Nitruro de aluminio (Aln) Ceramic Substrate Fabricante
Nitruro de aluminio (Aln) Fabricante de sustratos cerámicos,Nitruro de aluminio (Aln) Ceramic Substrate is renowned for its exceptional thermal conductivity and electrical insulation properties, making it ideal for high-power and high-frequency electronic applications. AlN substrates efficiently dissipate heat, ensuring the reliability and longevity of electronic components such as power transistors, LEDs, y dispositivos de microondas. Adicionalmente, their thermal expansion coefficient closely matches that of silicon, minimizing thermal stress in semiconductor devices. AlN ceramic substrates also offer good mechanical strength and chemical stability, allowing them to perform well in harsh environments. Their ability to support complex circuit designs makes them a critical component in advanced electronic packaging solutions.
Qué es Nitruro de aluminio (Aln) Ceramic Substrate?
Nitruro de aluminio (Aln) ceramic substrate is a specialized material used primarily in electronics and semiconductor industries for its excellent thermal conductivity, electrical insulation properties, and mechanical strength. It is composed of aluminum and nitrogen atoms arranged in a hexagonal crystal structure, imparting unique properties ideal for high-performance applications.
The key characteristics of AlN include its thermal conductivity, which is among the highest of all ceramics, making it effective for dissipating heat from electronic components. This property helps in maintaining optimal operating temperatures, enhancing device reliability and longevity. Adicionalmente, AlN exhibits good electrical insulation, crucial for isolating components and preventing electrical interference.
Due to its mechanical robustness and resistance to thermal shock, AlN ceramic substrates are used in applications requiring reliability under varying temperature conditions. These substrates are commonly used in power electronics, LEDs, microwave devices, and integrated circuits where heat dissipation and electrical isolation are critical.
Manufacturing techniques for AlN substrates involve methods such as hot pressing, sintering, and chemical vapor deposition (CVD), ensuring precise control over material properties and substrate dimensions. Ongoing research aims to further enhance AlN’s performance for next-generation electronics and semiconductor devices, illustrating its importance in advancing technology.
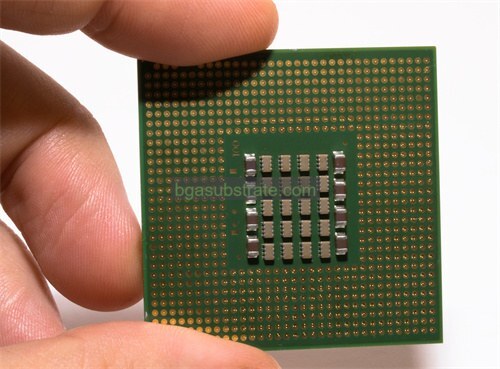
Nitruro de aluminio (Aln) Fabricante de sustratos cerámicos
¿Qué es el Nitruro de aluminio (Aln) Ceramic Substrate Directrices de diseño?
Design guidelines for Nitruro de aluminio (Aln) ceramic substrates are essential to ensure optimal performance and reliability in electronic and semiconductor applications. Here are some key design considerations:
- Gestión térmica: AlN substrates are chosen for their high thermal conductivity (approximately 170-230 W/mK), which allows efficient heat dissipation from electronic components. Designers should ensure that the substrate thickness and layout facilitate effective thermal management. Thermal vias and heat spreaders can be integrated into the design to enhance heat dissipation.
- Electrical Insulation: AlN exhibits excellent electrical insulation properties, with high breakdown voltage and low dielectric loss at high frequencies. Designers should maintain proper insulation distances and consider the dielectric strength when laying out circuit traces and components on the substrate.
- Coefficient of Thermal Expansion (CTE): Although AlN’s CTE (~4.5 ppm/K) is closer to that of silicon (~2.6 ppm/K) compared to other ceramics, mismatches with other materials like copper (CTE ~16-18 ppm/K) or silicon carbide (CTE ~3.0 ppm/K) must be considered to prevent thermal stress-induced failures. Designers may use techniques such as graded transition layers or compliant interfaces to mitigate CTE mismatches.
- Resistencia mecánica: AlN ceramic substrates are mechanically robust but can be brittle. Designers should avoid sharp corners and minimize mechanical stresses during handling and operation to prevent cracking or fracture.
- Surface Finish and Metallization: Proper surface finish and metallization are crucial for ensuring good adhesion and electrical contact with components mounted on the substrate. Thin-film metallization techniques such as sputtering or plating are commonly used to create conductive traces and pads on AlN substrates.
- Consideraciones medioambientales: AlN is stable in a wide range of environmental conditions but may require protective coatings or encapsulation depending on the application’s operating environment (e.g., humidity, corrosive gases).
- Design for Manufacturability (DFM): Consider manufacturability aspects such as substrate size, tolerance, and alignment features. AlN substrates are typically manufactured using processes like tape casting, hot pressing, or CVD, so design features should align with the chosen manufacturing method.
Al adherirse a estas pautas de diseño, engineers and designers can maximize the performance, fiabilidad, and longevity of electronic and semiconductor devices utilizing Aluminum Nitride ceramic substrates.
Las ventajas de Nitruro de aluminio (Aln) Ceramic Substrate
Nitruro de aluminio (Aln) ceramic substrates offer several distinct advantages that make them highly desirable for various electronic and semiconductor applications:
- Alta conductividad térmica: AlN exhibits exceptional thermal conductivity (approximately 170-230 W/mK), which is significantly higher than traditional ceramic substrates like alumina (Al2O3). This property allows for efficient heat dissipation from electronic components, thereby improving device reliability and longevity. It’s particularly beneficial in high-power applications where thermal management is critical.
- Electrical Insulation: AlN has excellent electrical insulation properties with a high breakdown voltage and low dielectric loss at high frequencies. This makes it ideal for applications requiring electrical isolation and minimal signal loss, such as in microwave devices, RF modules, and power electronics.
- Mechanical Strength and Stability: Despite its high thermal conductivity, AlN ceramic substrates are mechanically robust and dimensionally stable. They exhibit good resistance to thermal shock and can withstand rapid temperature changes without compromising structural integrity. This mechanical reliability ensures consistent performance over a wide range of operating conditions.
- Compatibility with Semiconductor Materials: AlN substrates have a coefficient of thermal expansion (CTE) that is closer to silicon compared to other ceramics, which enhances their compatibility with semiconductor materials. This reduces the risk of thermal stress-induced failures in devices where AlN substrates are used as a base material or carrier.
- Chemical and Thermal Stability: AlN is chemically inert and exhibits high thermal stability, making it suitable for harsh operating environments. It resists corrosion from acids, alkalis, and most organic solvents, ensuring long-term reliability in diverse industrial and electronic applications.
- Precision Manufacturing and Thin-Film Compatibility: AlN substrates can be manufactured with high precision using techniques such as tape casting, hot pressing, or chemical vapor deposition (CVD). This allows for the integration of fine features, thin-film metallization, and complex geometries, meeting the exacting requirements of modern electronic designs.
- Sostenibilidad Ambiental: Compared to some alternative materials, AlN is environmentally friendly due to its non-toxic composition and recyclability. Its longevity and reliability in devices contribute to reducing electronic waste and lifecycle environmental impact.
En general, Aluminum Nitride ceramic substrates offer a combination of superior thermal management, electrical insulation, Robustez mecánica, and compatibility with semiconductor materials, making them indispensable in advancing technologies across various industries.
¿Qué es el Nitruro de aluminio (Aln) Ceramic Substrate Proceso de fabricación?
The fabrication process of Aluminum Nitride (Aln) ceramic substrates typically involves several steps to achieve the desired material properties and dimensional accuracy. Aquí hay una descripción general del proceso de fabricación típico:
- Powder Preparation: The process begins with the preparation of Aluminum Nitride powder. The raw materials, typically aluminum oxide (Al2O3) and aluminum metal (Al), along with nitrogen gas (N2), are reacted under high temperature and controlled atmosphere conditions to synthesize AlN powder. The purity and particle size of the powder are crucial for achieving high-quality substrates.
- Formulation and Mixing: The synthesized AlN powder is then mixed with binders and additives to improve the forming characteristics and green strength of the material. This mixture is often referred to as a ceramic slurry or paste.
- Shaping (Green Forming): The slurry is shaped into the desired form of the substrate using various techniques such as tape casting, extrusion, or dry pressing. Tape casting involves spreading the slurry onto a flat surface to form thin sheets, while extrusion uses a die to shape continuous profiles. Dry pressing compresses the slurry into molds under high pressure to form green bodies with the approximate shape of the final substrate.
- Green Machining: After forming, the green bodies may undergo machining processes such as milling or drilling to achieve precise dimensions and features. This step helps in preparing the green bodies for the subsequent sintering process.
- Sintering: The green bodies are then sintered in a high-temperature furnace under controlled conditions. During sintering, the AlN powder particles bond together, and the structure densifies to achieve the final ceramic substrate. Sintering temperatures typically range from 1700°C to 1900°C, depending on the specific requirements of the substrate.
- Acabado superficial: After sintering, the ceramic substrates may undergo surface finishing processes such as grinding, polishing, or lapping to achieve smooth surfaces and precise thickness tolerances. This step is critical for ensuring the substrate’s flatness and uniformity, which are essential for subsequent device assembly and performance.
- Metallization:In many applications, Aluminum Nitride substrates require metallization of specific areas to create conductive pathways for electronic components. Thin-film metallization techniques such as sputtering or plating are commonly used to deposit metal layers (e.g., gold, silver, copper) onto the substrate surfaces.
- Quality Control and Testing: Throughout the fabrication process, quality control measures are implemented to ensure the substrates meet specified requirements for thermal conductivity, electrical insulation, dimensional accuracy, and mechanical strength. Testing may include thermal conductivity measurements, dielectric strength testing, surface roughness analysis, and visual inspection.
- Packaging and Shipping: Once fabricated and tested, Aluminum Nitride ceramic substrates are packaged and prepared for shipping to customers or assembly facilities where they will be incorporated into electronic devices or semiconductor packages.
Each step in the fabrication process is critical to achieving Aluminum Nitride substrates with the high thermal conductivity, excellent electrical insulation, Robustez mecánica, and dimensional precision required for advanced electronic and semiconductor applications.
La aplicación de la cerámica Nitruro de aluminio (Aln) Ceramic Substrate
Nitruro de aluminio (Aln) ceramic substrates find widespread application across various industries due to their unique combination of thermal conductivity, electrical insulation, y propiedades mecánicas. Some key applications include:
- Electrónica de potencia: AlN substrates are extensively used as bases for power electronic modules such as insulated-gate bipolar transistors (IGBTs), high-power LEDs, and diode lasers. Their high thermal conductivity helps in efficiently dissipating heat generated during operation, thus enhancing device reliability and performance.
- Microwave and RF Components: AlN substrates are ideal for microwave and radio frequency (RF) applications due to their low dielectric loss and high electrical insulation properties. They are used in components such as microwave circuit boards, Antenas, filtros, and passive RF components where signal integrity and minimal loss are critical.
- Semiconductor Packaging: In semiconductor manufacturing, AlN substrates serve as a reliable base for packaging high-frequency semiconductor devices. They provide excellent thermal management and dimensional stability, reducing thermal mismatch issues that can affect device performance and reliability.
- High-Brightness LEDs:AlN substrates are preferred for high-brightness LEDs (HB-LEDs) because they can effectively dissipate heat from the LED die, enabling higher power densities and longer operational lifetimes. The thermal conductivity of AlN helps in maintaining stable LED performance over extended periods.
- Electrónica automotriz: In automotive applications, AlN substrates are used in power modules, LED lighting systems, and sensors where reliability under harsh conditions (temperature fluctuations, vibrations) is crucial. Their thermal conductivity and mechanical strength contribute to the durability and performance of electronic components in automotive environments.
- Aeroespacial y Defensa: AlN substrates are utilized in aerospace and defense electronics for their ability to withstand extreme temperatures and thermal cycling. They are employed in radar systems, communication equipment, and satellite components where reliability, Gestión térmica, and signal integrity are paramount.
- Medical Electronics: In medical devices and equipment, AlN substrates are used for their biocompatibility, Estabilidad térmica, y confiabilidad. They find applications in imaging systems, Equipos de diagnóstico, and surgical instruments where precise thermal control and electrical insulation are required.
- Electrónica de consumo: AlN substrates are increasingly used in consumer electronics such as smartphones, Tabletas, and wearables. They contribute to the miniaturization and performance enhancement of electronic devices by managing heat dissipation effectively and ensuring reliable operation over prolonged usage.
En general, Aluminum Nitride ceramic substrates play a crucial role in advancing technology across industries by enabling the development of high-performance electronic and semiconductor devices that require superior thermal management, electrical insulation, y estabilidad mecánica.
Preguntas frecuentes sobre Nitruro de aluminio (Aln) Ceramic Substrate
What is Aluminum Nitride (Aln) ceramic substrate?
Nitruro de aluminio (Aln) ceramic substrate is a material used in electronics and semiconductor industries for its high thermal conductivity, excellent electrical insulation, and mechanical strength. It provides effective heat dissipation, electrical isolation, and stability under varying operating conditions.
What are the advantages of using AlN ceramic substrates?
AlN substrates offer high thermal conductivity (~170-230 W/mK), superior electrical insulation, Robustez mecánica, and compatibility with semiconductor materials. These properties make them ideal for applications requiring efficient heat dissipation, reliability in harsh environments, and minimal signal loss in high-frequency circuits.
Where are AlN ceramic substrates used?
AlN substrates find applications in power electronics (IGBT modules, LED lighting), microwave and RF components (Antenas, filtros), semiconductor packaging, high-brightness LEDs, Electrónica automotriz, Sistemas aeroespaciales y de defensa, Dispositivos médicos, y electrónica de consumo.
Are AlN ceramic substrates environmentally friendly?
Sí, AlN is environmentally friendly due to its non-toxic composition and recyclability. Its longevity and reliability in devices also contribute to reducing electronic waste.
What are some typical quality control measures for AlN ceramic substrates?
Quality control involves testing for thermal conductivity, dielectric strength, dimensional accuracy, surface roughness, metallization adhesion, and visual inspection throughout the fabrication process to ensure consistent performance and reliability.
What are the future trends in AlN ceramic substrate technology?
Future trends include advancements in manufacturing techniques to enhance substrate performance and integration with emerging technologies such as 5G communications, electric vehicles, y dispositivos médicos avanzados. Research focuses on improving thermal conductivity, reducing manufacturing costs, and expanding application capabilities.