Multilayer Ceramic Substrate Hersteller
Multilayer Ceramic SubstrateManufacturer,Multilayer ceramic substrates are advanced materials used in electronic packaging to support complex circuit integration. Composed of multiple layers of ceramic material, typically alumina or aluminum nitride, these substrates provide excellent thermal conductivity, mechanische Festigkeit, und elektrische Isolierung. Each layer can contain embedded circuits, Vias, and interconnects, allowing for compact and high-density electronic assemblies. Multilayer ceramic substrates are ideal for high-frequency applications, Leistungsmodule, and environments requiring reliable thermal management. Their robust construction ensures durability and performance in demanding applications such as aerospace, Telekommunikation, and advanced computing systems.
Was ist Multilayer Ceramic Substrate?
A Multilayer Ceramic Substrate (MLC substrate) is a key component in electronics manufacturing, particularly for integrated circuits and electronic packages. It’s made from layers of ceramic material (typically alumina or aluminum nitride) that are stacked and bonded together using advanced ceramic processing techniques. These substrates are essential for creating complex electronic circuits in a compact space.
Each layer of the substrate can have circuits, Vias (connections between layers), and pads for attaching electronic components like resistors, capacitors, und integrierte Schaltkreise. The layers are interconnected using metallization patterns that are precisely designed and applied using techniques such as screen printing or thin-film deposition.
MLC substrates offer several advantages over traditional printed circuit boards (Leiterplatten), such as higher circuit density, besseres Wärmemanagement, and improved electrical performance due to the properties of ceramic materials. They are crucial in applications requiring miniaturization, high-frequency operation, und Zuverlässigkeit in rauen Umgebungen.
Manufacturing MLC substrates involves precision engineering to ensure dimensional accuracy, high reliability, and compatibility with various electronic components and assembly processes. These substrates are widely used in telecommunications, Fahrzeugelektronik, medizinprodukte, and aerospace applications where performance and durability are critical.
Zusammenfassend, a Multilayer Ceramic Substrate plays a vital role in modern electronics by providing a robust foundation for creating intricate electronic circuits in a compact form factor, enhancing overall device performance and reliability.
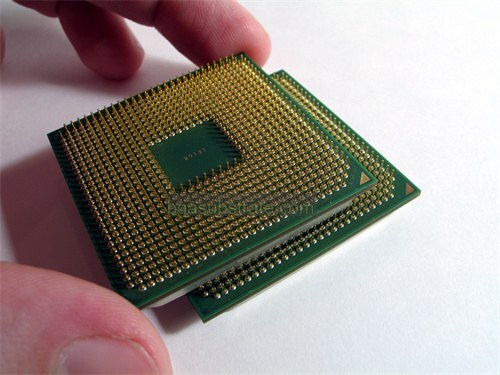
Hersteller von mehrschichtigen Keramiksubstraten
Was ist das Multilayer Ceramic Substrate Richtlinien für die Gestaltung?
Gestaltungsrichtlinien für Multilayer Ceramic Substrates (MLCs) are critical to ensure the reliability, Leistung, and manufacturability of electronic circuits. Here are some key guidelines that engineers typically follow when designing MLC substrates:
- Layer-Konfiguration: Decide on the number of layers based on the complexity of the circuit and the required density. More layers allow for denser circuit designs but increase complexity and cost.
- Materialauswahl: Choose ceramic materials such as alumina (Al2O3) oder Aluminiumnitrid (Aln) based on thermal conductivity, coefficient of thermal expansion (CTE), electrical properties, and cost. The choice impacts thermal management and electrical performance.
- Substrate Dimensions: Define the substrate dimensions based on the size constraints of the overall electronic package and the required number of components and connections.
- Via and Pad Design: Design vias (interlayer connections) and pads (contact points for components) with appropriate sizes and shapes to ensure reliable electrical connections and mechanical stability. Consider the aspect ratio of vias for manufacturability.
- Signalintegrität: Optimize trace routing and layer stacking to minimize signal interference, Übersprechen, and impedance mismatch, especially for high-frequency applications.
- Wärmemanagement: Incorporate thermal vias and thermal pads to efficiently dissipate heat generated by components. Ensure a good thermal interface between components and the substrate.
- Alignment and Tolerances: Maintain tight tolerances for layer alignment during manufacturing to ensure proper registration of vias and pads across layers.
- Design für Herstellbarkeit (DFM): Consider manufacturing capabilities and limitations such as minimum feature sizes, aspect ratios of vias, and tolerances. Ensure the design can be reliably reproduced in mass production.
- Reliability Considerations: Design for mechanical robustness and thermal stress management to ensure the substrate can withstand temperature cycling and mechanical shocks.
- Testing Provisions: Include test points and access areas for testing during assembly and quality control processes.
- Documentation: Provide comprehensive documentation including layer stack-up, Verwendete Materialien, critical dimensions, and design rules to facilitate manufacturing and troubleshooting.
Following these guidelines helps ensure that Multilayer Ceramic Substrates meet performance specifications, reliability requirements, and can be manufactured efficiently and cost-effectively. Collaboration between design engineers and manufacturing experts is crucial to optimize designs for both functionality and manufacturability.
Die Vorteile von Multilayer Ceramic Substrate
Multilayer Ceramic Substrates (MLCs) offer several significant advantages, making them highly valuable in various high-performance electronic applications. Hier sind die wichtigsten Vorteile:
- High Circuit Density: MLC substrates allow for the stacking of multiple layers of circuits, enabling high-density interconnections in a compact space. This is essential for miniaturization of electronic devices.
- Excellent Thermal Management: Ceramic materials such as alumina and aluminum nitride have high thermal conductivity, which helps dissipate heat effectively. This is crucial for high-power and high-frequency applications where heat management is critical.
- Superior Electrical Properties: Ceramics exhibit low dielectric loss and high dielectric strength, making them ideal for high-frequency and high-speed electronic circuits. They provide excellent electrical insulation and reduce signal loss.
- Mechanische Stabilität: Ceramic substrates are rigid and stable over a wide temperature range, providing mechanical robustness and reliability in harsh environments. This makes them suitable for automotive, Luft- und Raumfahrt, and industrial applications.
- Chemische Beständigkeit: Ceramics are chemically inert and resistant to corrosion, ensuring long-term reliability even in aggressive environments.
- High Reliability: The multilayer construction allows for redundant interconnections and robust design, improving the overall reliability of the electronic circuits.
- Customized Layering and Interconnections: The ability to design custom layers with specific circuit patterns, Vias, and embedded passive components provides flexibility in meeting specific application requirements.
- Miniaturisierung: MLC substrates enable significant size reduction of electronic packages by integrating more functionality into a smaller footprint. This is particularly beneficial for portable and wearable electronics.
- Enhanced Performance: Improved signal integrity due to reduced parasitic inductance and capacitance, along with better electromagnetic compatibility, enhances overall device performance.
- Skalierbarkeit:MLC technology is scalable, allowing for the development of complex multi-functional modules with varying numbers of layers and integrated components.
- Compatibility with Advanced Packaging Technologies: MLC substrates are compatible with various advanced packaging technologies such as flip-chip, Drahtanschluss, and surface mount technology (SMT), supporting modern electronic assembly processes.
- Cost-Effectiveness for High-Volume Production: For high-volume production, MLC substrates can be cost-effective due to automated manufacturing processes and material efficiencies.
These advantages make Multilayer Ceramic Substrates an attractive choice for high-performance, high-reliability electronic applications, einschließlich Telekommunikation, medizinprodukte, Fahrzeugelektronik, Systeme für die Luft- und Raumfahrt, und Unterhaltungselektronik.
Was ist das Multilayer Ceramic Substrate Herstellungsprozess?
The fabrication process of Multilayer Ceramic Substrates (MLCs) involves several precise steps to create robust ceramic structures capable of supporting complex electronic circuits. Hier finden Sie einen Überblick über den typischen Herstellungsprozess:
- Materialauswahl: High-purity ceramic materials like alumina (Al2O3) oder Aluminiumnitrid (Aln) are chosen based on desired electrical properties (dielectric constant, Wärmeleitfähigkeit), mechanische Festigkeit, and thermal expansion characteristics.
- Green Tape Preparation: The selected ceramic material is initially formed into thin, flexible sheets known as “green tapes.” These tapes are made by mixing ceramic powder with organic binders and solvents, then casting or extruding the mixture into a thin, uniform layer.
- Layering and Printing: Circuit patterns, Vias (interlayer connections), and pads (contact points) are printed onto the green tapes using screen printing or photolithography techniques. These patterns define the layout of electronic components and interconnections on each layer.
- Stacking and Lamination: Multiple layers of green tapes with printed patterns are stacked together in a precise alignment to form the multilayer structure. Between each layer, a thin layer of ceramic or glass-based paste (dielectric paste) may be applied to facilitate bonding during firing.
- Compression and Bonding: The stacked layers undergo a compression process to ensure intimate contact between adjacent layers and to remove any air or voids. This compression can be done using a mechanical press or by rolling the stack.
- Machining: After compression, the stack is machined to achieve precise dimensions and to expose vias and pads for subsequent metallization. This machining step ensures that the substrate meets exacting tolerances required for electronic assembly.
- Metallisierung: Metallization layers are applied to the exposed vias and pads using techniques such as thick-film screen printing or thin-film deposition (Sputtern, evaporation). These metallization layers provide electrical conductivity between different layers of the substrate.
- Abschuss (Sintern): The assembled substrate undergoes a firing process in a high-temperature kiln (typically between 1000°C to 1700°C depending on the ceramic material) to remove organic binders and solvents, and to densify the ceramic layers through sintering. This process bonds the ceramic particles together, forming a solid, dense ceramic structure.
- Oberflächenveredelung: After firing, the substrate may undergo additional processes such as polishing or surface coating to achieve smooth surfaces and to enhance electrical properties or solderability.
- Qualitätskontrolle: The fabricated substrates undergo rigorous testing and inspection to ensure dimensional accuracy, Elektrischer Durchgang, und Zuverlässigkeit. Tests may include electrical testing, thermal cycling, und Sichtprüfung.
- Verpackung: Einmal getestet und zugelassen, the substrates are packaged and shipped to electronics manufacturers for assembly into final electronic devices.
The fabrication process of Multilayer Ceramic Substrates requires careful control of materials, precise manufacturing techniques, and quality assurance measures to produce substrates that meet the stringent requirements of modern electronic applications.
Die Anwendung von Keramik Multilayer Ceramic Substrate
Multilayer Ceramic Substrates (MLCs) find extensive applications across various industries and technologies due to their unique properties and capabilities. Hier sind einige wichtige Anwendungen:
- Microelectronics and Integrated Circuits: MLC substrates are widely used as the base for integrated circuits (Ik), microprocessors, and microcontrollers. They provide a stable and reliable platform for mounting and interconnecting semiconductor devices, resistors, capacitors, and other passive components in compact electronic assemblies.
- High-Frequency RF/Microwave Devices: Due to their low dielectric loss and high-frequency performance, MLC substrates are essential for RF/microwave applications. They are used in components such as antennas, Filter, Kupplungen, and amplifiers in telecommunications, Radarsysteme, Satellitenkommunikation, and wireless networks.
- Leistungselektronik:MLC substrates with high thermal conductivity and excellent thermal management properties are crucial in power electronic applications. They are used in power modules, Wechselrichter, converters, and motor drives where efficient heat dissipation and electrical insulation are essential.
- Fahrzeugelektronik: In der Automobilindustrie, MLC substrates are employed in engine control units (Steuergeräten), Sensoren, LED lighting systems, and safety systems. They withstand high temperatures, Schwingungen, and harsh environmental conditions, ensuring reliable performance in automotive electronics.
- Medizinprodukte: MLC substrates are used in medical imaging equipment, patient monitoring systems, diagnostic devices, and implantable medical devices. Their biocompatibility, Zuverlässigkeit, and compact size make them suitable for critical medical applications.
- Luft- und Raumfahrt und Verteidigung: In der Luft- und Raumfahrt und im Verteidigungsbereich, MLC substrates are used in avionics, Kommunikationssysteme, Radarsysteme, guidance systems, and missile electronics. They offer high reliability, Haltbarkeit, and resistance to extreme temperatures and environmental factors.
- Unterhaltungselektronik: MLC substrates are found in consumer electronics such as smartphones, Tabletten, wearable devices, and digital cameras. They enable miniaturization of electronic components and support high-speed data processing and connectivity.
- Industrieelektronik: In industrial automation, MLC substrates are used in control systems, Robotertechnik, power supplies, and instrumentation. They provide ruggedness, Zuverlässigkeit, and longevity in industrial environments.
- Energy Storage and Renewable Energy: MLC substrates are utilized in energy storage systems such as batteries and capacitors, as well as in renewable energy applications including solar inverters and wind turbine controls. They contribute to improving efficiency and reliability in energy conversion and storage.
- LED Lighting: MLC substrates support the thermal management and electrical insulation requirements of high-power LED lighting systems, ensuring longevity and efficiency in lighting applications.
Insgesamt, Multilayer Ceramic Substrates play a crucial role in enabling advanced electronic systems across diverse industries by providing a robust foundation for compact, high-performance electronic circuits and components.
Häufig gestellte Fragen zur Multilayer Ceramic Substrate
What are Multilayer Ceramic Substrates (MLCs)?
MLCs are ceramic-based structures composed of multiple layers of ceramic material bonded together with metallization layers. They serve as a foundation for mounting and interconnecting electronic components in compact electronic devices.
What materials are used to make Multilayer Ceramic Substrates?
Common materials include alumina (Al2O3) und Aluminiumnitrid (Aln). Alumina is preferred for its excellent electrical insulation and thermal conductivity, while AlN offers even higher thermal conductivity, making it suitable for high-power applications.
What are the advantages of using Multilayer Ceramic Substrates?
MLCs offer advantages such as high circuit density, Hervorragendes Wärmemanagement, überlegene elektrische Eigenschaften, Mechanische Stabilität, chemical resistance, and high reliability. They are essential for high-frequency applications, Leistungselektronik, and environments requiring robust performance.
How are Multilayer Ceramic Substrates fabricated?
The fabrication process involves steps such as preparing green tapes from ceramic powders and binders, printing circuit patterns and vias on these tapes, stacking and compressing multiple layers, metallizing vias and pads, firing (Sintern) to densify the ceramic layers, and finishing with surface treatments and quality control checks.
What are the typical applications of Multilayer Ceramic Substrates?
MLCs find applications in microelectronics (Ik, microprocessors), HF-/Mikrowellengeräte (Antennen, Filter), Leistungselektronik (Wechselrichter, converters), Fahrzeugelektronik (Steuergeräten, Sensoren), medizinprodukte, Luft- und Raumfahrt und Verteidigungssysteme, Unterhaltungselektronik (Smartphones, wearables), und Industrieelektronik (control systems, instrumentation).
What considerations should be made when designing with Multilayer Ceramic Substrates?
Design considerations include material selection based on thermal and electrical requirements, layer configuration for circuit density, via and pad design for reliable connections, thermal management strategies, and adherence to manufacturing guidelines for optimal performance and manufacturability.