TU-900 Substrate Hersteller
TU-900 Substrat Hersteller,TU-900 substrate is an advanced laminate designed for high-frequency and high-speed applications in the electronics industry. It boasts a low dielectric constant and low loss tangent, ensuring optimal signal integrity for RF and microwave circuits. The substrate offers excellent thermal stability and low moisture absorption, making it reliable in demanding conditions. TU-900 is compatible with fine-line processing, allowing for complex multilayer designs and high-density interconnects. Widely used in telecommunications, Luft- und Raumfahrt, und Automotive-Anwendungen, TU-900 meets the rigorous performance standards required for modern electronic devices, providing engineers with a dependable solution for their high-performance needs.
What is TU-900 Substrate?
The TU-900 substrate is a high-performance ceramic substrate primarily used in high-frequency and high-power electronic devices. It has gained widespread attention for its excellent electrical properties and thermal stability, particularly in radio frequency (RF) und Mikrowellenanwendungen.
Key characteristics of the TU-900 substrate include a low dielectric constant and low dielectric loss, making it highly suitable for high-speed signal transmission circuits. Its superior thermal conductivity ensures effective heat dissipation under high-power operating conditions, thereby extending the lifespan of electronic components. Zusätzlich, the TU-900 substrate possesses good mechanical strength, allowing it to maintain stable performance in harsh environments.
The TU-900 substrate is widely used in communications, Fahrzeugelektronik, medizinprodukte, und Luft- und Raumfahrtindustrie. In the communication sector, it is commonly utilized in critical components such as antennas, Filter, und Verstärker. In der Automobilelektronik, it can be found in sensors and control modules, ensuring reliability under high-temperature and high-pressure conditions.
Zusammenfassend, the TU-900 substrate is becoming an important choice in high-end electronic products due to its outstanding performance and diverse application prospects. With ongoing technological advancements, the range of applications for the TU-900 substrate is expected to expand further, driving the development of the electronics industry.
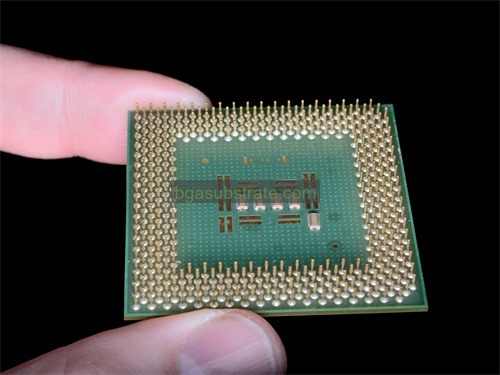
TU-900 Substrat Hersteller
What is the TU-900 Substrate Design Guidelines?
Die Gestaltungsrichtlinien für die TU-900 substrate focus on optimizing its performance in high-frequency and high-power applications. Key considerations include:
- Layer-Aufbau: Ensure the substrate’s layer configuration supports the intended application, such as RF circuits or microwave components.
- Leiterbahnbreite und -abstand: Calculate appropriate trace widths and spacing to maintain impedance control and reduce signal loss. This is critical for high-speed signal integrity.
- Wärmemanagement: Incorporate thermal vias and adequate copper thickness to enhance heat dissipation, Speziell in High-Power-Anwendungen.
- Über Design: Utilize microvias or blind/buried vias to minimize inductance and maintain signal integrity. Consider the aspect ratio to ensure manufacturability.
- Oberflächengüte: Select an appropriate surface finish to improve solderability and reduce oxidation, enhancing reliability.
- Grundebene: Implement a continuous ground plane to reduce electromagnetic interference (EMI) and improve overall performance.
- Mechanische Überlegungen: Account for mechanical stresses, especially in applications with thermal cycling, to prevent cracking or delamination.
- Galvanische Isolierung: Ensure sufficient isolation between high-frequency traces and sensitive components to minimize interference.
- Testen und Prototyping: Conduct thorough testing of prototypes to validate performance against design expectations, especially for critical parameters like dielectric constant and loss.
Following these guidelines helps maximize the performance and reliability of designs using the TU-900 substrate in demanding applications.
The advantages of TU-900 Substrate
Das TU-900 substrate bietet mehrere Vorteile, making it a preferred choice for various high-frequency and high-power applications:
- Geringer dielektrischer Verlust: Its low dielectric loss allows for minimal signal attenuation, ensuring efficient signal transmission in RF and microwave circuits.
- Hohe Wärmeleitfähigkeit: The substrate provides excellent thermal management, enabling effective heat dissipation and enhancing the reliability of high-power devices.
- Stable Electrical Performance: With a low dielectric constant, the TU-900 substrate maintains stable electrical properties across a wide frequency range, making it suitable for high-speed applications.
- Mechanische Festigkeit: Its robust mechanical properties allow it to withstand harsh environments, reducing the risk of cracking or delamination.
- Compatibility with Advanced Manufacturing: The TU-900 substrate is compatible with various PCB manufacturing processes, enabling the integration of complex circuit designs.
- Excellent EMI Shielding: The substrate’s construction provides effective electromagnetic interference shielding, improving overall circuit performance.
- Vielseitigkeit: Suitable for a wide range of applications, einschließlich Telekommunikation, Fahrzeugelektronik, und Luft- und Raumfahrt, the TU-900 substrate adapts well to diverse industry needs.
- Erhöhte Zuverlässigkeit: Its durable nature and stable performance contribute to the long-term reliability of electronic devices, especially in demanding conditions.
These advantages make the TU-900 substrate an excellent choice for designers looking to enhance the performance and reliability of their electronic products.
What is the TU-900 Substrate Fabrication Process?
The TU-900 substrate fabrication process is associated with a specific type of high-performance substrate used in advanced electronic applications, wie HF- und Mikrowellenschaltungen. The TU-900 process involves several key steps:
- Materialvorbereitung: This involves selecting and preparing the base material, which is usually a type of ceramic or composite material that provides the desired electrical and thermal properties.
- Deposition: Thin films of conductive materials, like copper, are deposited onto the substrate. This can be done using techniques like sputtering or electroplating.
- Nachbildend: Photolithography or other patterning techniques are used to define the circuit layout on the substrate. This process involves coating the substrate with a light-sensitive material, exposing it to a pattern of light, and then etching away the unexposed material to create the desired circuit patterns.
- Radierung: The exposed areas of the substrate are etched away to remove excess material, leaving behind the defined circuit patterns.
- Schichtung: For multi-layer substrates, layers of material are laminated together using heat and pressure. This step is crucial for creating complex, multi-layer circuits.
- Prüfung und Qualitätskontrolle: The fabricated substrates undergo rigorous testing to ensure they meet performance and quality standards.
The TU-900 process is designed to produce substrates with high precision and reliability, often used in demanding applications where performance and durability are critical.
The application of ceramic TU-900 Substrate
Ceramic TU-900 substrates are used in various high-performance electronic applications due to their excellent electrical, thermisch, und mechanische Eigenschaften. Hier sind einige wichtige Anwendungen:
- HF- und Mikrowellenschaltungen: TU-900 substrates are ideal for high-frequency applications due to their low dielectric loss and stable electrical performance. They are commonly used in RF amplifiers, oszillatoren, und Filter.
- Luft- und Raumfahrt und Verteidigung: In aerospace and defense industries, where reliability and performance under extreme conditions are critical, TU-900 substrates are used in radar systems, communication devices, and other advanced electronic systems.
- Fahrzeugelektronik: These substrates are used in automotive electronics for high-frequency applications such as radar sensors and advanced driver-assistance systems (ADAS), where durability and high performance are essential.
- Telekommunikation: In der Telekommunikation, TU-900 substrates support high-speed data transmission and signal integrity, making them suitable for components like base stations and communication modules.
- Medizinprodukte: The high thermal conductivity and electrical performance of TU-900 substrates make them suitable for medical devices that require precise and reliable electronic performance.
- Hochleistungselektronik: Due to their excellent thermal management properties, TU-900 substrates are used in high-power electronic devices, including power amplifiers and high-power RF circuits.
Their ability to handle high frequencies and power levels, combined with their thermal and mechanical stability, makes ceramic TU-900 substrates a preferred choice for demanding electronic applications.
FAQs about TU-900 Substrate
What is a TU-900 substrate?
TU-900 is a type of ceramic substrate known for its high performance in RF and microwave applications. It provides excellent electrical and thermal properties.
What are the key features of TU-900 substrates?
Key features include low dielectric loss, hohe Wärmeleitfähigkeit, Mechanische Stabilität, und Hochfrequenzleistung.
What are TU-900 substrates used for?
They are used in RF and microwave circuits, Luft- und Raumfahrt und Verteidigungssysteme, Fahrzeugelektronik, Telekommunikation, medizinprodukte, and high-power electronics.
Why are TU-900 substrates preferred in high-frequency applications?
They offer low signal loss and stable electrical performance, which are crucial for maintaining signal integrity at high frequencies.
How do TU-900 substrates manage heat?
TU-900 substrates have high thermal conductivity, which helps dissipate heat effectively and prevent overheating in high-power applications.
Are TU-900 substrates suitable for all electronic applications?
While TU-900 substrates are excellent for high-frequency and high-power applications, they may not be necessary for lower-frequency or less demanding applications.