Microtrace/Clearance PCB Fabricant
Microtrace/Clearance PCB Manufacturer,Microtrace or Clearance PCBs are designed for applications requiring extremely small trace widths and tight spacing between conductive paths. These PCBs are engineered to handle high-density interconnects and achieve precise electrical performance in compact spaces. The manufacturing process involves advanced photolithography and etching techniques to ensure that trace widths and spacing meet stringent design specifications. Microtrace PCBs are essential in high-performance electronics, such as smartphones and medical devices, where maximizing circuit density without compromising reliability is crucial. Their ability to support fine pitch components and high-speed signal transmission makes them a key choice for cutting-edge technology applications.
Quoi Microtrace/Clearance PCB?
Microtrace PCB, also known as Clearance PCB, refers to a type of printed circuit board designed to accommodate very fine traces and tight spacing between conductive elements. This type of PCB is engineered to manage and minimize signal interference, ensure reliable electrical performance, and meet the stringent requirements of modern electronic devices.
In microtrace PCBs, the traces—the pathways through which electrical signals travel—are extremely narrow, often in the range of micrometers (µm). This precision allows for higher density of circuitry on the same board size, which is essential for compact electronic devices. The term “clearance” in this context refers to the spacing between these narrow traces and other conductive elements like vias, Tampons, and components. Proper clearance is crucial to prevent short circuits, signal interference, and to ensure that the PCB operates correctly under various electrical and environmental conditions.
To achieve these fine traces and clearances, manufacturers use advanced fabrication techniques, such as high-resolution photolithography, laser etching, and precision chemical etching. The use of high-quality substrates with excellent electrical insulation properties is also essential to maintain the integrity of these fine traces.
Microtrace PCBs are commonly used in applications where space is limited, such as in mobile devices, électronique médicale, and high-performance computing systems. They play a critical role in ensuring that modern electronic devices are both compact and reliable, making them indispensable in the electronics industry.
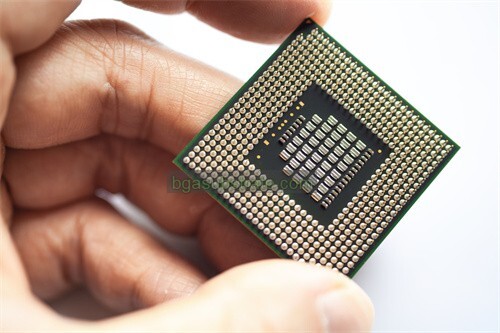
Microtrace/Clearance PCB Manufacturer
Qu’est-ce que le Microtrace/Clearance PCB Directives de conception?
Microtrace or Clearance PCB Design Guidelines focus on ensuring that printed circuit boards (PCB) with extremely fine traces and tight clearances perform reliably. These guidelines address various design considerations to prevent issues such as signal interference, short circuits, and manufacturing defects. Here are key design guidelines for Microtrace/Clearance PCBs:
- Largeur et espacement des traces: Determine the minimum trace width and spacing based on the manufacturing capabilities and electrical requirements. Ensure that the trace width is sufficient to handle the current without excessive heating, while the spacing avoids unintentional short circuits and interference.
- Intégrité du signal: Use controlled impedance traces and differential pairs where necessary to maintain signal integrity. Implement proper grounding and shielding to reduce noise and crosstalk between traces.
- Tolérances de fabrication:Collaborate with PCB manufacturers to understand their capabilities and limitations for microtraces and clearances. Verify that the design adheres to the manufacturer’s minimum trace and spacing requirements.
- Conception pour la fabricabilité: Include design features that facilitate the manufacturing process, such as well-defined solder mask openings and sufficient pad sizes for component placement. Avoid overly complex geometries that may be challenging to fabricate.
- Gestion thermique: Implement adequate thermal management techniques to dissipate heat effectively. Use thermal vias and copper pours to help manage heat generated by high-current traces.
- DFM (Design for Manufacturing): Conduct design reviews and simulations to identify potential manufacturing and assembly issues. Ensure that the design can be reliably produced using available PCB fabrication technologies.
- Tests et validation: Plan for testing and validation procedures to ensure that the PCB meets all performance and reliability standards. Use appropriate test points and access for in-circuit testing.
- Placement des composants: Optimize component placement to minimize trace lengths and avoid crossing traces. Ensure proper clearance around components to facilitate soldering and prevent mechanical stress.
En respectant ces directives, designers can create Microtrace/Clearance PCBs that are both high-performing and manufacturable, meeting the needs of advanced electronic applications.
Les avantages de Microtrace/Clearance PCB
Microtrace or Clearance PCBs offrent plusieurs avantages, particularly in applications requiring high-density circuitry and compact designs. Voici les principaux avantages:
- Increased Circuit Density: Microtrace PCBs enable higher component density on a single board by allowing for very narrow traces and tight clearances. This results in a smaller overall PCB size, making it ideal for compact electronic devices.
- Performances améliorées: The use of fine traces and precise clearances can improve signal integrity and reduce electromagnetic interference (EMI). This is crucial for high-frequency and high-speed applications, where maintaining signal quality is essential.
- Reduced Signal Interference: By carefully managing trace spacing and routing, Microtrace PCBs can minimize crosstalk and noise between traces. This leads to more reliable operation of sensitive electronic components.
- Lower Manufacturing Costs: Although the initial setup for Microtrace PCBs may involve higher precision, the ability to pack more functionality into a smaller space can reduce the overall material and assembly costs. This is particularly advantageous in high-volume production.
- Improved Reliability: Proper design practices in Microtrace PCBs, such as controlled impedance and adequate thermal management, contribute to enhanced reliability and durability of the PCB in various operating conditions.
- Advanced Design Flexibility: Microtrace PCBs allow for more complex circuit designs and integration of advanced technologies. This flexibility supports innovation in product development, enabling the creation of sophisticated electronic devices.
- Better Space Utilization: The compact nature of Microtrace PCBs helps optimize the use of available space within electronic devices, making it easier to fit additional features and components without increasing the device size.
- Higher Component Placement Precision: The design and fabrication techniques used for Microtrace PCBs allow for precise component placement, which is beneficial for achieving high performance and accuracy in electronic circuits.
These advantages make Microtrace/Clearance PCBs particularly valuable in applications where space is limited, performance is critical, and advanced technology integration is required.
Qu’est-ce que le Microtrace/Clearance PCB Processus de fabrication?
The fabrication process for Microtrace or Clearance PCBs involves several advanced steps to achieve the fine trace widths and tight clearances required. Here is an overview of the key steps in the fabrication process:
- Conception et mise en page: The process begins with detailed PCB design and layout, using specialized software to define trace widths, spacings, et le placement des composants. Designers must ensure that the design adheres to the manufacturing capabilities and tolerances for microtraces and clearances.
- Photomask Generation: A photomask is created based on the PCB design. This mask is used to transfer the circuit pattern onto the PCB substrate. For microtraces, high-resolution photomasks are required to accurately define the narrow traces and small clearances.
- Préparation du substrat: The PCB substrate, typically made from materials like FR4, Rogers, or other high-quality laminates, is prepared. It is cleaned and coated with a photoresist material that will react to light exposure during the imaging process.
- Imagerie: The prepared substrate is exposed to UV light through the photomask. The light alters the photoresist’s chemical properties according to the circuit pattern. This process creates a patterned layer on the substrate that defines the trace and clearance areas.
- Développement: The exposed photoresist is developed using a chemical solution that removes the unexposed areas, leaving a patterned resist on the substrate. This pattern will serve as a protective layer during the etching process.
- Gravure: The substrate undergoes an etching process, where unwanted copper or conductive material is removed, leaving behind the desired trace pattern. For microtraces, precise etching is essential to ensure the accuracy of the narrow traces and tight clearances.
- Layer Registration and Lamination: In multi-layer PCBs, layers are aligned and laminated together using heat and pressure. Each layer is carefully registered to ensure proper alignment of traces and vias throughout the board.
- Forage: Holes are drilled for vias and component leads. For microtrace PCBs, drilling must be precise to avoid damaging the delicate traces and clearances.
- Placage: The drilled holes are plated with a conductive material to establish electrical connections between layers. This step also involves adding a protective coating to prevent oxidation and damage.
- Application du masque de soudure:A solder mask is applied to protect the traces from soldering and environmental damage. The mask is carefully aligned to avoid covering the microtraces and critical clearances.
- Finition de surface: The PCB surface is treated with a finish such as HASL (Nivellement de la soudure à l’air chaud), ENIG (Nickel autocatalytique par immersion d’or), or other coating to enhance solderability and protect the copper traces.
- Inspection et essais: The final PCB undergoes thorough inspection and testing to ensure that it meets all design specifications and quality standards. Cela inclut l’inspection visuelle, Essais électriques, and sometimes automated optical inspection (AOI).
- Cutting and Final Processing: The PCB is cut from the panel, and additional processing such as edge routing or scoring is performed to prepare it for assembly and integration into electronic devices.
The Microtrace/Clearance PCB fabrication process requires precision and advanced technology to ensure the accurate production of fine traces and tight clearances, making it suitable for high-density and high-performance electronic applications.
L’application de la céramique Microtrace/Clearance PCB
Ceramic Microtrace or Clearance PCBs utilize ceramic substrates with fine traces and tight clearances for applications where high performance and reliability are critical. Here are the primary applications and benefits of using ceramic materials in Microtrace/Clearance PCBs:
- High-Frequency and High-Speed Electronics: Ceramic PCBs are ideal for high-frequency and high-speed applications due to their low dielectric loss and high signal integrity. They are used in RF (radiofréquence) and microwave circuits where maintaining signal quality and minimizing signal attenuation are essential.
- Advanced Communication Systems: In telecommunications and data communication systems, ceramic Microtrace PCBs support high-density interconnections and complex routing required for advanced communication technologies, including 5G and satellite communications.
- Aérospatiale et défense: Ceramic PCBs are widely used in aerospace and defense applications where reliability, durabilité, and resistance to extreme environmental conditions are crucial. They are employed in avionics, systèmes radar, and other critical components where performance cannot be compromised.
- Dispositifs médicaux: The high thermal conductivity and biocompatibility of ceramic materials make them suitable for medical devices. Ceramic Microtrace PCBs are used in implantable devices, Équipement de diagnostic, and other medical electronics that require precise and reliable performance.
- Electronique de puissance: Ceramic PCBs are utilized in power electronics applications where efficient heat dissipation is necessary. Their high thermal conductivity helps manage the heat generated by power components, making them suitable for power converters, Onduleurs, and other high-power applications.
- Électronique automobile: Dans l’industrie automobile, ceramic Microtrace PCBs are used in advanced driver-assistance systems (ADAS), Unités de commande du moteur (Écus), and other automotive electronics that require high performance and resistance to harsh operating conditions.
- Électronique grand public: Électronique grand public haute performance, tels que les smartphones, Comprimés, et wearables, benefit from the compact and efficient design made possible by ceramic Microtrace PCBs. Their ability to handle high-frequency signals and reduce signal interference is crucial for modern electronic devices.
- Industrial Equipment: Dans les applications industrielles, ceramic PCBs are used in equipment that demands high reliability and precision, such as industrial automation systems, Capteurs, et systèmes de contrôle.
The use of ceramic materials in Microtrace/Clearance PCBs provides several advantages, including excellent thermal conductivity, Faible perte diélectrique, haute résistance mécanique, and resistance to environmental factors. These properties make ceramic Microtrace PCBs suitable for demanding applications where performance and reliability are paramount.
FAQ sur Microtrace/Clearance PCB
What are the benefits of using Microtrace PCBs?
Benefits include increased circuit density, improved performance and signal integrity, reduced signal interference, and efficient space utilization.
What is the difference between Microtrace and standard PCBs?
Microtrace PCBs have much finer traces and tighter clearances compared to standard PCBs, enabling more complex and densely packed circuitry.
What materials are used for Microtrace PCBs?
Common materials include high-quality laminates like FR4, Rogers, and ceramics, which provide the necessary electrical and thermal properties.
What challenges are associated with Microtrace PCB fabrication?
Challenges include maintaining precise trace widths and spacings, preventing signal interference, managing thermal dissipation, and ensuring manufacturability.
How are Microtrace PCBs manufactured?
The manufacturing process involves precise design, photomask generation, imaging, developing, gravure, Laminage de couches, forage, Placage, Application du masque de soudure, et inspection finale.
What applications are suitable for Microtrace PCBs?
Suitable applications include high-frequency and high-speed electronics, aérospatial, Dispositifs médicaux, Électronique automobile, and advanced consumer electronics.