HF-Substrat Hersteller
Hersteller von HF-Substraten,HF-Substrate sind spezielle Materialien, die bei der Herstellung von Hochfrequenz verwendet werden (RF) Leiterplatten, die für das Senden und Empfangen von Signalen in drahtlosen Kommunikationsgeräten unerlässlich sind. Diese Substrate sind so konzipiert, dass sie hervorragende elektrische Eigenschaften bieten, wie z. B. geringer dielektrischer Verlust und stabile Dielektrizitätskonstante, Gewährleistung von minimalen Signalverlusten und hoher Effizienz. HF-Substrate besitzen auch eine gute thermische Stabilität und sind in der Lage, hohe Frequenzen zu verarbeiten, Damit eignen sie sich für Anwendungen in der drahtlosen Kommunikation, Satellitenanlagen, Radar, und mehr. Ihre einzigartigen Eigenschaften machen sie entscheidend für die Gewährleistung der Leistung und Zuverlässigkeit von elektronischen Hochfrequenzgeräten.
Was ist HF-Substrat?
HF-Substrate sind spezielle Materialien, die bei der Herstellung von HF verwendet werden (Radiofrequenz) Leiterplatten und Komponenten. Diese Substrate sind so konzipiert, dass sie hochfrequente elektronische Signale unterstützen, die in verschiedenen Anwendungen wie der drahtlosen Kommunikation von entscheidender Bedeutung sind, Satellitenanlagen, Radartechnik, und Mikrowellenschaltungen.
Die Hauptfunktion eines HF-Substrats besteht darin, eine stabile und zuverlässige Plattform für das Senden und Empfangen von hochfrequenten Signalen bereitzustellen. Um dies zu erreichen, HF-Substrate sind mit spezifischen Eigenschaften ausgestattet, die Signalverluste und Verzerrungen minimieren. Zu den wichtigsten Merkmalen von HF-Substraten gehören geringe dielektrische Verluste, hohe thermische Stabilität, und präzise Regelung der Dielektrizitätskonstante. Diese Eigenschaften sind für die Aufrechterhaltung der Signalintegrität und -leistung bei hohen Frequenzen unerlässlich.
Zu den gängigen Materialien, die für HF-Substrate verwendet werden, gehören Materialien auf Keramikbasis, wie Aluminiumoxid und Beryllien, sowie fortschrittliche Polymere wie PTFE (Polytetrafluorethylen) und Verbundwerkstoffe auf Epoxidbasis. Jedes Material bietet je nach den Anforderungen der Anwendung unterschiedliche Vorteile, wie z.B. Thermomanagement, Elektrische Leistung, und mechanische Stabilität.
Neben den Materialeigenschaften, Bei der Gestaltung von HF-Substraten werden Faktoren wie die Schichtdicke sorgfältig berücksichtigt, Routing von Leiterbahnen, und Impedanzkontrolle. Ziel ist es, sicherzustellen, dass das Substrat die spezifischen Frequenzbereiche und Leistungspegel bewältigen kann, die für die vorgesehene Anwendung erforderlich sind, bei gleichzeitiger Minimierung von Verlusten und Interferenzen.
Insgesamt, HF-Substrate spielen eine entscheidende Rolle bei der Ermöglichung eines effizienten und zuverlässigen Betriebs von hochfrequenten elektronischen Systemen, was sie zu einem unverzichtbaren Bestandteil moderner Kommunikations- und Elektroniktechnologien macht.
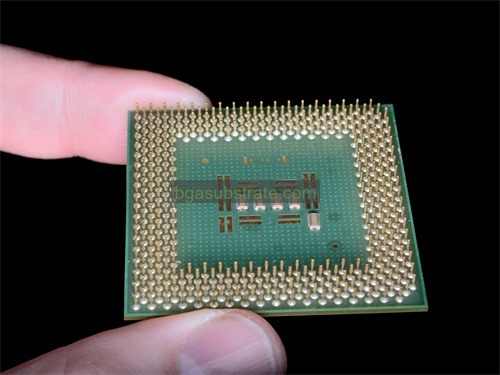
Hersteller von HF-Substraten
Was ist das HF-Substrat Richtlinien für die Gestaltung?
HF-Substrat Designrichtlinien sind entscheidend, um eine optimale Leistung und Zuverlässigkeit in hochfrequenten elektronischen Schaltungen zu gewährleisten. Hier sind die wichtigsten Überlegungen:
- Materialauswahl: Wählen Sie Substrate mit niedriger Dielektrizitätskonstante (Dk) und verlustarme Tangente (Df) zur Minimierung der Signaldämpfung und zur Aufrechterhaltung der Signalintegrität bei hohen Frequenzen. Zu den gängigen Materialien gehört PTFE (zum Beispiel., Rogers RO4000 Serie), Keramik (zum Beispiel., Tonerde, Aluminiumnitrid), und fortschrittliche Laminate. Stellen Sie sicher, dass das gewählte Material dem Frequenzbereich und den thermischen Anforderungen der Anwendung entspricht.
- Dielektrizitätskonstante: Halten Sie eine konsistente Dielektrizitätskonstante über das gesamte Substrat aufrecht, um eine vorhersagbare Impedanz und ein vorhersagbares Signalverhalten zu gewährleisten. Schwankungen des Dk können zu Signalreflexionen führen, Verlust, und Impedanzfehlanpassungen. Wählen Sie Materialien mit stabilen Dk-Werten aus und verifizieren Sie sie mit genauen Messungen.
- Verlust-Tangente: Minimieren Sie Signalverluste durch Auswahl von Substraten mit einer geringen Verlusttangente. Eine geringere Verlusttangente reduziert die Menge an Signalenergie, die als Wärme verloren geht, was besonders für Hochfrequenzanwendungen wichtig ist. Überprüfen Sie die Materialspezifikationen und die Leistung im gewünschten Frequenzbereich.
- Dicke und Schichtaufbau: Entwerfen Sie die Substratdicke und den Schichtaufbau, um die Impedanz und Signalausbreitung zu steuern. Die Dicke sollte so gewählt werden, dass die gewünschte Impedanz erreicht wird und die mechanischen und thermischen Anforderungen der Konstruktion unterstützt werden. Für mehrschichtige Designs, Stellen Sie sicher, dass die Schichten richtig ausgerichtet und verklebt werden, um Leistungseinbußen zu vermeiden.
- Wärmemanagement: Berücksichtigen Sie die Wärmeleitfähigkeit des Substratmaterials, um die Wärmeableitung effektiv zu steuern. Hochleistungs-HF-Schaltkreise erzeugen erhebliche Wärmeentwicklung, die effizient von empfindlichen Bauteilen weggeführt werden müssen. Werkstoffe mit hoher Wärmeleitfähigkeit, wie Keramik, kann helfen, die Hitze effektiver zu bewältigen.
- Fertigungs-Toleranzen: Berücksichtigen Sie Fertigungstoleranzen in der Konstruktion, um sicherzustellen, dass die Abmessungen, Layer-Ausrichtungen, und Funktionen liegen innerhalb akzeptabler Grenzen. Enge Toleranzen sind für Hochfrequenzanwendungen von entscheidender Bedeutung, um die Impedanzkontrolle und Signalintegrität zu gewährleisten.
- Elektromagnetische Verträglichkeit (EMC):Entwerfen Sie das Substrat so, dass elektromagnetische Störungen minimiert werden (EMI) und Aufrechterhaltung der elektromagnetischen Verträglichkeit. Dazu gehört auch die richtige Erdung, Abschirmung, und Layoutpraktiken, um unerwünschte Signalkopplung und Übersprechen zwischen Schaltkreisen zu verhindern.
- Testen und Validieren: Führen Sie gründliche Tests und Validierungen des Substrats und des endgültigen Schaltkreises durch, um sicherzustellen, dass er die erforderlichen Spezifikationen und Leistungskriterien erfüllt.. Dazu gehört auch die Messung der Impedanz, Signalverlust, und andere kritische Parameter unter Betriebsbedingungen.
Durch die Einhaltung dieser Richtlinien, Entwickler können sicherstellen, dass HF-Substrate zum zuverlässigen und effizienten Betrieb von hochfrequenten elektronischen Systemen beitragen, Verbesserung der Leistung und Minimierung von Problemen im Zusammenhang mit der Signalintegrität und dem Wärmemanagement.
Die Vorteile von HF-Substrat
HF-Substrate bieten mehrere Vorteile, die sie für Hochfrequenz- und drahtlose Kommunikationsanwendungen unerlässlich machen. Hier sind die wichtigsten Vorteile:
- Geringer Signalverlust: HF-Substrate sind mit geringen dielektrischen Verlusten und verlustarmen Tangenteneigenschaften ausgelegt, die die Signaldämpfung minimieren. Dies ist entscheidend für die Aufrechterhaltung der Signalintegrität und die effiziente Übertragung hochfrequenter Signale.
- Hochfrequenz-Leistung: Materialien, die in HF-Substraten verwendet werden, wie PTFE und Hochleistungskeramik, Bieten stabile elektrische Eigenschaften bei hohen Frequenzen. Dies ermöglicht einen zuverlässigen Betrieb in Anwendungen, die eine präzise Signalübertragung und -empfängung erfordern, wie HF-Kommunikationssysteme und Radar.
- Thermische Stabilität: HF-Substrate weisen oft eine ausgezeichnete thermische Stabilität auf, Dies hilft bei der Verwaltung der von Hochleistungs-HF-Komponenten erzeugten Wärme. Materialien wie Keramik bieten eine hohe Wärmeleitfähigkeit, Unterstützung bei der effektiven Wärmeableitung und Vermeidung von thermischen Schäden am Kreislauf.
- Impedanzkontrolle: HF-Substrate ermöglichen eine präzise Steuerung der Impedanz, Dies ist entscheidend für die Minimierung von Signalreflexionen und die Gewährleistung einer ordnungsgemäßen Signalübertragung. Eine konsistente Impedanz über das gesamte Substrat trägt zur Aufrechterhaltung der Signalintegrität und -leistung bei.
- Mechanische Robustheit:Viele HF-Substrate, insbesondere Keramik, bieten eine hervorragende mechanische Festigkeit und Haltbarkeit. Diese Robustheit hilft dem Substrat, physikalischen Belastungen und Umweltbedingungen standzuhalten, Beitrag zur Langlebigkeit und Zuverlässigkeit der HF-Schaltung.
- Design-Flexibilität: Fortschrittliche HF-Substrate ermöglichen das Design kompakter und effizienter Hochfrequenzschaltungen. Mit Optionen für Multilayer-Konfigurationen und Integration passiver Bauelemente, Entwickler können anspruchsvolle Schaltungen mit verbesserter Leistung und reduzierter Größe erstellen.
- Reduziertes Übersprechen: Die Eigenschaften von HF-Substraten tragen zur Minimierung von Übersprechen und elektromagnetischen Störungen bei (EMI) zwischen verschiedenen Schaltungselementen. Dies ist wichtig, um die Integrität der Signalpfade zu erhalten und das Rauschen in empfindlichen Anwendungen zu reduzieren.
- Konsistente Leistung: HF-Substrate bieten konsistente Leistungsmerkmale über einen weiten Bereich von Frequenzen und Betriebsbedingungen. Diese Zuverlässigkeit ist entscheidend für Anwendungen, die eine hohe Präzision und einen stabilen Betrieb erfordern, wie Kommunikationssysteme und Luft- und Raumfahrttechnik.
- Verbesserte Signalintegrität: Die hochwertigen Materialien, die in HF-Substraten verwendet werden, unterstützen eine verbesserte Signalintegrität, indem sie Signalverluste und Verzerrungen reduzieren. Dies gewährleistet eine klare und genaue Signalübertragung, was für Hochfrequenzanwendungen von entscheidender Bedeutung ist.
Insgesamt, HF-Substrate bieten wesentliche Vorteile für das Design von Hochfrequenz-Schaltungen, Ermöglicht eine effiziente und zuverlässige Leistung in einer Vielzahl fortschrittlicher elektronischer und Kommunikationssysteme. Ihre besonderen Eigenschaften und Vorteile machen sie zu einem wichtigen Bestandteil der modernen Technologie.
Was ist das HF-Substrat Herstellungsprozess?
Der Herstellungsprozess von HF-Substraten umfasst mehrere Schritte, um hochwertige Substrate für Hochfrequenzanwendungen herzustellen. Hier finden Sie eine detaillierte Übersicht:
- Materialauswahl und -aufbereitung: Wählen Sie das geeignete Substratmaterial basierend auf der gewünschten elektrischen, thermisch, und mechanische Eigenschaften. Zu den gängigen Materialien gehört PTFE (zum Beispiel., Rogers RO4000 Serie), Keramik (zum Beispiel., Tonerde, Aluminiumnitrid), und fortschrittliche Laminate. Das Material wird in Formen wie Platten oder Bändern aufbereitet, und kann eine Vorbehandlung erfordern, um eine ordnungsgemäße Haftung und Verarbeitung zu gewährleisten.
- Schichtung: Für mehrschichtige Substrate, Beim Laminierungsprozess werden mehrere Schichten Trägermaterial miteinander verbunden. Dies geschieht in der Regel mit einer Kombination aus Hitze und Druck, um eine starke Haftung zwischen den Schichten zu gewährleisten. Die Schichten sind präzise ausgerichtet, um die Gleichmäßigkeit zu gewährleisten und die Impedanz zu kontrollieren.
- Musterung und Radierung: Der nächste Schritt besteht darin, die Schaltungsmuster auf dem Substrat zu definieren. Dabei wird eine Fotolackschicht auf das Substrat aufgebracht, das dann durch eine Maske UV-Licht ausgesetzt wird, um das gewünschte Muster zu erzeugen. Der belichtete Fotolack wird entwickelt, und das darunterliegende Substratmaterial wird mit chemischen oder Plasmaätztechniken weggeätzt. Dieser Prozess erzeugt die notwendigen Leiterbahnen und Merkmale auf dem Substrat.
- Beschichtung und Metallisierung: Nach der Musterung, Die freiliegenden Bereiche des Substrats werden mit Metall beschichtet, um leitfähige Spuren zu bilden. Zu den gängigen Beschichtungsmethoden gehören Galvanik und Sputtern. In diesem Schritt werden die notwendigen Metallschichten für elektrische Verbindungen und die Montage von Komponenten hinzugefügt.
- Bohrungen und Via-Formation:Wenn das Design Durchkontaktierungen enthält (vertikale elektrische Verbindungen zwischen den Schichten), Das Substrat wird mit Präzisionsgeräten gebohrt. Die Durchkontaktierungen werden dann mit Metall beschichtet, um elektrische Verbindungen zwischen den verschiedenen Schichten des Substrats herzustellen.
- Reinigung und Inspektion: Das Substrat wird gründlich gereinigt, um Rückstände aus den vorangegangenen Herstellungsschritten zu entfernen. Es wird eine Inspektion durchgeführt, um sicherzustellen, dass das Substrat den Qualitätsstandards entspricht und dass die Schaltungsmuster, Beschichtung, und Durchkontaktierungen werden korrekt gebildet. Dieser Schritt umfasst häufig sowohl visuelle als auch automatisierte Inspektionen.
- Testen und Validieren: Die hergestellten Substrate werden elektrischen Tests unterzogen, um sicherzustellen, dass sie die erforderlichen Leistungsspezifikationen erfüllen. Die Tests können Impedanzmessungen umfassen, Analyse von Signalverlusten, und andere Bewertungen der elektrischen Eigenschaften.
- Schneiden und Fräsen: Die endgültigen Substrate werden auf die gewünschte Größe und Form zugeschnitten, basierend auf den spezifischen Anwendungsanforderungen. Das Routing kann auch durchgeführt werden, um Schlitze oder Ausschnitte zu erstellen, die für die Montage von Komponenten oder Steckverbindern benötigt werden.
- Endmontage und Integration: Die fertigen Substrate werden zum Endprodukt zusammengefügt. Dies kann das Anbringen von Komponenten beinhalten, Verbinder, oder andere Elemente, die für die fertige HF-Schaltung erforderlich sind. Die Endmontage stellt sicher, dass sich das Substrat nahtlos in den Rest des elektronischen Systems integriert.
- Verpackung und Versand: Die fertigen HF-Substrate werden verpackt, um sie während des Transports und des Transports zu schützen. Die richtige Verpackung stellt sicher, dass die Substrate in gutem Zustand am Bestimmungsort ankommen, Bereit für den Einsatz in Hochfrequenzanwendungen.
Indem Sie diese Schritte befolgen, Hersteller können HF-Substrate herstellen, die die hohen Anforderungen an Hochfrequenz- und Hochleistungselektroniksysteme erfüllen, Gewährleistung von Zuverlässigkeit und Effizienz in ihren Anwendungen.
Die Anwendung von Keramik HF-Substrat
Keramische HF-Substrate werden aufgrund ihrer überlegenen elektrischen Bedeutung in großem Umfang in Hochfrequenz- und Hochleistungselektronikanwendungen eingesetzt, thermisch, und mechanische Eigenschaften. Hier sind die wichtigsten Anwendungen von keramischen HF-Substraten:
- Hochfrequenz-Schaltungen: Keramische HF-Substrate eignen sich aufgrund ihrer niedrigen Dielektrizitätskonstante ideal für Hochfrequenzanwendungen (Dk) und verlustarme Tangente (Df). Diese Eigenschaften minimieren Signalverluste und Verzerrungen, Dadurch sind sie für den Einsatz in HF-Kommunikationssystemen geeignet, einschließlich Mobilfunk, Satellit, und Radarsysteme.
- Mikrowellengeräte: Keramik wird bei der Herstellung von Mikrowellengeräten wie Filtern verwendet, oszillatoren, und Verstärker. Die stabilen elektrischen Eigenschaften von keramischen Substraten gewährleisten einen zuverlässigen Betrieb bei Mikrowellenfrequenzen, die für Anwendungen wie Mikrowellenkommunikation und Radar von entscheidender Bedeutung sind.
- Leistungsverstärker: In Hochleistungs-HF-Anwendungen, Keramische Substrate werden aufgrund ihrer hervorragenden Wärmeleitfähigkeit bevorzugt. Sie helfen, die von Leistungsverstärkern erzeugte Wärme abzuleiten, Vermeidung von Überhitzung und Gewährleistung einer stabilen Leistung. Keramiken wie Aluminiumnitrid (Aln) werden häufig in diesen Anwendungen verwendet.
- Luft- und Raumfahrt und Verteidigung: Keramische HF-Substrate werden in der Luft- und Raumfahrt sowie in Verteidigungssystemen eingesetzt, bei denen Zuverlässigkeit und Leistung von größter Bedeutung sind. Durch ihre Fähigkeit, unter extremen Umgebungsbedingungen und hohen Leistungen effektiv zu arbeiten, eignen sie sich für den Einsatz in der Avionik, Lenkflugkörpersysteme, und Satellitenkommunikation.
- Unterhaltungselektronik: In der Unterhaltungselektronik, Keramische HF-Substrate werden in Geräten wie Smartphones eingesetzt, Tabletten, und WLAN-Router. Ihr geringer Signalverlust und ihre hohe Frequenzleistung tragen zu einer effizienten drahtlosen Kommunikation und hohen Datenübertragungsraten bei.
- Anwendungen in der Automobilindustrie: Keramische Substrate werden in HF-Systemen für Kraftfahrzeuge verwendet, einschließlich Radarsensoren für Fahrerassistenzsysteme (ADAS). Aufgrund ihrer Langlebigkeit und ihrer Fähigkeit, in rauen Umgebungen eingesetzt zu werden, eignen sie sich gut für Automobilanwendungen, bei denen Zuverlässigkeit und Leistung entscheidend sind.
- Medizinprodukte: In der Medizintechnik, Keramische HF-Substrate werden in bildgebenden Systemen eingesetzt, wie z.B. MRT-Geräte, und in anderen hochfrequenten Medizinprodukten. Ihre Stabilität und Leistung bei hohen Frequenzen unterstützen genaue Bildgebungs- und Diagnosefunktionen.
- Industrielle Ausstattung: Keramische Substrate werden auch in industriellen HF-Geräten verwendet, einschließlich HF-Heizsysteme und Kommunikationsgeräte, die in Fertigungsprozessen verwendet werden. Ihre robusten Eigenschaften und ihr Hochfrequenzverhalten tragen zur Effizienz und Zuverlässigkeit industrieller Anwendungen bei.
- RFID-Systeme: Keramische Substrate werden in der Radiofrequenz-Identifikation verwendet (RFID-Technologie) Tags und Lesegeräte. Durch ihre Fähigkeit, mit verschiedenen Frequenzen zu arbeiten, und ihre Langlebigkeit eignen sie sich für RFID-Anwendungen in der Logistik, Bestandsverwaltung, und Zutrittskontrolle.
- Passive Bauelemente: Keramische Substrate werden bei der Herstellung von passiven Bauelementen wie Kondensatoren verwendet, Induktivitäten, und Widerstände. Diese Komponenten sind für verschiedene HF- und Mikrowellenschaltungen unerlässlich und profitieren von den stabilen elektrischen Eigenschaften und dem geringen Signalverlust keramischer Materialien.
Zusammenfassend, Keramische HF-Substrate sind für eine Vielzahl von Hochfrequenz- und Hochleistungsanwendungen unerlässlich. Ihre einzigartigen Eigenschaften, einschließlich geringer Signalverluste, hohe Wärmeleitfähigkeit, und mechanische Robustheit, machen sie zu einer bevorzugten Wahl für anspruchsvolle Elektronik- und Kommunikationssysteme.
Häufig gestellte Fragen zur HF-Substrat
Was ist ein HF-Substrat??
Ein HF-Substrat ist ein Material, das verwendet wird, um elektronische Komponenten in Hochfrequenz zu stützen und zu isolieren (RF) und Mikrowellenschaltungen. Es wurde entwickelt, um Signalverluste zu minimieren und die Signalintegrität bei hohen Frequenzen zu erhalten.
Warum sind niedrige Dielektrizitätskonstanten? (Dk) und verlustarme Tangente (Df) wichtig für HF-Substrate?
Eine niedrige Dielektrizitätskonstante und eine geringe Verlusttangente sind entscheidend, da sie die Signaldämpfung und den Signalverlust reduzieren, Sicherstellung eines effizienten Sendens und Empfangens von hochfrequenten Signalen mit minimaler Verzerrung.
Welche Materialien werden üblicherweise für HF-Substrate verwendet??
Zu den gängigen Materialien gehört PTFE (Polytetrafluorethylen), Keramik (zum Beispiel., Tonerde, Aluminiumnitrid), und fortschrittliche Laminate wie Rogers’ RO4000 Serie. Jedes Material bietet je nach Anwendung spezifische Vorteile.
Wie wirkt sich die Wahl des Substratmaterials auf die Leistung von HF-Schaltungen aus??
Die Wahl des Substratmaterials beeinflusst die Impedanzkontrolle, Signalverlust, Thermomanagement, und allgemeine Zuverlässigkeit der Schaltung. Materialien mit stabilen elektrischen Eigenschaften und guter Wärmeleitfähigkeit verbessern die Leistung und Haltbarkeit der Schaltkreise.
Welche Rolle spielt das Wärmemanagement in HF-Substraten??
Das Wärmemanagement ist unerlässlich, um die von Hochleistungs-HF-Komponenten erzeugte Wärme abzuleiten. Werkstoffe mit hoher Wärmeleitfähigkeit, wie z.B. Keramik, helfen, Überhitzung zu verhindern und eine stabile Leistung zu erhalten.
Wie werden HF-Substrate hergestellt??
Der Herstellungsprozess umfasst in der Regel die Materialauswahl, Schichtung, nachbildend, Radierung, Beschichtung, Bohrung, und Tests. Diese Schritte sorgen für präzise Schaltungsmuster, Elektrische Anschlüsse, und die Gesamtqualität des Substrats.