Others High Frequency Substrate Fabricant
Autres fabricant de substrats haute fréquence,High Frequency Substrates encompass a diverse range of advanced materials tailored for RF and microwave applications. These substrates typically feature low dielectric constants and low loss tangents to ensure minimal signal attenuation and superior signal integrity. They are characterized by excellent thermal management properties, supporting reliable operation in demanding environments such as aerospace, télécommunication, and radar systems. High Frequency Substrates enable engineers to design intricate circuitry with precise electrical characteristics across a broad frequency spectrum. Their versatility and performance make them essential components in modern electronic systems where high-speed data transmission and signal reliability are paramount.
Quoi Others High Frequency Substrate?
“Others High Frequency Substrate” refers to high-frequency substrates that are not specifically categorized under well-known brand names like Rogers or Megtron. These substrates are designed for applications requiring excellent electrical performance at high frequencies, typically above 1 Ghz. They are used in RF (Radiofréquence) and microwave circuits where signal integrity, tangente à faible perte, and consistent dielectric properties are crucial. These substrates often feature specialized materials like PTFE (Polytétrafluoroéthylène) or ceramic-filled hydrocarbon resins. Engineers and designers choose these substrates for their ability to maintain signal integrity across a wide range of frequencies, making them ideal for radar systems, communications par satellite, and high-speed data transfer applications. Manufacturers of “Others High Frequency Substrates” emphasize customizability and performance consistency to meet stringent specifications in modern electronics.
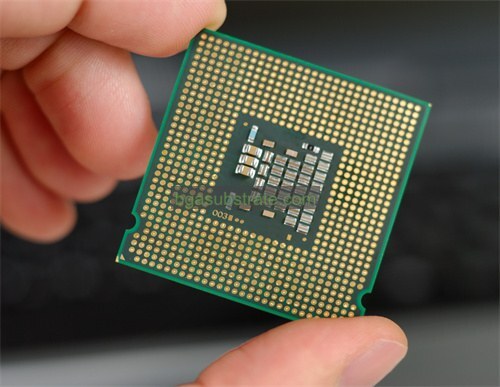
Autres fabricant de substrats haute fréquence
Qu’est-ce que le Others High Frequency Substrate Directives de conception?
Directives de conception pour “Others High Frequency Substrates” typically focus on achieving optimal performance in RF and microwave applications. Voici quelques considérations clés en matière de conception:
- Sélection des matériaux:Choose a substrate material that matches the specific RF performance requirements, tels qu’une faible constante diélectrique (εr) et faible facteur de dissipation (δ beige). Materials like PTFE-based or ceramic-filled hydrocarbon resins are common choices for their stable electrical properties over a wide frequency range.
- Constante diélectrique (εr) and Loss Tangent (δ beige): Ensure the substrate material has a well-characterized and stable dielectric constant and loss tangent across the frequency spectrum of interest. This helps in maintaining signal integrity and minimizing signal loss.
- Thickness:The substrate thickness influences the characteristic impedance of transmission lines. Design the substrate thickness according to the desired impedance matching requirements of the RF circuit.
- Copper Cladding Thickness: Select an appropriate copper thickness for the conductive layers based on the current-carrying capacity and skin effect at high frequencies. Thicker copper layers reduce resistance and improve signal conductivity.
- Finition de surface: Choose a suitable surface finish that ensures good solderability and minimizes surface roughness for high-frequency applications. ENIG (Nickel autocatalytique par immersion d’or) ou OSP (Organic Solderability Preservatives) are commonly used finishes.
- Via Design: Optimize via structures and placements to minimize impedance mismatch and signal reflections. Consider using blind or buried vias to reduce parasitic effects and maintain signal integrity.
- Gestion thermique: Ensure the substrate can dissipate heat efficiently, especially in power amplifiers and high-power RF circuits. Consider thermal vias or metal-backed substrates for effective heat dissipation.
- Considérations environnementales: Design the substrate to withstand environmental conditions such as temperature variations, humidité, et contraintes mécaniques, en fonction des exigences de l’application.
- Fabricabilité:Ensure the design is manufacturable with the chosen substrate material and manufacturing processes. Consider factors like panel size, registration accuracy, and tolerances during fabrication.
En respectant ces directives de conception, engineers can optimize the performance and reliability of “Others High Frequency Substrates” in demanding RF and microwave applications.
Les avantages de Others High Frequency Substrate
Others High Frequency Substrates offer several advantages that make them suitable for RF (Radiofréquence) et applications micro-ondes:
- Excellent Electrical Properties: These substrates typically exhibit low dielectric constant (εr) et faible facteur de dissipation (δ beige), ensuring minimal signal loss and high signal integrity across a wide frequency range. This makes them ideal for high-frequency applications where maintaining signal integrity is critical.
- Capacité haute fréquence: They are designed to operate efficiently at frequencies above 1 GHz and can often support frequencies up to tens of GHz, depending on the specific material and design.
- Customizability: Manufacturers of Others High Frequency Substrates often offer customization options in terms of material formulations, thicknesses, and copper cladding options. This flexibility allows engineers to tailor the substrate to meet specific performance requirements.
- Stabilité mécanique: These substrates typically have good mechanical stability and dimensional accuracy, which is crucial for maintaining performance under varying environmental conditions and mechanical stresses.
- Dissipation de la chaleur: Some variants may offer good thermal management properties, helping in dissipating heat generated by high-power RF components or circuits.
- Cost-Effective Alternatives: Depending on the specific material and manufacturer, Others High Frequency Substrates can offer cost-effective alternatives to more specialized brands like Rogers or Megtron, while still delivering reliable performance.
- Wide Application Range: They find applications in various industries including telecommunications, aérospatial, défense, systèmes radar, communications par satellite, and high-speed data transfer applications due to their robust performance characteristics.
- Fiabilité: These substrates are designed and manufactured to stringent quality standards, ensuring reliable operation over extended periods.
Total, Others High Frequency Substrates combine excellent RF performance with customization options and cost-effectiveness, making them a preferred choice for engineers designing high-frequency circuits and systems.
Qu’est-ce que le Others High Frequency Substrate Processus de fabrication?
The fabrication process for Others High Frequency Substrates typically involves several key steps to ensure the substrates meet the stringent requirements for RF and microwave applications:
- Préparation du matériel: Select and prepare the substrate material based on the desired electrical properties (low dielectric constant, tangente à faible perte) and mechanical characteristics. Common materials include PTFE-based composites or ceramic-filled hydrocarbon resins.
- Substrate Lamination: The chosen substrate material is laminated into sheets of specified thicknesses. This lamination process involves bonding multiple layers together to achieve the desired substrate thickness.
- Revêtement en cuivre: Apply copper foil to one or both sides of the substrate sheets. The copper foil is typically bonded using heat and pressure to ensure good adhesion and electrical conductivity. The thickness of the copper foil is chosen based on the current-carrying capacity and impedance requirements of the RF circuit.
- Forage: Precision drilling is performed to create holes for vias, component leads, and mounting holes. The drilling process must maintain tight tolerances to ensure accuracy in via placements and minimize signal losses.
- Galvanoplastie: Electroplate the walls of the vias with conductive materials such as copper to ensure electrical connectivity between different layers of the substrate. This step is crucial for maintaining signal integrity and reducing impedance mismatch.
- Gravure: Use chemical etching processes to define the circuit traces and patterns on the copper-clad surfaces of the substrate. Etching removes unwanted copper from the substrate while leaving behind the desired circuit patterns.
- Surface Finish Application: Apply a surface finish to the substrate to ensure good solderability and protect against oxidation. Common surface finishes include ENIG (Nickel autocatalytique par immersion d’or), OSP (Organic Solderability Preservatives), or immersion silver.
- Inspection et essais finaux: Conduct thorough inspection and testing of the fabricated substrates to verify dimensional accuracy, Performance électrique (including dielectric constant and loss tangent), and adherence to specifications. This step ensures that the substrates meet the required standards for RF and microwave applications.
- Emballage et livraison: Once inspected and tested, the substrates are packaged according to customer requirements and shipped for further assembly into RF circuits or systems.
Tout au long du processus de fabrication, strict quality control measures are implemented to ensure consistency and reliability in the performance of Others High Frequency Substrates, meeting the demanding requirements of high-frequency applications.
L’application de la céramique Others High Frequency Substrate
Ceramic-based Others High Frequency Substrates find extensive applications in various RF (Radiofréquence) and microwave circuits where excellent electrical performance and reliability are critical. Some key applications include:
- Télécommunication: Used in base station antennas, Filtres RF, and amplifiers for wireless communication systems. Les substrats’ ability to maintain signal integrity and low loss tangent is crucial for efficient transmission and reception of RF signals.
- Aérospatiale et défense: Employed in radar systems, communications par satellite, avionique, and electronic warfare equipment. These applications demand substrates that can operate reliably under harsh environmental conditions and maintain consistent RF performance.
- Dispositifs médicaux: Used in RF medical equipment such as MRI machines and RF ablation devices. High-frequency substrates ensure accurate signal transmission and reception, contributing to the effectiveness of medical procedures.
- Automotive: Utilized in radar systems for collision avoidance, Régulateur de vitesse adaptatif, and vehicle-to-vehicle communication. Les substrats’ stability and reliability in high-temperature environments are crucial for automotive applications.
- Électronique grand public: Found in high-frequency modules for smartphones, Comprimés, and IoT devices where compact size and high performance are essential. These substrates enable reliable wireless connectivity and data transfer.
- Applications industrielles: Used in industrial automation systems, Capteurs, and instrumentation where high-frequency signals need to be transmitted accurately and with minimal interference.
- Wireless Infrastructure: Deployed in infrastructure equipment such as base stations, Répéteurs, and small cells for cellular networks. These substrates contribute to the efficient operation and expansion of wireless networks.
- Research and Development: Used in laboratories and R&D facilities for prototyping and testing high-frequency circuits and systems due to their predictable electrical properties and performance consistency.
In each of these applications, ceramic-based Others High Frequency Substrates play a crucial role in enabling reliable and efficient operation of RF and microwave devices, ensuring high performance and durability under demanding conditions.
FAQ sur Others High Frequency Substrate
What are Others High Frequency Substrates?
Others High Frequency Substrates refer to high-performance materials used in RF (Radiofréquence) et applications micro-ondes. They offer excellent electrical properties like low dielectric constant and low loss tangent.
What are the advantages of Others High Frequency Substrates?
They provide high frequency capability, excellent signal integrity, customizability in material and design, and cost-effectiveness compared to more specialized brands.
Where are Others High Frequency Substrates used?
They are used in telecommunications, aérospatial, défense, Dispositifs médicaux, automotive radar systems, Électronique grand public, industrial applications, and wireless infrastructure.
What materials are used in Others High Frequency Substrates?
Common materials include PTFE-based composites and ceramic-filled hydrocarbon resins, chosen for their stable electrical properties across a wide frequency range.
How are Others High Frequency Substrates fabricated?
Fabrication involves processes like material preparation, laminage, bardage en cuivre, forage, Galvanoplastie, gravure, finition de surface, and rigorous testing to ensure quality and performance.
What are the key considerations in designing with Others High Frequency Substrates?
Designers focus on selecting the right material for specific RF requirements, optimizing thickness, bardage en cuivre, via la conception, surface finish, and ensuring mechanical and thermal stability.
Why choose Others High Frequency Substrates over branded alternatives?
They offer similar performance characteristics at a potentially lower cost, with flexibility in customization to meet specific application needs.