒸着とエッチング: 銅のトレースとパッドは、電気めっきや化学堆積などの技術を使用してPCBの表面に堆積されます. 銅の層は、ボードの表面全体に均一に適用されます, キャビティ内を含む. 次に、フォトリソグラフィーとエッチングプロセスを使用して、余分な銅を選択的に除去し、目的の回路パターンを定義します.
- 6. 部品実装: 表面実装およびスルーホールコンポーネントは、自動ピックアンドプレースマシンまたは手動組み立て技術を使用してPCBに取り付けられます. キャビティ内に収納されるコンポーネントは、それぞれのキャビティに配置されます, 適切な位置合わせとクリアランスの確保.
- はんだ付けと組み立て: すべてのコンポーネントが配置されたら, PCBは、コンポーネントとPCBトレース間の電気的接続を確立するために、はんだ付けプロセスを経ます. これには、リフローはんだ付けが含まれる場合があります, ウェーブはんだ付け, または、設計の特定の要件に応じた手はんだ付け技術. 追加の組み立て手順, コンフォーマルコーティングやポッティングなど, コンポーネントを保護し、信頼性を高めるために実行できます.
- テストと検査: 完成したPCBは、機能を確認するために厳格なテストと検査を受けます, 電気的導通, 品質基準の遵守. 自動試験装置と目視検査方法は、修正が必要な欠陥や異常を特定するために一般的に使用されます.
- 最終仕上げ: テストが完了したら, PCBは、表面仕上げアプリケーションなどの最終仕上げプロセスを受けます, エッジメッキ, とラベリング. これらの仕上げ工程により、耐久性が向上します, 耐食性, PCBのはんだ付け性, 最終的な電子アセンブリに統合するための準備.
次の手順に従います, メーカーは、さまざまな電子アプリケーションの設計要件と性能の期待を満たすキャビティPCBを製造できます. 設計エンジニア間の緊密な連携, PCBファブリケーター, また、組み立てパートナーは、スムーズで成功した製造プロセスを確保するために不可欠です.
キャビティPCBの応用
キャビティPCBは、スペース効率が優れたさまざまな業界や電子機器に応用されています, サーマルマネジメント, およびコンポーネントの保護は重要な考慮事項です. 一般的なアプリケーションには、次のようなものがあります:
- モバイルデバイス: キャビティPCBはスマートフォンで広く使用されています, 錠剤, また、プロセッサなどの必要なコンポーネントを収容しながらコンパクトなフォームファクタを実現するウェアラブルデバイスも搭載しています, メモリモジュール, とセンサー. キャビティPCBの省スペースの利点は、スリムで軽量なモバイルデバイスの設計において特に価値があります.
- カーエレクトロニクス: 自動車用途, キャビティPCBは、先進運転支援システムで利用されています (ADASの), インフォテインメントシステム, エンジンコントロールユニット (ECU(エキュエート), およびその他のオンボード電子機器. PCB内にコンポーネントを統合する機能は、スペースの最適化に貢献し、過酷な動作環境での信頼性を向上させます.
- 医療機器: キャビティPCBは、さまざまな医療機器や機器に採用されています, 患者モニタリングシステムを含む, 診断デバイス, および埋め込み型デバイス. キャビティPCBによって提供されるコンパクトな設計とコンポーネント保護は、高い信頼性を必要とする医療機器に有益です, 精度, と耐久性.
- 航空宇宙・防衛: キャビティPCBは、アビオニクスシステムなどの航空宇宙および防衛アプリケーションで使用されます, 衛星通信システム, およびレーダーシステム. 軽量, 嵳, また、キャビティPCBのスペース効率の高い設計により、航空宇宙および防衛電子機器に最適です, 信頼性とパフォーマンスが最優先される場所.
- インダストリアル・オートメーション: 産業オートメーションおよび制御システム, キャビティPCBは、プログラマブルロジックコントローラで利用されています (PLC), モータードライブ, ロボティックス, および監視機器. PCB内にコンポーネントを統合する機能は、スペースの最適化に貢献し、合理化された組み立ておよびメンテナンスプロセスを促進します.
- 家電: キャビティPCBは、幅広い家電製品に採用されています, スマートホームデバイスを含む, ゲーム機, オーディオ/ビデオ機器, とデジタルカメラ. キャビティPCBによって提供されるコンパクトな設計とコンポーネント保護は、家電製品の洗練された美観と耐久性の向上に貢献します.
- 電気通信: キャビティPCBは、通信インフラストラクチャで重要な役割を果たします, 基地局を含む, ルーター, スイッチ, および光ネットワーク機器. キャビティPCBの省スペースの利点と熱管理機能は、通信システムの信頼性とパフォーマンスを維持するために不可欠です.
- エネルギーシステム: キャビティPCBは、再生可能エネルギーシステムで利用されています, 電力変換器, およびエネルギー貯蔵システム. キャビティPCBのコンパクトな設計と熱管理機能は、エネルギー変換および貯蔵システムの効率と信頼性に貢献します.
全, 汎用性, スペース効率, サーマルマネジメント, キャビティPCBによって提供されるコンポーネント保護により、業界全体の幅広いアプリケーションに最適です, よりコンパクト化の発展に貢献, 頼もしい, 効率的な電子デバイスおよびシステム.
よくあるご質問(FAQ)
キャビティPCBの利点は何ですか?
キャビティPCBの利点には、スペース効率が含まれます, 熱管理の改善, シグナルインテグリティの向上, コンポーネント保護, 機械的安定性, 合理化された組み立て, 設計の柔軟性. これらの利点により、キャビティPCBはさまざまな電子アプリケーションに適しています.
キャビティPCBはどのように製造されますか?
キャビティPCBの製造プロセスには、いくつかのステップが含まれます, 基板選択を含む, 加工技術を用いたキャビティ作成, レイヤースタッキング, 銅蒸着とエッチング, 部品実装, はんだ付けと組み立て, 試験と検査, そして最終仕上げ. 設計エンジニアと製造パートナーとの緊密な協力関係は、製造を成功させるために不可欠です.
キャビティPCBの用途は何ですか?
キャビティPCBは、モバイルデバイスなどの業界全体でアプリケーションを見つけます, 自動車用電子機器, 医療機器, 航空宇宙および防衛, 産業オートメーション, 家電, 電気通信, およびエネルギーシステム. これらは、スペース効率の高いさまざまな電子機器やシステムで使用されています, サーマルマネジメント, そして、コンポーネントの保護が不可欠です.
キャビティPCBを設計する際に従うべき設計ガイドライン?
キャビティPCBの設計ガイドラインには、キャビティのサイズと形状に関する考慮事項が含まれます, キャビティ配置, キャビティの深さ, キャビティ壁の厚さ, キャビティエッジクリアランス, 信号ルーティングとグランドプレーン, サーマルマネジメント, 組み立てと製造に関する考慮事項. これらのガイドラインに従うことで、キャビティPCB設計の最適な性能と製造可能性が保証されます.
キャビティPCBは電子機器のスペース最適化にどのように貢献しますか?
キャビティPCBにより、コンポーネントをPCBに直接統合できます, 電子機器の全体的なフットプリントを削減し、部品密度の向上を実現. この省スペース設計アプローチは、サイズと重量の制約が重要な要素であるアプリケーションで特に価値があります.
キャビティPCBの設計と製造に関連する課題は何ですか?
キャビティPCBに関連する課題には、キャビティの設計と製造の複雑さが含まれます, シグナルインテグリティと熱管理に関する潜在的な問題, 特殊なプロセスによる製造コストの増加, また、特定の要件や制限に対処するために、設計エンジニアと製造パートナーとの緊密な協力が必要です.