Megtron 8 Substrat Fabricant
Megtron 8 Fabricant de substrat,Megtron 8 Le substrat est un stratifié haute fréquence avancé conçu pour les applications électroniques exigeantes. Il offre une stabilité thermique exceptionnelle et une faible constante diélectrique, ce qui le rend idéal pour les circuits RF et micro-ondes. Megtron 8 Caractéristiques Propriétés tangentes à faible perte, qui aident à minimiser la dégradation du signal, Garantir l’intégrité du signal haute performance. Le substrat est conçu pour une faible absorption d’humidité et une excellente stabilité dimensionnelle, Contribuer à un fonctionnement fiable dans des environnements difficiles. Sa compatibilité avec le traitement des lignes fines le rend adapté aux conceptions d’interconnexion à haute densité, Couramment utilisé dans les télécommunications, automobile, et l’aérospatiale. Total, Megtron 8 est un choix privilégié pour les ingénieurs à la recherche de performances supérieures dans les systèmes électroniques complexes.
Qu’est-ce que Megtron 8 Substrat?
Megtron 8 est un substrat PCB haute performance principalement utilisé pour les applications électroniques à haute vitesse et à haute fréquence. Ce matériau a été développé par la société japonaise Megtron et possède d’excellentes propriétés électriques et mécaniques, Répondre aux exigences de plus en plus strictes des produits électroniques modernes.
Megtron 8 Les substrats sont fabriqués à partir d’un matériau en résine spécial avec une faible constante diélectrique et un faible facteur de perte, ce qui garantit des performances exceptionnelles dans la transmission de signaux haute fréquence. Par rapport aux matériaux FR-4 traditionnels, Megtron 8 a une meilleure stabilité thermique et un coefficient de dilatation thermique plus faible, réduisant efficacement les déformations structurelles causées par les fluctuations de température. Cette caractéristique est cruciale pour la conception de circuits à haute fréquence, car même des modifications mineures peuvent avoir un impact significatif sur l’intégrité du signal lors de opérations à grande vitesse.
De plus, Megtron 8 Présente une résistance chimique et des taux d’absorption d’humidité supérieurs, Maintien de performances stables même dans des environnements difficiles. Ce substrat est largement utilisé dans les appareils de communication, Matériel informatique, Automatisation industrielle, et l’électronique automobile.
En résumé, Megtron 8 est devenu un choix idéal pour la conception de circuits imprimés haute fréquence et haute vitesse en raison de ses propriétés électriques exceptionnelles et de ses performances mécaniques supérieures, S’adapter aux progrès rapides de la technologie électronique moderne.
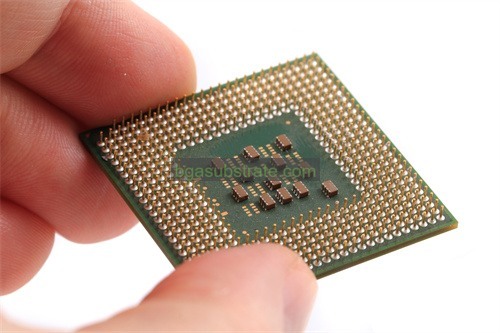
Megtron 8 Fabricant de substrat
Qu’est-ce que le Megtron 8 Directives de conception de substrat?
Les directives de conception pour Megtron 8 Substrats Concentrez-vous sur l’optimisation des performances dans les applications à haute fréquence et à grande vitesse. Voici quelques considérations clés:
- Empilement de couches: Assurez-vous d’une disposition appropriée des couches pour minimiser la perte de signal et maintenir le contrôle de l’impédance. Utilisez des configurations de microbandes ou de lignes de débandelette selon les besoins.
- Largeur et espacement des traces: Calculez soigneusement les largeurs de piste pour maintenir les niveaux d’impédance souhaités. Faites attention à l’espacement entre les traces pour éviter la diaphonie.
- Via Design: Utilisez des vias aveugles et enterrés dans la mesure du possible pour réduire l’inductance et améliorer l’intégrité du signal. Maintenez les diamètres de via petits pour minimiser la capacité parasite.
- Plan de masse: Utiliser des plans de masse continus pour réduire les interférences électromagnétiques (EMI) et améliorer les voies de retour pour les signaux à haut débit.
- Gestion thermique: Tenez compte de la dissipation thermique, Surtout dans les applications à haute puissance. Utilisez des vias thermiques et des tampons de manière stratégique pour améliorer la dissipation de la chaleur.
- Outils de simulation: Utiliser des outils de simulation à haute fréquence (comme HFSS ou ADS) pendant la phase de conception pour valider l’intégrité du signal et les performances électromagnétiques.
- Tolérances de fabrication: Être conscient des capacités de fabrication et des tolérances du substrat. Collaborer avec les fabricants dès le début du processus de conception pour s’assurer de la faisabilité.
- Tests et validation: Planifier des méthodes d’analyse appropriées, y compris TDR (Réflectométrie dans le domaine temporel) et mesures du paramètre S, pour valider les performances de conception post-fabrication.
En respectant ces directives, les concepteurs peuvent exploiter toutes les capacités de Megtron 8 Substrats pour des performances de circuit fiables à haute fréquence et à grande vitesse.
Les avantages de Megtron 8 Substrat
Megtron 8 Substrats offrent plusieurs avantages, particulièrement adapté aux applications à haute fréquence et à grande vitesse:
- Faible constante diélectrique: Cette propriété garantit une perte de signal minimale, Amélioration de l’intégrité du signal dans les circuits à grande vitesse.
- Faible facteur de perte: Le substrat minimise la perte d’énergie lors de la transmission du signal, ce qui est crucial pour maintenir les performances dans les applications à haute fréquence.
- Haute stabilité thermique: Megtron 8 peut résister à des températures plus élevées, Réduire le risque de déformation et maintenir les performances dans des environnements exigeants.
- Faible coefficient de dilatation thermique: Cela aide à maintenir la stabilité dimensionnelle, Réduire le gauchissement et le stress pendant les cycles thermiques.
- Excellente résistance à l’humidité: Les faibles taux d’absorption d’humidité du substrat empêchent la dégradation des performances, Particulièrement dans des conditions humides.
- Résistance chimique supérieure: Il peut résister à divers produits chimiques, ce qui le rend adapté aux applications dans des environnements difficiles.
- Propriétés mécaniques robustes: Megtron 8 offre une bonne résistance mécanique, ce qui contribue à la durabilité lors de la manipulation et de l’assemblage.
- Versatilité: Il convient à un large éventail d’applications, y compris les télécommunications, informatique, automobile, et l’électronique industrielle.
Ces avantages font de Megtron 8 Un choix privilégié pour les ingénieurs qui conçoivent des systèmes électroniques haute performance.
Qu’est-ce que le Megtron 8 Processus de fabrication du substrat?
Le processus de fabrication de Megtron 8 substrats implique plusieurs étapes clés, Garantir une précision et une qualité élevées adaptées aux applications à haute fréquence:
- Préparation du matériel: Commencez par le Megtron brut 8 matériel, qui est un type de résine époxy avec des charges spécialisées. Ce matériau est disponible en feuilles de différentes épaisseurs.
- Découpe de couches: Couper le Megtron 8 feuilles aux dimensions requises sur la base des spécifications de conception.
- Laminage du cuivre: Collez la feuille de cuivre à la surface du substrat à l’aide de la chaleur et de la pression. Cela se fait généralement dans une presse à laminer pour assurer une forte adhérence.
- Tracé de photos: Appliquez une couche de résine photosensible sur la surface en cuivre, suivi d’une exposition à la lumière ultraviolette à travers un photomasque. Ce processus définit les modèles de circuit.
- Développement: Après l’exposition, Le PhotoResist est développé, en supprimant les zones non exposées et en laissant le motif de circuit souhaité sur la couche de cuivre.
- Gravure: Le cuivre exposé est gravé chimiquement, laisser les traces du circuit intactes sur le substrat.
- Forage: Les trous pour les vias et les fils des composants sont percés à l’aide d’un équipement de perçage de précision. Cette étape doit être soigneusement contrôlée pour maintenir l’intégrité.
- Via le placage: Si besoin est, Les vias sont plaqués de cuivre pour créer des connexions électriques entre les couches. Cette étape peut impliquer des processus de galvanoplastie ou de placage chimique.
- Finition finale: Processus supplémentaires, tels que les traitements de surface ou l’application de masques de soudure, Peut être appliqué pour améliorer les performances et la durabilité.
- Test:Effectuer des tests rigoureux pour assurer l’intégrité électrique et le respect des spécifications de conception, y compris les tests d’impédance, Intégrité du signal, et propriétés thermiques.
En suivant ces étapes de fabrication, fabricants peuvent produire des Megtron de haute qualité 8 Des substrats qui répondent aux exigences élevées des applications électroniques modernes.
L’application de la céramique Megtron 8 Substrat
Megtron en céramique 8 Les substrats sont utilisés dans diverses applications en raison de leurs propriétés électriques et mécaniques supérieures. Voici quelques applications clés:
- Télécommunication: Utilisé dans les appareils de communication à haut débit, tels que les routeurs et les commutateurs, où l’intégrité du signal est essentielle.
- Électronique grand public: Trouvé dans les smartphones, Comprimés, et consoles de jeux, où une conception compacte et des performances élevées sont requises.
- Électronique automobile: Utilisé dans les systèmes avancés d’aide à la conduite (ADAS) et composants de véhicules électriques, Fiabilité dans les environnements difficiles.
- Automatisation industrielle: Utilisé dans les systèmes de contrôle et les capteurs, Offrir durabilité et performance dans les environnements industriels.
- Aérospatiale et défense: Utilisé dans l’avionique et les communications militaires, où une fiabilité et des performances élevées dans des conditions extrêmes sont essentielles.
- Dispositifs médicaux: Mis en œuvre dans les équipements de diagnostic et de surveillance, Garantir la précision et la fiabilité dans les applications critiques.
Ces applications tirent parti de la stabilité thermique, Faible perte, et la résistance mécanique de Megtron 8 Substrats, ce qui les rend idéaux pour les environnements électroniques exigeants.
FAQ sur Megtron 8 Substrat
Qu’est-ce que Megtron 8?
Megtron 8 est un substrat PCB haute performance conçu pour les applications électroniques à haute fréquence et à grande vitesse, offrant une faible constante diélectrique et une faible perte.
Quels sont les principaux avantages de Megtron 8?
Les principaux avantages sont la faible perte de signal, haute stabilité thermique, faible absorption d’humidité, et des propriétés mécaniques supérieures, ce qui le rend idéal pour les environnements exigeants.
Dans quelles applications se trouve Megtron 8 Couramment utilisé?
Il est utilisé dans les télécommunications, Électronique grand public, Systèmes automobiles, Automatisation industrielle, aérospatial, défense, et dispositifs médicaux.
Comment Megtron 8 par rapport aux substrats FR-4 traditionnels?
Megtron 8 Offre de meilleures performances aux hautes fréquences, Perte plus faible, Stabilité thermique améliorée, et une plus grande fiabilité dans des conditions difficiles par rapport au FR-4.
Quel est le processus de fabrication de Megtron 8 Substrats?
Le processus de fabrication comprend la préparation des matériaux, Laminage de cuivre, Tracé de photos, gravure, forage, par placage, et finition finale.
Can Megtron 8 substrats à utiliser dans des conceptions multicouches?
Oui, Megtron 8 Les substrats conviennent aux conceptions multicouches, Offrant d’excellentes performances et une fiabilité sur plusieurs couches.
Quelles sont les méthodes d’essai utilisées pour Megtron 8 Substrats?
Les méthodes de test courantes incluent la réflectométrie dans le domaine temporel (TDR), Mesures du paramètre S, et des tests de cyclage thermique pour garantir les performances et la fiabilité.
Existe-t-il des directives de conception spécifiques pour Megtron ? 8?
Oui, Les directives de conception incluent des considérations pour l’empilement des couches, Largeur et espacement des traces, via la conception, Utilisation du plan de masse, et la gestion thermique.