Substrat Megtron 7N Fabricant
Fabricant de substrats Megtron 7N,Le substrat Megtron 7N est un matériau haute performance spécialement conçu pour les applications électroniques avancées. Connu pour son excellente conductivité thermique et sa faible constante diélectrique, Il offre des performances électriques supérieures dans les circuits haute fréquence. Megtron 7N se caractérise par une faible absorption d’humidité et une grande stabilité dimensionnelle, qui améliorent sa fiabilité dans des environnements exigeants. Sa formulation unique en résine permet un traitement fin, ce qui le rend adapté aux cartes de circuits imprimés multicouches et aux interconnexions à haute densité. De plus, Le substrat est compatible avec divers procédés de fabrication, Permettre une production efficace d’assemblages électroniques complexes. Megtron 7N est largement utilisé dans les télécommunications, automobile, et applications aérospatiales, Là où la performance est essentielle.
Qu’est-ce que le substrat Megtron 7N?
Le substrat Megtron 7N est un matériau de carte de circuit imprimé haute performance conçu pour les applications à haute fréquence et à grande vitesse. Développé par la société japonaise Megtron, Il utilise une gamme de matériaux et de procédés avancés, ce qui se traduit par d’excellentes performances électriques et une résistance mécanique dans les appareils électroniques.
Les principales caractéristiques du substrat Megtron 7N comprennent une faible constante diélectrique (Dk) et faible facteur de dissipation (Df), ce qui le rend particulièrement adapté aux applications de transmission de signaux à haut débit, tels que les appareils de communication, systèmes radar, et équipement micro-ondes à haute fréquence. De plus, Megtron 7N présente une excellente stabilité thermique et une excellente résistance chimique, ce qui lui permet de maintenir de bonnes performances dans des environnements à haute température et difficiles.
Ce substrat offre également de bonnes caractéristiques de traitement, ce qui facilite le collage avec d’autres matériaux, tels que les couches de cuivre et les composants montés en surface, facilitant son utilisation dans des conceptions de circuits complexes. En raison de ses propriétés électriques et mécaniques exceptionnelles, Megtron 7N est largement utilisé dans l’électronique grand public haut de gamme, informatique, et l’électronique automobile, Répondre aux exigences strictes de performance et de fiabilité des produits électroniques modernes.
En résumé, Le substrat Megtron 7N est un choix idéal pour les applications à haute fréquence et à grande vitesse, Et ses performances électriques supérieures et sa fiabilité en font un matériau privilégié dans de nombreuses industries de haute technologie.
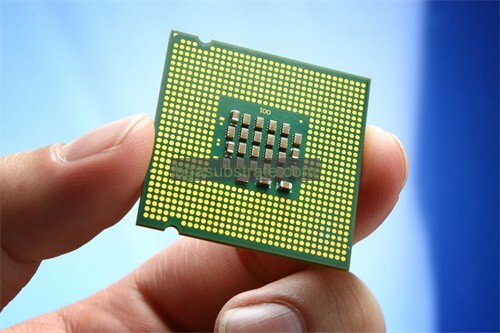
Fabricant de substrats Megtron 7N
Qu’est-ce que les directives de conception du substrat Megtron 7N?
Les directives de conception pour Substrat Megtron 7N se concentrent généralement sur l’optimisation des performances pour les applications à haute fréquence et à grande vitesse. Voici quelques considérations clés:
- Empilement de couches: Concevez l’empilement des couches de manière à minimiser les problèmes d’intégrité du signal. Envisagez d’utiliser des couches d’impédance contrôlée pour les signaux à grande vitesse.
- Largeur et espacement des traces: Calculez la largeur et l’espacement des pistes pour obtenir l’impédance souhaitée. Utilisez des outils de conception pour garantir des dimensions appropriées en fonction des propriétés diélectriques du substrat.
- Via Design: Utilisez des microvias ou des vias aveugles/enterrés lorsque cela est possible pour réduire l’inductance et améliorer l’intégrité du signal. Assurez-vous d’un placage et d’une finition appropriés pour plus de fiabilité.
- Gestion thermique: Incorporez des vias thermiques et des tampons pour gérer la dissipation de chaleur, Spécialement pour les composants de puissance. Envisagez des coulées de cuivre pour une meilleure répartition de la chaleur.
- Routage du signal: Gardez les signaux haute vitesse courts et directs. Évitez les angles vifs et les vias inutiles pour minimiser les réflexions et les pertes.
- Terre: Utilisez un plan de masse solide pour réduire les interférences électromagnétiques (EMI) et améliorer les performances. Assurez-vous d’une mise à la terre correcte pour les chemins de retour du signal.
- Séparation des couches: Maintenir une séparation adéquate entre les couches d’alimentation et de signal pour réduire le couplage du bruit.
- Considérations relatives à la fabrication: Suivez les recommandations du fabricant pour la taille des trous, dégagement des bords, et finitions de surface pour assurer la fabricabilité et la fiabilité.
- Tests et validation:Planifier l’analyse de l’intégrité du signal et les tests thermiques pendant la phase de conception afin de valider les performances dans les conditions de fonctionnement.
En respectant ces directives, les concepteurs peuvent optimiser les performances des substrats Megtron 7N dans des applications électroniques exigeantes.
Les avantages du substrat Megtron 7N
Substrat Megtron 7N offre plusieurs avantages, en particulier pour les applications à haute fréquence et à grande vitesse:
- Faible constante diélectrique (Dk): Cette fonctionnalité permet de réduire les délais de propagation du signal, ce qui le rend idéal pour les applications numériques et RF à haut débit.
- Faible facteur de dissipation (Df): Le faible Df contribue à une perte de signal minimale, Amélioration des performances globales des circuits haute fréquence.
- Stabilité thermique: Megtron 7N présente d’excellentes propriétés thermiques, Maintien des performances dans des environnements à haute température, ce qui est essentiel pour la fiabilité dans les applications exigeantes.
- Résistance chimique: Le substrat est résistant à divers produits chimiques, Amélioration de la durabilité et de la longévité dans différentes conditions de fonctionnement.
- Résistance mécanique: Il offre de bonnes propriétés mécaniques, Robustesse et stabilité pendant la fabrication et l’utilisation finale.
- Bonnes caractéristiques de traitement:Megtron 7N est compatible avec les processus de fabrication de circuits imprimés standard, facilitant la conception et la fabrication.
- Excellent contrôle de l’impédance: Le substrat prend en charge une adaptation précise de l’impédance, ce qui est crucial pour maintenir l’intégrité du signal dans les applications à haut débit.
- Versatilité: Convient à un large éventail d’applications, y compris les télécommunications, automobile, et l’électronique grand public, ce qui en fait un choix polyvalent pour les designers.
Ces avantages font du Megtron 7N un matériau privilégié pour les fabricants à la recherche de performances et de fiabilité élevées dans les produits électroniques.
Qu’est-ce que le processus de fabrication du substrat Megtron 7N ??
Le processus de fabrication du substrat Megtron 7N comporte généralement plusieurs étapes clés, similaire à la fabrication standard de PCB mais adaptée à ses propriétés spécifiques. Voici un aperçu:
- Préparation du matériel: Les feuilles Megtron 7N sont coupées à la taille souhaitée et préparées pour le laminage. Le substrat est généralement constitué d’un matériau époxy renforcé de verre conçu pour les applications à haute fréquence.
- Marcottage: Si la conception comprend plusieurs couches, Les couches sont empilées selon la configuration d’empilement requise. Cela peut impliquer l’ajout de couches préimprégnées entre les couches centrales.
- Laminage: Les couches empilées sont soumises à la chaleur et à la pression dans un processus de laminage, qui durcit la résine et lie les couches entre elles. Cette étape est essentielle pour assurer la stabilité mécanique et les performances électriques.
- Forage: Après le laminage, Des trous sont percés pour les vias et les trous de montage. Le processus de perçage doit être précis pour éviter d’endommager le substrat et pour maintenir l’intégrité des signaux haute fréquence.
- Placage de cuivre: Les trous percés sont plaqués de cuivre pour créer des voies conductrices. Il peut s’agir d’un placage de cuivre autocatalytique suivi d’un placage électrolytique pour obtenir l’épaisseur souhaitée.
- Gravure: Les couches de cuivre sont gravées pour créer les motifs de circuit souhaités. Il s’agit d’appliquer une couche de résine photosensible, l’exposant à la lumière UV, puis la gravure du cuivre non protégé.
- Finition de surface: Une finition de surface est appliquée pour protéger le cuivre et améliorer la soudabilité. Les finitions courantes incluent l’or par immersion, HASL, ou ENEPIG, en fonction des exigences de l’application.
- Essais et inspections: Les substrats fabriqués subissent des tests électriques, inspection visuelle, et d’autres mesures de contrôle de la qualité pour s’assurer qu’ils répondent aux normes de rendement spécifiées.
- Découpe finale et emballage: Une fois les tests terminés, Les substrats sont coupés aux dimensions finales et emballés pour l’expédition.
Ces étapes sont conçues pour optimiser les propriétés uniques de Megtron 7N, Garantir des performances élevées dans les applications qui exigent fiabilité et rapidité.
L’application du substrat céramique Megtron 7N
Substrat Megtron 7N, malgré son nom qui sonne comme une céramique, est en fait un matériau de carte de circuit imprimé à base d’époxy haute performance, pas un substrat céramique. Il est spécialement conçu pour les applications à haute fréquence et à haute vitesse dans les appareils électroniques. Voici quelques applications typiques:
- Télécommunication: Utilisé dans les stations de base, Antennes, et d’autres équipements de communication où les performances à haute fréquence sont essentielles.
- Communications de données: Utilisé dans les routeurs, Commutateurs, Serveurs, et d’autres équipements de réseau pour une transmission efficace des données.
- Aérospatiale et défense: Utilisé dans les systèmes radar, avionique, et les équipements de communication par satellite en raison de leur fiabilité dans des conditions extrêmes et de leurs capacités de signal à haut débit.
- Électronique automobile: Présent dans les systèmes avancés d’aide à la conduite (ADAS), systèmes d’infodivertissement, et les unités de commande du moteur (Écus) où la durabilité et l’intégrité du signal sont cruciales.
- Électronique grand public: Utilisé dans les smartphones haut de gamme, Comprimés, et d’autres appareils portables où une taille compacte et des performances élevées sont requises.
- Électronique industrielle: Appliqué dans les équipements d’automatisation, systèmes de contrôle, et des capteurs où la robustesse et la fiabilité sont essentielles.
- Dispositifs médicaux: Utilisé dans l’équipement de diagnostic, Systèmes d’imagerie, et moniteurs médicaux pour un traitement du signal et une transmission de données fiables.
Avantages du substrat Megtron 7N, tels qu’une faible constante diélectrique, faible facteur de dissipation, excellente stabilité thermique, et résistance mécanique, le rendent adapté aux applications exigeantes où les performances et la fiabilité des hautes fréquences sont primordiales.
FAQ sur le substrat Megtron 7N
De quoi est fait le substrat Megtron 7N?
Le substrat Megtron 7N est principalement fabriqué en matériau époxy renforcé de verre, Spécialement conçu pour les applications à haute fréquence et à grande vitesse.
Quels sont les principaux avantages de l’utilisation de Megtron 7N?
Les principaux avantages incluent une faible constante diélectrique (Dk), faible facteur de dissipation (Df), excellente stabilité thermique, Bonne résistance mécanique, et haute résistance chimique, ce qui le rend idéal pour les applications électroniques exigeantes.
Dans quelles applications Megtron 7N est-il généralement utilisé?
Il est couramment utilisé dans les télécommunications, communications de données, Aérospatiale et défense, Électronique automobile, Électronique grand public, Électronique industrielle, et dispositifs médicaux.
Comment Megtron 7N se compare-t-il aux substrats FR-4 traditionnels ??
Megtron 7N offre des performances supérieures aux hautes fréquences et vitesses par rapport aux substrats FR-4 traditionnels, notamment en termes d’intégrité du signal et de stabilité thermique.
Megtron 7N peut-il être utilisé dans des conceptions de circuits imprimés multicouches?
Oui, Megtron 7N convient aux conceptions de circuits imprimés multicouches, Prise en charge des implantations complexes et des conceptions à impédance contrôlée.
Quel est le processus de fabrication des substrats Megtron 7N?
Le processus de fabrication comprend la préparation des matériaux, marcottage, laminage, forage, Placage de cuivre, gravure, Application des finitions de surface, et tests.
Le Megtron 7N est-il compatible avec les processus de fabrication de circuits imprimés standard ??
Oui, il est compatible avec la plupart des processus de fabrication de PCB standard, Bien que certaines considérations spécifiques puissent être nécessaires en raison de ses propriétés uniques.
Quel type de test est recommandé pour les substrats Megtron 7N?
Essais électriques, Essais thermiques, et l’inspection visuelle sont recommandées pour garantir la performance et la fiabilité.